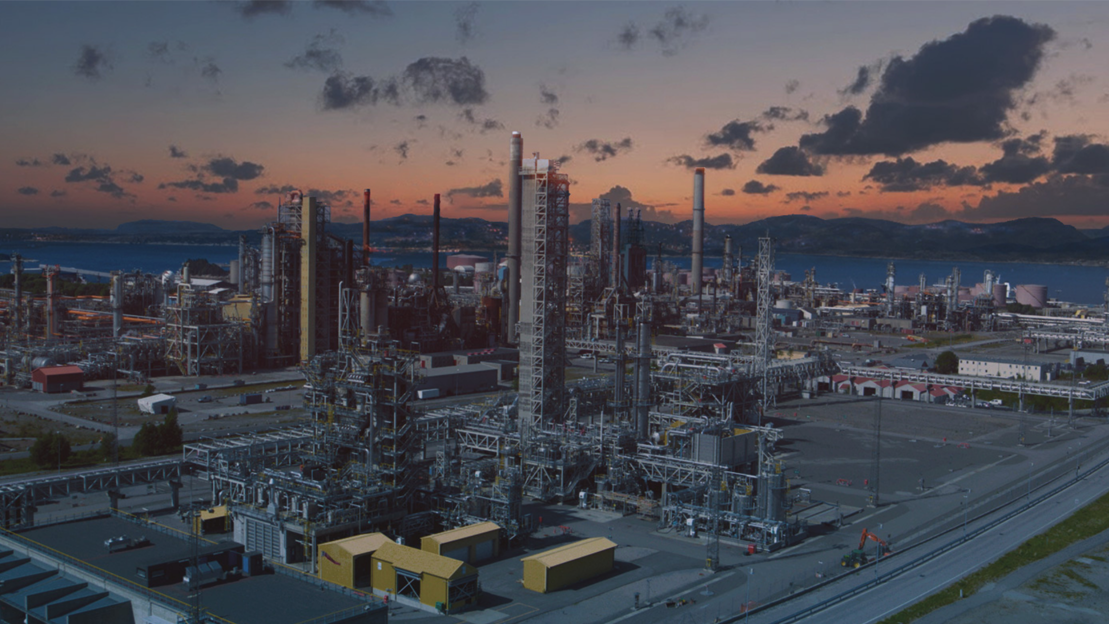
20.04.2022
– Aker has a lot to thank TCM for
When I look at everything that is now moving in the market for carbon capture and storage, I can only be optimistic. That’s what Aker’s «grand old» industrial builder and head of the gas technology business, Oscar Graff (69), says.
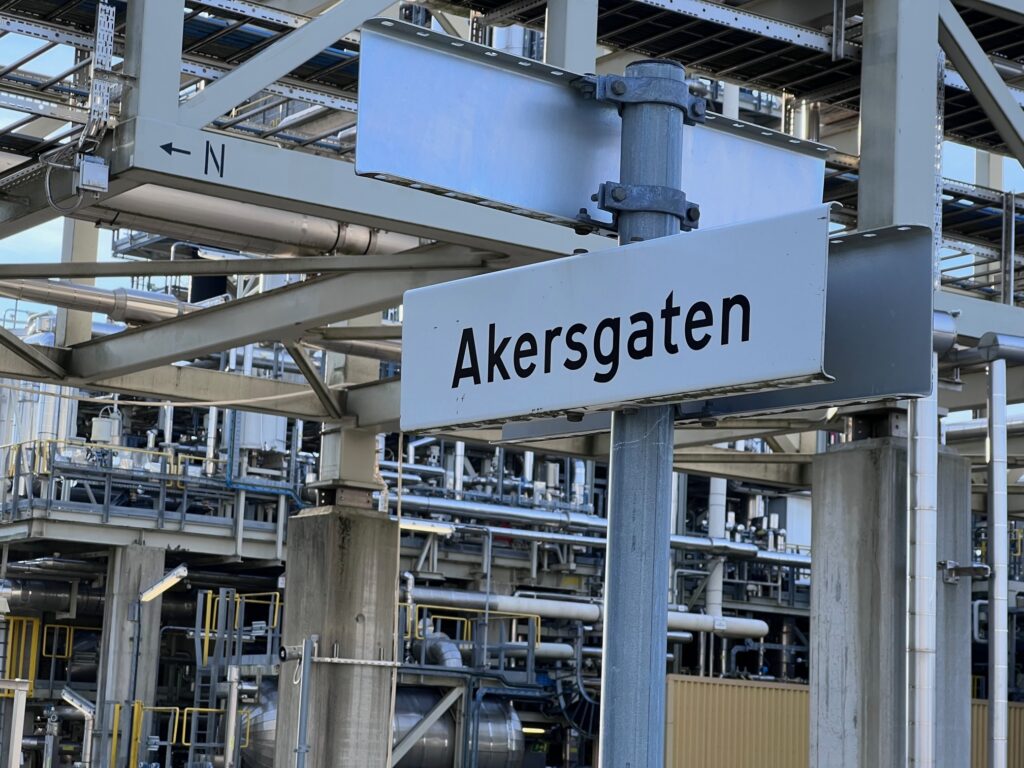
Until he retired two years ago, he spent all his time on technology and project development, with construction and then testing at TCM’s plant as one of the highlights of his career. He still follows the CCS industry with a watchful eye, among other things through his board position in Aker Carbon Capture.
Aker was early out with CCS projects
– For me, it is basically about being able to go to the grave in the knowledge that there is both hope and possible to save our common planet. The UN’s latest climate report is frightening reading. The climate challenges are gigantic, and both the UN and the IEA leave no doubt that carbon capture and storage, together with the transition to renewable energy, is an absolutely necessary part of the solution. My descendants should know that my generation has also understood the seriousness and done the best we could to develop technology that makes it possible to avoid the world’s biggest environmental disaster.
According to Graff, Aker was out early out with projects, first with natural gas and permanent storage of CO2 in the Sleipner field in 1996. The experiences with the use of amine as a tool for removal of CO2 in this and several other natural gas projects, indicated that this was also applicable in the most other industries – with necessary adjustments. The difference between removing CO2 from natural gas and flue gas is mainly that the flue gas has a low pressure (i.e. treatment of large volumes), and that it can contain oxygen and other components, which can have a negative impact on the amine solution.
Collaboration with SINTEF and NTNU
– In 2005, we landed a strategy for investing in post-cleaning with amine technology. Post-cleaning was applicable and could be used for most industrial flue gases. We defined 15 improvement points for CO2 capture with this technology. At the same time, we established a team of experts which has been the core in our developments. Collaboration with the research communities at NTNU and SINTEF was an important prerequisite – we needed research partners who could do analyzes in the laboratory, and we needed our own test facilities to verify the solutions.
In 2008, SOLVit was launched, an eight-year research program between Aker Clean Carbon, NTNU and SINTEF, and with Gassnova as a financial cocontributor. The same year, Aker built its mobile test unit (MTU) in Verdal, and at Tiller in Trondheim, a new test facility was put in place. The purpose of the investment was to develop technology with less energy demand and lower emissions. In the winter of 2008 – 2009, the MTU was first used for testing and measuring CO2 capture from a gas power flue gas in Risavika near Stavanger. The world’s first, comprehensive emission measurement from amine plants to air was carried out.
– The goal was to test the efficiency of using the amine solvent both in terms of energy consumption and emissions to air, and we succeeded quite well.
Went out into the world with MTU
The MTU was taken to Scotland and on to Alabama in the United States for testing with other types of flue gas sources. These experiments also led to significant experience and great progress. Among other things, they developed and patented a solution that stopped the formation of «mist» in emissions to air. «Mist» are small water droplets that the amine adheres to, and which can lead to high amine emission. This was followed by a number of test campaigns with various flues gases, among others; gas and coal power plants, cement factories and in connection with waste incineration. The main focus was to make the technology suitable for capturing industrial emissions. Recently, the MTU has been testing on blue hydrogen production at the Preem refinery near Gothenburg and is presently testing at the Polchar facility in Poland.
During the research program, Aker in 2009 was awarded a contract with TCM to design and build the amine plant and then test its technology in an industrial scale. In this connection, the MTU was transported to Mongstad for parallel testing.
– This was an exciting project for us. The big question was how the technology would work in an upscale setting, and the size of emissions under such conditions. We handed over our predicted data for plant performance to TCM and were strong in the belief that this will work as intended. It was still incredibly satisfying when, after the demonstrating, we could say that our calculations and predictions had been spot on, says Graff.
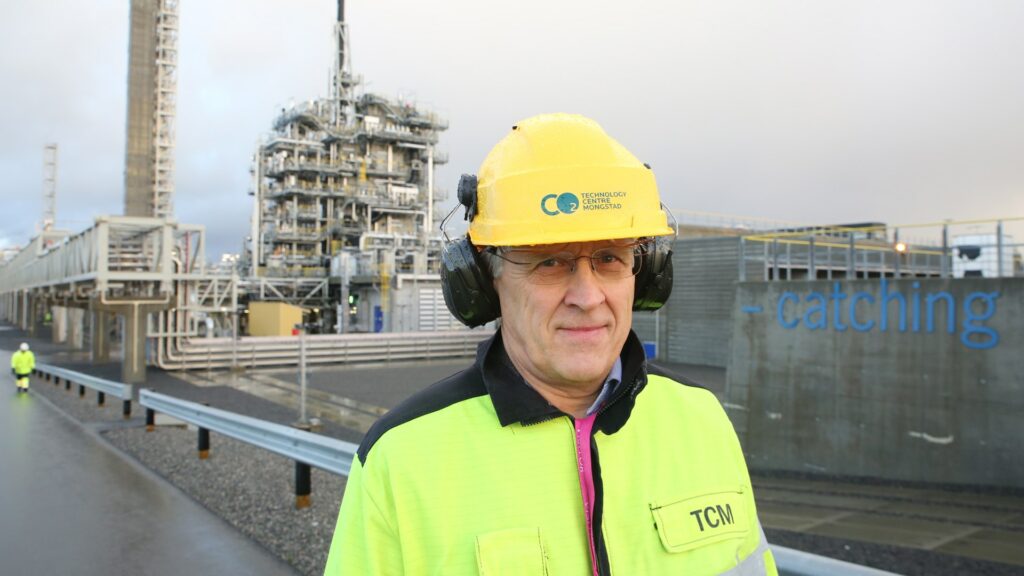
Oscar Graff has led Aker’s business to CCS for a lifetime. – We have a lot to thank TCM for.
Lay the groundwork for breakthrough at TCM
Aker’s commitment through the successful construction of the plant and testing at TCM laid the foundation for a solid market breakhrough in CO2 capture. As one of four possible suppliers, the company was invited to test the technology at Heidelberg Materials in Brevik. Their conclusion was that Aker had the best technology for the capture project. Great emphasis was also placed on the fact that Aker had built the plant at Mongstad, and that the company had completed a successful 2-year test with the MTU in Brevik and had built up broad expertise. The EPC contract was entered into in 2020, and the plant will be ready for capture and liquefaction of 400,000 tonnes of CO2 annually in 2024. The CO2 will be transported liquid form in ships for permanent injection and storage in rocks beneath the North Sea.
– We were also invited by ScottishPower to take part in a national CCS competition in the UK for the annual capture of two million tonnes of CO2 in connection with one of Europe’s largest coal power plants near Edinburgh. We were the first to capture CO2 in UK with our MTU. After FEED execution, long term testing with the MTU and documenting efficiency with our solvent, the authorities concluded in 2011 – following a recommendation from ScottishPower – that our technology was preferable. However, the project did not go ahead, and the power plant was shut down some years later, but the process itself was instructive and gave us learning and faith in what we had to offer.
«Just Catch» in the Netherlands
Over the years, Aker has refined its concept for the delivery of compact and standardized facilities for capturing CO2. With «Just Catch», costs and construction time are significantly reduced at the same time as the area requirement is significantly less than for conventional facilities. In 2019, a contract was entered into between Aker Solutions, then with Oscar Graff as head of CCS, and Dutch Twence, which owns and operates a large waste sorting and incineration plant in Hengelo near the border with Germany. When the plant is completed in November next year, after only 18 months of construction, 100,000 tonnes of CO2 will be captured and liquefied annually from the waste incineration flue gas. The catch capacity is slightly larger than at Mongstad, but the plant needs less than 10 percent of the area.
Pioneering work
– The module based capture plant for waste incineration in Hengelo and the large-scale plant for cement in Brevik will be first of its kind in the world, so you can rightly call this pioneering work.
In Hengelo, the CO2 will be transported chilled and in liquid form for use in local greenhouses, where it replaces the use of fossil CO2. – That in this way a project is realized that includes CO2 utilization, is both fun and important.
TCM – a large laboratory
Oscar Graff emphasizes that Aker would not have reached this far with its investment in CCS without TCM. In his eyes, TCM is a large laboratory, not least characterized by the facility’s great flexibility.
– During the planning of the facilities at Mongstad, the size and flexibility of the plant was the subject of discussion. It was expensive, but the experience after ten years of operation is that the investments were right and necessary. For our part, it has provided very valuable experience, both in the terms of design and production of modules that were assembled at Mongstad, and testing of our solvent. We learned an incredible amount about how we could commercialize the entire value chain of CO2 capture, and from that we are harvesting now.
He describes the collaboration between his own engineers and the staff at TCM as very good. – In the test phase, we saw, for example, that the choice of material for some parts of the amine plant had not been optimal, but there we jointly found new and better solutions. Actually, we were quite surprised at how easy it was to achieve stable operation and capture over time. That the plant now has been in operation for 10 years, and that it is still just as relevant, is a seal of quality for both TCM and Aker, says Graff.
TCM’s professionalism a success factor
He makes no secret of the fact that Aker was concerned that TCM’s business model implied that competing technology suppliers would be allowed to test at the amine plant after they had ended their campaign in 2014.
– However, it has turned out that TCM has managed to comply with the strict agreements that were into confidentiality about the secrets we shared with selected people about the nature of the technology, and similarly later for other technology suppliers who have used the facility. TCM’s professionalism in this respect has thus been an important success factor for the business. In retrospect, we must also be able to say that it has been a strength for Aker that also other large and reputable players have invested in amine technology and chosen to test these at Mongstad. If you look at completed and planned carbon capture plants globally, the amine technology has become dominant, and will probably retain this position for many years to come.
Wish TCM the best of luck
The Aker veteran also praises TCM for the position the company has taken in the international CCS community through, among other things, sharing knowledge from open and research-based test campaigns at the facility. – I also think it is very good that TCM has now facilitated testing of new capture technologies on a smaller scale. This is very important for the entire CCS industry.
Oscar Graff believes that TCM should include solutions that ensure that CO2 captured in connection with tests at the plant is not emitted, but is permanently stored or has an industrial application. – It will be good both for the climate and for TCM.
Do not regret that it became technology
Fifty years after he started his education and long career in process and gas technology, Graff remembers the dilemma ha had when he came to Trondheim to study. Should he study at the Norwegian College of Teaching in environmental sciences, or start at NTH (now NTNU). The study advisor at NTH added the crucial word: «You know, Oscar, if you are going to contribute something that brings the world forward, you have to invest in technology.» – I have not regretted it!
Teknologisentret på Mongstad