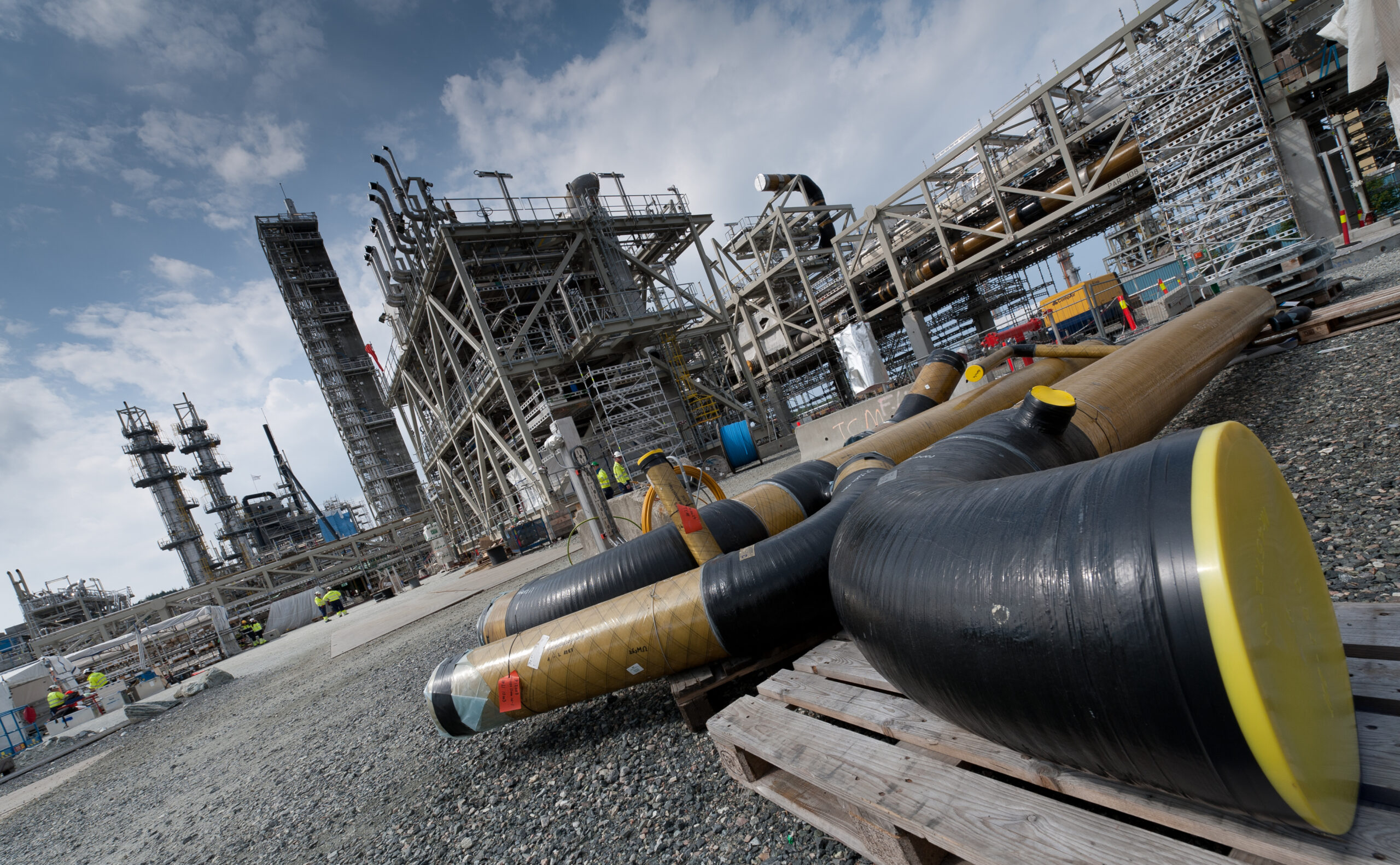
14.05.2024
What happens in the absorber?
Aker Carbon Capture constructed the TCM absorber present at the technology center today. During the construction process in 2012, significant emphasis was placed on ensuring the plant’s flexibility, a key factor in prolonging the center’s operational lifespan.
The absorber column has a cross-section 3.55 meters × 2 meters and total height of 60 meters. Three packing beds are installed in the absorber. This absorber column serves as the primary site for both CO2 capture and emission control, effectively addressing environmental concerns in tandem.
Establishing an Absorber column accounts for 45% of the costs for a CO2 capture plant
Establishing a new absorber constitutes a significant portion, approximately 45%, of the costs associated with a CO2 capture unit. A key insight from one of TCM’s cost analyses underscores that absorbents alone represent nearly half of the total material expenses for such a plant.
To mitigate these costs, various strategies can be implemented, including streamlining the scrubbing section, optimizing solvent consumption, enhancing capture rates, reducing steam consumption (thus lowering energy usage), and increasing the CO2 content in the flue gas.
At TCM, we collaborate closely with technology suppliers to optimize plant performance. Through meticulous testing of different CO2 concentrations ranging from 1% to 20% and strategic positioning of the solvent within the plant, we leverage our team’s expertise and extensive operational experience. Our rigorous test campaigns provide a robust foundation for comparison and enable us to offer valuable insights to technology suppliers striving to achieve maximum efficiency.
Ultimately, our shared goal is to advance the development of the most efficient CO2 capture technologies, and we take pride in leveraging our knowledge and resources to support industry partners in realizing this objective.
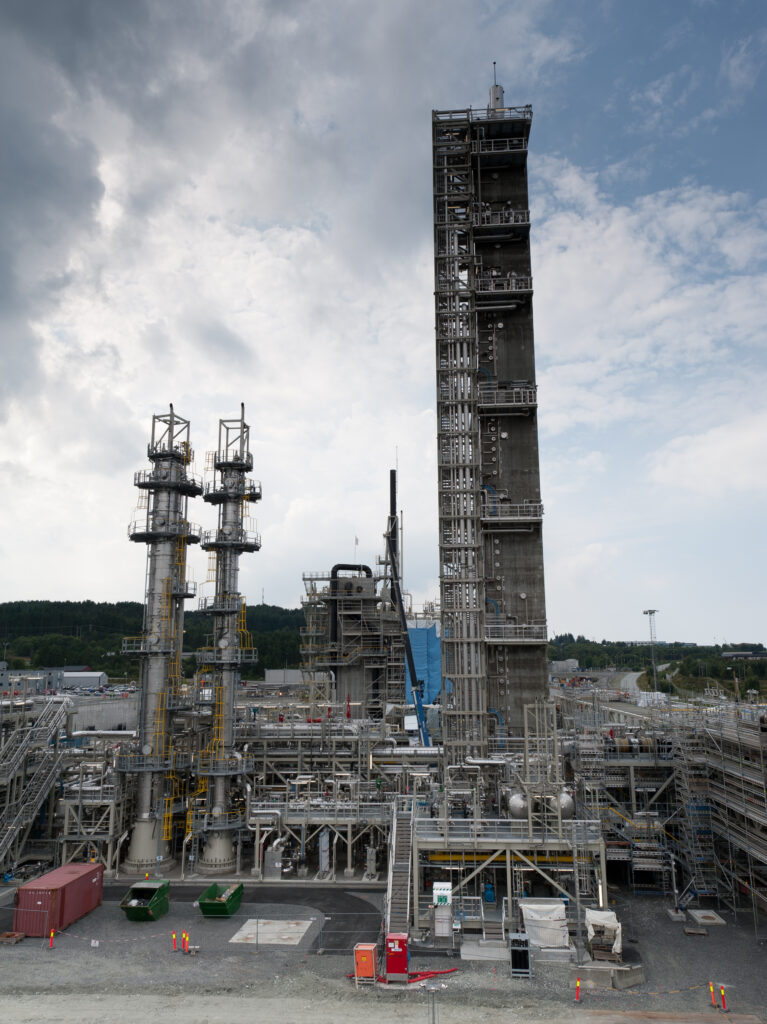
High flexibility and solvent’s path to CO2 capture at TCM
At TCM, our focus is not on determining the superiority of one technology over another, instead we support the technology developers by providing guidance on enhancing the efficiency of their solvent technology. This involves furnishing actionable insights through continuous monitoring of the absorption process. To achieve this, we employ various measurements obtained from different sample points, including CO2 inlet, outlet, and water wash sections.
In terms of flexibility, as highlighted in our earlier article, the amine absorber is capable of testing with two distinct industrial sources of flue gas, complemented by recycling and dilution capabilities.
Transitioning to the solvent aspect, the key to the absorber operation efficiency lies in ensuring optimal contact between the solvent and the CO2. At TCM, this is accomplished by introducing the solvent to the packing material within the absorber column. Furthermore, three solvent feed injection levels enable adaptable absorber operation, offering variations with 12 meters, 18 meters, or 24 meters of packing.
As the processed flue gas moves upwards, it passes through the water washes at the top section of the absorber, which helps scrub the flue gas and reduce solvent entrainment, thereby minimizing solvent loss. The amine absorber incorporates two distinct water wash sections, serving dual purposes:
- to maintain a closed water balance in the solvent system by condensing water vapors in the exit flue gas, and
- to reduce the concentration of volatile organic compounds, such as MEA, or amine degradation products (formaldehyde, acetone, acetaldehyde), in the depleted flue gas. The
CO2-depleted flue gas exits the top of the absorber column, and the rich solvent exits the bottom of the absorber column and is heated in the cross-heat exchanger by a countercurrent stream of hot lean solvent.
In a rapidly evolving landscape of CO2 capture technologies, it’s imperative to remain ahead of professional advancements. Active participation in collaborative initiatives is a key. At TCM, we’re engaged in partnerships with EU projects, to test and demonstrate their CO2 capture technologies at our “site for emerging technologies.”
Owners test campaigns
Beyond vendor testing, the owners of TCM have conducted numerous test campaigns utilizing commercially available solvents, including MEA and CESAR1. These campaigns have scrutinized multiple parameters and operational scenarios to ascertain optimal system performance. These endeavors have yielded invaluable insights that serve as a benchmark for comparison among various technology developers and buyers.
The wealth of experience garnered through these endeavors is now available for sharing with other upcoming technology vendors, including Longship; Heidelberg Materials, and Hafslund Oslo Celsio. By facilitating knowledge exchange, we collectively drive progress in CO2 capture efforts.
Meeting evolving needs with expert guidance
A significant portion of our clientele returns to TCM for solvent re-testing. Whether they have refined their existing solvent based on lab findings or introduced a completely new solvent, we accommodate both scenarios. The feedback we consistently receive from our customers underscores their appreciation for the insightful guidance provided during the testing process.