Helping Svante to Advance Groundbreaking Carbon Capture Technology
At the Technology Centre Mongstad (TCM), Canada-based Svante Technologies Inc. is testing its innovative solid sorbent-based carbon capture technology in a campaign that began in November and is scheduled to run until February 2025.
This collaboration marks a critical step in Svante’s mission to validate its modular rotary contactor machines for industrial carbon capture and further demonstrate their potential to reduce costs and improve efficiency in addressing global CO2 emissions.
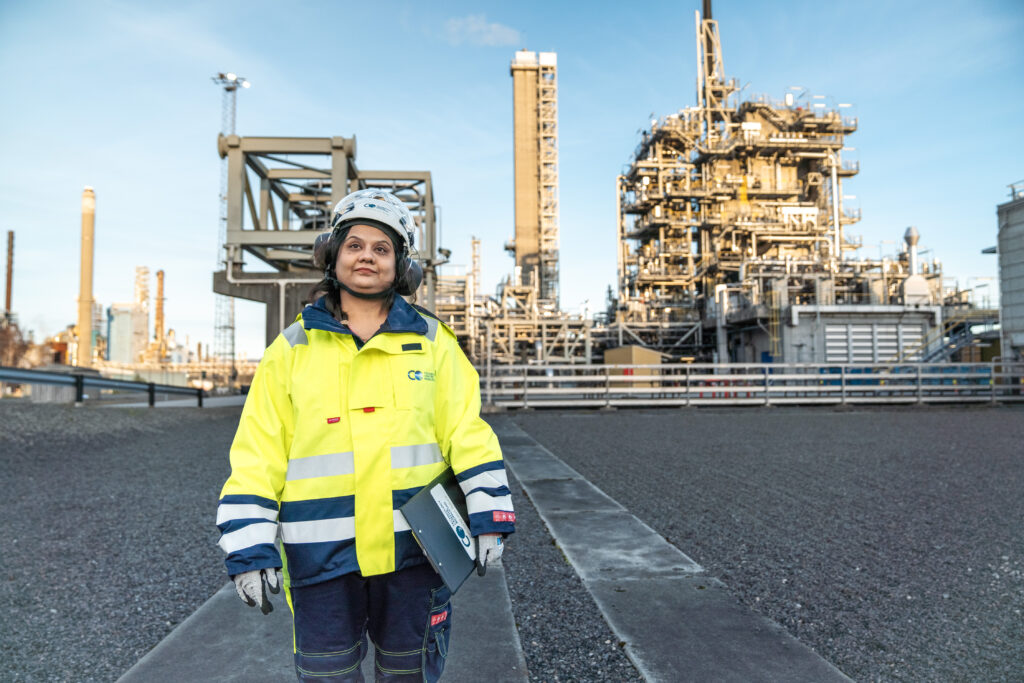
Real-World Testing at a World-Class Facility
Svante selected TCM for its advanced facilities and expertise in testing carbon capture technologies under real-world conditions. “Svante’s benefit in coming to TCM is the ability to test their technology with real flue gas and validate the performance and stability of their adsorbent beds for industrial applications. In addition, Svante will also benefit from TCM’s excellent analytical capabilities to validate thier low emission performance,” says Sundus Akhter, CO2 Capture Technologist at TCM and lead coordinator for the campaign.
The campaign utilizes flue gas from Equinor’s Residue Fluid Catalytic Cracker (RFCC) unit, allowing Svante to evaluate the stability of its adsorbent materials under challenging industrial conditions. “We supported Svante by making the necessary modifications and arrangements to ensure they could start the campaign on schedule,” Sundus adds.
Svante’s innovative sorbent technology is designed to operate without harmful chemical fugitive emissions, and the company aims to demonstrate its material stability and low emission profile during the campaign.
Svante’s system stands out with its innovative rotating adsorption machine designed for CO2 capture. During the campaign, the company is conducting tests under varying levels of contaminants in the flue gas. Additionally, TCM has supported their efforts by providing advanced instruments and result analysis to monitor and assess secondary emissions effectively.
Flexibility and Collaboration at the Site for Emerging Technologies
The testing takes place in a newly constructed tent at TCM’s Site for Emerging Technologies. This setup, designed to protect equipment from harsh weather, has proven to be a flexible solution for Svante’s campaign and future testing operations. “The tent allows us to run campaigns under varying weather conditions while saving costs on various modifications and insullations for our partners,” Sundus explains.
“Svante has a strong on-site presence, with two full-time operators and additional personnel filling in as needed,” Sundus says. “Whenever there are interesting results during the parametric testing, we collaborate with the Svante team to analyze the outcomes with expert input from TCM’s side, which provides valuable insights for their technology development.”
Pioneering Technology with Global Implications
Svante’s sorbent material technology is at the forefront of carbon capture innovation, designed to trap CO2 from industrial settings. The solid sorbent work within modular rotary contactor machines, offering scalable solutions for industries such as cement, power generation, and refining. By demonstrating that their technology can withstand impurities like SOx and NOx without pre-cleaning the flue gas, Svante hopes to pave the way for significant cost savings in carbon capture operations.
The collaboration with TCM underscores the facility’s role as a key partner for technology developers seeking to scale carbon capture solutions. “Svante is very professional and appreciative of the arrangements we’ve made to support their testing. Our advanced analytical capabilities, especially in detecting emissions, make TCM an ideal testing ground,” Sundus says.
A Shared Commitment to Innovation
With operations continuing into early 2025, Svante and TCM are making significant strides toward advancing carbon capture technology. The collaboration not only validates the resilience of Svante’s sorbent technology but also highlights the importance of partnerships in tackling the climate crisis.
By combining Svante’s cutting-edge technology with TCM’s expertise, the campaign is poised to deliver critical insights for scaling sustainable carbon capture solutions that benefit industries and the environment alike.
Impressed by the Potential of TCM
«For many of the participants from industrial companies with no prior knowledge of TCM, the visit to Mongstad provided a true “aha” moment. They were impressed by the scale of the facility and the potential the technology center represents for developing efficient and secure solutions for carbon capture and storage (CCS).»
TCM regularly receives visitors from many countries eager to see and learn about technologies for CO2 capture. Recently, senior engineer Klas Solberg of DNV and Gaute Svenningsen, group leader at the Institute for Energy Technology (IFE), led a large delegation of representatives from companies participating in three international research projects related to various aspects of carbon capture, transport, and storage. These delegates gathered for project meetings in Bergen and made a joint excursion to learn more about what TCM represents and can offer.
“After the visit, several participants expressed that testing technologies at TCM or receiving assistance to find solutions to specific challenges would be relevant for advancing their emission-reducing projects. This included large oil companies, industrial enterprises, and companies supplying materials for constructing CO2 capture or storage facilities.”
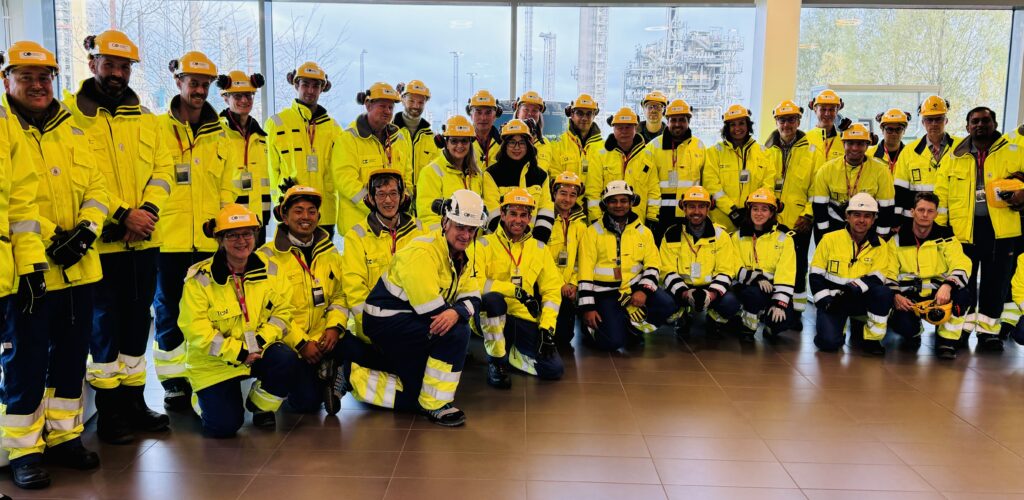
Studying Impurities in CO2 in Ship Tanks and Pipelines
At IFE, the KDC project (Kjeller Dense Phase CO2 Corrosion) is now in its fourth phase. All phases have received financial support from CLIMIT in addition to industry funding. KDC-IV began in 2023 and will continue until 2028. The project brings together 22 participants from industries worldwide.
Rolf Nyborg, explains that the KDC projects focus on studying the effects of impurities in CO2 on corrosion in pipelines and ship tanks.
“The goal is to identify combinations of concentrations of various impurities in CO2 that ensure safe CO2 transport. IFE conducts a series of laboratory experiments with controlled amounts of different impurities at ppm levels to study this. This work is central to the development of CO2 specifications for safe CO2 transport internationally,” he says.
Material Selection for Injection Wells
IFE is also behind the CO2WellMat project (Materials for CO2 injection wells), which started in 2017. With 16 participating companies, including several steel producers the project is now in phase II.
The CO2WellMat projects focus on studying which stainless steel alloys can be used in the lower sections of CO2 injection wells, where injected CO2 meets formation water in the reservoir where CO2 will be stored. The project examines the effects of impurities in the injected CO2 on corrosion in various steel and nickel alloys.
This work is crucial for material selection in injection wells for several planned CO2 storage projects.
Investigating Sulphide Stress Cracking and Corrosion Damage Caused by Hydrogen Sulfide
DNV’s CO2 Safe & Sour is another collaborative project, involving 15 industrial companies from Norway and abroad. Initiated in 2022, the project examines how increasing levels of hydrogen sulfide (H2S) will affect the risk of sulfide stress corrosion (SSC) and other corrosion damage in carbon steel pipelines used for CCS.
”The goal is of the project is to provide clearer guidance related to the level of H2S in the CO2 stream to be transported in CCS pipelines and in particluar to establish limits for carbon steel with respect to H2S in dense phase CO2.” Says project manger Klas Solberg
The project will provide general recommendations for broad industry use and will lead to an update of the DNV-RP-F104 “Design and operation of carbon dioxide pipelines.”
Driving Global Collaboration: TCM’s Role in Advancing CO₂ Capture Technologies
“TCM’s greatest opportunities lie in strengthening its position as a global hub for CO2 capture technology validation and commercialization,” says Rouzbeh Jafari, who was appointed the company’s Business Development Manager earlier this year.
Rouzbeh highlights that the growing international urgency to meet climate targets presents immense potential for Technology Centre Mongstad to aid emerging markets in adopting carbon capture and storage (CCS) solutions.
“By forging partnerships with key players across regions such as North America, Europe, the Middle East, and Asia-Pacific, TCM can establish itself as the premier facility for technology demonstration and risk mitigation.”, says Rouzbeh Jafari.
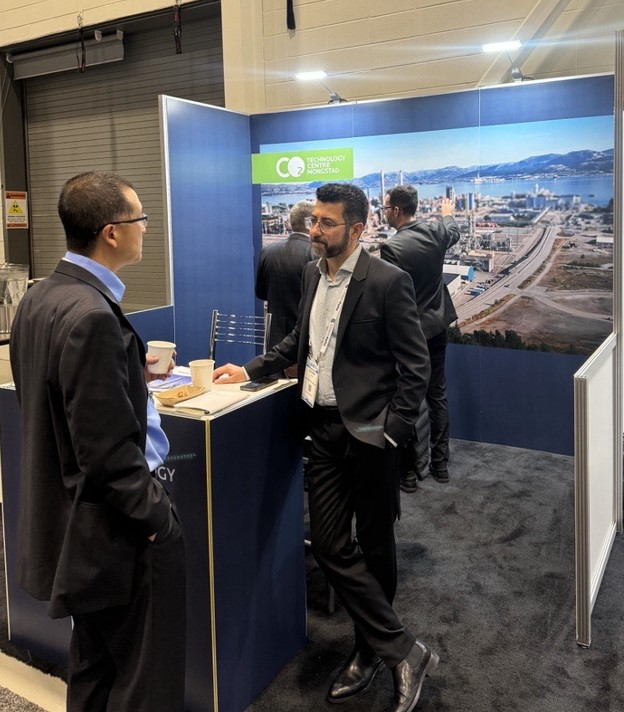
Rouzbeh Jafari at GHGT-17 in Canada.
“What was your first impression of TCM, and how did that experience shape your decision to join the team?”
“My first visit to TCM was in 2015, during my time with Shell Cansolv. I was immediately impressed by its status as a world-class facility tackling one of the most pressing challenges of our time—carbon emissions reduction. The scale of operations, depth of technical expertise, and unwavering focus on advancing CO2 capture technologies stood out to me. This experience played a pivotal role in my decision to join TCM, as it offered a rare opportunity to contribute to cutting-edge innovation with real-world impact. The collaborative environment and the chance to work alongside leading experts solidified my belief that TCM was the ideal place to help drive the transition to a sustainable, low-carbon future.”
2_capture_technologist_consultant_starting_in_2022,_what_attracted_you_to_the_role,_and_how_did_it_fit_with_your_long-term_career_goals?"">“As a CO2 Capture Technologist Consultant starting in 2022, what attracted you to the role, and how did it fit with your long-term career goals?”
“The role offered a chance to tackle one of the planet’s most urgent challenges—reducing carbon emissions—while blending technical problem-solving and collaboration with industry leaders. I was excited by the potential to scale impactful technologies that support the net-zero transition. This role perfectly aligned with my goal to drive meaningful change in energy and environmental sectors, allowing me to apply my expertise in technology maturation and commercialization while influencing sustainable solutions.”
Name: Rouzbeh Jafari
Age: 46
Marital status: Married
Education: Ph. D. in Chemical Engineering from Ecole Polytechnique Montreal, Canada,
Position: Business Development Manager since July 2024
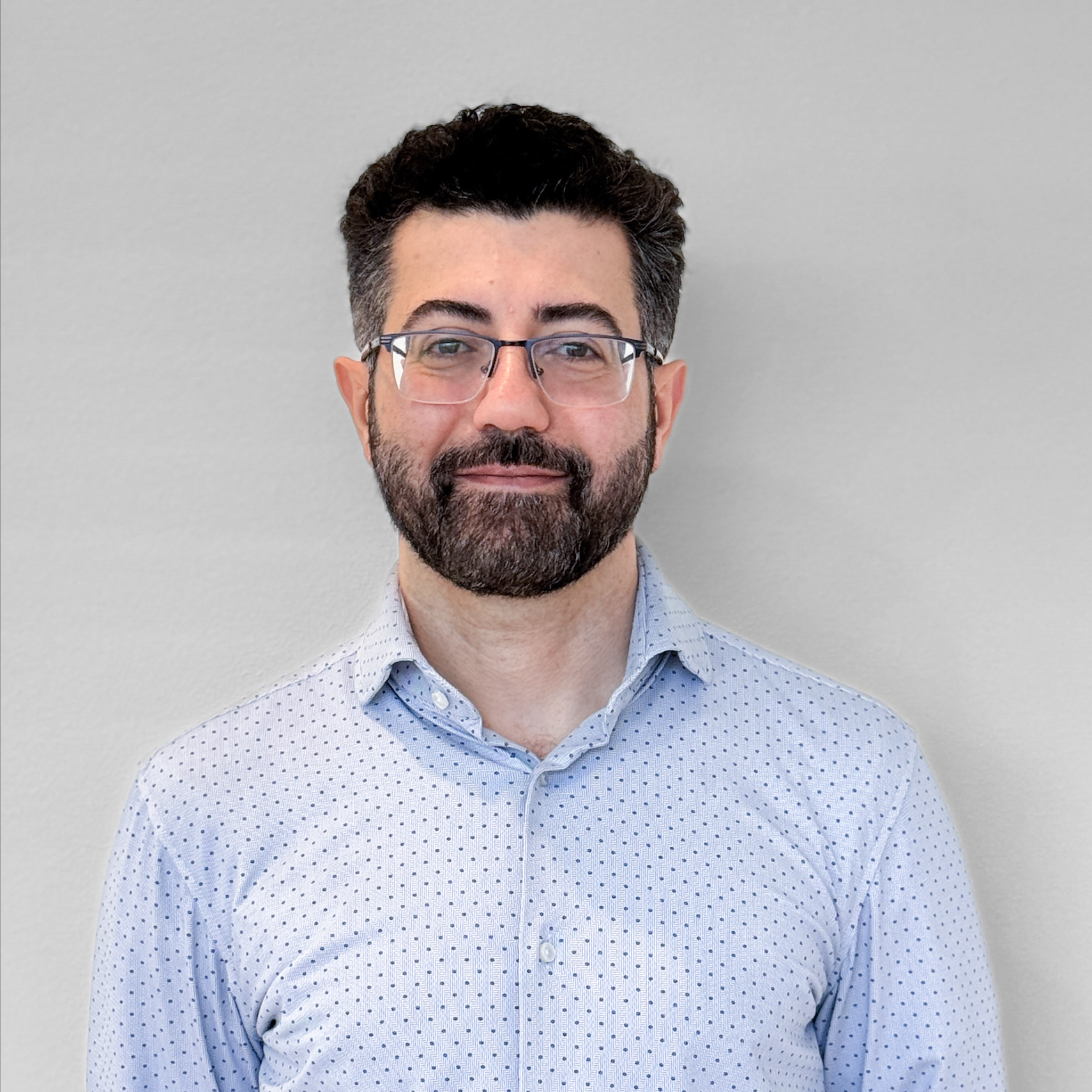
2_capture_technologies,_what_insights_did_you_bring_to_tcm,_and_how_have_they_influenced_your_contributions?"">“With over ten years of experience in CO2 capture technologies, what insights did you bring to TCM, and how have they influenced your contributions?”
”With over a decade of experience in CO2 capture technologies—ranging from solvent systems to emerging solutions—I have developed a strong expertise in scaling these technologies effectively. At TCM, I’ve optimized testing protocols, refined client campaigns for actionable insights, and aligned capture solutions with industry demands. My contributions have also strengthened TCM’s position in global markets, particularly in North America.”
“Rouzbeh, As Business Development Manager, how do you plan to address challenges and seize opportunities for TCM’s growth?”
“My approach focuses on building strong partnerships, leveraging TCM’s unique capabilities, and navigating evolving regulatory landscapes. TCM’s biggest opportunities lie in expanding its global role in CO2 capture technology validation, particularly in North America, Europe, and Asia-Pacific. Locally, aligning with net-zero strategies in sectors like cement and steel can broaden our impact. My goal is to align TCM’s offerings with market demands, attract new clients, and secure funding for future advancements.”
“How do you engage with stakeholders to advance TCM’s mission?”
“I prioritize trust and collaboration by aligning TCM’s expertise with stakeholders’ goals. Proactively engaging industry partners through workshops and direct dialogue, I ensure TCM remains indispensable in decarbonization efforts. Strategic connections with policymakers and participation in funding programs like the EU Innovation Fund further strengthen TCM’s role. Sharing success stories and showcasing TCM’s impact amplifies our credibility and attracts broader support.”
“What are your priorities this winter, and how do they support TCM’s long-term objectives?”
“My priorities include strengthening client engagement, driving new business opportunities through global funding streams, and ensuring impactful results from testing campaigns. Promoting TCM’s work at conferences and improving internal collaboration will streamline operations and enhance our value proposition, ensuring we remain a leader in CO2 capture technology validation and commercialization.”
“What changes have you observed during your time at TCM, and how do they reflect its strategic direction?”
“TCM has sharpened its focus on global collaborations, aligning with net-zero goals and emerging markets. Customized testing campaigns and stronger integration between business and technical teams have improved client outcomes, while deepened partnerships reinforce TCM’s position as a hub for innovation and decarbonization.”
“Rouzbeh, What is your vision for TCM’s future?”
“My vision is for TCM to lead globally in advancing CO2 capture technologies, fostering collaboration, and accelerating decarbonization efforts. By continuing to validate breakthrough technologies, expanding partnerships, and meeting evolving climate targets, TCM will drive innovation and support the transition to a sustainable, low-carbon economy.”
TCM Employees Experience Northern Lights Up Close
“As exciting and beautiful as the Northern Lights in the sky,” said one of the employees from Technology Centre Mongstad (TCM) after visiting the Northern Lights facility in Øygarden, just outside Bergen.
At the end of September, Energy Minister Terje Aasland inaugurated, Northern Lights, the world’s first commercial facility for the transport and permanent storage of CO2 beneath the seabed. On November 15, nearly 20 TCM employees had the chance to visit this groundbreaking facility and see its operations in action. While TCM focuses on developing and testing CO2 capture technology, the visit offered insight into the next critical steps in the value chain—transport and storage—as part of Norway’s flagship Longship project.
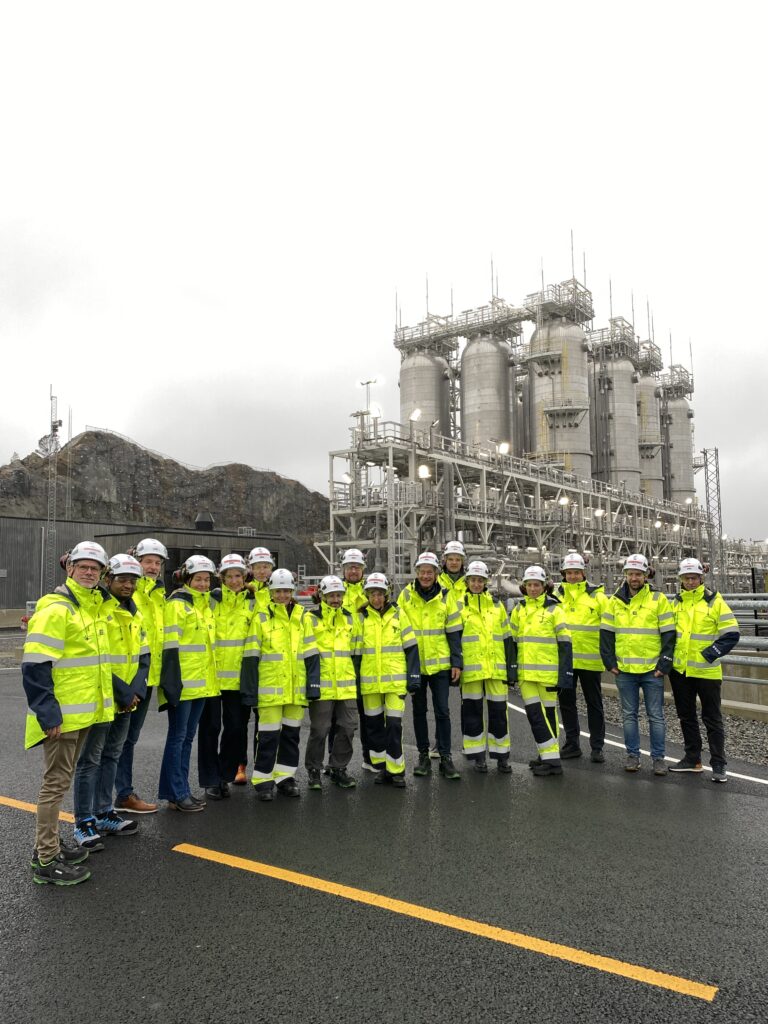
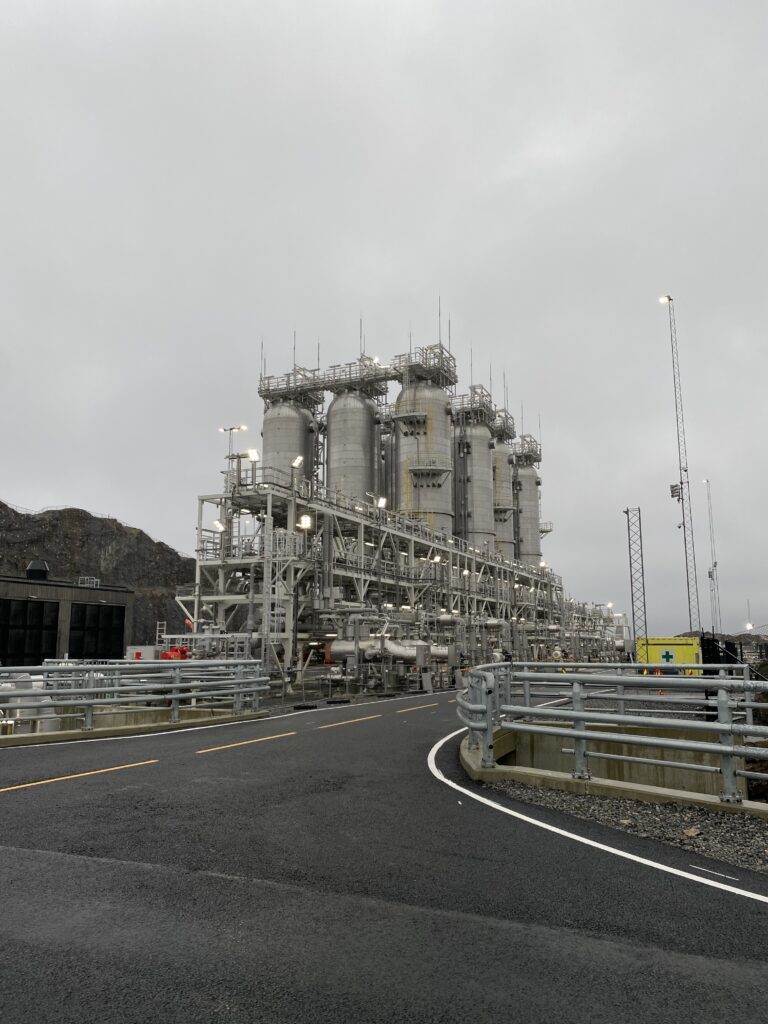
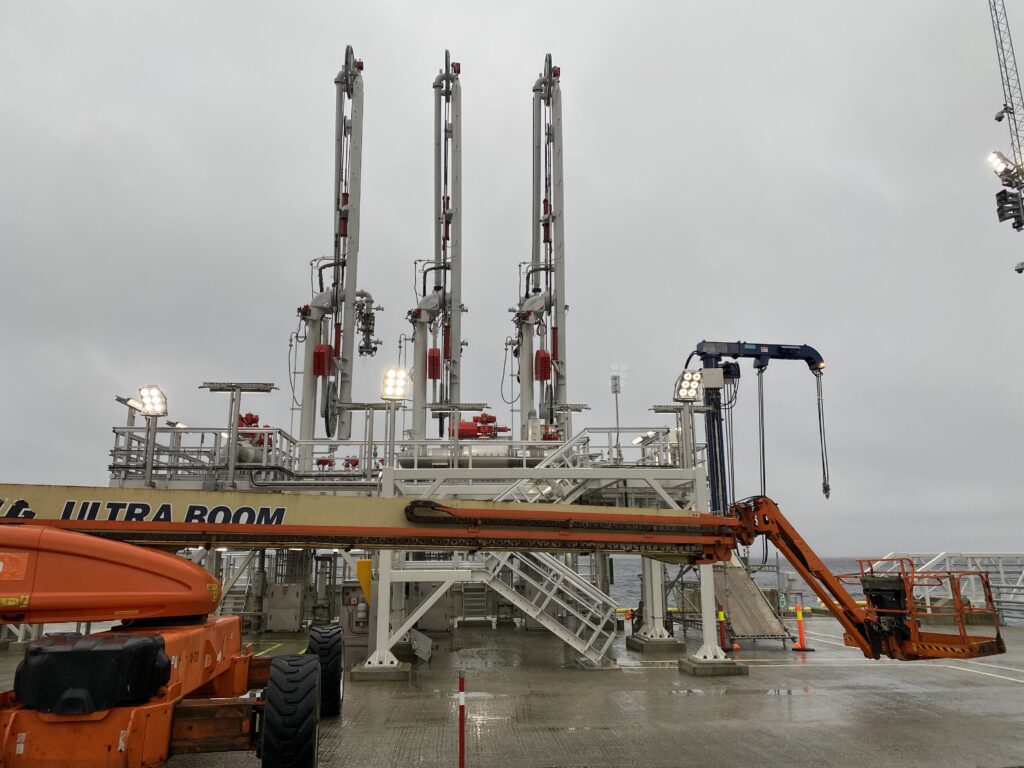
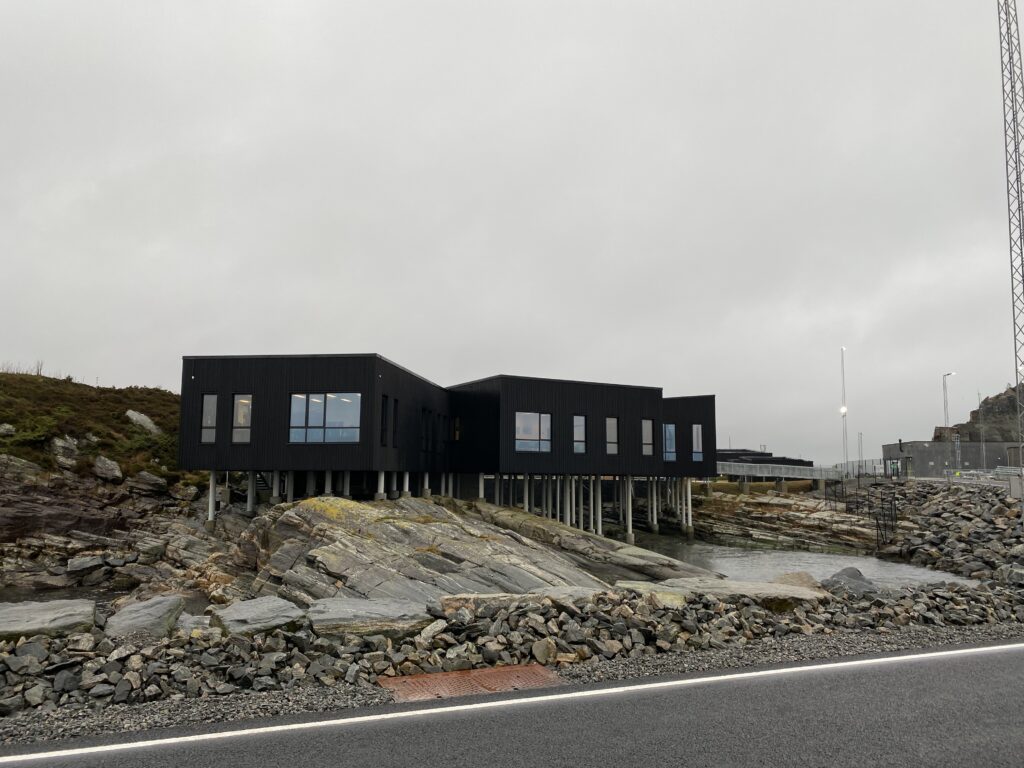
Fully Operational by Next Year
The Longship project is set to become fully operational next year when the CO2 capture facility at Heidelberg Materials in Brevik is completed in 2025. The capture technology, extensively tested at TCM, will enable the facility to collect around 400,000 tons of CO2 annually. The captured CO2 will then be transported by specially built ships to Øygarden, where it will enter pipelines stretching 110 kilometers out into the North Sea. From there, it will be safely and permanently stored in a reservoir located 2,600 meters below the seabed.
Scaling Up for the Future
Northern Lights will play a key role in transporting liquid CO2 by ship from both Norwegian and European sources to Øygarden. During the first phase, the facility has the capacity to store 1.5 million tons of CO2 annually. However, the pipeline from the onshore terminal to the reservoir is designed to accommodate up to 5 million tons. The project aims to gradually scale capacity to 5 million tons per year through phased expansions, aligned with growing demand from industries in Norway and Europe.
The facility’s owners—Equinor, Shell, and Total Energies—are expected to make a decision by February next year regarding a potential investment in Phase 2 of the project, which could further expand the scope and impact of this pioneering CO2 storage initiative.
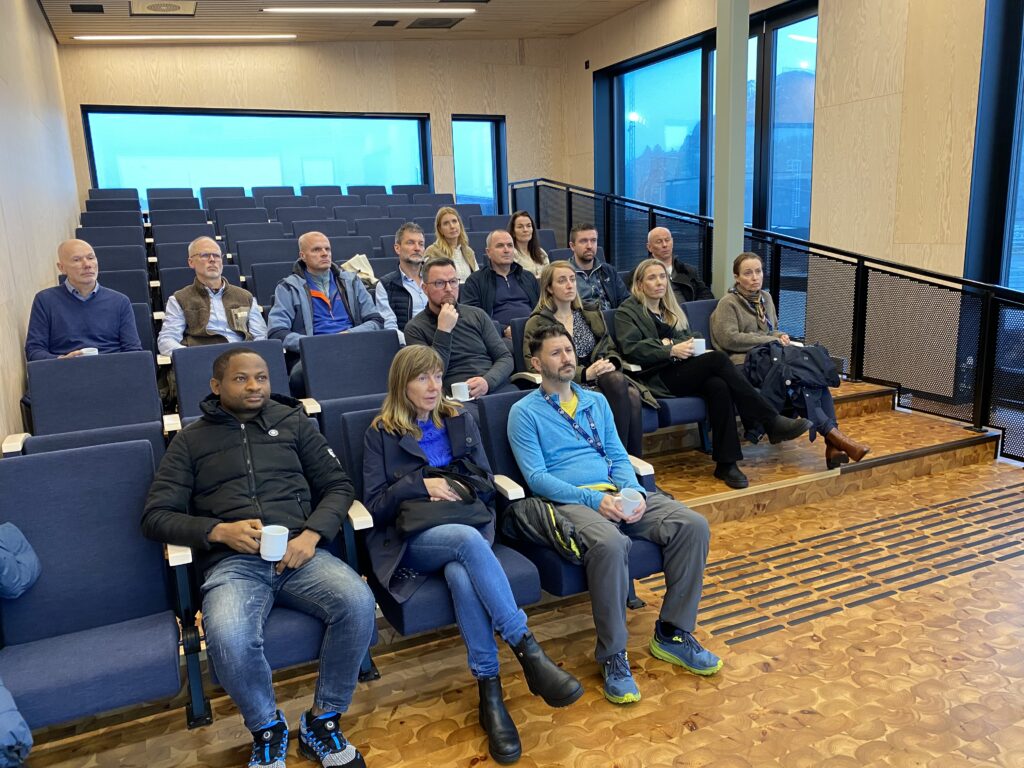
Two Rewarding Days for TCM in Hamburg
“We look back on two inspiring and highly productive days at the Carbon Capture Technology Expo Europe in Hamburg,” says Muhammad Ismail Shah, Managing Director at Technology Centre Mongstad (TCM).
This expo in Hamburg had around 15,000 visitors and 800 exhibitors and is the largest event for carbon capture, utilization, and storage (CCUS) in the world.
TCM’s stand in the conference area was highly visited. Together with Technical services lead and projects coordinator Koteswara Rao Putta and Communication Manager Liv Lønne Dille, Shah met numerous industry leaders and carbon capture specialists.
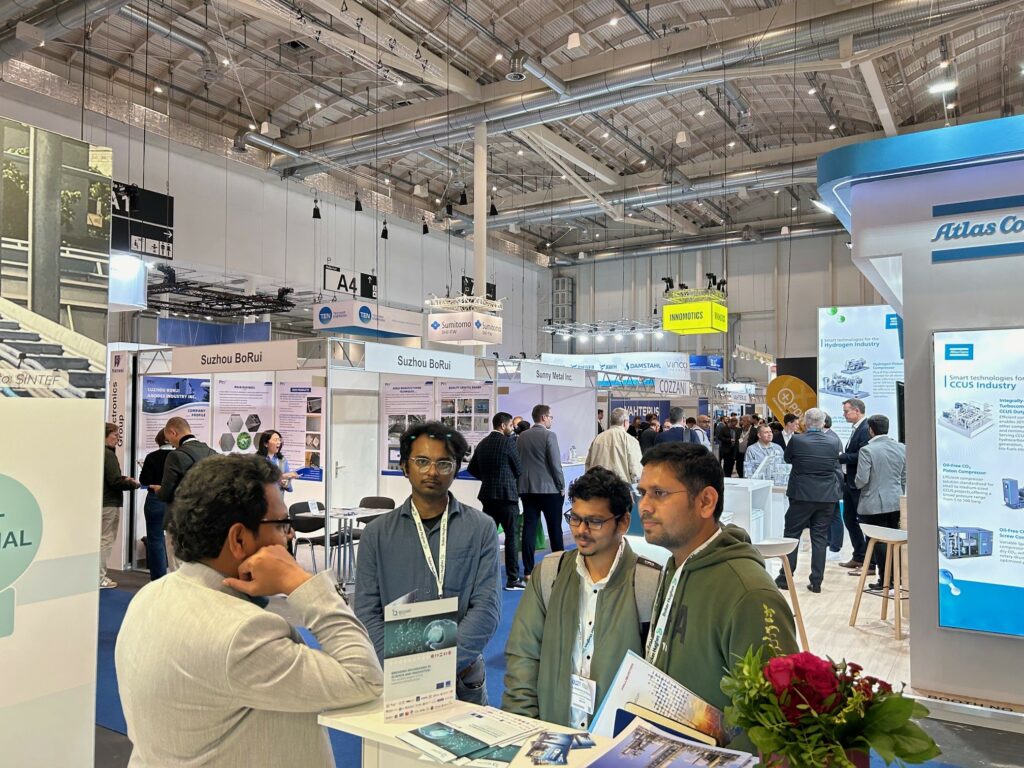
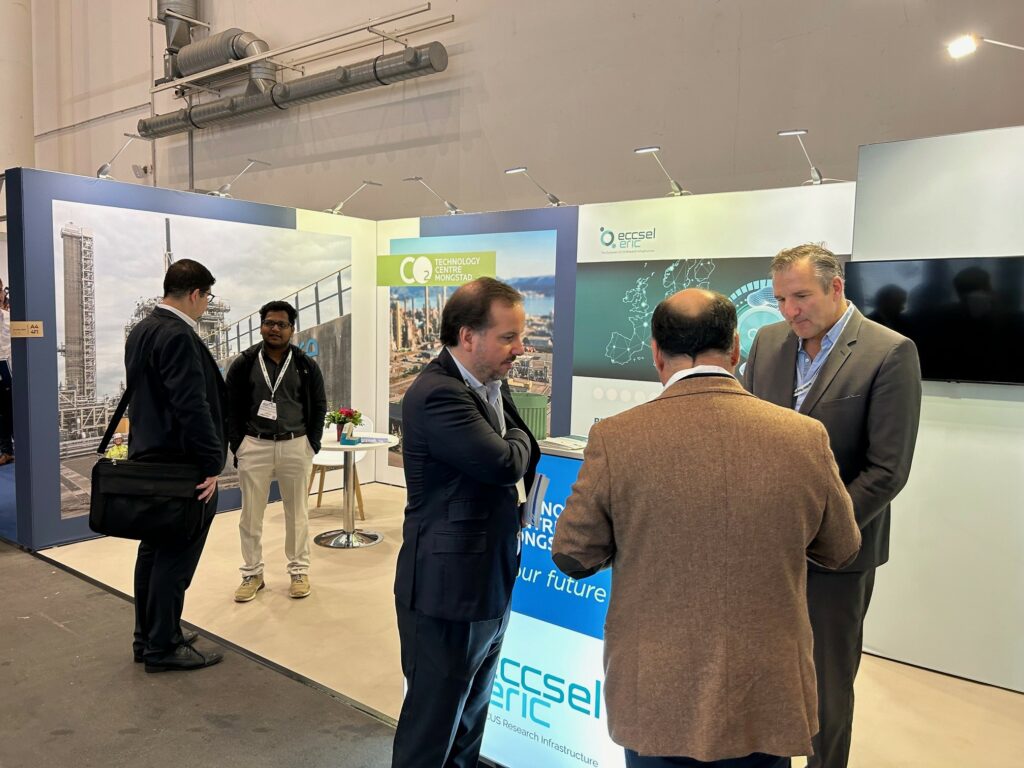
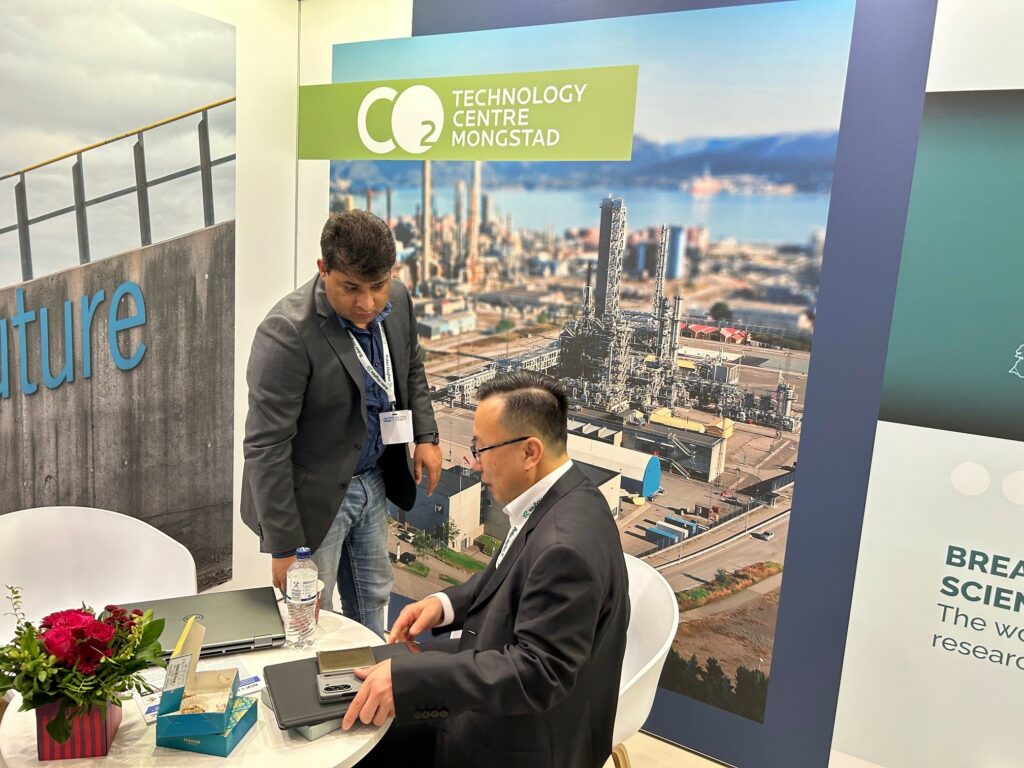
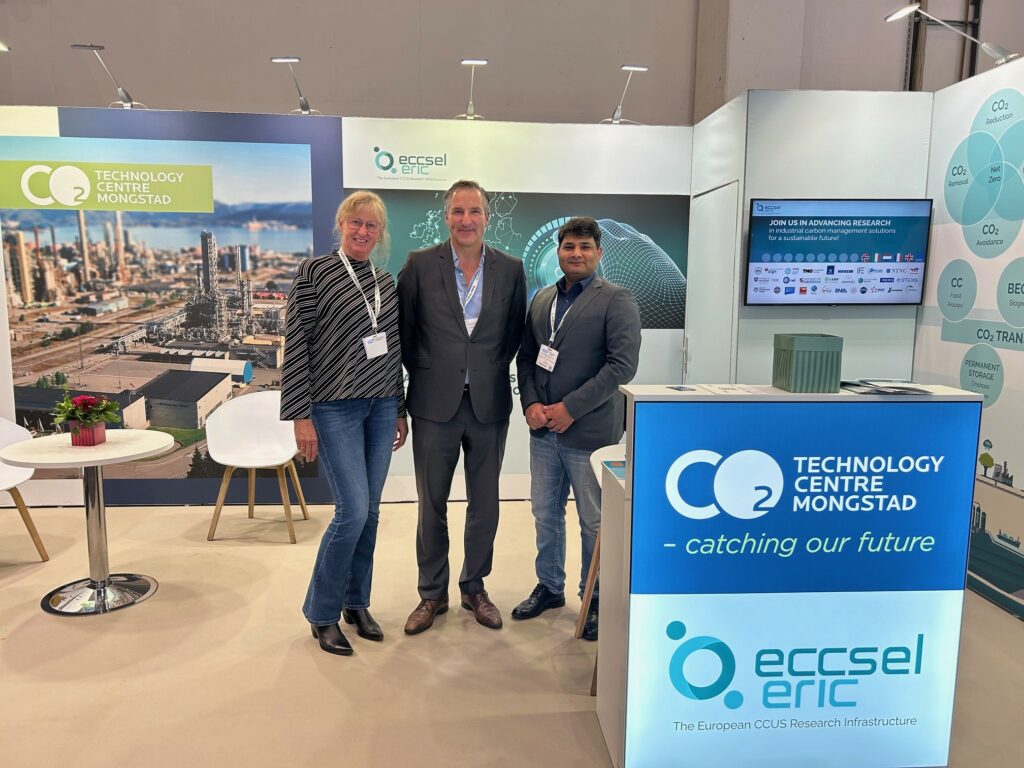
Many useful conversations in Hamburg.
Established new and valuable contacts
“We established new and valuable contacts with technology vendors, project owners, and others who may be interested in testing and cooperating with TCM. We are already working to set up meetings with several of them. I hope this will lead to synergies that can accelerate the commercialization of carbon capture technologies,” Shah says.
Koteswara Rao Putta shared that he had fruitful discussions during the event with representatives from several companies interested in collaborating with TCM, either for testing at the facilities or for assistance from TCM Advisory Services to develop their projects.
“I also found it interesting that some were keen to learn more from our open campaigns on the amine plant with MEA and CESAR1 solvents. All of these contacts will be followed up in the coming months.”
Joint Stand with ECCSEL ERIC
At this event, TCM shared a joint stand with ECCSEL ERIC. ECCSEL is the European Research Infrastructure for CO2 Capture, Utilization, Transport, and Storage (CCUS). Their mission is to advance European research, technology development, innovation, and education in the CCUS field. ECCSEL ERIC is a distributed, integrated research infrastructure that includes interconnected transnational scientific facilities and national hubs.
“ECCSEL ERIC is the largest infrastructure for CCUS in Europe, and we held high-level discussions with them. That they chose to collaborate with TCM at this event was positively noted,” emphasizes Muhammad Ismail Shah.
Based on the positive experience for TCM’s business development at the expo in Hamburg, the management has already made a decision: “We will return to Hamburg next year,” says Liv Lønne Dille.
Great Engagement at the World’s Largest CCS Conference
The 17th Greenhouse Gas Control Technology Conference (GHGT-17) proved to be an invaluable experience, spotlighting TCM’s impactful work across various facets of carbon capture technology.
“TCM received outstanding attention for both our lectures and presentations at GHGT-17, as well as our booth in the exhibition area,” shared Matthew Campbell, Technology Manager at Technology Centre Mongstad (TCM).
From October 20 to 24, 2024, GHGT-17 gathered the world’s leading CCS experts in Calgary, Canada, uniting researchers, industry leaders, government officials, and business partners from around the world to exchange insights on the latest greenhouse gas mitigation technologies. Representing TCM were Technology Manager, Matthew Campbell, Business Development Manager Rouzbeh Jafari, and Senior CO2 Capture Technologist Ahmad Wakaa.
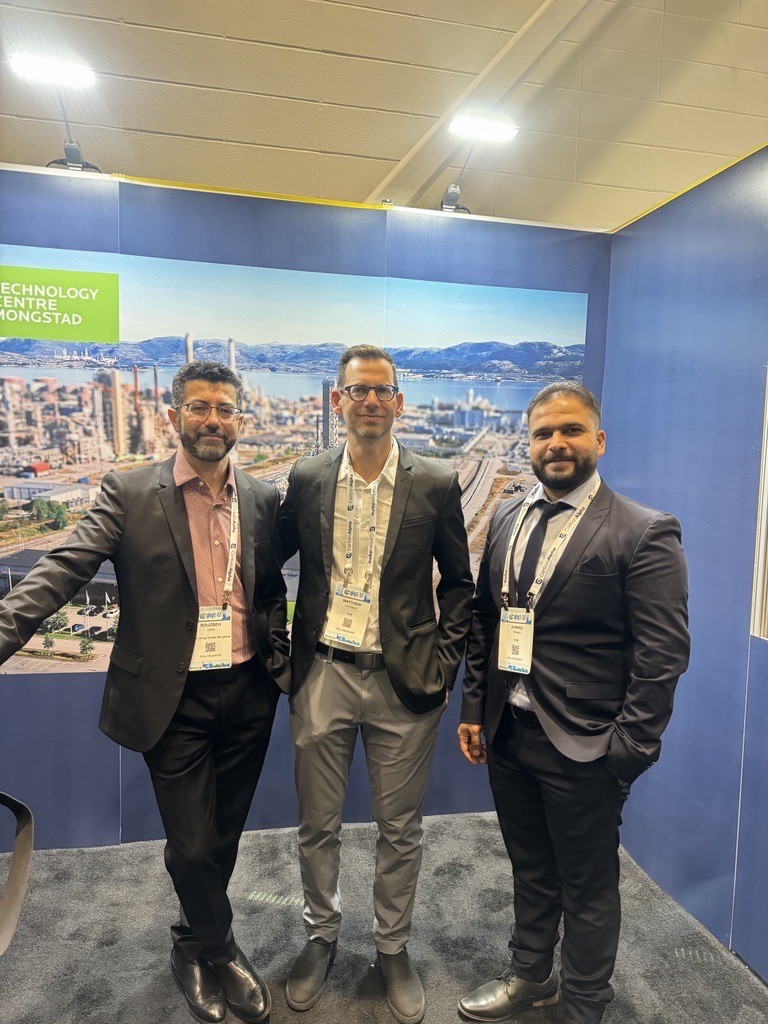
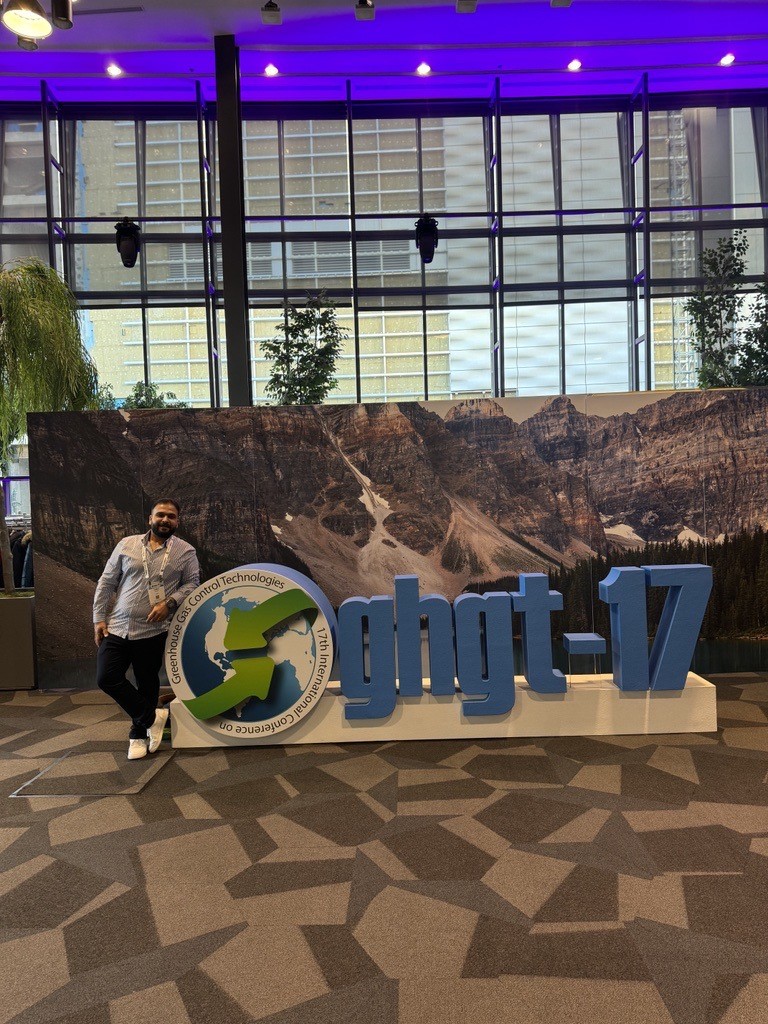
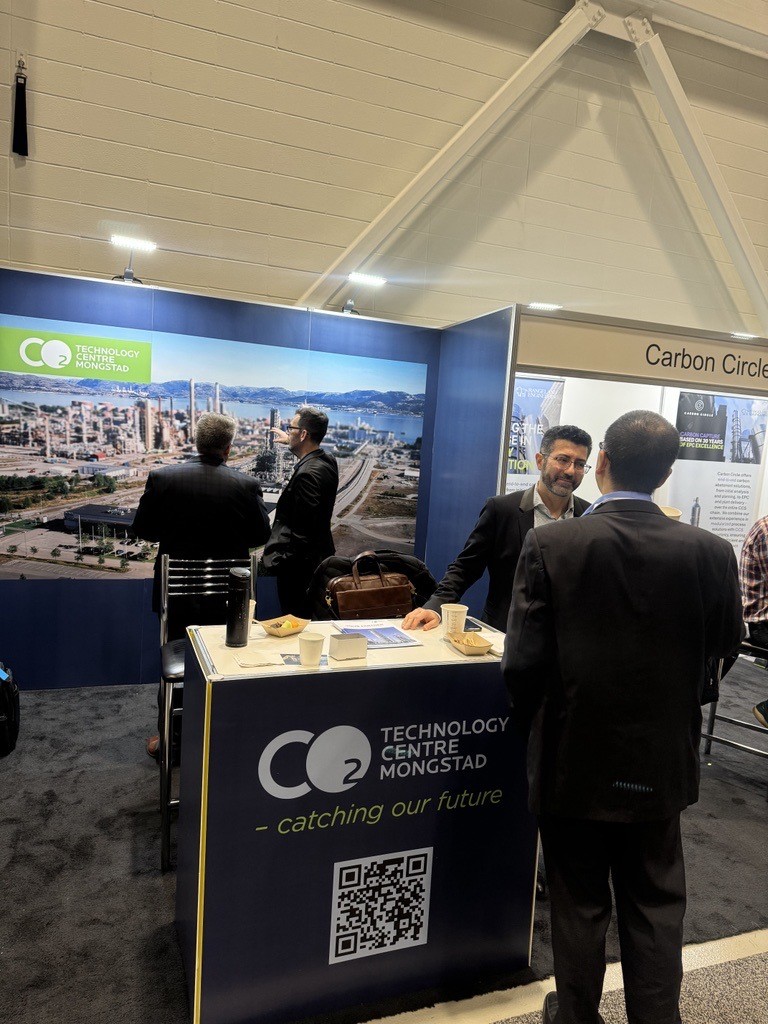
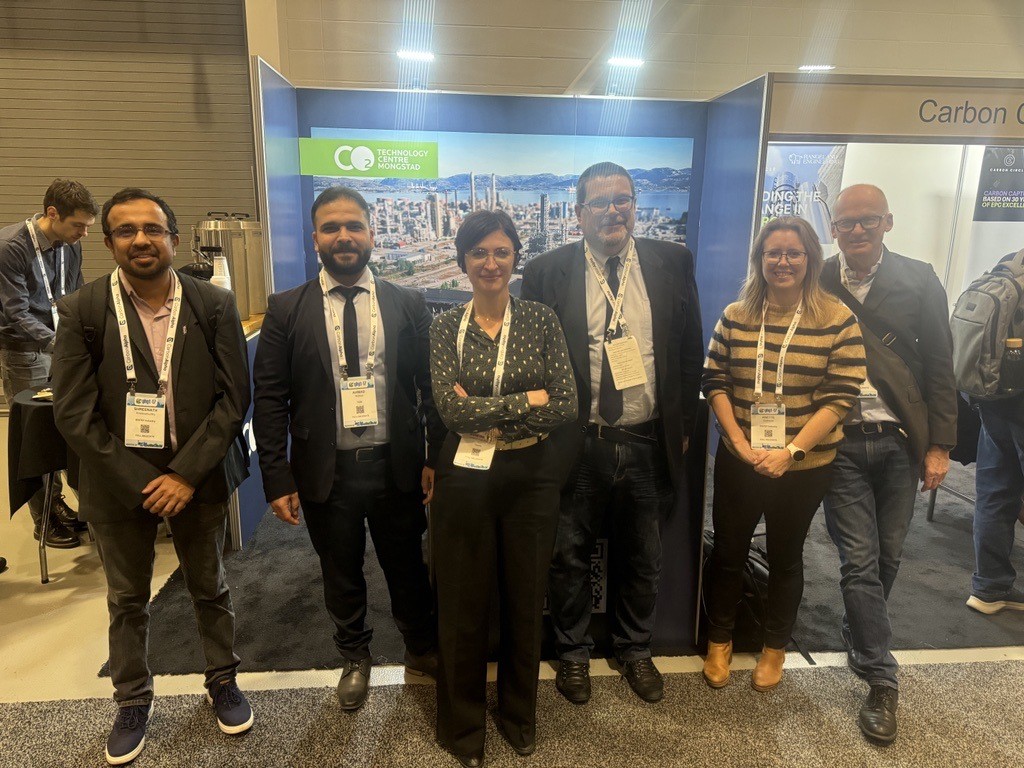
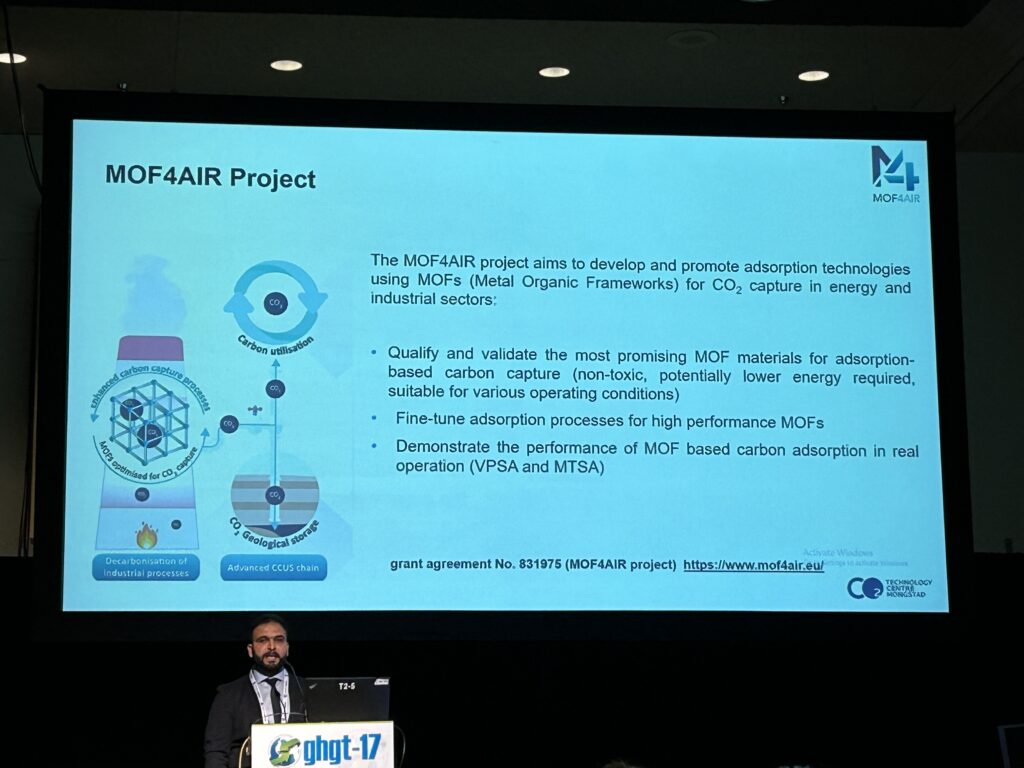
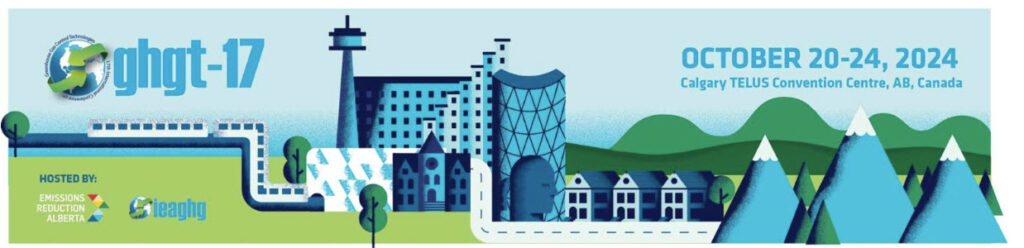
Great activity for TCM at GHGT-17 in Calgary.
A “Packed House” with TCM on Stage
Collaborating with industry and research partners, including Equinor, Gassnova, ION Clean Energy, InnoSepra, NIVA, Shell, SINTEF, and TotalEnergies, TCM made a substantial contribution to GHGT-17. The team delivered five oral presentations and displayed three posters, each drawing notable interest.
“The interest in these presentations was immense,” Matthew remarked. “In several sessions, the room filled to capacity, with lines forming outside and some attendees standing at the back. The level of engagement was thrilling for us as presenters, sparking valuable discussions afterward.”
Rouzbeh added, “We are now actively following up with contacts made at the event, including both former TCM clients and new companies interested in collaborative CO2 capture technology development and testing.”
Highlighted Papers and Posters at GHGT-17
The following papers and posters were presented by TCM and its collaborators at GHGT-17:
- Design, Development, and Validation of Analytical Methods for Measuring Degradation Products of CESAR1 Solvent by LC-MS/MS
- Pilot-Scale Testing of Metal Organic Frameworks (MOFs) for Post-Combustion CO2 Capture at Technology Centre Mongstad (TCM)
- CESAR1 Solvent Degradation in Pilot and Laboratory Scale
- Using a Dynamic Modeling Tool to Ensure the Safety of Drinking Water Sources near an Amine-Based CO2 Capture Plant
- Demonstration of the Latest Advancements in CANSOLV CO2 Capture Technology at TCM
- Transformational Sorbent-Based Process for Substantially Reducing CO2 Capture Costs
- Demonstration of ION’s Novel Capture Solvent (ICE-31) at TCM’s Amine Plant with Results on Transformational Deep Decarbonization and CO2 Capture Co-Benefits
- 18 Years of Public-Private Partnership for Developing Post-Combustion CO2 Capture at Technology Centre Mongstad in Norway
For more details on the presentations, visit our news page:
“It’s all about the people”
“Modification is a small department with highly skilled people who rarely say “no” and often say “yes”.
The modification team have to rely largely on themselves to deal with the day-to-day challenges – because there aren’t many others to ask. But in my experience, when people are given responsibility, they step up. Leadership is about showing respect and trust!
The Modification Team
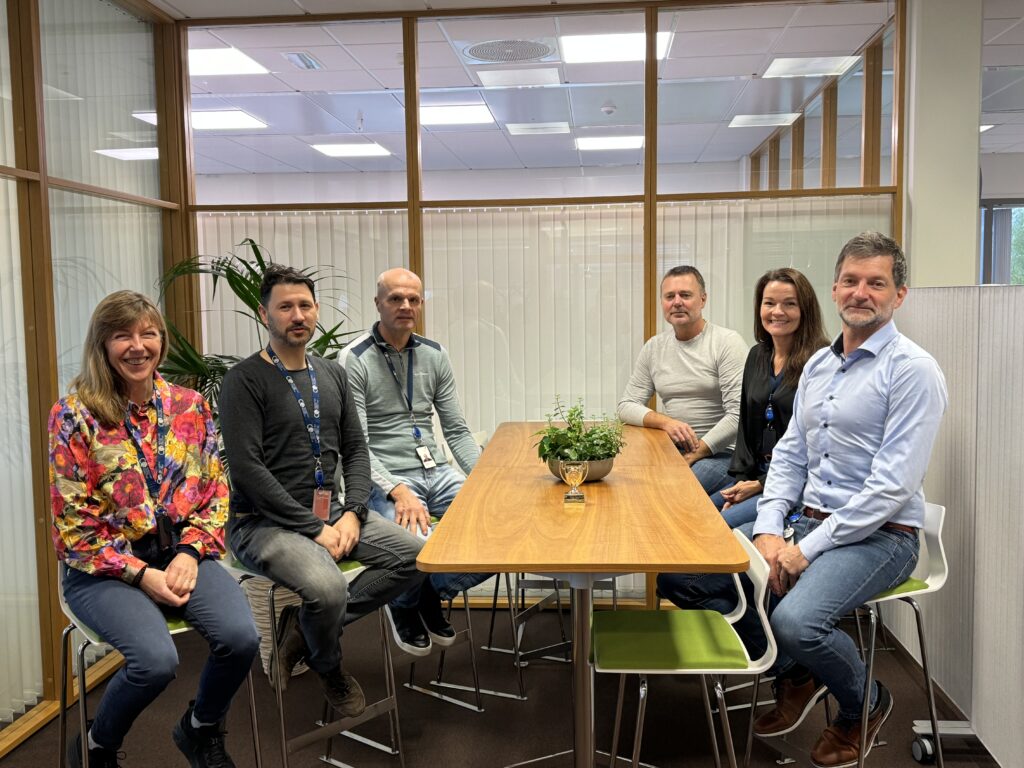
Kjetil Hantveit became head of the modification department at TCM in 2014. Prior to that, he had worked for almost ten years at Equinor on several large oil and gas projects in the North Sea and onshore, including the Mongstad refinery and the construction project for the new technology centre.
“I was used to having a large team of experts around me and knew that wouldn’t be the case at TCM. But I was intrigued by the many and varied technical challenges and the responsibility that comes with putting my name to the solutions that the team collectively decides are best for each operation or project.”
His team includes Magne Tresvik, an electrical engineer who, in addition to planning and installing all electrical systems, also ensures that documentation and drawings are kept up to date. Roger Solheim is the site supervisor who co-ordinates all modification work with the engineering and operations departments and analyses HSE risks. Istvan Szabo is a PDMS designer who continuously updates the plant’s 3D model to incorporate modifications using the Plant Design Management System (PDMS), now better known as E3D. These four form the core of Modifications. They also benefit greatly from the services of Elisabeth Nilsen as document controller and Jorunn Hovda, who works in finance and administration with budgeting and monitoring all orders and requisitions. The department also manages two people who work permanently at TCM with scaffolding and installation work.
“What sets this team apart is their extensive experience in knowing what’s needed to ensure that every test campaign planned at the Amine Plant and the site for Emerging Technologies can be carried out in accordance with the customer’s wishes and conditions. Among the employees, Istvan is the youngest, having started his career at TCM in 2015!”
“What is a typical working day like for you and your team?
“Typically, we receive proposals from the operations and engineering departments for changes that need to be made to the structures as part of a campaign. Our job is to evaluate possible improvements based on a study of the specific technology being tested, such as pipe dimensions and other technical issues that naturally arise. Our technical assessments lead to a solution, which is then estimated in terms of cost. Once the basis for modifications has been decided, our role is to ensure that the changes on paper are carried out on the plant. We make agreements with suppliers for welding and electrical work, and make sure they do what we’ve agreed. We then carry out tests before handing over the installations to operations. In addition, we maintain a dialogue with Business Development when potential customers have questions about what modifications are required for a possible technology test at TCM.
“How do you work with other departments at TCM?
“I can honestly say that we don’t face any challenges in terms of collaboration at TCM. We’re a small organisation with specialised expertise in CO2 capture, and we’re used to working across departments to solve problems that may arise in connection with a test campaign. The feedback we get from our customers shows that the team spirit at TCM is highly appreciated.
Two test campaigns have started at TCM this autumn: Honeywell at the amine plant and Svante at the Emerging Technologies site.
“How have these campaigns required adaptations or modifications to the facility to allow the customers to effectively test their technologies?”
“The Honeywell campaign involves the installation of new and better measuring equipment, which will remain permanently at the amine plant after the campaign. For Svante, we have been involved with their people in the assembly and installation of the modules that will be used and tested to ensure that they work as intended. I’m optimistic that these campaigns will go smoothly.
“TCM’s amine plant has been in operation since 2012. How are modification involved in the planning and implementation of technical upgrades to the plant?”
“Over the years, Modifications has played an active role, including the installation of a new filter (BD) in the plant to reduce the amount of particles in the flue gas. We’ve also made several improvements both inside and outside the absorber tower. We are currently working on a study of possible modifications to adapt the plant to the new composition of the flue gas we receive from the refinery’s heat plant”.
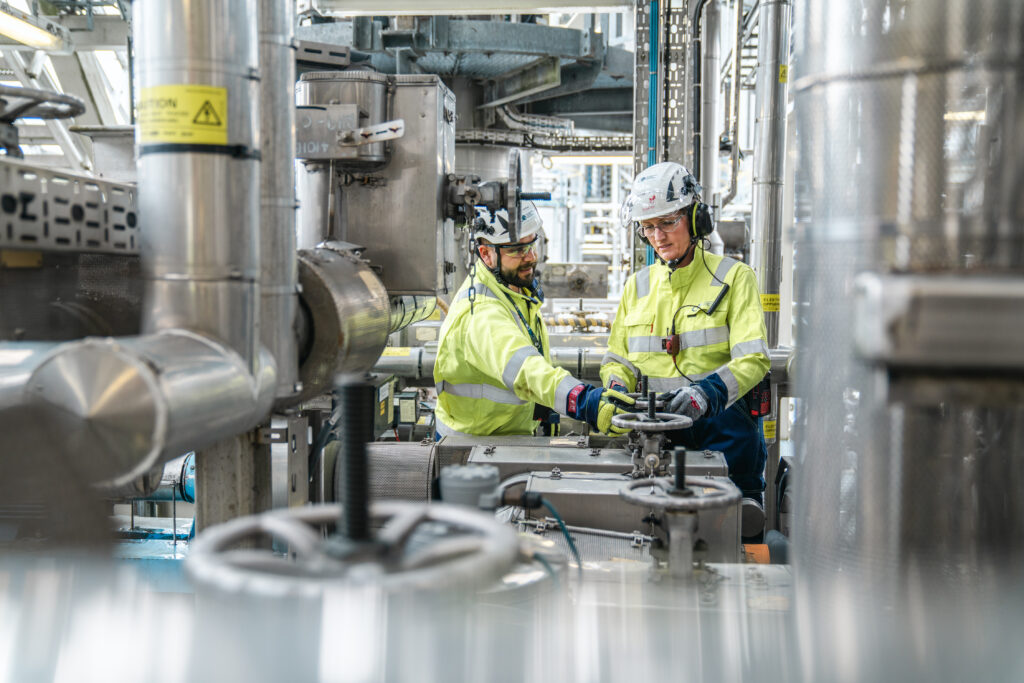
“How do you see new technologies contributing to more efficient operations in the coming years?
“For our part, we are already seeing the benefits of AI, for example in calculating the dimensions of equipment. However, we need to make sure that we, as humans, understand the basis for the results that appear on the PC, so that we don’t make bad investment decisions. We’ve also acquired equipment that allows us to visualise planned changes to the plant before they are physically made. So yes, we’re constantly adopting new technology to do the job better and with fewer people than before.
“TCM is in transition. How does this affect Modifications? Are you optimistic about the future?
“The work being done now to strengthen the sustainability of TCM’s operations is great – because with this transition we have all the conditions to continue as the world’s largest and most flexible CO2 capture test centre. Change has played a central role in the establishment of the Site for Emerging Technologies, and I believe we need to focus even more on becoming the site of choice for testing new and innovative capture methods. The expansion with new areas and increased capacity will provide plenty of work not only for us in Modifications, but for the whole of TCM. Most importantly, we must continue to be a company with great opportunities for professional development and a strong internal culture. Those of us who work at TCM are privileged, both because we do very important work and because the working environment is exceptionally good. This gives me confidence for the future!
Honeywell`s CO₂ Capture Solvent Technology To Be Tested at TCM
An advanced solvent for post-combustion carbon capture developed through a partnership involving the University of Texas at Austin (UT Austin) and Honeywell is set for engineering-scale testing in October at the Technology Centre Mongstad (TCM), the world’s largest carbon capture test facility located in western Norway.
The new Honeywell/UT Austin technology is an advanced solvent designed to capture carbon dioxide (CO2) found in flue gases generated from power, steel, cement and other industrial plants. The technology is the product of a multi-year cooperative agreement that was supported by the U.S. Department of Energy Office of Fossil Energy and Carbon Management and managed by the National Energy Technology Laboratory (NETL).
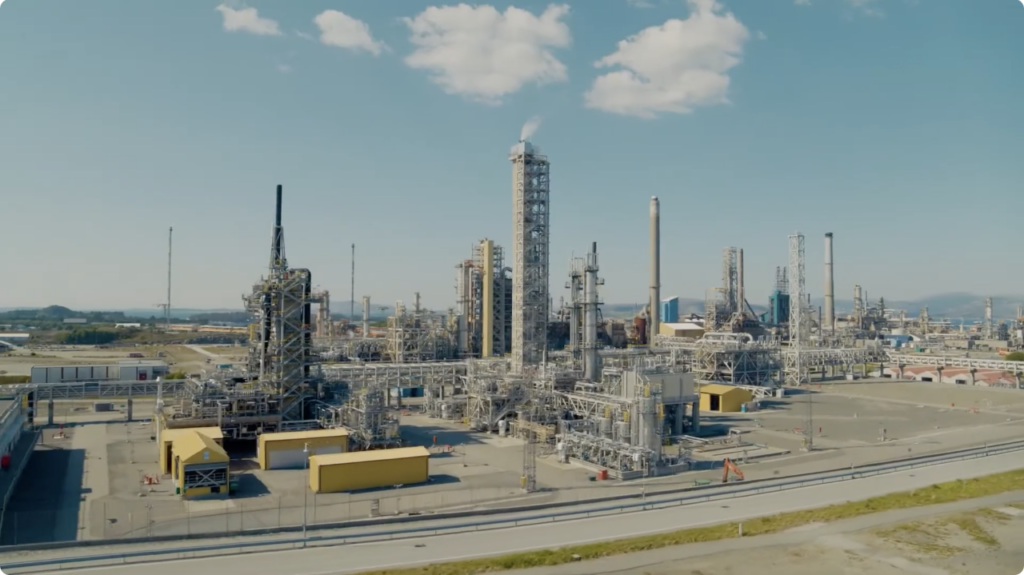
Engineering-scale testing
Engineering-scale testing enables technology developers to understand the technical and performance risks of the technology and validate scaling factors that will enable design of future commercial-scale systems.
In the technology to be tested, CO2 is absorbed into an amine solvent and then sent to a stripper where it is separated from the solvent. This CO2 would then be compressed for geological sequestration or used for other purposes. The technology is designed to be retrofitted within existing plants or included as part of a new installation.
The engineering-scale testing of the solvent technology beginning in October builds upon successful pilot-scale testing performed at the National Carbon Capture Center in 2023 and at UT Austin’s Separations Research Program plant in 2022. That testing totaled approximately 7,000 hours.
A technology solution to capture 95% of a facility’s CO2 emission
The lessons learned through long-term field tests, along with complementary bench-scale studies on mitigating solvent oxidation, has led to a technology solution to capture 95% of a facility’s CO2 emissions while managing non-CO2 emissions and reducing operating costs and environmental impacts relative to state-of-the-art carbon capture approaches.
According to the International Energy Agency, carbon capture can contribute about 20% of reduction in CO2 emissions needed to prevent uncontrolled global warming and achieve zero emissions targets. Testing and validation of CO2 capture technologies is an important part of the solution to the climate crisis.
TCM is the world’s largest and most flexible test facility for developing CO2 capture technologies and a leading competence center for carbon capture. It features unique scale and flexibility to simulate real-world conditions for post-combustion capture.
Ismail Shah, TCM’s managing director, said “TCM is glad to welcome Honeywell to our amine facility. We are looking forward to testing and verifying Honeywell CO2 capture technology and efficiently achieving campaign objectives by offering TCM capabilities. Together we will support accelerating commercialization of Honeywell’s technology.”
Large-scale, real-world testing fills an important gap between small-scale pilot projects and full-scale deployment of technologies. The TCM facility provides the ability to test a wide range of technologies on industrial flue gases as well as access to a comprehensive data set that can be used for comparison with similar or other technologies.
Honeywell
Honeywell is an integrated operating company serving a broad range of industries around the world. The business is aligned with three megatrends – automation, the future of aviation and energy transition. Honeywell helps organizations solve complex challenges, providing solutions and innovations through aerospace technologies, industrial automation, building automation and energy and sustainability.
UT Austin
UT Austin collaborates with a diverse array of partners — including entrepreneurs, investors, technology incubators, and large enterprises — and generates more than 150 new technologies each year, providing abundant and varied opportunities for industry collaboration.
NETL
NETL is a DOE national laboratory that drives innovation and delivers solutions for an environmentally sustainable and prosperous energy future. By using its world-class talent and research facilities, NETL is ensuring affordable, abundant, and reliable energy that drives a robust economy and national security, while developing technologies to manage carbon across the full life cycle, enabling environmental sustainability for all Americans.
“Capitalizing on Norway’s Leadership in CCS”
“As carbon capture and storage (CCS) gains momentum globally, Norway has established itself as a frontrunner. TCM and Norway’s strong technology environments have a unique opportunity to build on this position in the years to come.”
“Wenn jemand eine Reise tut, so kann er was erzählen.” In English, this well-known quote from the poet Mattias Claudius roughly translates to, “When someone goes on a journey, they return with stories to tell.” TCM’s Managing Director, Muhammad Ismail Shah, has undertaken three longer international trips in recent months and is brimming with impressions he’s eager to share.
The most recent trip was to India, the world’s most populous country, where the government is aiming to reduce annual CO2 emissions of 2.9 gigatons to net zero by 2070 — all while tackling widespread poverty.
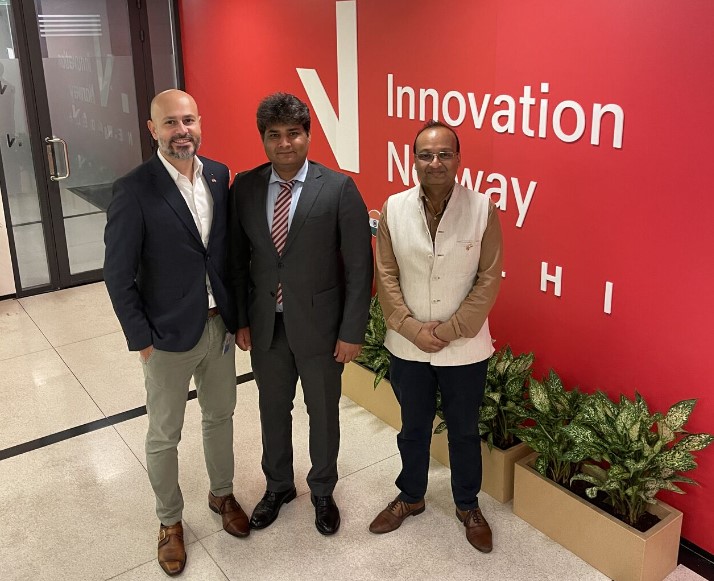
During his visit to India, Mr Shah was introduced to stakeholders from Govt., energy and heavy industries, facilitating fruitful discussions on the latest innovations in carbon capture, opportunities for technology transfer, and the critical role of multilateral partnerships in addressing global challenges. Photo: Innovation Norway
At the Start of a Long Climate Journey
“India is at the start of its journey to reduce emissions, but both politicians and industry leaders understand there is no alternative,” says Shah. “That’s why it was so inspiring to meet with key leaders of energy supply companies and emission-heavy industries and talk about Norway’s Longship project and the role TCM plays in developing technologies that make it possible to realize this and several other global CCS projects.”
During his well-organized week-long stay, coordinated by Innovation Norway’s local representative, Shah also attended an event at the Norwegian Embassy in Delhi, where the Norwegian Parliament’s Foreign Affairs and Defense Committee met with prominent Indian politicians and business leaders.
”What makes India particularly interesting for Norway is the trade agreement signed between the two countries this spring, which eliminates tariffs for over 90 percent of the goods we export. For TCM, this agreement lays the foundation for developing collaboration on technology, which will be crucial for India to reduce its enormous climate emissions in the long term.”
The Momentum of CCS in the USA
While Shah sowed seeds on his trip to India that will take time to sprout, his participation in the annual conference of the U.S. National Energy Technology Laboratory (NETL) was of a different caliber. Together with Chief Technology Officer Matthew Campbell and Business Development Manager Rouzbeh Jafari, he met around 1,500 participants from leading CCS communities in the U.S. and Europe.
”I participated in a panel discussion with representatives from American test centers and exchanged interesting views on how we can contribute to the further development of both mature and new carbon capture technologies. Once again, the experience was that TCM is held in high regard, both for our excellent facilities and the support we provide technology developers in planning and conducting test campaigns.”
At the NETL conference, the TCM delegation met with companies considering testing at Mongstad. These meetings were a key step toward commercializing new technologies.
”We also had good discussions with clients who, over the years, have conducted test campaigns at the amine plant or the Site for Emerging Technologies, and who may return to Mongstad. In addition, we enjoyed a pleasant dinner with the leadership of the CCS department at the U.S. Department of Energy (DoE), which is a strong contributor to funding the development of innovative capture technologies.”
Shah noted that the impression is that the Biden administration’s significant focus on technology development through the Inflation Reduction Act (IRA) is likely to continue regardless of the outcome of the November presidential election, as it has strong support in Congress. ”In the U.S., CCS as a tool in the climate fight has momentum that is hard to find elsewhere in the world”, Shah emphasizes.
Awaiting Investment Decisions So, what about our own continent – Europe?
Muhammad Ismail Shah and Communication Manager Liv Lønne Dille gained more insight into this during the Carbon Capture Global Summit in London. The conference gathered participants from all the major CCS players worldwide, where TCM had a well-visited stand.
“The professional environments in Europe are undoubtedly working hard to bring cost-effective technologies to market. However, while major projects in Norway and Denmark are already up and running, and projects in the UK are nearing investment decisions, most other European countries continue to face delays due to a lack of critical investment,” Shah highlights.
”Once this ‘bottleneck’ is resolved, I’m confident it will unlock a large market for TCM’s services, such as technology refinement and personnel training for operating CCS plants. That’s why it’s incredibly important that we in Norway succeed with the value chain for capturing, transporting, and storing CO2, thus showing Europe that CCS can be implemented in practice.”
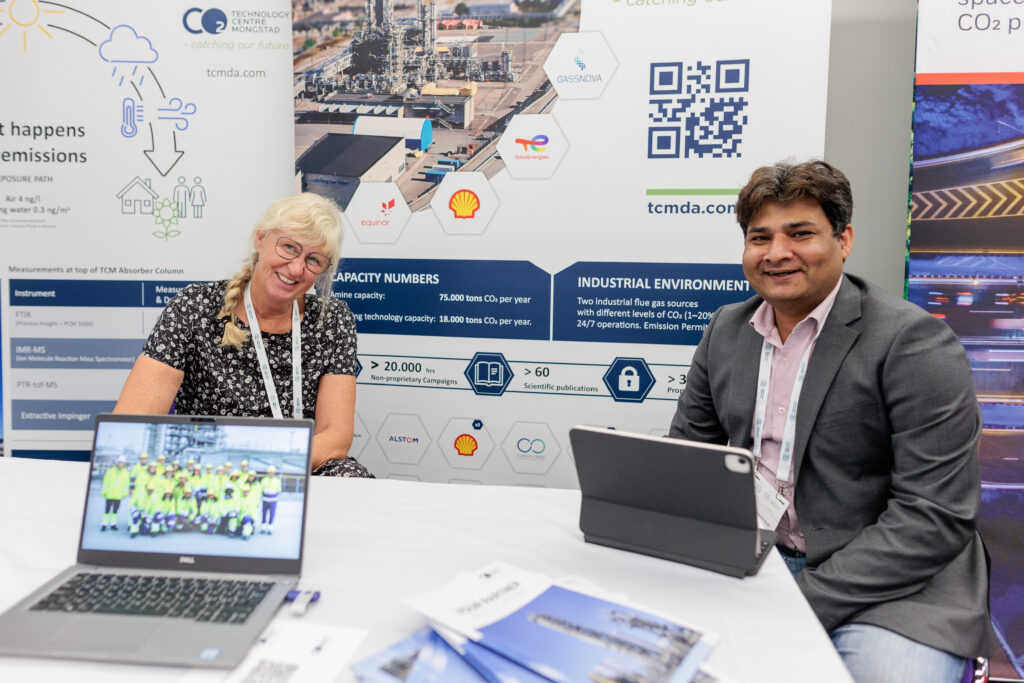
We look forward to sharing our knowledge with the world’s CO₂ capture experts
From 20 to 24 October 2024, the world’s CCS experts will meet at GHGT-17 in Calgary, Canada. TCM is pleased to contribute to the conference with five oral presentations and three poster presentations.
The titles of the GHGT-17 papers and short summaries of the next four are described below. The first three presentations can be found here.
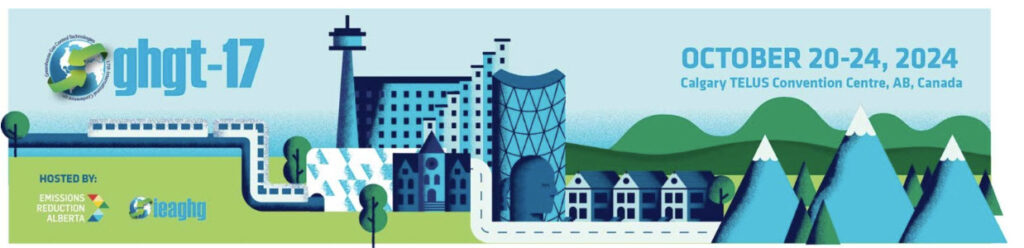
Using a dynamic modelling tool to ensure the safety of drinking water sources in the vicinity of an amine-based CO2 capture plant. (Presenter: NIVA)
The article presents a dynamic modeling tool designed to help industries prevent contamination of nearby water sources by carcinogenic nitrosamines (NSAs) and nitramines (NAs) from amine-based CO2 capture plants. The study describes the formation of NSAs and NAs in the air from escaped amines, the local dispersion conditions, and their eventual deposition in water sources. Preliminary applications of the tool at different sites, including a Norwegian lake, show potential risks and seasonal fluctuations in NSA and NA levels. The tool incorporates complex processes and is being improved with a new atmospheric module validated by airborne measurements. It can also evaluate technological measures to reduce amine emissions and subsequent contamination.
Demonstration of latest CANSOLV CO2 capture technology advancements at TCM (Presenter: Shell)
This article details the successful 6-month demonstration of Shell Global Solutions’ latest CANSOLV technology at the Technology Centre Mongstad (TCM). Results to be shared by Shell Cansolv during this conference.
Transformational Sorbent-Based Process for a Substantial Reduction in the Cost of CO2 Capture (Presenter: InnoSepra)
This paper presents lab and pilot scale test results and a techno-economic analysis for a sorbent-based CO2 capture process. At the conference, InnoSepra will also share some results from the tests at TCM with the 2nd generation process.
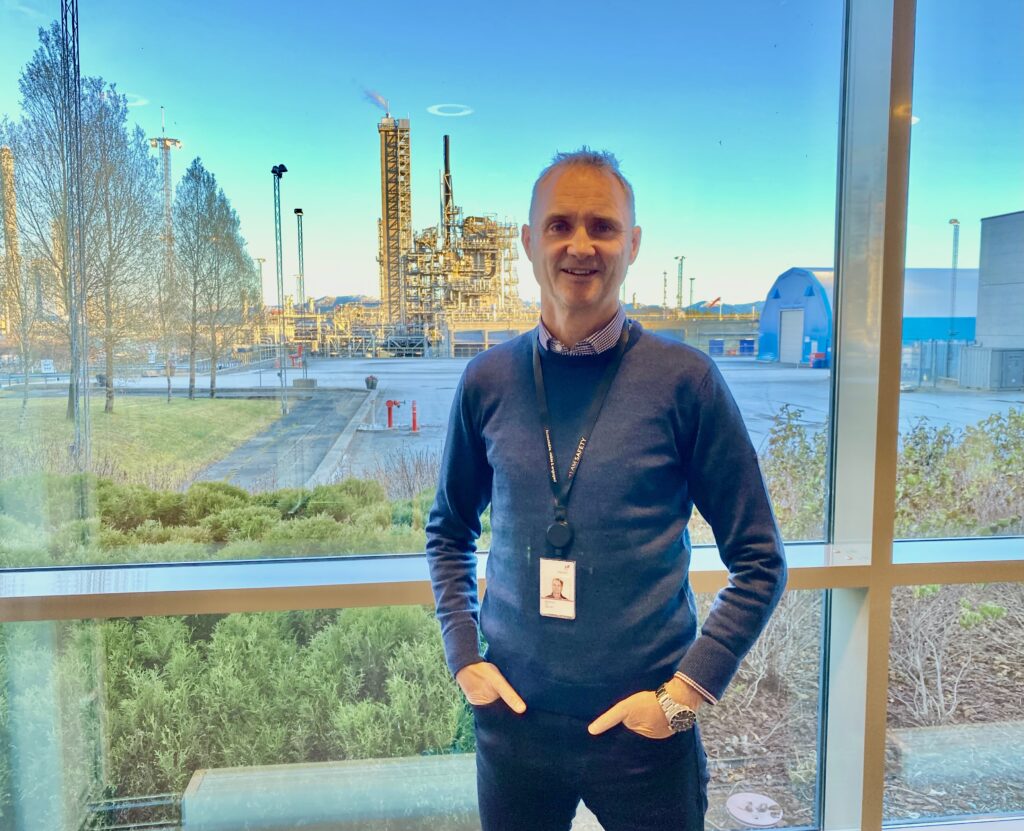
Demonstration of ION’s Novel CO2 Capture Solvent (ICE-31) at TCM’s Amine Plant with Transformational Deep Decarbonization and CO2 Capture Co-Benefit Results (Presenter: ION)
ION Clean Energy demonstrated their novel amine-based solvent system (ICE-31) at Technology Centre Mongstad. This paper presents the results of a 4-month testing period at TCM, which will be shared by ION during this conference.
If you would like to test your technology at TCM, please contact us.