Change in Management at TCM
Managing Director Ernst Petter Axelsen resigns and Operation Manager Robert Henricks will take on the position as acting Managing Director until further notice.
A new Managing Director will be proposed by Gassnova and appointed by the Company Meeting in due time.
Axelsen will now return to his position as senior advisor at Gassnova, as part of a normal secondment process;
As a joint venture without own employees, TCM’s organization consist of seconded personnel from the owners and externally hired personnel. The owners of TCM take an active role in the day-to-day operation by seconding highly specialized expertise to the company. These assignments vary in duration, but the secondees shall all return to their organisation with new knowledge.
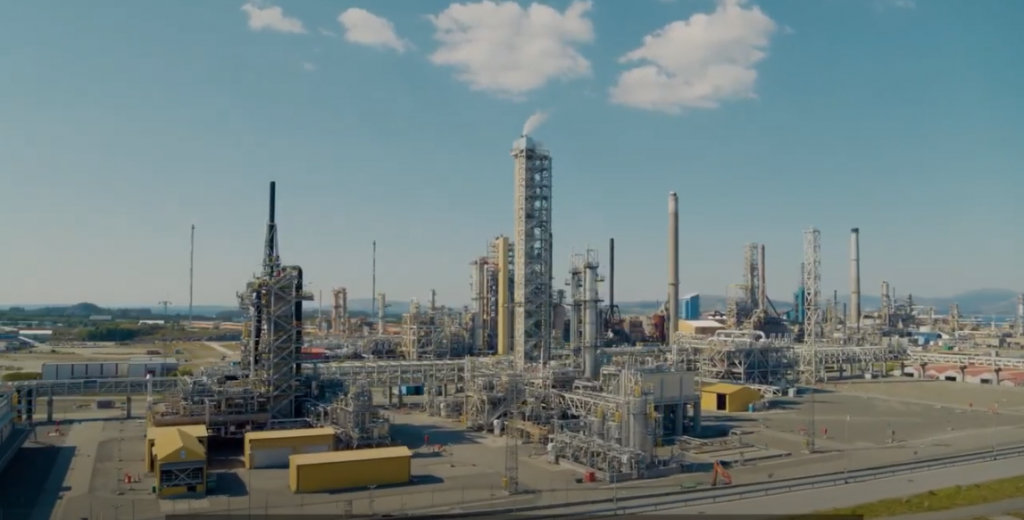
Axelsen started as Managing Director in 2018 and has guided the company through a transition period. The testing facilities has been further developed, in addition to broadening the Advisory Services in the aim to create a more sustainable foundation for TCM where cost reduction and increased income has been key factors.
TCM’s owners thank Axelsen for his work for TCM.
Promising test of new capture technology
– The test campaign at TCM using the open source capture solvent CESAR-1, a mixture of AMP and Piperazine, has been very promising, says Technical Support Manager, Muhammad Ismail Shah. – The preliminary results indicate significantly lower energy consumption and potential for lower costs when using a comparable solvent for capturing CO2. The test at TCM also shows that CESAR-1 can be handled properly in compliance with HSE requirements on an industrial scale and that the technical risks in the capture process are mitigated, he says.
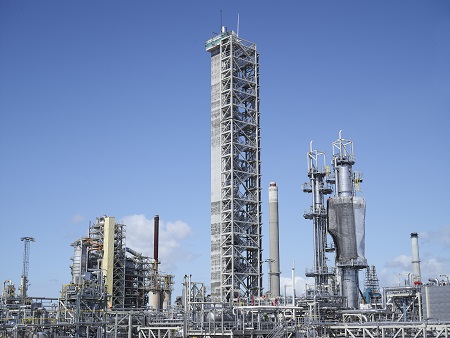
It were the owners of TCM, Gassnova (the Norwegian state) and the industrial partners Shell, TotalEnergies an Equinor, who last year initiated the implementation of the test with CESAR-1. The reason is that the International Energy Agency, through its Greenhouse Gas R & D Program (IEAGHG), has requested a comprehensive assessment of new CO2 capture technologies in the energy sector and an evaluation of their potential to reduce costs associated with the operation of full-scale facilities.
TCM has previously conducted five open source test campaigns with the carbon capture solvent MEA (Mono Ethanol Amine). TCM has managed to capture up to 98 percent of CO2 emissions with aqueous MEA (a mixture of water and MEA). TCM has established a third-party verified baseline for both flue gas from the gas power plant (CHP) and the «refinery cracker» (RFCC) at the refinery at Mongstad.
– Against this background, we have had a very good basis for comparison for the test with CESAR-1 both in terms of efficiency, energy consumption and technical risk in the process, Shah emphasizes.
Extensive material after the campaign
CESAR-1 is an open source solvent, a mixture of Piperazine and AMP. During the campaign at TCM, the properties of this solvent were tested in a process with CO2-containing flue gases for a total of approx. 8.000 hours. This has yielded a large amount of useful test results which are now being analysed and crunched.
– Our preliminary analysis from the test indicate that the energy consumption when using CESAR-1 gave a reduction of 15 – 20 percent compared to MEA under comparable operation conditions. We also have demonstrated that the technical risks of using CESAR-1, which mainly relates to the handling of Piperazine, could be carried out in a full compliance with HSE requirements. We have got good insight on important aspects of using this technology regarded to health, safety and environment.
In the test, a capture of about 98 – 99 percent of CO2 from the flue gas was demonstrated, which means that it is possible to reduce CO2 emissions from the flue gas significantly with a relatively low energy consumption. Through the test, TCM also has proven that it is possible to reclaim degraded CESAR-1 solvent by using thermal reclaiming technology.
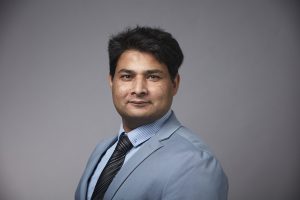
Will receive good reception
Shah believes the preliminary results from the CESAR-1 campaign will be well received in the carbon capture industry. They will form an important reference in the work for further development of capture technology with lower costs.
The preliminary results from the campaign were first presented at TCCS (Trondheim Conference on CO2 capture, transport and storage) on 23 June. Additional presentations with results in a more elaborated form will be given at conferences to come and in professional journals. TCM also will exchange experiences and results in the ongoing collaboration with NETL (National Energy Technology Laboratory) in the US, which will contribute to further development of capture technologies with lower costs.
Announces CESAR-1-results on TCCS-11
TCM will present results from last year’s CESAR-1 campaign during the TCCS-11 conference.
Results from last year’s CESAR-1 campaign
The 11th Trondheim Conference on CO2 Capture, Transport and Storage takes place on Tuesday 22 – Wednesday 23 June. TCCS-11 goes virtual. Since the start in 2003, the Conference has grown from a meeting for a select few, to be an important meeting for 350 – 400 CCS experts from all over the world. Erna Solberg, prime minister of Norway, will open this years conference.
CESAR-1 is the name of of a research based solvent used by the aim of capturing CO2 at the lowest possible cost. The title for TCM’s presentation on the conference is “Results from CESAR-1 testing with combined heat and power (CHP) flue gas at the CO2 Technology Centre Mongstad”. Scott Hume from EPRI – University of Strathclyde, Glasgow, Scotland will give the presentation. EPRI have verified the results from the campaign.
It was the owners of TCM; Gassnova (on behalf of the Norwegian state) and the industrial partners Shell, Total and Equinor, who together initiated the implementation of the test with CESAR 1. The reason is that the International Energy Agency, through its Greenhouse Gas R & D Program (IEAGHG), has requested a comprehensive assessment of new technologies for CO2 capture in the energy sector, and an evaluation of their potential to reduce costs associated with the operation of full-scale facilities.
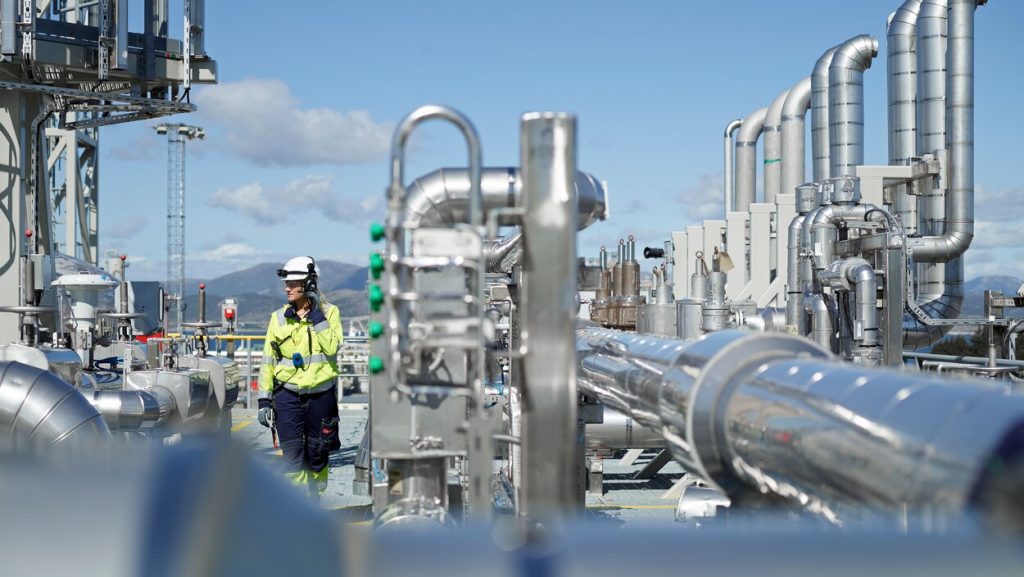
TCM to advice Wärtsilä on carbon capture
Wärtsilä Marine Systems has entered into an agreement with Technology Centre Mongstad (TCM) for advisory services in connection with the establishment of a pilot plant at Moss in Norway for capturing CO2 on board ships.
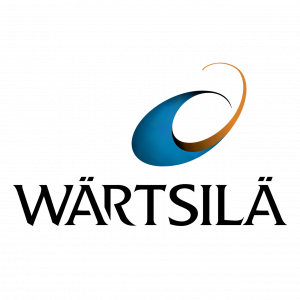
The purpose of the project is to design and upgrade systems for cleaning smoke and exhaust gases (scrubbers) to also capture CO2 from the exhaust. Among other things, TCM will contribute expertise on emissions and HSE. – Wärtsilä has conducted extensive research and development which show that carbon capture and storage (CCS) in the maritime sector technically is possible. We look forward to helping this technology to be used in the future, says Ernst Petter Axelsen, CEO at TCM.
Advisory services are a priority area
Since its inception in 2012, TCM has conducted 13 tests of various carbon capture technologies for private companies and research-based institutions, and three more such campaigns are planned this year. – In addition, we have been an advisor for several projects internationally for the deployment and implementation of CO2 capture in full scale. Many will use the knowledge and experience we have gained to reduce the risk of errors in the planning and implementation of such projects. As the capture and storage industry now takes new steps in many countries, advisory services are also becoming an increasingly important business area for TCM, Axelsen emphasizes.
Huge advantage for Wärtsilä
Through the collaboration with TCM, Wärtsilä receives expert assistance for modeling processes related to CO2 capture and storage, and for safeguarding health, environment and safety aspects in the capture process.
– TCM’s support gives Wärtsilä access to a deep well of insight and expertise on carbon capture technologies, alongside world-leading facilities that will enable us to bring a maritime CCS solution to market, says Wärtsilä’s General Manager Technical R&D, Jan Gannefors. – This agreement gives us a huge advantage in solving the challenge of reducing emissions on ships and supporting the industry’s wider decarbonisation pathway.
Can provide emission reductions relatively quickly
– CCS onboard vessels is clearly a substantial undertaking, but one that we believe we are well placed to pioneer, says Sigurd Jenssen, Director, Exhaust Treatment at Wärtsilä.
– Carbon capture is exciting because it can provide significant reductions in a relatively short timeframe. This is important in the context of the industry’s overall decarbonisation transition, as it will enable us to safeguard existing assets as we move to a cleaner mode of operating, Jenssen adds.
InnoSepra to test new technology for carbon capture at TCM
The US company InnoSepra, LLC has entered into an agreement with Technology Centre Mongstad (TCM) to conduct a test on its new adsorbent technology for carbon capture. The test campaign will take place at TCM’s new site for emerging technologies, starting in Q1 2022.
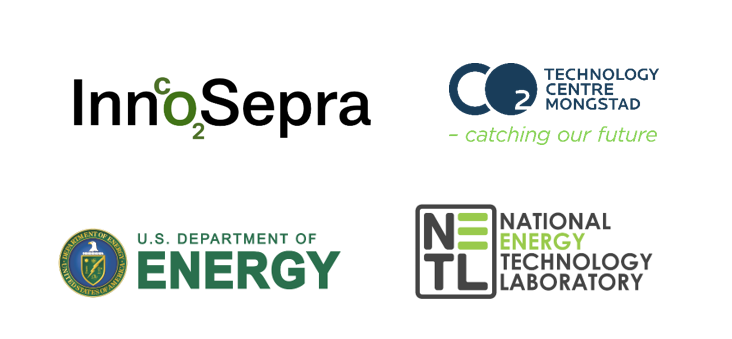
InnoSepra is focusing on development of cutting-edge technologies to be used for post combustion capture. The project to be tested at TCM is funded by the U.S. Department of Energy’s (DOE) National Energy Technology Laboratory (NETL).
The site for emerging technologies was built last year as TCM’s third test-facility at the plant and is used for testing technologies such as membranes and adsorbents, solid materials that bind CO2 in its surface. These emerging technologies are typically at a lower technology readiness level than more classical technologies, such as solvents, and the site creates new opportunities for technology development.
“For many years we have been collaborating with vendors funded by the U.S. Department of Energy Office of Fossil Energy’s National Energy Technology Laboratory to validate the performance of carbon capture technologies at a larger scale on actual flue gas by testing at TCM. We are now seeing this collaboration extending into our new test site during 2021”, tells Ernst Petter Axelsen, CEO at TCM. “We are also pleased that a reputable technology developer like InnoSepra has chosen it as arena for their test-program”, he says.
Improving energy requirements
“Our purpose is to demonstrate the scale up and long-term operation of the second generation of InnoSepra’s process for post combustion CO2 capture”, says Dr. Ravi Jain, President of InnoSepra. “We use physical sorbents to produce CO2 at high purity and high recovery ratios. This process aims at improving the energy requirements of the sorbent regeneration, leading to lower operational costs”, he adds.
InnoSepra was started in 2007 using the team’s long experience in industrial gases separation and purification. They have commercialized technologies in more than 100 plants for The BOC Group, which during its time was one of the world’s largest producers of industrial gases essential to almost every manufacturing process.
Using TCM’s expertise
InnoSepra has a portfolio of technologies based on a platform technology for CO2 capture and removal from various process streams. Together with TCM and NETL they are now ready to address various process risks that might arise from scaling up the process from lab and pilot testing into large scale.
“TCM offers expertise on de-risking technology, analytical capabilities and know-how that allows efficient troubleshooting and optimization of capture processes. This contribution is crucial for us to achieve the objectives of the campaign”, Ravi Jain emphasizes.
For more information, please contact:
Dr. Ravi Jain, President at InnoSepra LLC + 1 908 450-9840
Read more about InnoSepra at http://www.innosepra.com/
Read more about NETL at https://www.netl.doe.gov/
Mitsubishi Heavy Industries Engineering to test carbon capture technology at Technology Centre Mongstad in Norway
Mitsubishi Heavy Industries Engineering (MHIENG), part of Mitsubishi Heavy Industries (MHI) Group, has entered into an agreement with Technology Centre Mongstad (TCM) to test its proprietary solvent for capturing CO2 at the amine plant located in Mongstad, Norway. The test campaign will start in May.
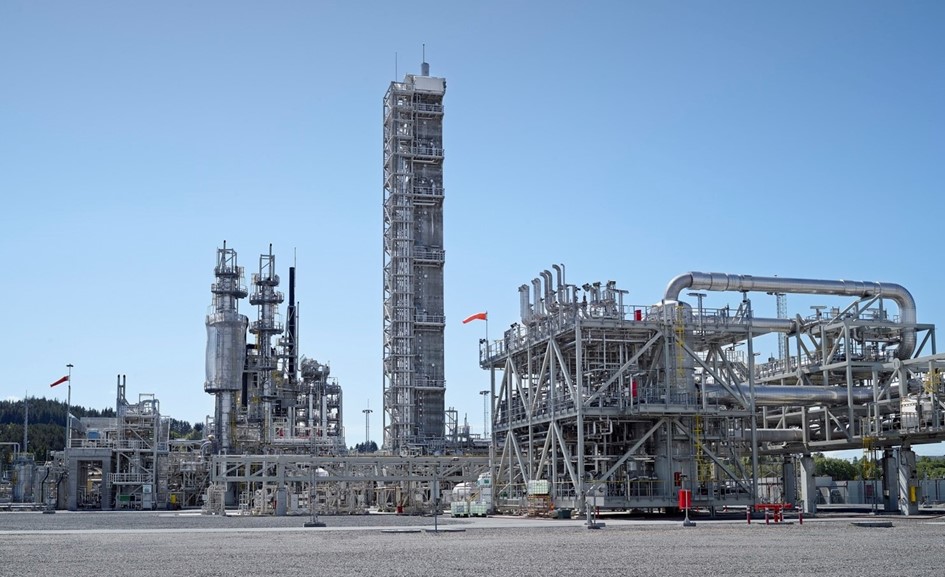
The KS-21TM
The proprietary solvent to be tested is the KS-21TM, an amine-based adsorbent used in the “Advanced KM CDR ProcessTM” newly developed by MHIENG in collaboration with Kansai Electric Power Co., Inc. (KEPCO). Its long-term usage will be demonstrated in Norway, one of the world’s most advanced countries with respect to environmental regulations on CO2 capture, in a quest to achieve commercialization within 2021. Compared to the earlier KS-1TM solvent, which has been adopted at 13 commercial plants delivered by MHIENG, KS-21TM has a number of advantageous properties such as lower volatility and greater stability against degradation. The newer solvent is also expected to enable reduced running costs and other economic benefits.
At a time when CO2 capture needs are expanding in the United Kingdom and Europe, the test program at TCM, which has state-of-the-art facilities and specialized knowledge, will confirm KS-21TM’s long-term durability and assess its environmental impact, thus providing MHIENG with technological data relating to its significantly higher CO2 capture rate. The test program will enable MHIENG to set a timetable for KS-21TM’s commercialization, opening the way for the company to expand orders in the UK and European markets.
Since its establishment in 2012, TCM, equipped with the world’s largest-scale CO2 capture testing facilities, has provided users with profound knowledge, online analysis, and advanced analytical technologies relating to the trace components of gas emissions. Its data accumulated through testing exceed 1,000 categories and contribute significantly to commercialization of absorbents.
On reaching the new agreement with TCM, Kenji Terasawa, MHIENG President & CEO commented: “MHI Group today is strengthening its efforts in the energy transition field, to help realize a carbon neutral world on a global scale. For many years, MHIENG has strived to minimize CO2 emissions from gas emissions, utilizing its cutting-edge technologies. Today we possess reliable and economically feasible carbon capture technologies supported by more than three decades of research and development activity and a robust track record of commercial plants around the world. TCM’s abundant knowledge and experience in environmental impact assessment, and its state-of-the-art testing environment, will raise the level of our CO2 capture technologies further, enabling us to accelerate business expansion in the vital UK and European markets. We expect the new testing program will contribute to realizing carbon neutrality in the years ahead.”
Ernst Petter Axelsen, CEO at TCM, also welcomed the new collaboration. “It’s very satisfying that a leading capture technology developer like MHIENG has chosen TCM as the arena for their carbon capture tests. Our staff is ready to ensure effective execution of the tests, and to provide expert advice throughout the campaign.”
About KM CDR Process™ and Advanced KM CDR Process™
MHI Group together with Kansai Electric Power Co, Inc. (KEPCO) started the development of the Kansai Mitsubishi Carbon Dioxide Recovery KM CDR Process™, a post-combustion carbon capture technology, in 1990. As of February 2021, MHIENG has delivered a total of 13 commercial plants with the KM CDR Process™, making it a global leader in carbon capture technology deployment. Two more plants are currently under construction.
During the test campaign, MHIENG’s proprietary KS-21™ will be tested, with comparisons to be made with its earlier KS-1TM solvent. KS-1™ is currently being used at all commercial plants that employ the KM CDR Process™ and has proven to be a competitive and reliable solvent of choice. MHIENG, with the support of KEPCO, has continued to improve upon the KM CDR Process™ and has recently developed KS-21™. KS-21™ has many promising characteristics including lower volatility and greater stability against degradation, and MHIENG believes that these properties will result in operational cost savings making the Advanced KM CDR Process™ even more economical for future deployment. MHIENG is aiming to commercialize the new KS-21™ solvent within 2021.
TCM offers unique test facilities
TCM’s test facilities for CO2 capture consist of an amine plant, a chilled ammonia plant, as well as an area for new, groundbreaking modular capture technologies. Both the amine and the chilled ammonia plants capture CO2 by means of a chemical liquid known as a solvent, consisting of a mix of water and either amine- or ammonia-based solutions. Starting in 2021, the site for modular technologies will be used for testing technologies such as membranes and adsorbents (solid materials that bind CO2).
TCM uses two different industrial live flue gas sources (fluidized catalytic cracker and combined cycle gas turbine) from Equinor’s refinery at Mongstad, with different content of CO2.
The amine plant is a unit with generic capabilities developed to serve as a demonstrator for solvent-based capture technologies. The unit has so far been utilized by five technology developers in addition to scientific testing using non-proprietary solvents (monoethanolamine and CESAR 1) for helping developments in the global carbon capture community.
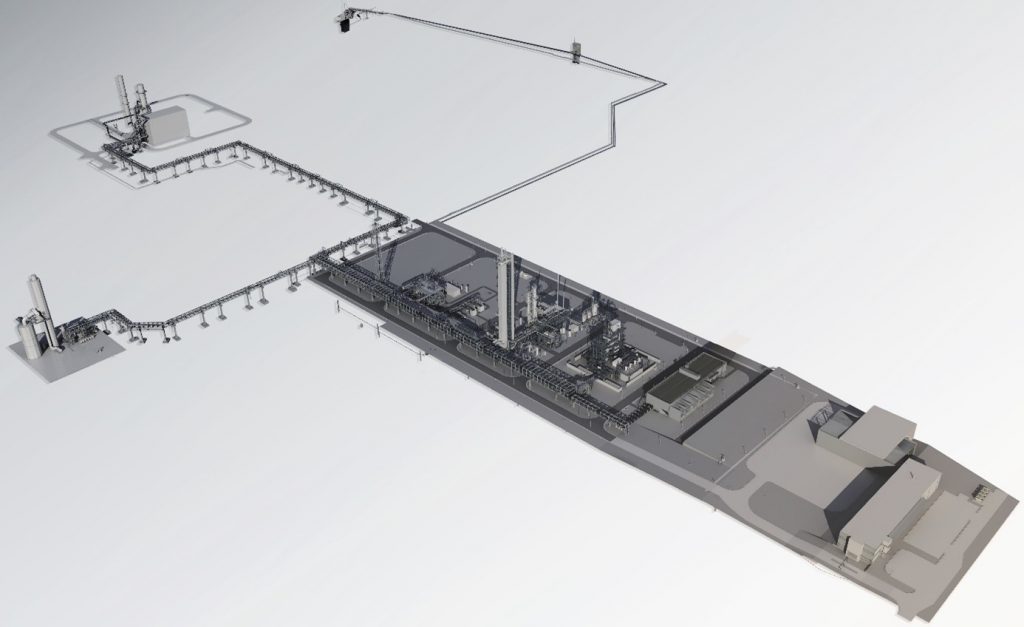
About Mitsubishi Heavy Industries Group
Mitsubishi Heavy Industries (MHI) Group is one of the world’s leading industrial groups, spanning energy, logistics & infrastructure, industrial machinery, aerospace and defense.
MHI Group combines cutting-edge technology with deep experience to deliver innovative, integrated solutions that help to realize a carbon neutral world, improve the quality of life and ensure a safer world.
For more information, please visit www.mhi.com
About Mitsubishi Heavy Industries Engineering, Ltd.
Mitsubishi Heavy Industries Engineering, Ltd. (MHIENG), headquartered in Yokohama, Japan, was founded as an engineering company of Mitsubishi Heavy Industries Group on January 1, 2018. MHIENG took over the engineering business in chemical plants and transportation systems of Mitsubishi Heavy Industries and extended them with newly added environmental facilities (CO2 capture plant). MHIENG has implemented numerous engineering, procurement and construction (EPC) projects covering large-scale infrastructure, such as chemical plants, environmental plants, and transportation systems, in many countries and regions around the world. The Company readily meets diversified customer expectations by undertaking all phases from project planning to basic design, detailed design, procurement, manufacture, construction, commissioning, after-sales service, and operation & maintenance (O&M), as well as capital participation in businesses.
For more information, please visit: https://mhieng.mhi.com/
For more information, please contact:
Ernst Petter Axelsen, CEO at Technology Centre Mongstad (TCM)+ 47 982 08 618
Group Strategy Promotion Office, Corporate Communications Dept., Mitsubishi Heavy Industries (mediacontact_global@mhi.co.jp)
TCM contributes to online course in carbon capture at UiB
The University of Bergen (UiB) has started a series of competence-developing courses with the aim of increasing the industry’s ability to carry out green restructuring of its businesses. Technology Centre Mongstad (TCM) participates with a carbon capture lecture module.
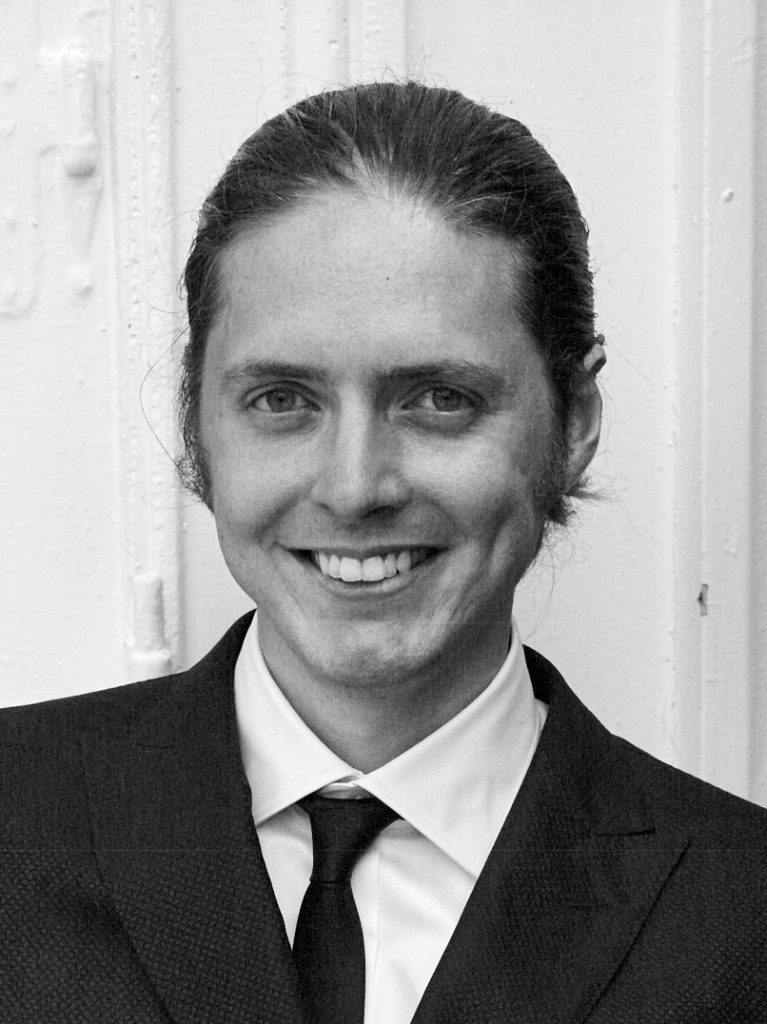
Online teaching
– Dissemination of knowledge within CO2 capture is an important part of our aim and mandate, says Audun Drageset (photo), Environmental engineer at TCM. – Before the pandemic, we regularly received master’s students at the plant in connection with relevant courses and master’s projects. Now we have contributed with materials for use in online teaching and gained valuable experience on how we can contribute with knowledge sharing in order to achieve the goals of reducing climate emissions.
When UiB last autumn announced its offer for further education under the Industry Program for the oil, gas and supplier industry, they received 196 applicants for the 60 available slots in the Carbon capture, use and storage (CCUS) course. The course started at the end of November and runs over ten weeks. One week in January was set aside for teaching CO2 capture with TCM as responsible.
– We produced a «package» with a total of eight modules, of which seven pre-recorded videos with a duration of 8 – 12 minutes. As the site visit at our carbon capture facility is the highlight for most of our visitors, we wanted to recreate this by giving the participants a virtual tour using a 3D model where we the different steps in the CO2 capture process were highlighted. Finally, we had an hour of questions and discussion on various capture-related topics – with great engagement among the participants.
Was the anything that surprised you during the course?
– Yes, while we previously mainly have had dialogue with engineering and science students, this time there was a large number of participants with practical experience from the industry. With their particular background and experiences, their interest and concern were more directly related to how the capture process impacts the main plant, like energy consumption and efficiency. I hope they found the session useful, Drageset says.
He adds that UiB will carry out an evaluation among the participants when the course is finished, and is looking forward to receive feedback on the program.
TCM shares knowledge on carbon capture
Due to the great interest in participating in the CCUS course, UiB is planning a new course this autumn. Ernst Petter Axelsen, CEO at TCM, says that the company wants to contribute to this and to other dissemination of knowledge on carbon capture.
– The Norwegian authorities’ decision to contribute to realization of the «Longship» project, has put a much stronger focus on carbon capture and storage as a tool for achieving the climate goals, not only in Norway, but also internationally. As the world’s largest and most flexible arena for testing capture technologies, we have knowledge and experience that is valuable for universities and research institutions as well as for suppliers of technology, he emphasizes.
Read more about the CCUS course at UiB: CCUS-kurs: CO2 fangst, bruk og lagring | Etter- og videreutdanning | Universitetet i Bergen (uib.no)
Read the report in Bergens Tidende / e24.no: https://e24.no/olje-og-energi/i/Bly65v/monica-har-jobbet-30-aar-innen-olje-og-gass-naa-vil-hun-rydde-opp?referer=https://www.bt.no
TCM «staffs up» its team
In 2020, TCM has been reinforced with new resources from its owner companies. The Management team has «staffed up» with four new members.
– This year has in several ways given a breakthrough for carbon capture and storage as tool in the climate battle. We are very well equipped to assist our customers at the test facility and to provide outstanding advisory services on CO2 capture globally, says Ernst Petter Axelsen, Managing Director at TCM.
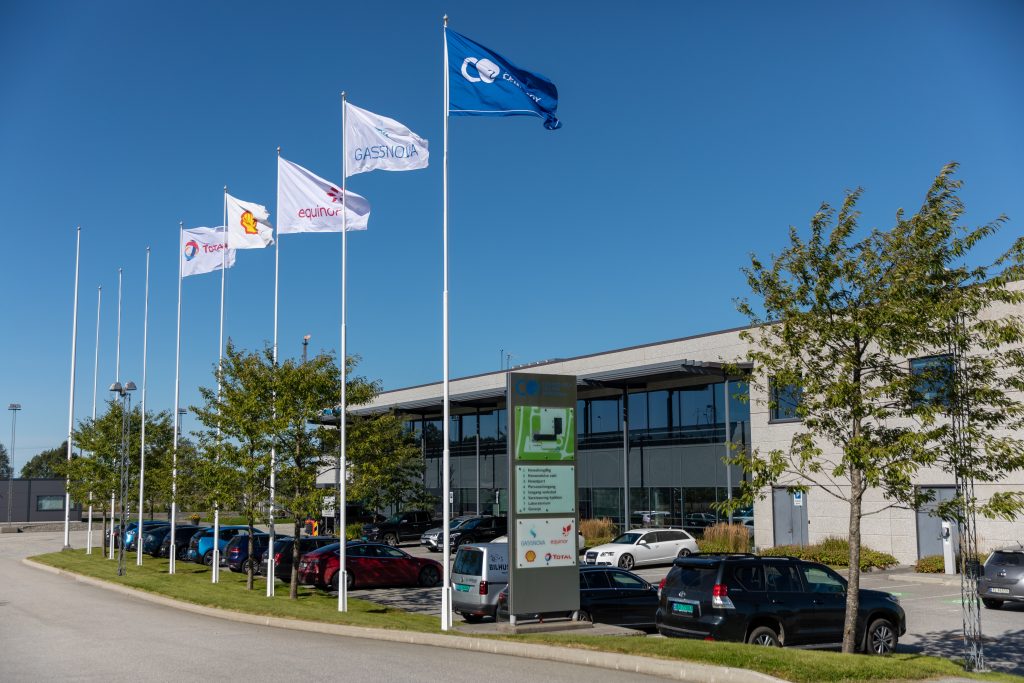
With a new mandate from the Norwegian state and further investment from TCM’s industrial partners in developing cost-effective methods for carbon capture, optimism is high among the company’s about 60 people.
Test Development Manager
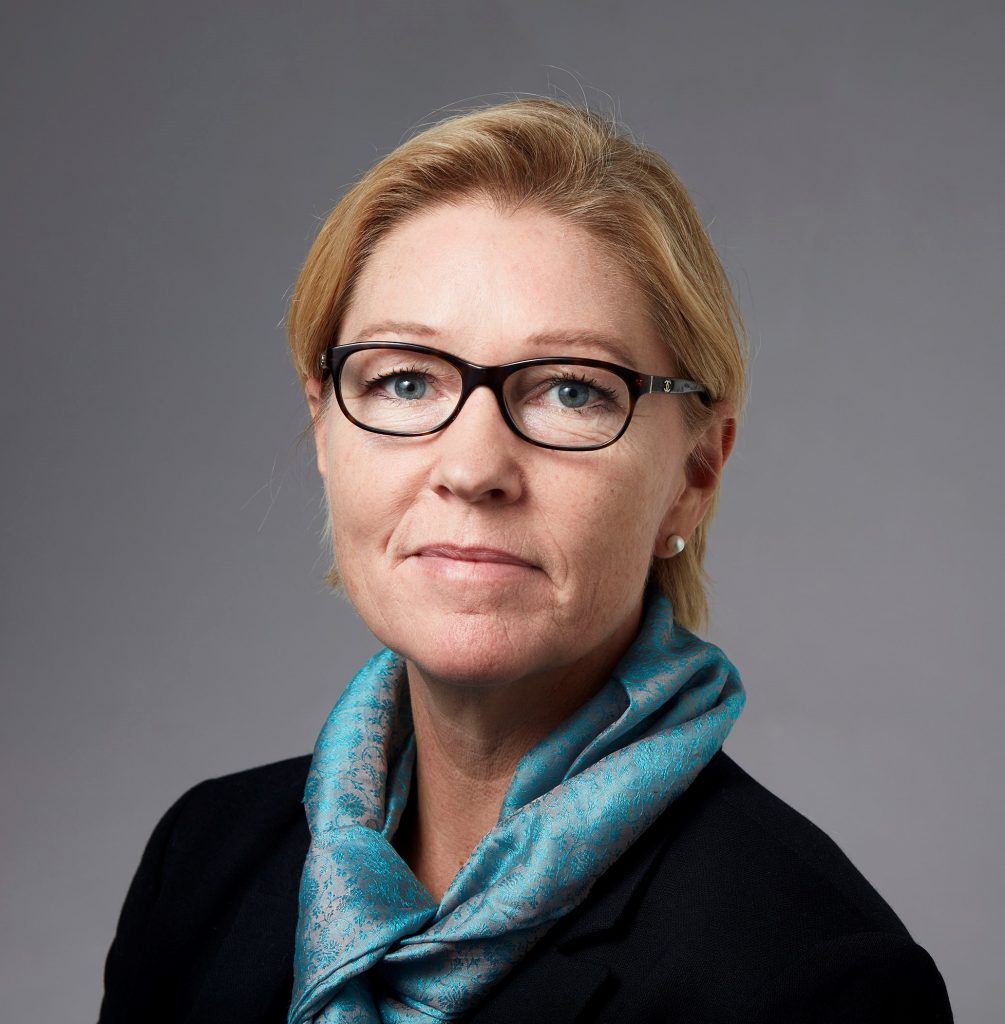
– My ambition is for TCM to be the premium collaboration partner for carbon capture technology developers and CCUS project developments also in the future, says Jorunn Brigtsen. She has joined the Management team as Test Development Manager. Brigtsen is seconded from Total, and has been working at TCM since 2017. Read more about her experience here.
Technical Support Manager
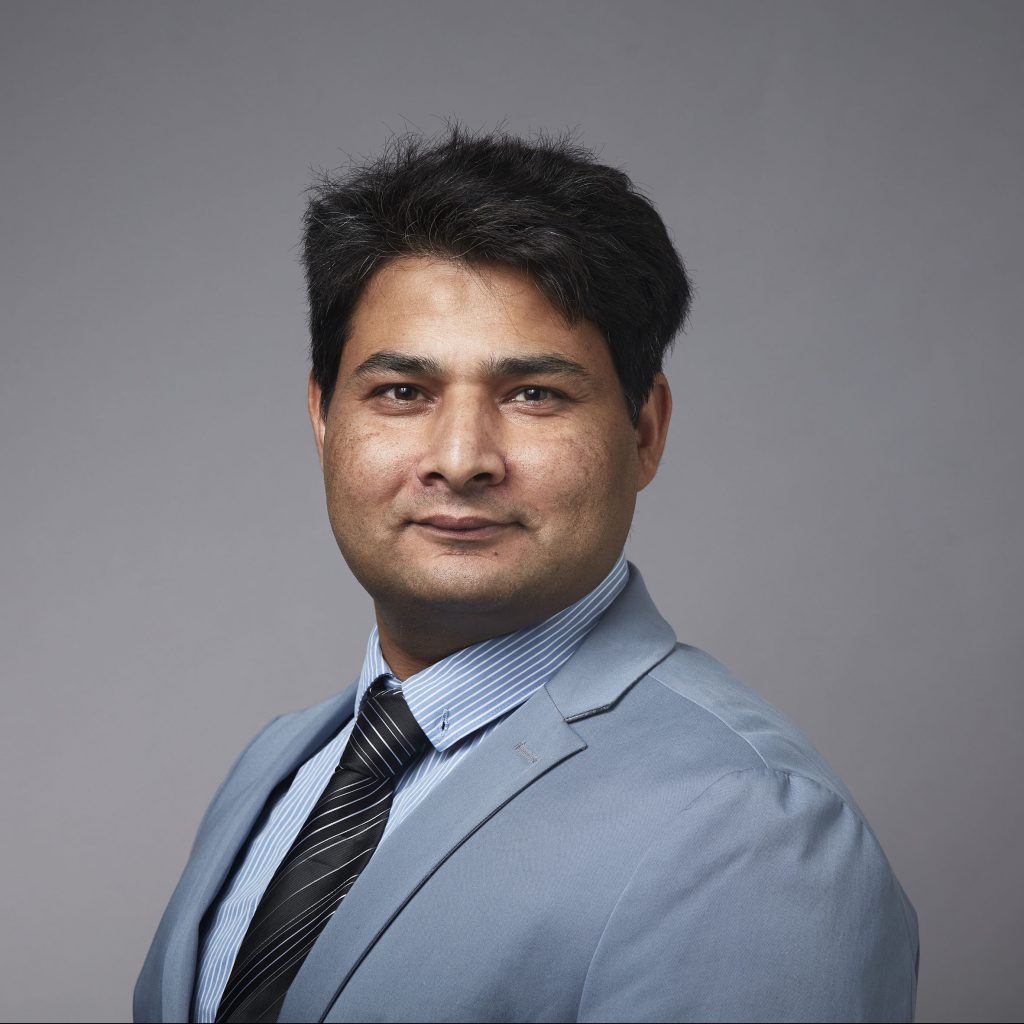
Muhammad Ismail Shah is Technical Support Manager and member of the Management team. He is seconded to TCM from Gassnova SF and have been working with TCM projects since 2011.
– I want large scale deployment of carbon capture and sequestration technologies soon to be able to combat climate change. Deployment of new technologies bear risk both technical, economical and environmental. TCM over the years have gained unique and hands on experience which can be utilized to reduce the risks, says Shah.
– Technology Centre Mongstad (TCM) is world’s unique engineering scale test facility, for reducing technical, economic and environmental risks in post-combustion carbon capture (PCC) technologies by providing access to world class test facilities and unique competence gained through long terms open access test campaigns and knop-how. TCM can support both technology developers, and capture project owners to de-risk the technology in question and be able to successfully demonstrate the technology on industrial scale. Read more about Shah’s experience here.
Technology and Advisory Services Manager
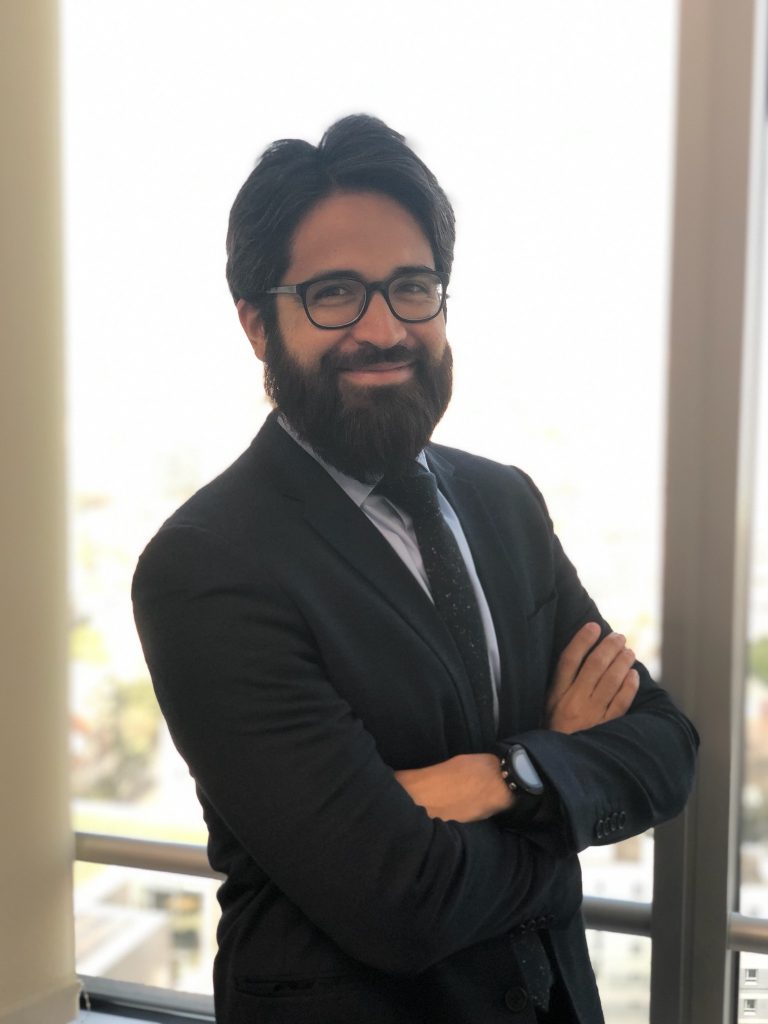
Freddy Garcia has recently started at TCM as Technology and Advisory Services Manager and member of the Management team, seconded from Total.
– I want TCM to be the leader in helping driving the cost of carbon capture costs down by finding ways to optimize the design and operation of the facilities and by sharing the open access knowledge generated, thus aiding to the deployment of the CCUS projects required to reach the net-zero emissions goal, says Garcia.
Read more about his experience here.
Commercial Manager
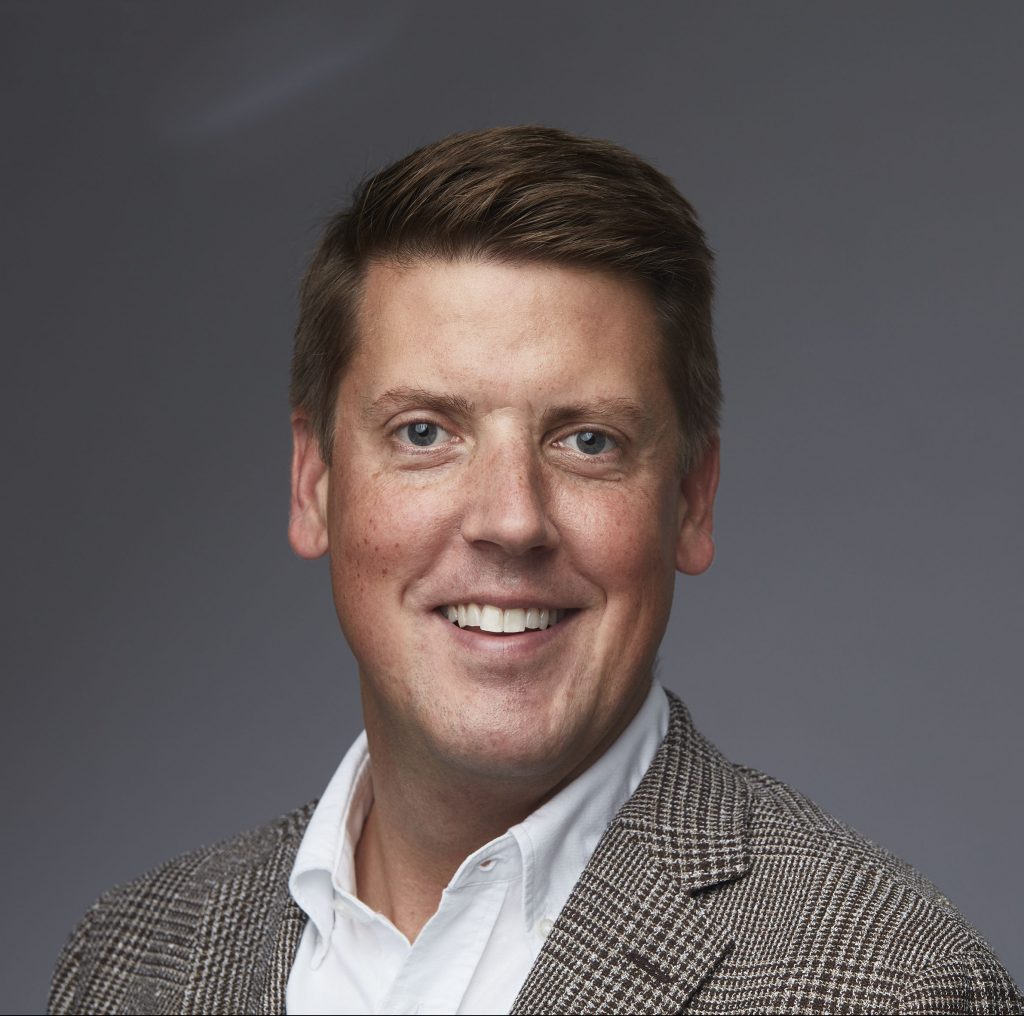
– My goal for the current operating period is that TCM remains relevant as the world’s most knowledgeable centre for CO2 capture technologies, says Arne Thorsen Kolle, Commercial Manager at TCM. – We need to be involved in the full breadth of emerging technologies from membranes to Direct Air Capture, applicable to anything from an offshore platform or a supply vessel to a waste-to-energy plant. Building on our unique competence I’d like us to expand our advisory services to a global reach and be a preferred partner for developing CO2 capture projects, he says.
Arne Thorsen Kolle started at TCM as Commercial Manager and member of the Management Team in April this year, seconded from Shell. Read more about his experience here.
Technology Analyst
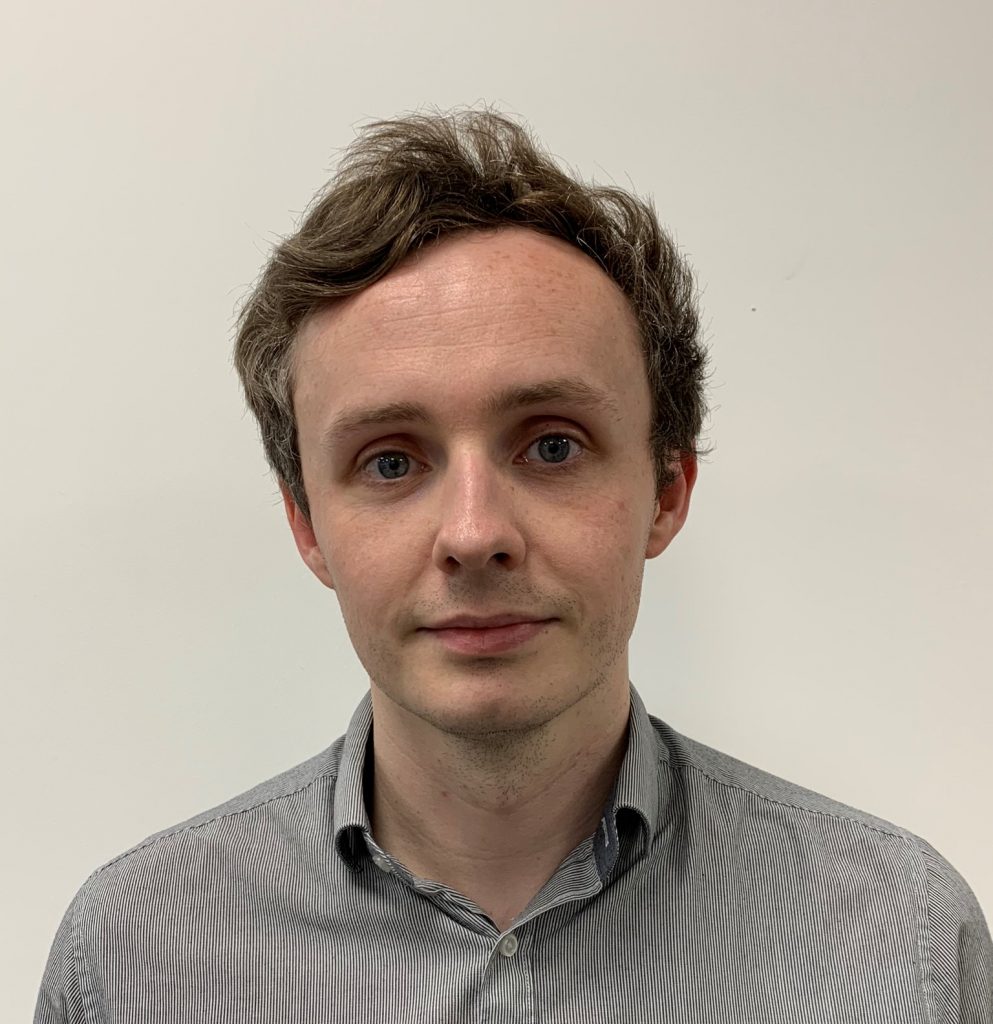
Blair McMaster has joined the Technical Support department at TCM in 2020. He is seconded from Total where he has six years experience in operations support including process engineering and flow assurance roles.
– In the coming years, my ambition for TCM is to continue to lead the advance of carbon capture as it becomes an increasingly important tool in working towards a cleaner future. By continuing the excellent work on solvent based solutions and also accelerating new technologies, TCM will be a key player in the further development, optimisation and deployment of carbon capture, he says.
Blair McMaster holds a Master’s degree in Chemical Engineering from the University of Strathclyde in Scotland.
TCM to join major international partnership on carbon capture and storage
Technology Centre Mongstad (TCM) will strengthen its efforts in developing technologies to fight climate change. Today a memorandum of understanding between three international organizations; TCM, DNV GL and SINTEF, was signed to further develop carbon capture and storage technologies.
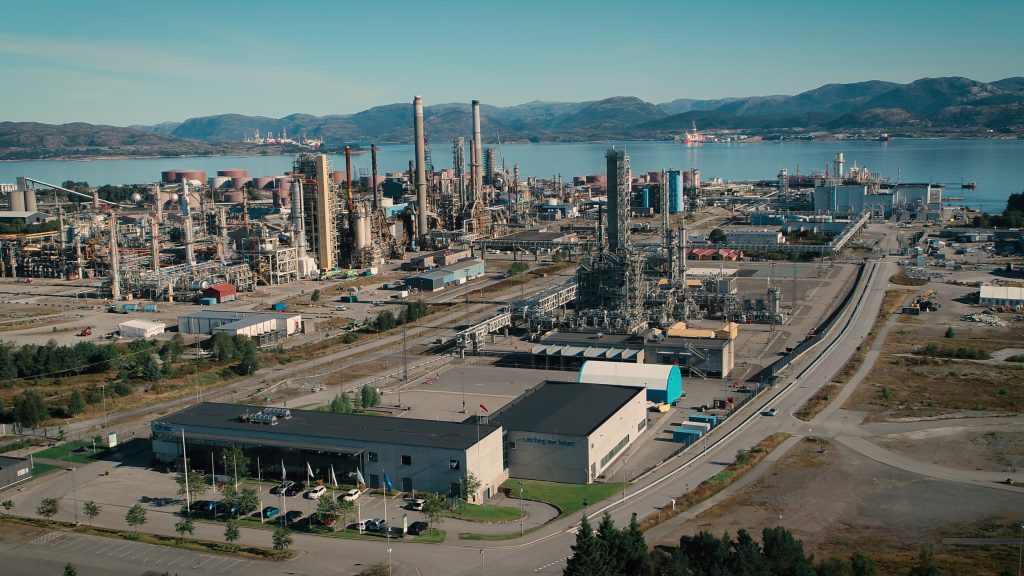
“Our common goal is to facilitate the adoption of carbon capture and storage (CCS) technologies in CO2 intensive industries”, says Ernst Petter Axelsen, Managing Director at TCM.
CCS is a critical technology to deliver deep emission reductions in many industrial processes that are vital to the global economy, such as steel and cement. Scaling the technology will be critical to the industrial sector’s ability to support national and international climate change targets.
The aim of the memorandum of understanding is to help bridge the gap from pilot demonstration to wide scale commercial deployment. TCM’s capability to allow large scale demonstration of CO2 capture technologies is key to lower the cost and risk of deployment of the technologies at scale. Our mandate is to reduce cost and risk for emerging CCS projects through sharing our accumulated knowledge.
As part of this development DNV GL and SINTEF will guide and support processes to qualify the technologies for intended industrial application. Upon successful validation of performance, a statement of qualified technology can be issued by the certification body DNV GL to raise stakeholder confidence in the technology.
“Longship” offers new opportunities
TCM has already provided advisory services to several CCS project developers. The company has been supporting the two potential full-scale CCS projects in Norway with expertise on CO2 capture; Fortum Oslo Varme (owned by Fortum and Oslo City) in Oslo, and at Heidelberg Materials’s cement factory in Brevik (owned by Heidelberg Cement). In a Government White Paper to the Norwegian parliament submitted 21. September, the Government proposed to launch a project named “Longship”, including financial funding to these carbon capture-projects and to “Northern Lights”, the transport and storage project.
Both main CCS technology vendors to these planned CCS projects have run test campaigns at TCM and SINTEF, and have had their technologies qualified by DNV GL.
“The Government’s decision opens up for a huge investment in technology development, where TCM, together with DNV GL and SINTEF, will play an active role”, Axelsen says.
Advisor for large climate fund
“TCM also provides advice to OGCI CI, the USD $1 billion climate fund founded by the world’s largest energy companies. Furthermore, TCM shared scientific knowledge and operational expertise with the first Asian open-access technology centre i.e., the Haifeng CO2 pilot plant in China”, he says.
CCS can help solve several problems
Axelsen emphasizes the importance of the three international organizations with recognized expertise on carbon capture and storage joining forces to provide advisory services worldwide.
“In many countries, CCS now is being highlighted as a vital part of the solution not only to the climate change, but also to reorienting the economy into a green and just future with minimum disruption to the regions of the world relying on heavy industries. Together with DNV GL and SINTEF we want to actively contribute to a sustainable future by sharing our knowledge in CCS,” he says.
TCM conducts testing of new technology for carbon capture
At Technology Center Mongstad (TCM), testing of new technology for carbon capture is now being carried out. Here, a research-based capture solvent, CESAR 1, is used with the aim of capturing CO2 at the lowest possible cost.
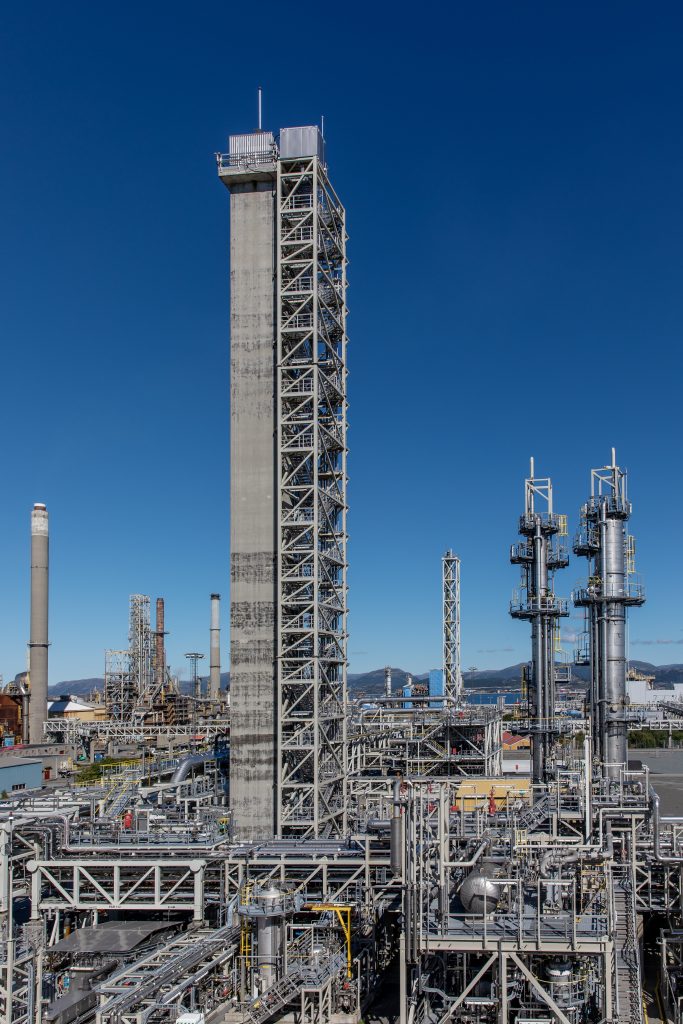
– The advantage of testing at our facility is that you get to test relatively mature capture technologies under almost the same physical conditions as with CO2 capture at full scale, says head of Technical Support at TCM, Muhammad Ismail Shah. – We are excited about the results of the testing, which is expected to be available by the end of the first quarter next year.
It is the owners of TCM, Gassnova (on behalf of the Norwegian state) and the industrial partners Shell, Total and Equinor, who together have initiated the implementation of the test with CESAR 1.
The reason is that the International Energy Agency, through its Greenhouse Gas R & D Program (IEAGHG), has requested a comprehensive assessment of new technologies for CO2 capture in the energy sector, and an evaluation of their potential to reduce costs associated with the operation of full-scale facilities.
– Fossil fuel-based energy producers need to reduce their climate emissions, and new capture technologies can help them along the way if these technologies are sufficiently cast-effective, Shah says.
TCM has previously conducted several tests of technologies with the carbon capture solvent MEA (Mono Ethanol Amine) and has managed to capture up to 98 percent of CO2 emissions with aqueous MEA (a mixture of water and MEA). IEAGHG has proposed a capture liquid with a different open and available chemical content (PZ + AMP) as a reference in connection with testing of new technologies. With this catch liquid, a reduction in catch costs of 22 percent for coal-fired and 15 percent for gas-fired power plants has been achieved in experiments, compared with ordinary MEA catch liquid.
– The capture liquid now being tested, CESAR 1, consists of a mixture of the mentioned AMP and piperrazine, which is another liquid used in connection with the capture of CO2. We believe the CESAR 1 mixture has the potential to further reduce capture costs.
The testing with CESAR 1 is carried out with CO2-containg flue gases from the refinery at Mongstad, and will also demonstrate the performance and stability of this solvent over time, and provide answers to important health, safety and environmental aspects when using this technology. It is also an ambition to promote innovation in the field of carbon capture by relating the use of technology with this capture solvent to key economic terms for carbon capture and storage. One of the aims is to establish experiments with CESAR 1 as a reference when comparing with other technologies, and contribute to more innovation and creativity in the development of technologies for carbon capture.