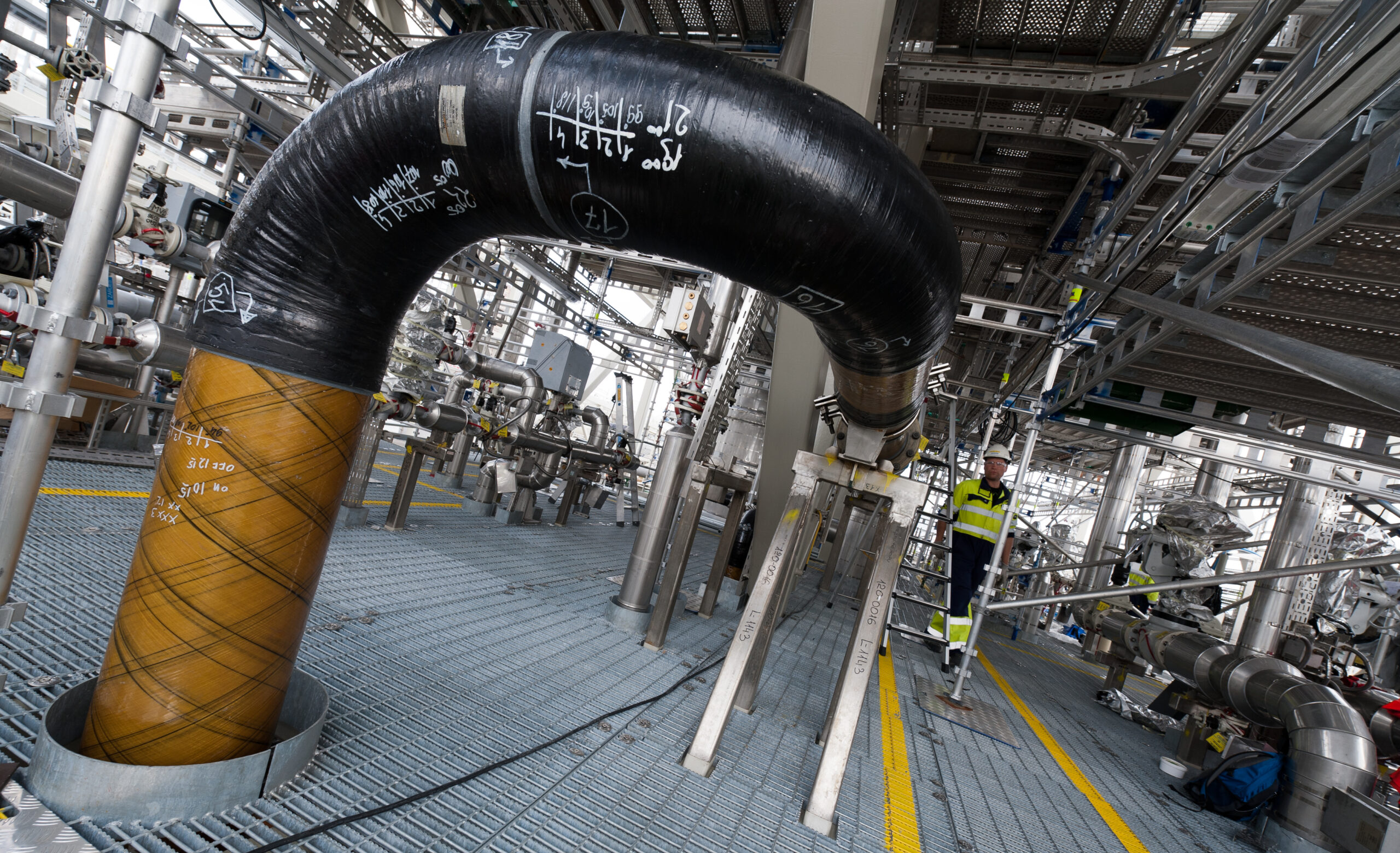
19.04.2024
An important ingredient
At the Technology Centre in Mongstad (TCM), we help technology suppliers find the best way to capture CO2.
Since it was established in 2012, TCM has supported more than 20 different technologies. Together with the technology suppliers, we have looked at how different solvents support the process of capturing CO2. TCM staff work every day to develop the capture technology. Our flexible flue gas is a key element.
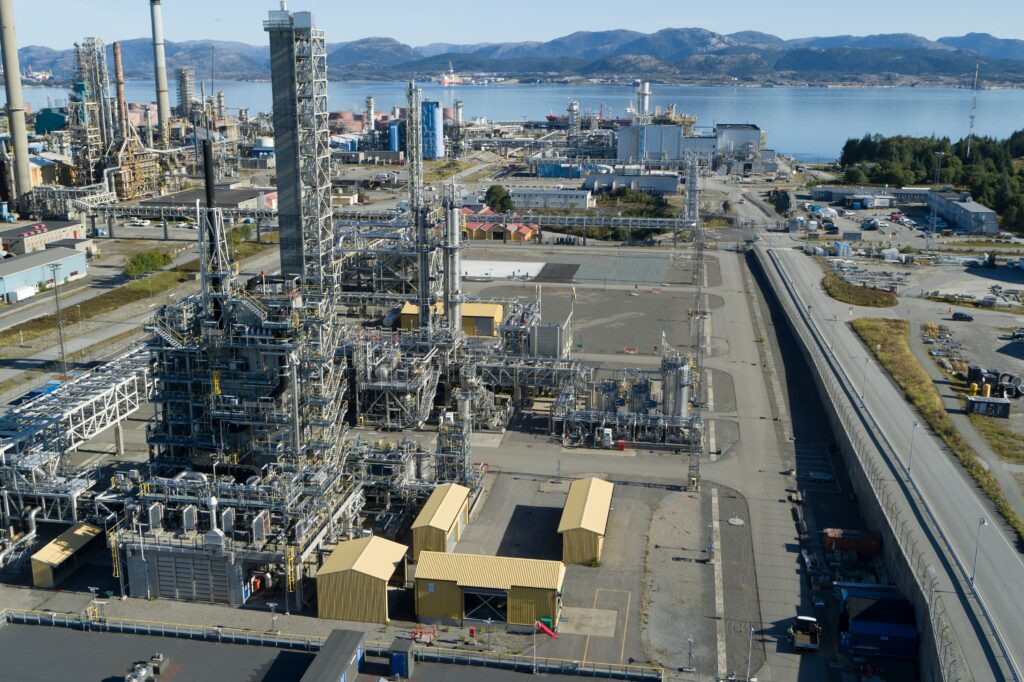
Enhancing Carbon Capture Research at TCM with Versatile Flue Gas Sources
At Technology Centre Mongstad (TCM), groundbreaking strides in carbon capture technology and emissions reduction are underway, fueled by the invaluable resource of flue gases provided by Equinor’s Mongstad refinery. These flue gases not only offer a testing ground but also a realm of possibilities for exploring diverse CO2 concentrations, ranging from 1%- 20%. Such flexibility empowers TCM to delve into a myriad of industry applications, including conditions for various industry applications, such as steel and cement type flue gases.
Traditionally, TCM has been supplied with flue gases from various sources, each contributing uniquely to its research endeavors. The journey began with the Combined Heat and Power plant (CHP), operating on a combined cycle gas turbine (CCGT), which ceased operation in 2022. This plant, fueled by a blend of natural gas and refinery fuel gas, facilitated the capture of approximately 80 tonnes of CO2/day, with a CO2 content typically ranging from 3.5 to 3.7 mole%.
An unparalleled testing environment
The transition post-2022 saw the emergence of the Mongstad Heat Plant (MHP), ushering in a new era of flue gas testing. With the closure of the CHP plant, Equinor’s strategic modifications introduced a steam boiler together with revamped waste heat recovery unit. This unit provides MHP flue gas. The CO2 content in MHP gas ranges from 8-9 mole%, expanding TCM’s testing capabilities to simulate conditions akin to steel and cement flue gases, with concentrations of up to 20 vol% CO2 achievable through product recycling.
Furthermore, the residual fluid catalytic cracker (RFCC) at the refinery stands as another significant source of flue gas, providing CO2 concentrations of up to 13-14 mole%. The amine plant, with a processing capacity of approximately 40000 to 45000 Sm3/h, captures around 200 tonnes of CO2 per day from this source, enriching TCM’s research portfolio with yet another dimension of exploration.
In essence, the convergence of these diverse flue gas sources equips TCM with an unparalleled testing environment, propelling advancements in carbon capture technology and emissions reduction. As TCM continues its quest for sustainability and innovation, the synergy between Equinor’s refinery operations and TCM’s research initiatives promises a brighter, greener future for industries worldwide.
Mix different concentrations and compositions
TCM uses two industrial sources of flue gas: Equinor’s residue cracker at the Mongstad refinery (13 per cent CO2) and the associated Mongstad Heat Plant (MHP) (8-9 per cent CO2). These two flue gas sources make it possible to simulate emissions from different industries, such as cement production, steel, waste management and oil refining. TCM can mix different concentrations and compositions from these two sources. This is unique in a global context and means that more people will be able to come to us to test how their technology works under different conditions.