New flue gas source at TCM
Technology Centre Mongstad (TCM) offers users of the test facility a new flue gas source (MHP flue gas).
In 2017
In 2017, Equinor decided to execute a plan to shut down the combined heat and power plant (CHP) in the coming years. This CHP plant is located adjacent to TCM testing facility and is based on a combined cycle gas turbine (CCGT) with two gas turbines, each with a waste heat recovery unit. The plant is fuelled by a mixture of natural gas from the Troll offshore gas field and refinery fuel gas.
In 2022
In the third quarter of 2022, Equinor completed the shutdown of the CHP plant and rebuilt one of the gas turbine trains into a new steam boiler, including revamp of the waste heat recovery unit. This plant is now referred to as the Mongstad Heat Plant (MHP). The intention of this steam boiler is to replace the old gas turbine.
As the MHP plant is only fuelled by the refinery gas, one of the main changes is the CO2 concentration in the flue gas, is 8 – 9 vol% compared to 3.5 – 3.7 vol% in the CHP flue gas.
Enable TCM to test at higher CO2 concentrations
Due to the design flexibility in the TCM amine plant, it should still be possible to provide low CO2 testing concentrations simulating CCGT type flue gas by diluting the MHP flue gas with air to around 3.7 vol% CO2. Moreover, this new flue gas type will enable TCM to test at higher CO2 concentrations up to 20 vol% CO2 (with CO2 product recycling to inlet) to mimic other industry applications such as steel and cement type flue gases.
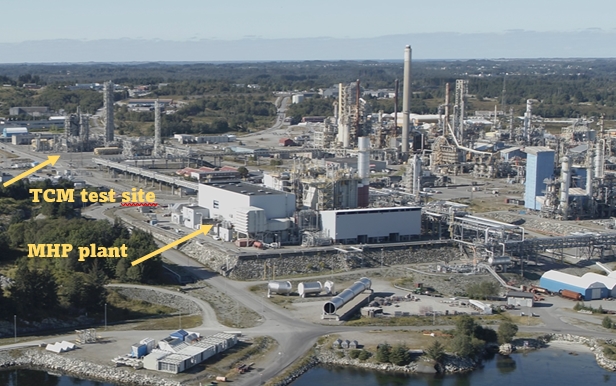
Mongstad Heat Plant (MHP).
She got a dream fulfilled at TCM
Christina Martavaltzi joined the team last year as Advisory Services Lead. – A dream come true, says Martavaltzi.
2022 marks Technology Centre Mongstad’s (TCM) 10th birthday. We are celebrating by interviewing a range of people have made their mark on TCM over the last decade.
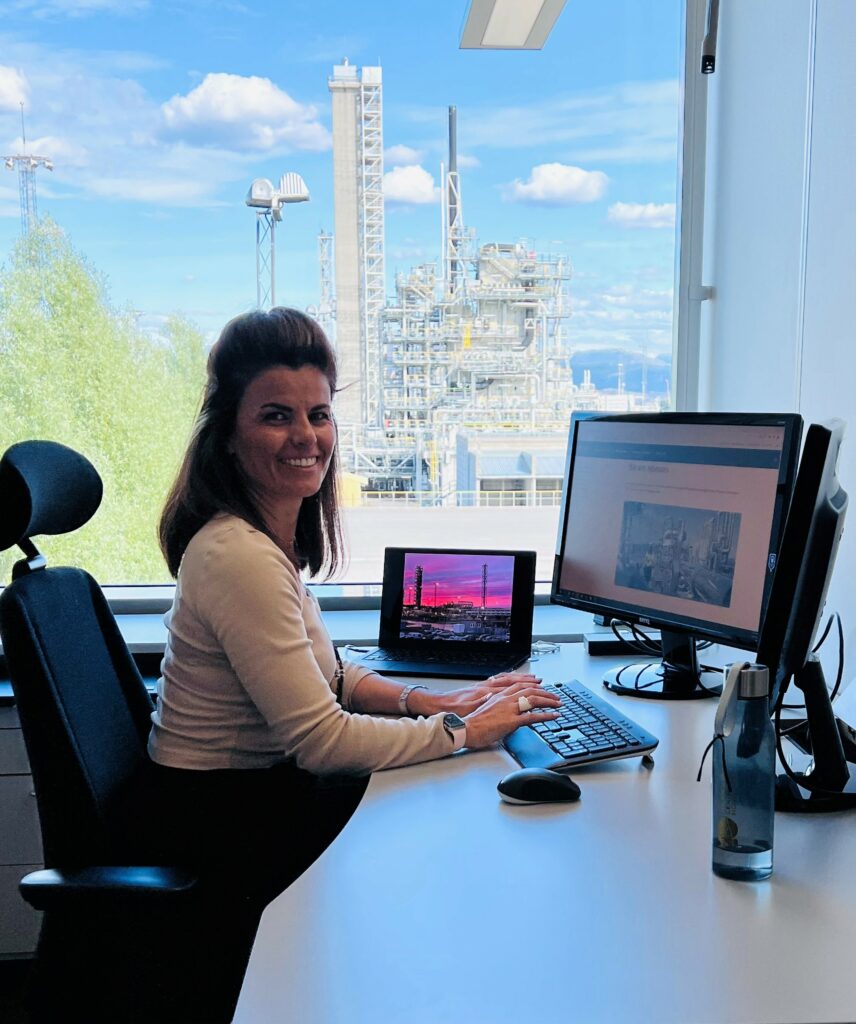
– Why did you apply for a position at TCM?
– When I first visited TCM back in 2013 as a member of the CO2 Abatement Research & Development team at Shell Global Solutions, I knew right away that I wanted to secure a role at Mongstad. On that visit, we discussed how to demonstrate a proprietary emerging capture technology. At the end of a packed day, there was no exhaustion – instead, I felt excited and motivated. A few days later, reflecting on the visit to TCM, I decided to make working there a career goal.
– Last year, Shell offered me the opportunity for a secondment, and I wasn’t going to let that pass me by.
– What were your first impressions of TCM in 2013?
– As impressive, exciting, and educational place to be. I’m a short Greek girl, and I remember trying to keep up with this tall Norwegian tour guide, trying to catch his every word.
– I couldn’t believe that after so many years in labs working with everything in miniature, I was now standing right next to a capture plant on an almost industrial scale! Obviously, I was following the exciting developments at the commercial CCS facilities that are using Shell technologies, but I’d never actually been up close and personal with a capture plant before then.
– I was also very lucky because the weather was unusually nice. I honestly couldn’t understand why people kept using comments about the weather as ice breakers. Now that I live here, I know! 😊
– What would you say is the most rewarding and interesting work you have taken part in at TCM since joining?
– The great thing about my job is that I’m at the centre of a team that is uniquely positioned to provide vital help to teams around the world who have ambitious plans to deploy carbon capture plants at their facilities. Every single time we receive enthusiastic feedback telling us that our support proved invaluable for the next phases of their projects and each time they come back to find out more from us, I know I have done my bit in helping the world to move a step closer to addressing climate change.
– What’s the most challenging thing about working at TCM?
– Its location, especially in winter. I really dislike driving in dark, but TCM is situated in a quite a rural area about an hour’s drive from Bergen where I live. That being said, I must admit that I do recognise that TCM is smartly located next to a refinery and power plant, which means we can utilise their flue gases and utilities for testing our technology under real industrial conditions.
– When you tell your friends and acquaintances about TCM, what do you emphasise as its most important aspect?
– That TCM is a powerful addition to our toolbox in the fight to reduce CO2 emissions. It is the only facility in the world that can support carbon capture technology developers in their efforts to fully de-risk their technology before commercialisation, and we are the only team in the world that can share the impartial expertise that is needed if technology buyers are going to make smart decisions independently.
– Looking back on 10 years of TCM, what should TCM employees past and present be most proud of?
– Back in 2006, the realisation that the technology and the financials were not mature enough for commercial scale applications lead to the decision to build a test facility to serve as the world’s centre of expertise in order to de-risk the technology. Since the opening its doors in 2012, TCM has – through a range of proprietary testing – contributed to creating a competitive commercial landscape by supporting key stakeholders as they de-risk their technology. TCM’s non-proprietary campaigns have also delivered invaluable knowledge to the scientific and industrial community, which has made it possible to overcome the barriers to deploying technology. Tackling key blockers such as emissions monitoring, emission permit process, operating with complex flue gases and of course reducing the cost of the technology are just some of the highlights on the list of TCM’s achievements over its first 10 years of operation.
– What are your hopes for TCM in the coming decade?
– I expect TCM to maintain its recognised position as the centre of expertise in amine carbon capture technology at engineering scale for years to come. I envision TCM’s task force growing its capabilities in emerging carbon capture technologies by deploying a series of both non-proprietary and proprietary testing campaigns at the emerging technologies site which launched last year.
Name: Christina Martavaltzi
Age: 45
Education: PhD in Chemical Engineering, Aristotle University of Thessaloniki, Greece
Marital status: Married
Afiliation with TCM: Lead Advisory Services since June 2021 (on secondment from Shell)
Present position: Lead Advisory Services at TCM
– You and your colleagues in Advisory Services are helping carbon capture initiatives both in Norway and abroad. Can you tell us about some of the projects you are focusing on?
– One of the main areas of focus for my team has been to provide support for “Longship”, which I believe is the biggest climate project ever undertaken by Norwegian industry, and with strong backing from the Norwegian Government. TCM provided Advisory Services to both of the primary capture projects encompassed in “Longship”. We provided expertise during early studies for the Hafslund Oslo Celsio Waste-to-Energy plant, for the full-scale project at Klemetsrud in Oslo, and we participated in the HAZOP assessment of the capture project at Heidelberg Cement’s Heidelberg Materials Brevik factory. We have also supported Statkraft, Kvitebjørn Varme and Hoegh LNG in a range of other important Norwegian CCS projects.
– TCM also provided advisory services to OGCI (Oil and Gas Climate Initiative), the USD $1 billion climate fund founded by the world’s largest energy companies. Examples of other projects that have requested TCM’s support have included Net Zero Teesside, Phillips 66 and SSE Keadby, all of which are leading projects in the British CCS sphere that are most promising.
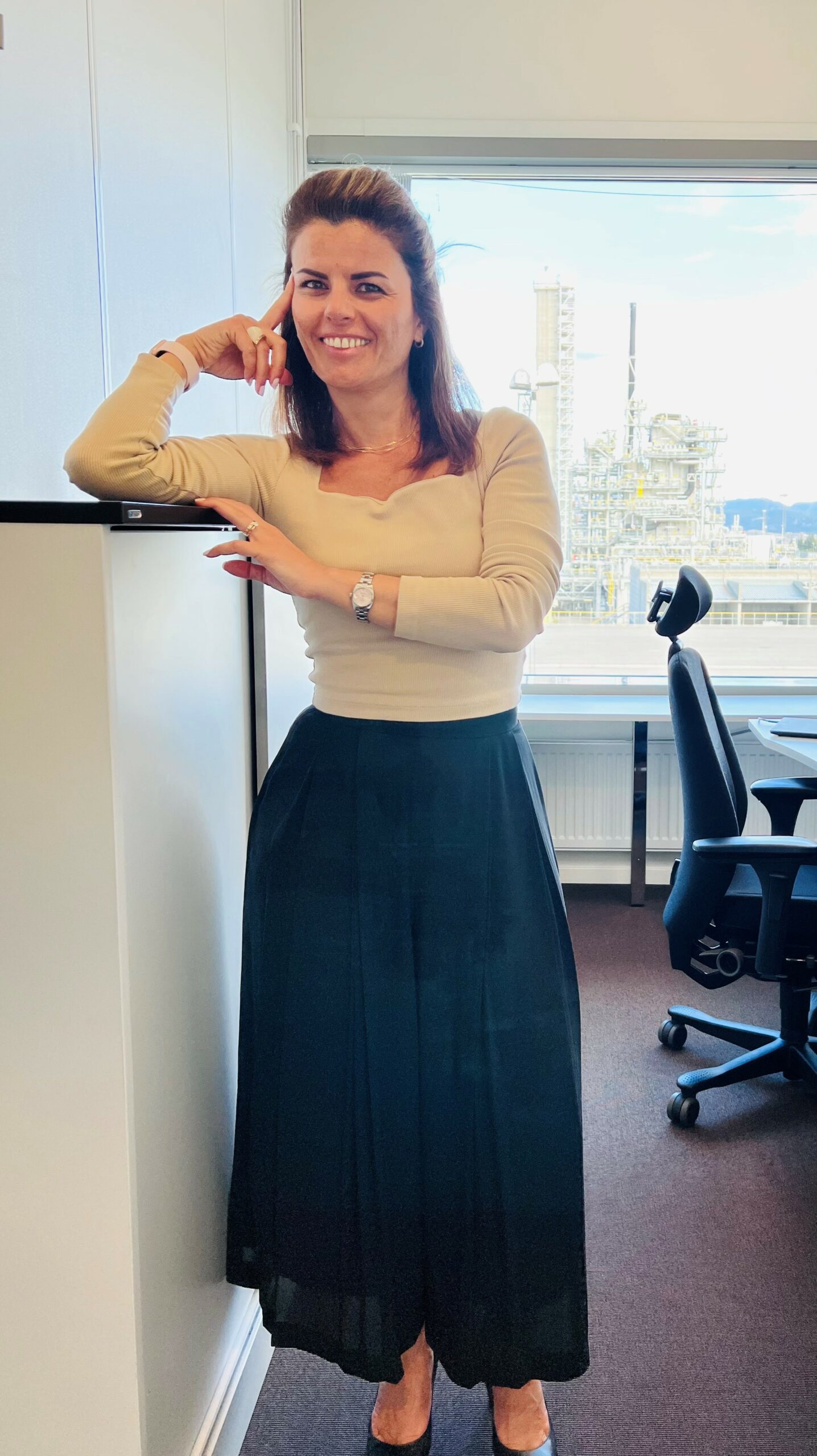
– TCM has not outplayed its role
– The research community at SINTEF believes that Technology Centre Mongstad (TCM) has an important role to play in demonstrating technologies so that they can be scaled up, thereby creating a viable CO2 capture and storage industry and elevating other climate technologies, Alexandra Bech Gjørv, CEO of SINTEF
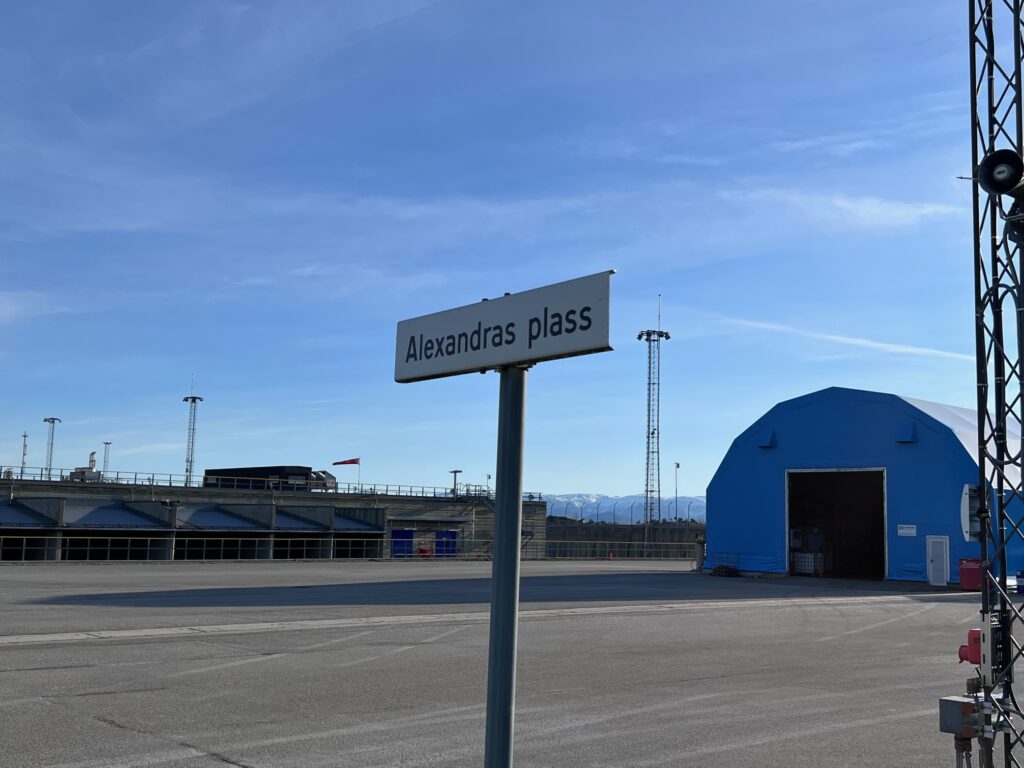
– My hope is that a strategy will set out the future of CCS investment in Norway, exploring needs and trends and how to respond to these through interaction between centres of knowledge and infrastructure stakeholders, says Alexandra
Familiar with the history of TCM
She is more familiar with the history of TCM than most, having been tasked with overseeing the construction of the world’s largest and most flexible test centre for carbon capture when she headed up the New Energy division at what was then StatoilHydro. Nevertheless, she emphasizes that her commitment to TCM is not based on rose-tinted nostalgia, but on the need for continuous technological development to achieve climate goals.
– Given the targets that have been set for CO2 capture both in Norway and in other countries, we still have a long way to go to if we’re to realize both large facilities and smaller projects. As an industry, CCS needs to be scaled up, and the cost of each unit of CO2 captured must come down. If we’re going to succeed, we need further investment in research and development. In that regard, both SINTEF and TCM have key roles to play.
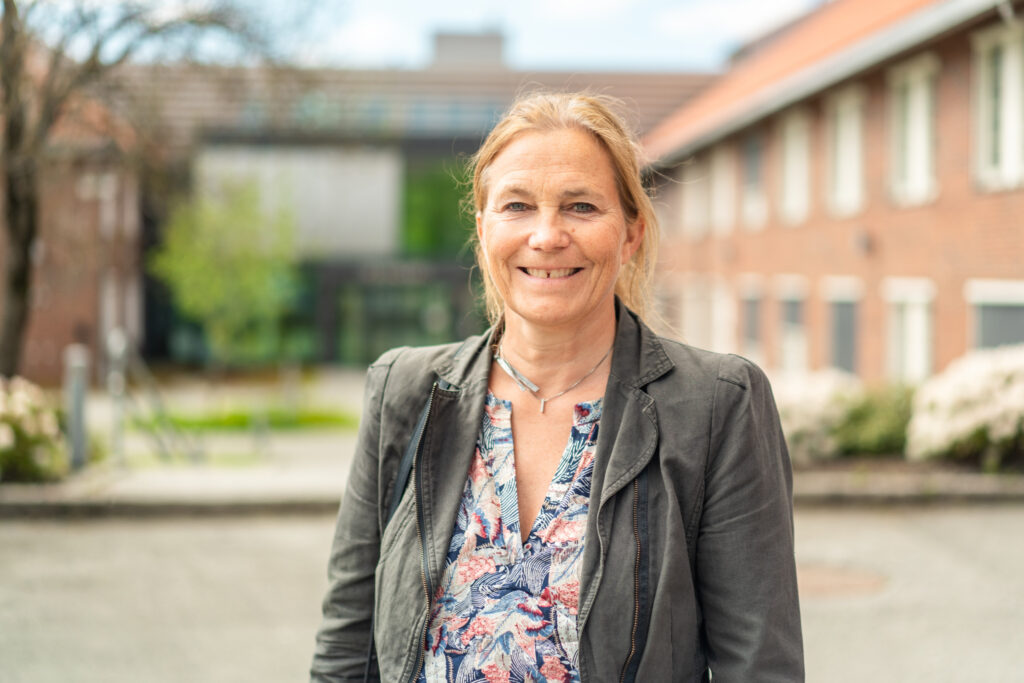
The CEO of SINTEF, Alexandra Bech Gjørv, played an important role in the creation of Technology Centre Mongstad. Photo: SINTEF
CCS a crucial investment area
Gjørv agrees with the designation of SINTEF and TCM as ‘toolboxes’ for the development of technologies for carbon capture to meet the needs of the society.
– We have been able to work well together, with our researchers working on tasks that have laid the foundations for solutions that have gone on to be tested and validated by our colleagues at Mongstad. In addition to capture technology, SINTEF has spent decades working on solutions for the transport and storage of CO2, and we are seeing increased commercial interest in this area as well. Overall, CCS constitutes a significant part of SINTEF’s portfolio. We are focusing extensively on research into hydrogen, both as an energy carrier and as an industrial raw material for various industrial stakeholders who must find their practical solutions to achieve net zero or carbon negative solutions.
Having trained as a lawyer, Alexandra Bech Gjørv practised as a partner at Hjort before being appointed CEO of SINTEF in 2016. She became a familiar face to many in Norway for her work as chair of the independent commission tasked by the government to investigate what went wrong before and during the terrorist attacks in the Norwegian Government Quarter in Oslo and on the island of Utøya on 22 July 2011. Prior to this, she spent many years as head of New Energy at Norsk Hydro and later as part of the merged StatoilHydro entity (now known as Equinor), where project responsibility for TCM became one of her main tasks in 2007.
The devil is in the detail
– At Hydro, I had worked on positioning the company commercially for the storage of CO2, but capture was a new area for me, even though Hydro’s researchers had also worked a lot on this. If I were to characterize the experience of overseeing construction of the technology centre, the words painful and instructive spring to mind. It was a project with very high levels of political visibility which had been initiated based on an unfinished draft of a project plan with cost estimates that turned out to be unrealistic. It required a lot of work and effort both to make a good plan and to create an understanding that the real cost was going to be at a completely different level than had first been envisaged. This experience with TCM has served me well since then. Among other things, I have contributed to the fact that an enormous effort has been put in over many years related to quality assurance of the plans for the Ocean Space Center in Trondheim, says Gjørv. – The devil is often in the detail, she adds.
Kept faith in what was important
– But even though TCM as a project was anything but plain sailing, it also taught me valuable lessons in not losing faith in things that are important. It’s worth noting that other key individuals from that project have gone on to bigger things: Sverre Overå, who managed construction of the facility, is today project director for Northern Lights. The person I dealt with most in government as part of the project, Andreas Eriksen, has gone on to be the Secretary General at Ministry of Petroleum and Energy.
Unique facility – relevant expertise
Alexandra Bech Gjørv emphasizes that capturing CO2 will be vital if we are address climate change.
– At SINTEF, we believe that both those who will deliver proven technology to full scale capture facilities and those who will introduce new technologies will need to make use of the unique facilities TCM offers. We are eager to collaborate with them on this, and also on the development of other climate technologies. Congratulations on your 10th anniversary – and good luck for the future!
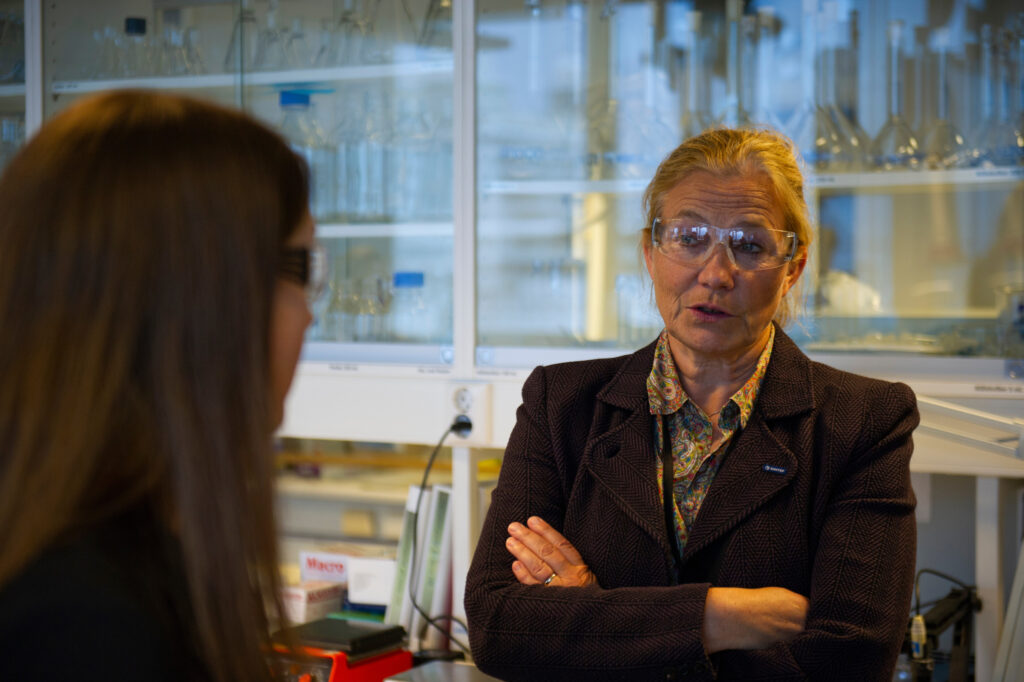
Photo: SINTEF
He had seven rewarding years at TCM
Thomas De Cazenove came from the Netherlands to Norway with his familiy in 2013, and worked for seven years at TCM. – An important part of my career I would not have been without, he says.
Technology Centre Mongstad (TCM) has a 10-year anniversary in 2022. We celebrate ourselves with interviews with people who in various ways have had impact on the business in these years.
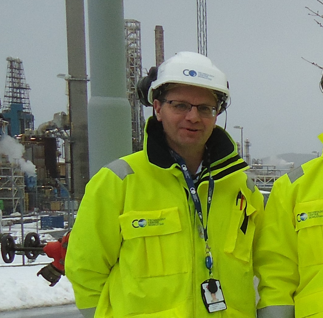
Thomas De Cazenove worked at TCM for seven years, the last three as Technology Manager.
– Why did you apply for a position at TCM?
– Before I started at TCM, I had worked for seven years as a Specialist advisor on amine and caustic treating processes to world wide clients, within CO2 capture, refineries, LNG, GTL and sour gas processing facilities. This included development of scouting and feasibility studies and test run simulations for various plants, and also some trouble shootings. When the opportunity for an engagement at the newly started test center at Mongstad opened up, I thought this both could be very evolving and interesting, and that I had something to contribute. I have never regretted that decision.
– How was your first meeting with TCM?
– I cannot now remember what happened my first day at Mongstad. But what is strong in my memory was that I was fascinated by the size of the facility. TCM is unique in the world, both in terms of size, flexibility and not least competence. I therefore realized early on that here I was going to thrive. The family had then established themselves in Stavanger, and I commuted three to four days a week to Mongstad. In the first years I lived in an apartment nearby, before I moved to Bergen.
– What will you highlight as the most rewarding and interesting work you took part in at TCM?
– I started my work at TCM just over year after the opening and was like everyone else excited about whether testing of technologies seemed as assumed, that is, whether theory and experiments in laboratories could actually be put into practice. Not least, it was important to measure and to document that the emissions were within the regulations laid down by the Norwegian authorities. The most rewarding and interesting thing was to experience that as a result of collaboration at a high professional level, we succeeded in measuring results and continuously making improvements in operation and performance – to the delight of both the customers and the entire CCS community.
– Are there projects or events you remember back with special joy?
– What I look back on with the greatest joy is the open test campaigns the owner companies with partners planned and carried out. With these, we had full control of all input factors and preparations. The campaigns resulted in important learning that made it possible to set a baseline for the operation of full-scale capture facilities using the amine technology.
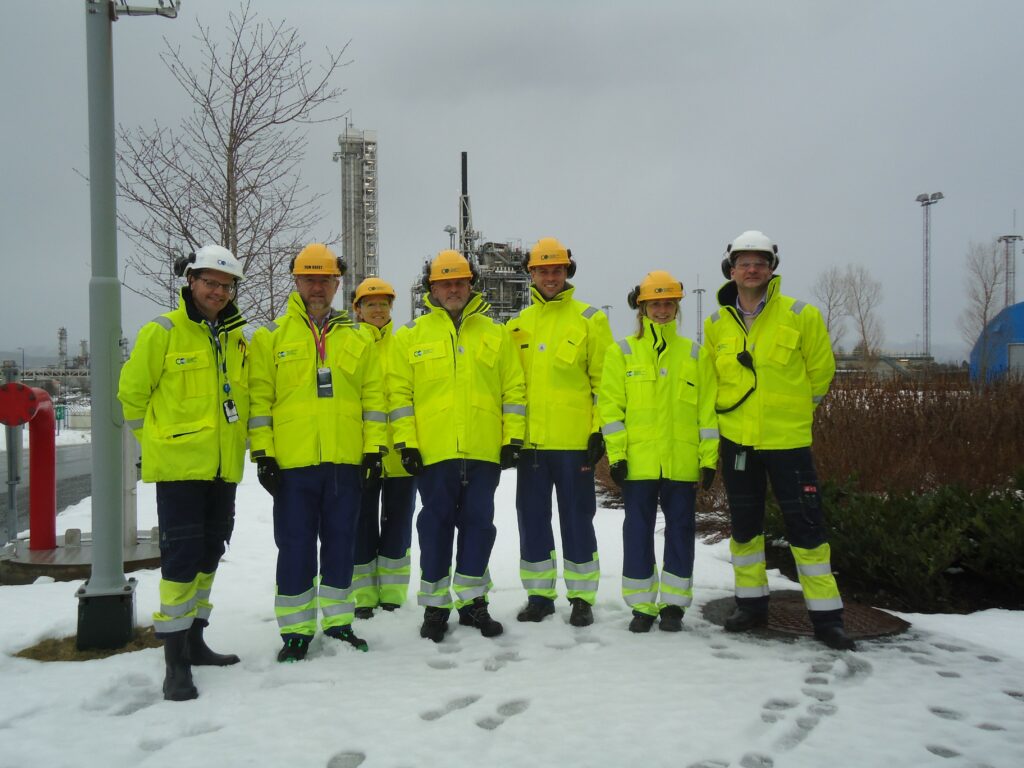
– What do you think of as most challening about your work at TCM?
– My most important experience was the good team spirit that characterized the business. Ability and willingness to discuss and to solve problems across the organization was generally very good. Disagreements could still sometimes arise between departments when it came to priorities, which could be a bit challenging, but no worse than that in the end good and committing solutions were found that everyone could agree on.
– When you generally look back on 10 years of business at TCM, what do people that worked at TCM or still are working there have particular reason to be most proud of?
– I will mention two things; the fact that TCM has and continues to be relevant as an arena for testing technologies for industrial deployment, and the importance TCM has as a provider of knowledge to the CCS community worldwide. The scientific articles TCM has produced and presented have been of great importance for the industry and have made the company an internationally recognized brand.
– What is your wish for TCM the next ten years?
– My hope is that TCM succeeds in strengthening its position as a world-leading center for testing and improving both mature and new technologies. I wish all my colleagues and friends at Mongstad the best for the years to come!
Name: Thomas De Cazenove
Age: 54
Education: Master’s degree in Engineering Chemistry, CPE Lyon
Marital status: Married, four children
Affiliation with TCM: Seconded from Shell as a Senior process and environment advisor 2013 – 2016, Key account manager at the Business Development Department 2016 – 2017 and Technology Manager 2017 – 2020
Present position: Senior Engineer CO2 Abatement Deployment, Shell
– When you tell your friends and acquaintances about the business at TCM, what do you emphasize as the most important utility value?
– In relation to my colleagues at Shell, I use to highlight the fantastic opportunities TCM offers, both by virtue of the size of the plant, the various flue gases that can be used in testing and the flexibility that operation 24/7 by skilled personnel entails.
When it comes to “ordinary people”, there have long been many in the Netherlands who have been skeptical of carbon capture and storage, but that mood is about to change. I emphasize the importance of the fact that TCM has tested the efficiency and safety of technologies that are now available in the market and are being used in full scale in industries both in the Netherlands and several other European countries. In this way, TCM has been crucial in reducing greenhouse gas emissions.
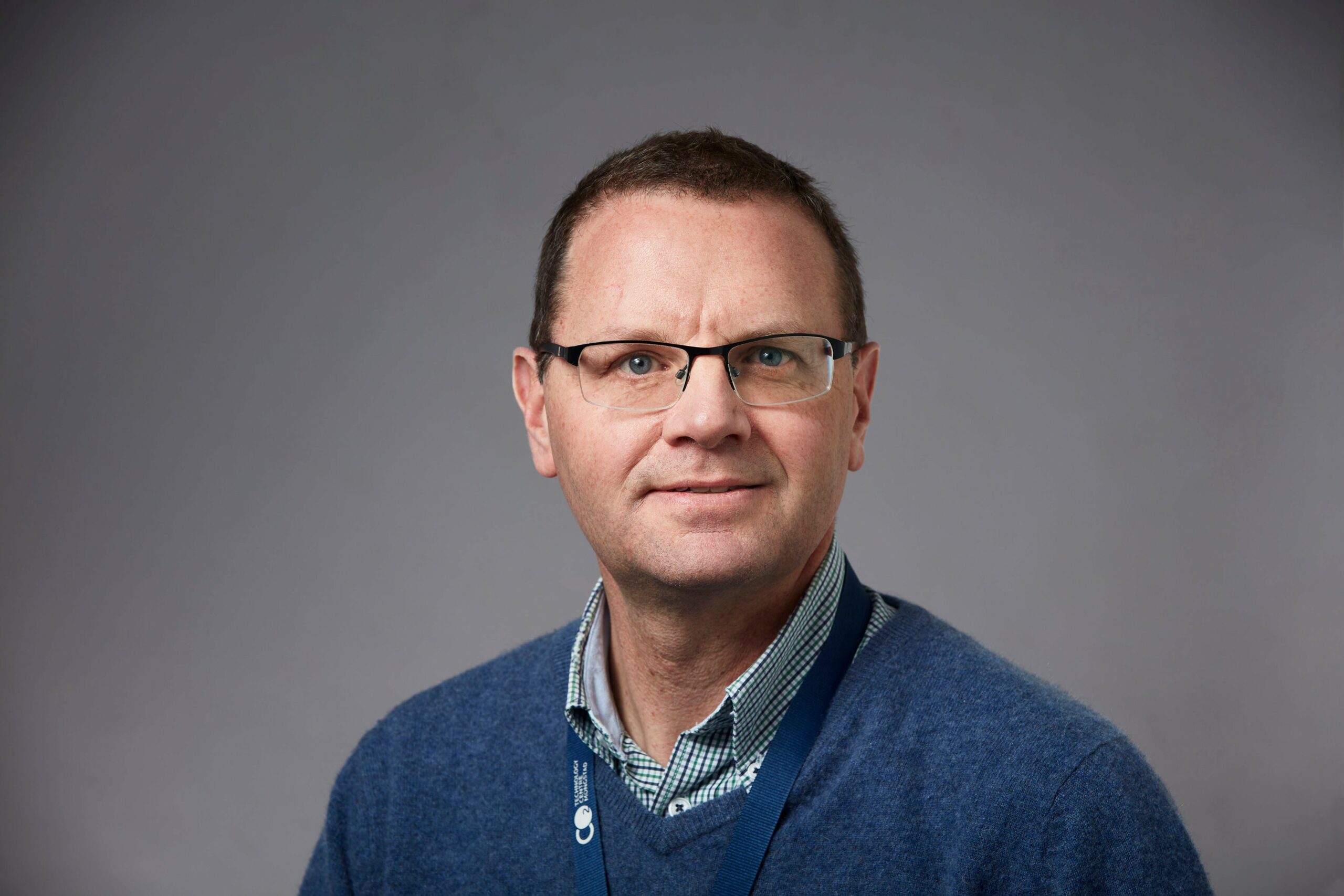
He had the dream job at TCM
Espen Steinseth Hamborg was Technology Manager for four years. – I had the dream job, he says in this interview.
Technology Centre Mongstad (TCM) has a 10-year anniversary in 2022. We celebrate ourselves with interviews with people who in various ways have had impact on the business in these years.
– Why did you apply for a position at TCM?
– After having taken my doctorate in CO2 capture, in 2012 I was employed by Equinor to work in this field. Just over a year later, the opportunity opened to become Technology Manager at TCM. I had then mostly worked in laboratories, and thought it was incredibly exciting to be able to contribute to the development of capture technology and knowledge in an industrial environment. So I applied, and was the lucky one who got the job.
– How was your first meeting with TCM?
– For me, the transition was smooth, because I had also participated in the process of building the technology centre. In the spring of 2012, I spent some time at TCM to see and learn, and also got to participate in the ceremony when Jens Stoltenberg opened the facility. My interest in what we could achieve with the technology centre had thus long been very alive. So when I started working in October 2013, I had a very strong and good feeling that I should now be able to work with what I really wanted. The expectations of both my own and the skilled technology colleagues were high.
– What will you highlight as the most rewarding and interesting work you took part in at TCM?
– When I started, there was a lot of skepticism about carbon capture as a concept, both in Norway and internationally. Therefore, we felt a very strong obligation to prove that we could actually help create a new industry that was useful in the climate battle. TCM’s role has been and is to demonstrate that the capture of CO2 from flue gases is possible, through testing and qualification of various technologies and technology suppliers. However, at that time we moved into an unknown landscape, which was both exciting and at times a little intimidating. What I look back on as most rewarding is that we succeeded in moving boundaries and breaking down barriers in technological development. This is due both to the fact that TCM has the best facilities and personnel in the world that attracted the best technology suppliers and research expertise, but also that we had strong owners who were willing to invest in what we were doing.

Espen Steinseth Hamborg (to the right) was the Technology Manager at TCM in the period 2013 – 2017. – My best memory is that we gathered employees with different mindsets, approaches and views to professional discussions around the same table, and found solutions that in total were very good.
– Are there projects or events you remember back with special joy?
– The fact that we, together with Aker Carbon Capture (now Aker Clean Carbon) and Cansolv Technologies, managed to carry out their test campaigns in 2013 – 2016 with very good results, was of great importance both to Aker, Cansolv and to TCM. Among other things, this laid the foundation for us in Norway now realizing CCS as an industry through the Longship and Northern Lights project – without a doubt very gratifying.
What I remember as special both with this and later test campaigns, was the fantastic team effort that was put in by people from the various units at TCM. Involving people from different cultures and with different backgrounds in processes to achieve common goals can be demanding. But in a relatively small organization like TCM, it is both a virtue of necessity, and it gives enormous power if one succeeds. My best memory is that we gathered employees with different mindsets, approaches and views to professional discussions around the same table and found solutions that in total were very good.
– What do you think of as most challenging about your work at TCM?
– Everyday life at TCM generally went without major frustrations. It was enough to hang our fingers in, and the progress we experienced stimulated constant efforts and improvements. What was a bit tiring was how people in the environment – and especially in the media – related to the business. The use of CO2 resources on management and CCS was and is still challenging, and it became demanding time and time again to explain that what we were doing was not a waste, but an important measure for the climate.
– You say you had your dream job at TCM, what made you quit as Technology Manager?
– My departure was solely for a private reason. I commuted between Drammen and Mongstad, and in 2017 our first child was born. I prioritized the dad role over TCM, and have not regretted it.
– When you generally look back on 10 years of business at TCM, what do people that worked at TCM or still are working there have particular reason to be most proud of?
– It is that TCM has been a crucial contributor to the development and realization of the value chain for capture and storage of CO2 in full scale, both in Norway and globally. Both those who have invested in TCM and those who work there have had faith in it all the way – and everyone can rightly be proud of it.
– What is your wish for TCM the next ten years?
– TCM will exist as a technology centre that is both the most influential in the world and has a unique strength of knowledge, given that it makes the business relevant to new low-carbon technologies, such as hydrogen. I hope both the owners and the employees see the potential in expanding the repertoire for climate technology. TCM has all the possibilities.
Name: Espen Steinseth Hamborg
Age: 42
Education: Master’s degree in chemical process technology at the Norwegian University of Science and Technology (NTNU) in Trondheim and doctorate in CO2 capture from the University of Groningen (RUG), the Netherlands
Marital status: Married, two children
Afiliation with TCM: Technology Manager 2013 – 2017, seconded from Equinor
Present position: Principal Researcher hydrogen and CCS in Equinor
– When you tell your friends and acquaintances about the business at TCM, what do you emphasize as the most important utility value?
– For my own part, I emphasize that I will hardly get such an exciting job again as the one I had at TCM. I tend to say TCM represents the largest research effort on technology in Norway since the Halden reactor, which was in operation for 60 years until it was shut down in 2018. The investment in the development of technologies for capturing CO2 is and will be an absolutely necessary part of the climate battle, and I think most people gradually beginning to understand that.
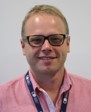
She remembers the great enthusiasm
Jorunn Brigtsen worked with business development and remembers the great enthusiasm that characterized both her colleagues at TCM and the many she met with the technology suppliers.
Technology Centre Mongstad (TCM) has a 10-year anniversary in 2022. We celebrate ourselves with interviewing people who in various ways have had impact on the business in these years.
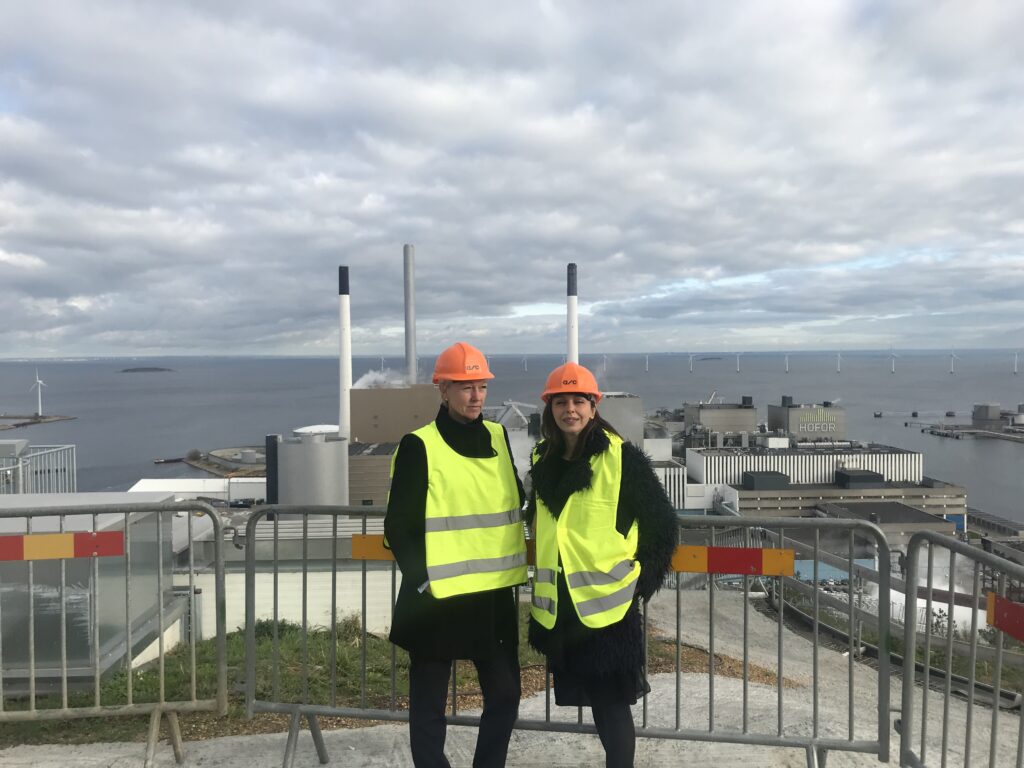
Jorunn Brigtsen and Leila Faramarzi at the top of the «skiing facility» at the combined heat and power waste-to-energy plant Amager Bakke in Copenhagen, in connection with a conference.
– Why did you apply for a job at TCM?
– I had long been interested in environmental issues and technologies and wanted to work with climate-reducing activities. When TotalEnergies in 2017 had become an owner of TCM, I had also taken further studies in environmental technology. As a result of vacancies in TCM being made available to us at TotalEnergies, I immediately applied for a position that was advertised in the business development department. Bjørn-Erik Haugan, who headed the department, met me for an interview at the airport at Torp. I was very happy when I received the offer.
– How was your first meeting with TCM?
– The agreement was that I would commute from Stavanger and stay at Mongstad for the first few weeks. I was well received from day one. One of the things that is unique about TCM is that even though the organizational model with secondees from owner companies involves rotation of the staff, people are cordial and inclusive. I got an introduction to the facilities to familiarize with projects and tasks. Then followed very interesting and educational years with stays both at Mongstad, at Gassnova and around the world.
– What was your most rewarding and interesting work at TCM?
– I was lucky to get the opportunity to work with many different technology suppliers who are incredibly dedicated to their projects. The aim was to facilitate possible testing of their technologies at TCM. What gave me most was to experience the great enthusiasm for something larger than us individually. I do not think I will get another job that gives me such a satisfaction.
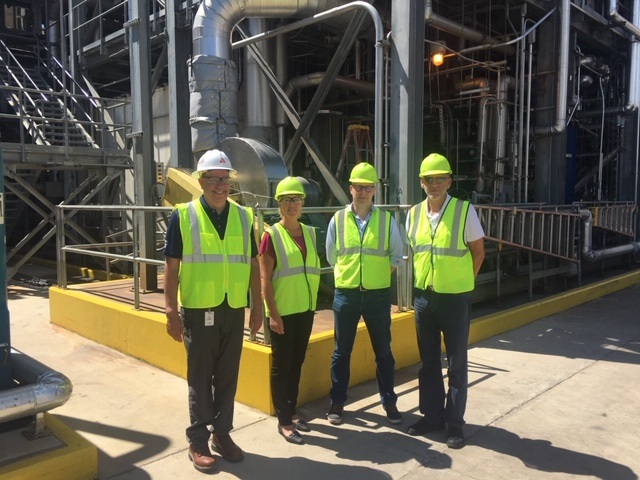
Jorunn Brigtsen here with former colleagues during a visit at the National Carbon Capture Center in Alabama, United States.
– Are there projects or events you remember back with special joy?
– TCM’s decision to establish the site for emerging technologies, gave us a great boost. It was very satisfying to contribute to the signing of contracts for testing with suppliers of membranes and sorbents, such as MTR, TDA Research and InnoSepra. In addition, it was always a pleasure to receive visitors at Mongstad, where everyone contributes to the guests having a good experience.
– What do you think is most challenging about your work at TCM?
– We worked hard to enter the European market. The funding schemes for technology development in the EU were few during the time I worked at TCM. This is in contrast to the United States, which had more structured support schemes to mature the technologies. European test campaigns were made possible in the form of collaboration with various research-based project groups.
– When you look back on 10 years of business at TCM, what do people that worked at TCM or still are working there have particular reason to be most proud of?
– It is the continuous work and dedication to facilitate testing, and to get the best out of the center and every campaign. This effort is the foundation for TCM’s fantastic deliveries.
– What is your wish for TCM the next ten years?
– There are still many CO2 capture technologies in the world that are immature, and which undoubtedly have great potential. My wish is that TCM for many more years can contribute to develop the best and most cost-effective technologies for the various industries and applications that will be used to achieve the goal of net zero emissions.
Name: Jorunn Brigtsen
Age: 53
Education: Bachelor’s degree in mechanical engineering at NTNU (Norwegian University of Science and Technology), Trondheim
Marital status: Partner, two children and four grandchildren
Affiliation with TCM: Key Account Manager and Test Development Manager in the Business Development Deparment 2017 – 2021, seconded from TotalEnergies. Member of the management team 2019 – 2021.
Present position: CCS Project Developer in TotalEnergies
– When you tell your friends and acquaintances about the business at TCM, what do you emphasize as most valuable?
– My short description is that TCM is the world’s largest center for the development of carbon capture technologies. Here, flue gas with a high CO2 concentration is captured from the chimney at the Mongstad refinery, which is used to test different CO2 capture methods. TCM contributes in reducing carbon capture costs and accelerate technologies to meet the climate challenge.
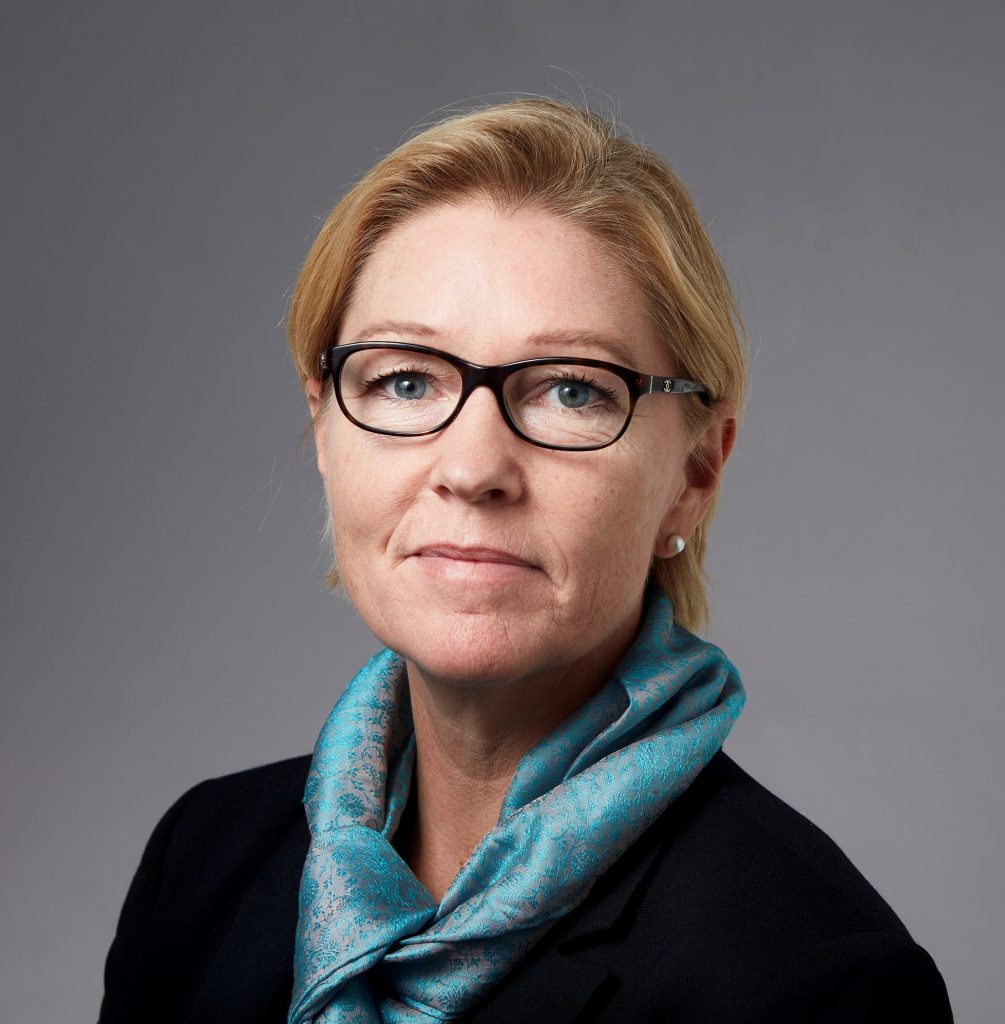
Photo: Styrk Fjærtoft Photo: Styrk Fjærtoft
Working at TCM never gets boring
With a recent doctorate in chemistry, Audun Drageset took over as environmental engineer in December 2018. At TCM, it never gets boring.
Technology Centre Mongstad (TCM) has a 10-year anniversary in 2022. We celebrate the anniversary by interviewing people who in various ways have had impact on the business during these years.
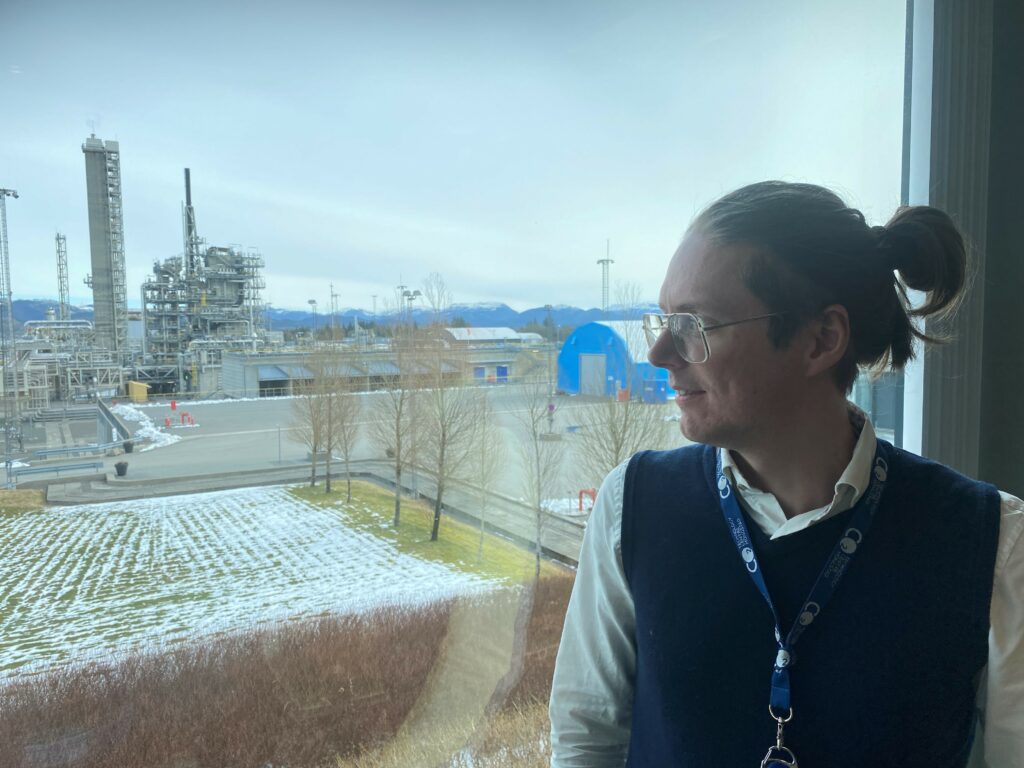
– We can be very proud to run a test facility that is world-leading in its kind, says Audun Drageset in this interview.
– Why did you apply for a position at TCM?
– When I had completed my doctorate in chemistry at UiB in 2018, I got a job in the laboratory of DNV in Bergen. One day the boss called out to the room; «Is there anyone here who knows anything about environmental chemistry», and I replied that I knew a little about it. The next day I drove to TCM at Mongstad for a meeting with the Managing Director, HSE Manager, Technical Manager and Operations Manager. I introduced myself and was informed about the tasks as an environmental engineer. The taskes were so interesting that I immediately took the offer I got a few days later.
– How was your first meeting with TCM?
– From the first day of work, I remember the sight of a big stack of documents lying on my desk waiting to be read. It was many scientific publications, the Pollution Control Act and a lot of regulations. I was introduced to my colleagues in the HSE Department and shown around the facility, and then it was just a matter of getting started. At this time, a test campaign under the auspices of the owner companies and SINTEF had just ended, and the preparations were made for the next campaign for the American Fluor Corporation. The professional issues were many and challenging – and right up there for a «nerd» like me.
– What will you highlight as the most rewarding and interesting work you took part in at TCM?
– With my background, working with emissions and environmental consequences related to CO2 capture has been very rewarding. Here, TCM has had several good supporters, not least Professor Claus Nielsen at UiO and meteorologist Dag Tønnesen at NILU. We have managed to build up a competence that many have benefitted from, but we are never fully trained or «finished». The interaction between professionals across the organization; in operations, technology, business development, as well as from the laboratory and maintenance, enables us to push boundaries and come up with solutions that strengthen the development of new and more efficient technologies. Our goal is to be a world leader in our field, and that makes everyday life very interesting and exciting. There is always something new to tackle, and it never gets boring.
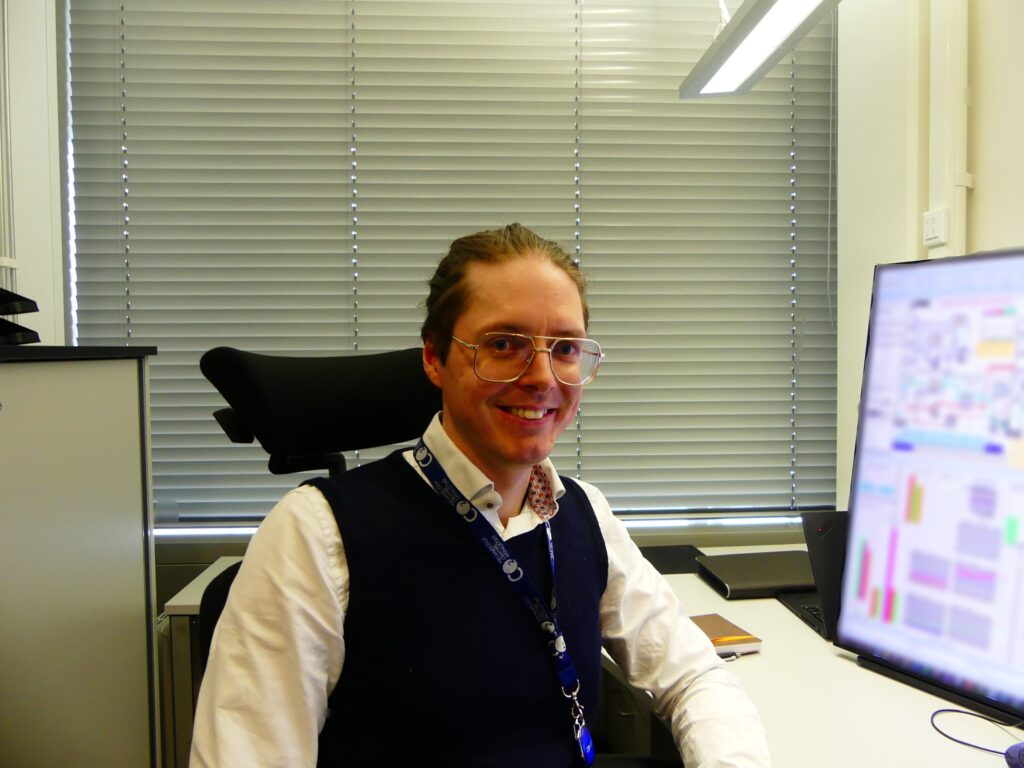
Audun Drageset has been an environmental engineer at TCM since 2018.
– Are there projects or events you remember with special joy?
– The test campaign we conducted last year for Mitsubishi Heavy Industries Engineering was a preliminary highlight. It was carried out during the pandemic, which was very demanding. We who were responsible for facilitation and implementation never met the customer physically, neither before, during, nor after the campaign ended last autumn. Still, it went incredibly well, and the Japanese are very happy.
The reason why we succeeded with the test campaign, was the ability to adapt both in the team at Mongstad and in Japan. For us, the digital dialogue with the customer started at 07.30 every morning, at the end of their working day. Results from the day before were reported and commented on, and goals for activities in the coming day were set. There were many long evenings during the more than five months the campaign lasted, to manage and follow up deviations along the way. It was very interesting!
When we finally were able to summarize the process, the feedback from Mitsubishi was that we had used the time very efficiently, which meant that they carried out far more tests than planned.
– What do you think is most challenging about your work at TCM?
– What I think is very interesting about this job is all the people I get to meet during meetings, conferences or when they visit the plant. I like to share what we are doing at TCM. It is especially interesting to attend events with representatives from other parts of the CCS «congregation» – researchers and others with same prerequisites who ask interesting and demanding questions. The prerequisite is then that we are in the process of preparing documentation for scientific publications, which must be 100 percent quality assured before we can publish the results. Sometimes I get questions about the tests before the result is published. It can be a bit tricky since I can’t give them an answer at that poing, even though I know what the results are. It takes time to document and verify results from the open test campaigns at TCM and give them a form that keep an academically level.
Professional presentations and discussions have suffered during the pandemic. That is why I am looking forward to the upcoming GHGT conference in Lyon in October. It will be incredibly nice to be able to meet old and new acquaintances who are passionate about carbon capture and storage.
– When you tell your friends and acquaintances about the business at TCM, what do you emphasize as the most important utility value?
– The most of my friends probably perceive me as a bit strange, someone who lives and breathes for something very special. But I think I have managed to convey that effective carbon capture technologies are a prerequisite for us to be able to implement the green shift. Testing at TCM contributes to the development of safe CO2 capture, which does not come at the expense of the local environment where the capture processes take place. I think it is important to emphasize that point.
– What is your wish for TCM the next ten years?
– My hope is that TCM will continue to be at the forefront of technology development. We have come a long way in these ten years, but it is obvious that there will be new and better solutions that must be tested and verified before they can be used industrially. We see this in the large number of inquiries and visits we receive from companies end environments that evaluate test campaigns with us, not leas ton the Site for Emerging Technologies. Whether I will be allowed to work at TCM until I retire may be doubtful, but I envision many good and interesting years ahead.
Name: Audun Drageset
Age: 32
Education: Doctorate (Ph.D.) in chemistry from the University of Bergen (UiB)
Marital status: Married
Affiliation with TCM: Environmental engineer, 2018 –
Present position: Environmental engineer, employed in TCM
– When you look back on 10 years of business at TCM, what do people that works/worked at TCM have particular reason to be most proud of?
– We can be very proud to run a test facility that is world-leading in its kind, which is used by technology suppliers and researched-based institutions from almost the entire globe. They come not only because the facilities are first class, but also because they are met by a very competent crew who provide them with excellent professional technical support along the way.
I also think we can be proud of our ability and willingness to share our knowledge both nationally and internationally. I am an active member of the Norwegian Chemical Society and have good contact with researchers at both UiB and other universities. The dialogue with qualified academic environments gives us a lot of useful knowledge back.
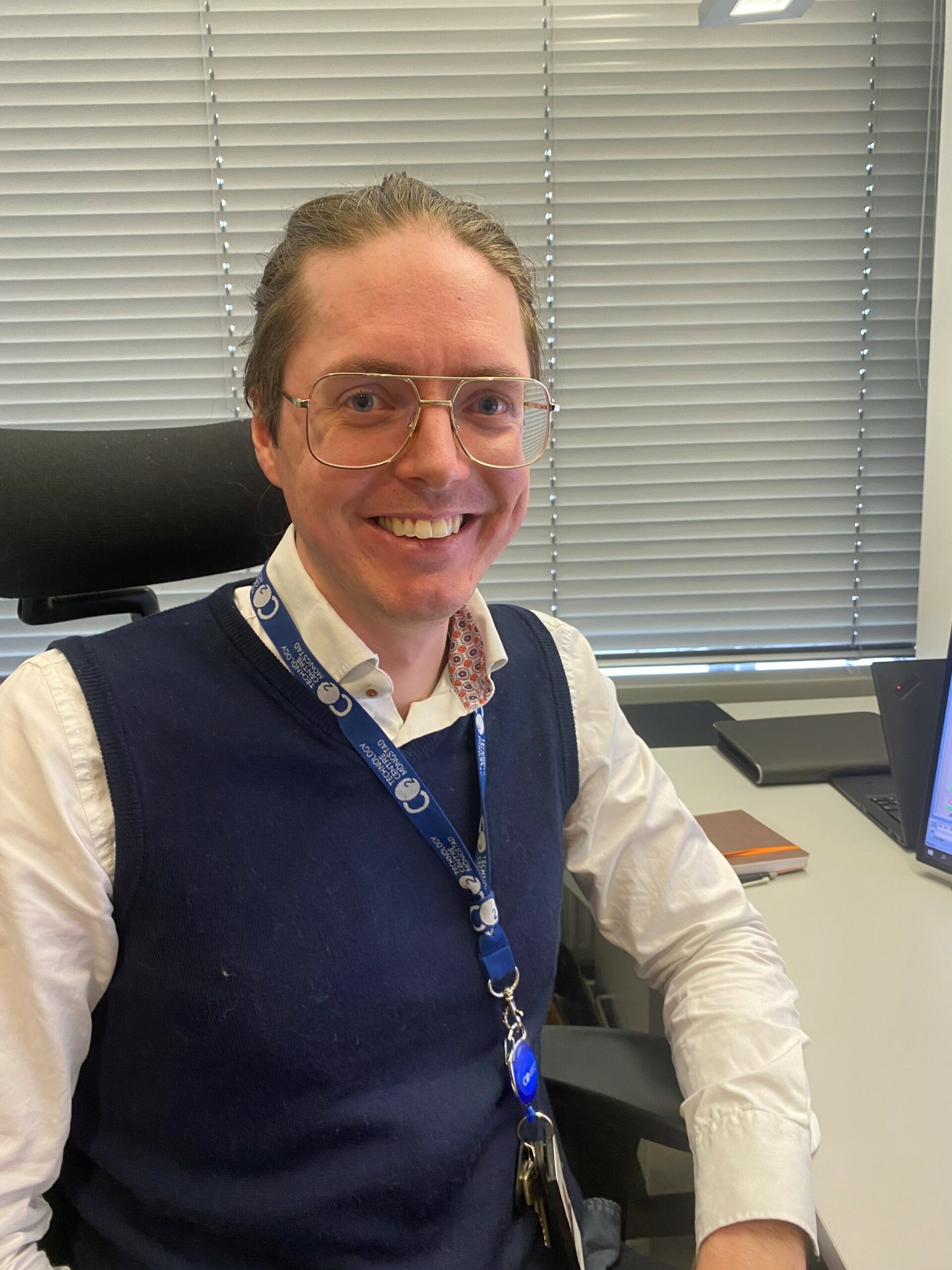
Photo: Styrk Fjærtoft Photo: Styrk Fjærtoft
– TCM has met great expectations
– After we put in place a realistic schedule and budget, the construction of the test facilwell. But best of all is that the operation of the plant has met our high expectations.
In my opinion, TCM has been crucial for carbon capture and storage going from being a good idea to a realistic solution and important contribution to the climate battle.
This says Sverre Overå (62). He was Equinor’s project manager for the development and construction of the test center at Mongstad. Since 2016, he has led the construction of Northern Lights, where the first part of the project will be completed and taken in use in two years. Phase two, starting in 2026, is under planning and the third phase is in the pipeline.
– The projects are similar in many aspects, both in that the owners are the same and that there is significant commitment from the Norwegian state. Expectations of results are high, both politically and in the population, and the strong element of innovation makes the work both challenging and interesting. But unlike the establishment of TCM, Northern Lights is very well anchored at the top of everyone who participates. This makes it easier to make decisions and ensure good progress during the project.
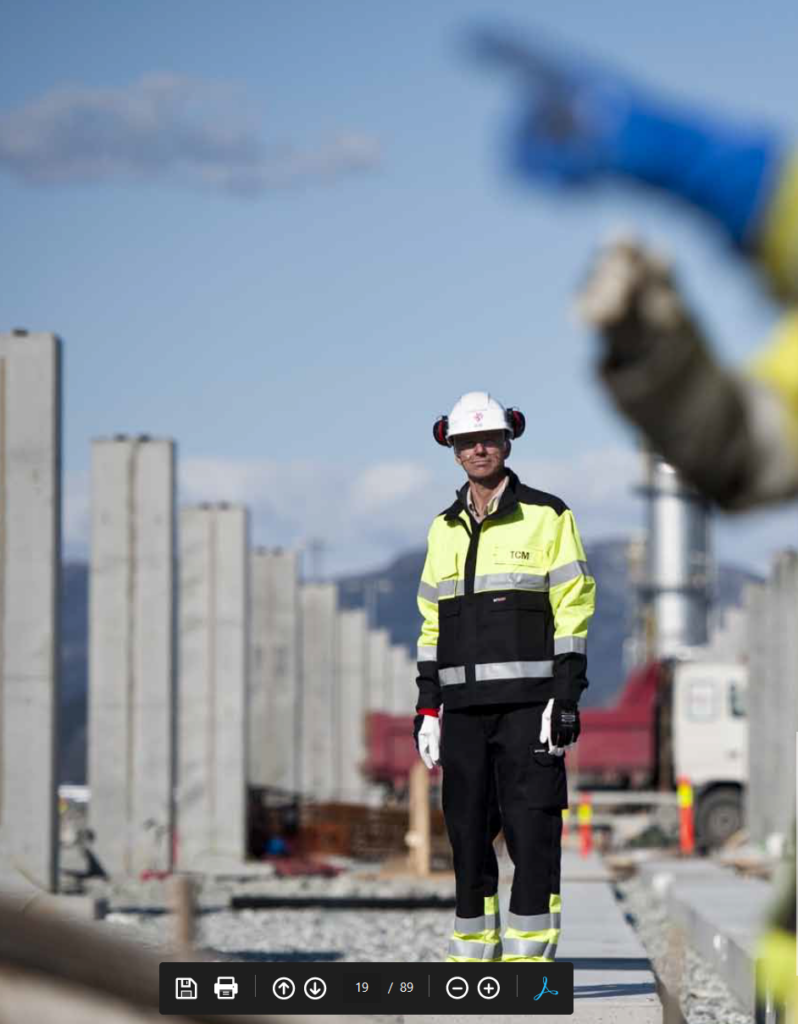
Sverre Overå was Equinor’s project manager for the construction of TCM. – The technology centre has been absolutely crucial for carbon capture and storage going from being a good idea to a realistic solution for achieving a reduction in greenhouse gas emissions – both in Norway and internationally.
Winding road to the goal
It was not straightforward to plan and carry out the construction of TCM. Sverre Overå’s entry into the project was in 2006 based on the job he had in Hydro’s oil department with the responsibility of CO2 management. The Stoltenberg government had taken the initiative to build a technology center, and Hydro, together with several other companies, was asked to provide an assessment of a project plan Statoil, now Equinor, had prepared – with the completion of the plant in 2009.
Based on the comments that came, a working group was set up on the initiative of Gassnova to revise the project plan. – The funny thing was that on the same day as we had our first meeting with Statoil, 18 December 2006, the StatoilHydro merger was announced by Helge Lund in the meeting room next door. We immediately thought that we could thus work completely in teams and were a little disappointed when we were told that it would be business as usual for another year.
The preparation of a project plan was more demanding than expected. It went almost two years before the project organization with Overå as a leader established itself in Stavanger. It soon proved more practical to work from Oslo, especially because all the contractor companies had their headquarters in the capital. In parallel, work was underway to establish the partnership agreement for TCM between Gassnova, Statoil and Shell, which was formally entered into at the founding meeting on 17 June 2009.
The local community was not prepared
– What was clear when we established the project organization at Mongstad was that the local community was unprepared for what TCM would entail. This applied to Statoil’s established organization at the refinery as well as local authorities and people. Many were surprised at how big the facility would be. In addition to a large parking area and pristine wilderness, we occupied barracks where Statoil’s pensioners’ association was located. Besides, we had to move the well-known Mongstad troll. This was not popular, to say the least, and for a while gave us the feeling of being a foreign element that took a little too much for granted.
However, these were not the only challenges for the project in relation to the surroundings. In both Austrheim and Lindås, there were current concerns that testing technologies for capturing CO2 would lead to dangerous emissions.
– This fear was a little strange, while they already had lived for many years with operations and emissions from a large refinery in the neighborhood. But it was also indicative of what one often experiences in processes that bring about change. People need time to adjust and get used to the new, says Overå, and adds:
– What I learned in particular and have taken with me from the TCM project is the importance of dealing with all stakeholders in a good manner, spending time listening and explaining to those concerned about conditions in a project they are interested in.
«Catching our future»
The establishment and construction of TCM is described in text and photos in the book «Catching our future». If you want to receive it, send an e-mail to hilde.bergum@tcmda.com
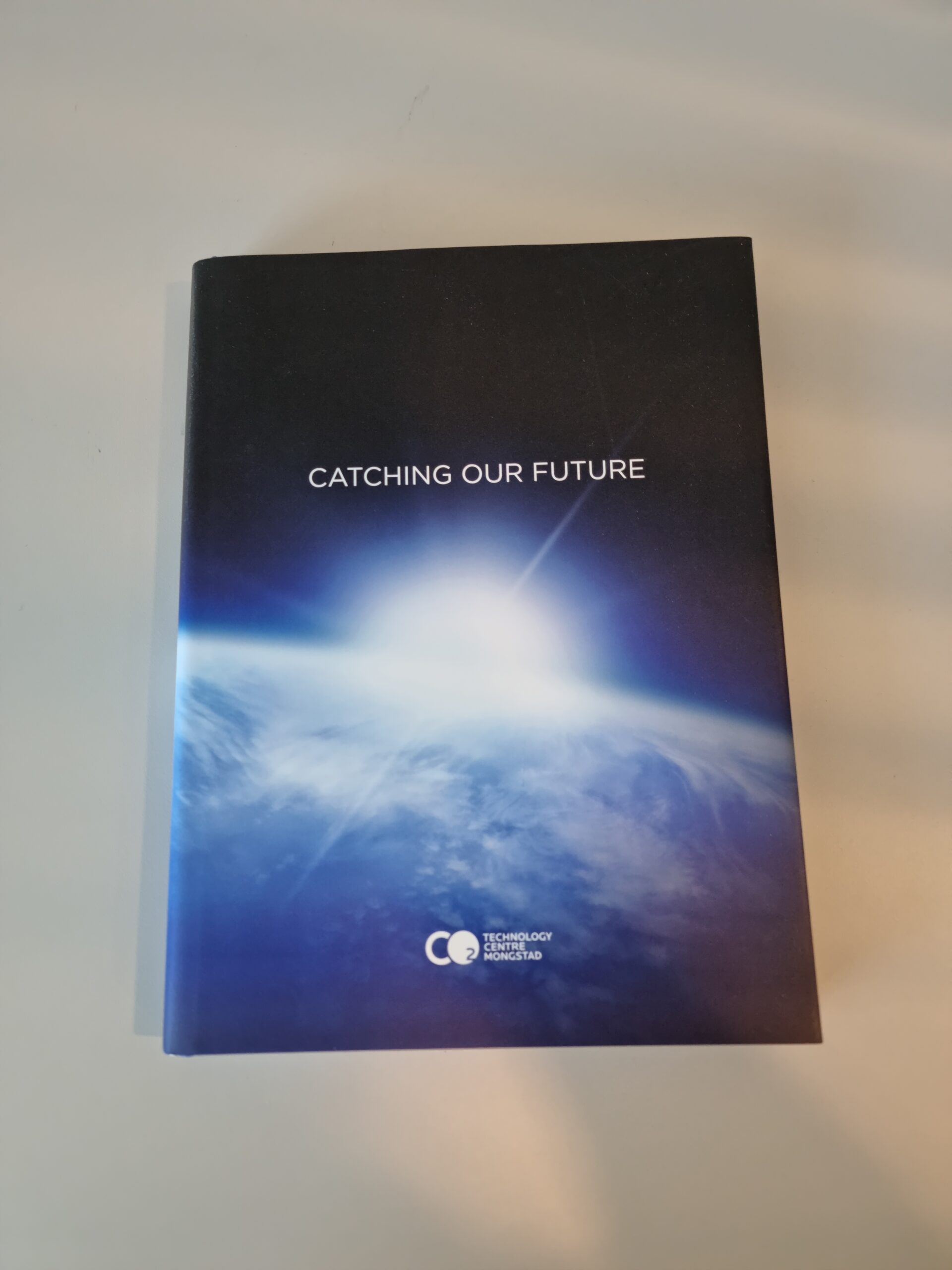
Has given «value for money»
Sverre Overå says that it was not uncomplicated to build the world’s largest test center for CO2 capture close to a large industrial plant.
– But when we first got started, I think the implementation of the project was good, both in terms of time and finances. That some thought the plant was too expensive is probably mainly due to the fact that the original cost estimates were too low. It is unfortunately the case that uncertain budget figures that are initially communicated for large construction projects tend to become entrenched and become a measure, regardless of what may be unknown cost factors or extra qualities in the project that are decided to be added along the way.
– Then it is also my opinion that the investment in TCM has been worth the money. The technology centre has been crucial for carbon capture and storage going from being a good idea to a realistic solution for achieving a reduction in greenhouse gas emissions – both in Norway and internationally. To test the use and effect of technologies that on the paper have looked good in the format TCM offers, is very important to be able to take the last step to use in full scale. Those who work at TCM with the operation of the facility have all the credit for that.
Arena for the development of new technologies
Sverre Overå believes that the expertise built up at TCM will also be valuable in the years to come.
– The potential for improvements in amine-based technologies is probably limited. Here, TCM has contributed to the development of a market with several good providers of technology that can be used in various industries. But TCM can still play an important role in the development of completely new capture technologies that provide significant reductions in costs and energy use than those currently available. It will be like the leap in the battery industry from production in lead to lithium. TCM has the physical areas and the infrastructure the technology developers need – and not least very skilled professionals in the field.
Sverre Overå (right) together with TCM’s first Managing Director, Tore Amundsen, in 2012. Both have had streets at the facility named after them.
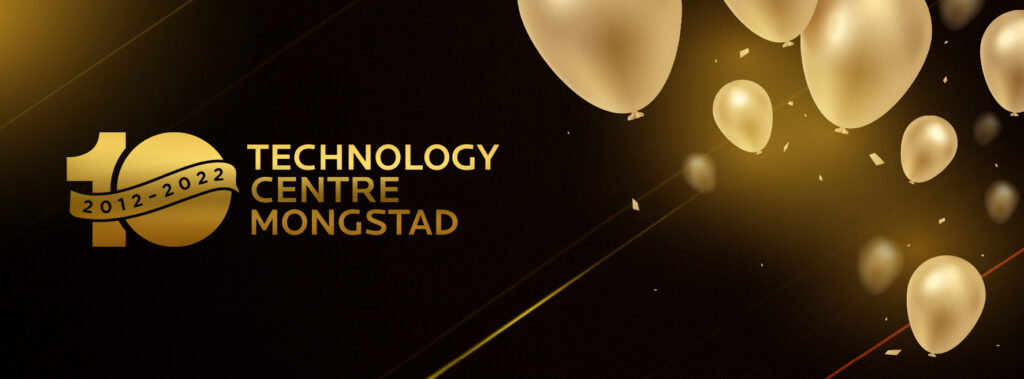
He was our first Technology Manager
Olav Falk-Pedersen was a key person during the years before and after start-up of the plant as Technology Manager and Business Development Manager.
Technology Centre Mongstad (TCM) has a 10-year anniversary in 2022. We celebrate ourselves with interviews with people who in various ways have had impact on the business in these years.
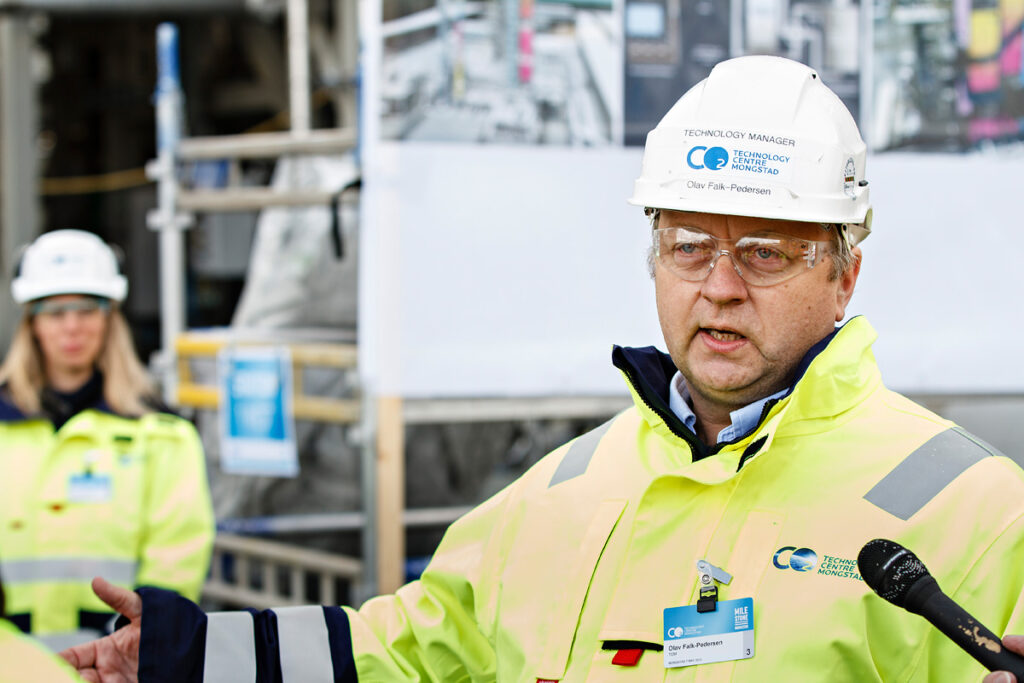
Olav Falk-Pedersen was TCM’s first Technology Manager.
– Why did you apply for a position at TCM?
– The positions in the group that was to plan the facility at Mongstad were advertised in the owner companies, and the team was put together with support from a recruitment agency. I then worked at Gassnova, and was their candidate for the position of Technology Manager. For me, this was by far the most exciting and challenging job in Norway I could think of, and was naturally very happy to be shown this trust. At the same time, I was aware that with the large amounts that were to be used and the prestige that was associated with the project, it was extremely important that we succeeded both technically and commercially.
– How was your first meeting with TCM?
– It was at Equinor in Sandvika where the project team stayed until the first time. After a few months, we were able to move to a barracks rig at the construction site at Mongstad, and when the administration building was completed, we moved in there. I myself commuted from the family on Nøtterøy, and lived in an apartment in Mastrevik with colleagues as neighbors, not far from Mongstad. We worked from early morning until late at night thorough the weeks and had the feeling of being industrial pioneers. Along the way, we were also given responsibility for designing the emissions application, which has later set a standard for a number of CCS projects.
– What will you highlight as the most rewarding and interesting work you took part in at TCM?
– Being allowed to build a team that would realize something that had never been done before was incredibly rewarding. It was very important that we got hold of people from Equinor, Shell and Sasol who were not only competent, but also were passionate about the project. I think we succeeded well in that. We were aware that different languages and cultures could be a challenge, but did our best to weld the gang together. Among other things, we cycled Rallarveien together to strengthen the unity and knowledge of each other.
I would also like to highlight the collaboration with Equinor at Mongstad, and the great people who were given responsibility for the operation of the TCM facility. I also remember the meetings with the technologists who came to test with us as challenging and exciting.
Then I must mention the many interesting and important meetings we had with politicians and bureaucrats centrally, but also locally. It was important that both in the political environment and in the media, an understanding of and confidence was created in what was to happen at TCM. Especially with the then mayor of Lindås, Astrid Aarhus Byrknes, we had many good and confidential conversations. She was forward-thinking and demanding, but at the same time very supportive. I got a lot of respect for her.
– Are there projects or events you remember back with special joy?
– The greatest moment was when we had come so far that we could state that “now we have control – now we start the plant!”. The road ahead had been demanding and long, so it was of course incredibly satisfying to be able to get started in earnest.
I also remember the opening on May 7, 2012 with great joy. Even though we had the weather conditions against us, it was a very special day and evening. I was quite central in the planning and implementation of the program, large-scale in every way with many famous guests. But the best thing was that everyone who had a role in the preparations and worked at TCM, got the feeling of participating in something great and important.
An event I also remember as gratifying was when TCM first presented results from the business at the world’s largest CCS conference in Austin, Texas. My role was to lead the session, and it was skilled colleagues who presented and had to answer difficult questions. They did so with a professional weight and authority that really made an impression on the audience. I, who knew all the thorough work behind it, felt that this academic recognition was well deserved.
– What do you think was most challenging about your work at TCM?
– Of course, it was also on TCM days that we faced challenges we found difficult. But we still moved on, and built knowledge and experience step by step. We also received very good support from the owner companies when we had problems. So, all in all, I slept well and rarely got frustrated.

Team-building was important in the establishment of the world’s largest test center for CO2 capture. Here from a trip on Rallarveien in August 2011.
– When you generally look back on 10 years of business at TCM, what do people that worked at TCM or still are working there have particular reason to be most proud of?
– It is that they have managed to build and develop a business that has proven to be important and relevant for the development of technology – not only in Norway, but throughout the world. The proof is that all the major technology developers have come to Mongstad to test, and take the advantage of the strong competence that the employees at TCM possess. The fact that many of these have later been given key positions in other companies also says that TCM is an important arena for development and learning. I would also like to emphasize the great value TCM has for its owners, by continuously keeping up to date on developments in technology and what is happening in the CCS industry.
– What is your wish for TCM the next ten years?
– I think TCM definitely has a role to play in the next ten years, and I sincerely hope that the owners agree. It is incredibly important that the center survives as an arena for testing new and even better technologies, and that the competent staff are used as advisors in planning the implementation of projects with full-scale CO2 capture projects.
At Statkraft, we are now planning carbon capture with the waste incineration plant at Heimdal in Trondheim, starting in 2030. The assistance we have received from TCM has been of great value and provided security for the quality of the work we now carry out in the project development process. There will be many such projects in the years to come.
Name: Olav Falk-Pedersen
Age: 59
Education: Master of Science in mechanical engineering and production from NTNU, Trondheim
Marital status: Married, three children and five grandchildren
Affiliation with TCM: Technology Manager 2010 – 2013, Business Development Manager 2013 – 2014, seconded from Gassnova
Present position: Senior project developer at Statkraft
– When you tell your friends and acquaintances about the business at TCM, what do you emphasize as the most important utility value?
– Outside the CCS «congregation», it was for a long time a little demanding to explain why TCM had its justification even if the planned «moon landing» had to canceled. But when we in Norway now see that «Longship» is realized, with CO2 capture first at Heidelberg Materials in Brevik and then hopefully also at Hafslund Oslo Celsio, it is easy to explain that it would probably not have happened without testing of technologies and knowledge gained at TCM. The business at the world’s largest test center gives sellers and buyers of technology the certainty they need that «the map matches the terrain». This also applies to the authorities when they are to prepare their decision basis.
It was this that made the job at TCM so incredibly fun and interesting, because we saw that we had planned for worked in practice. TCM gives those who want the opportunity to conduct tests with an extreme degree of accuracy.
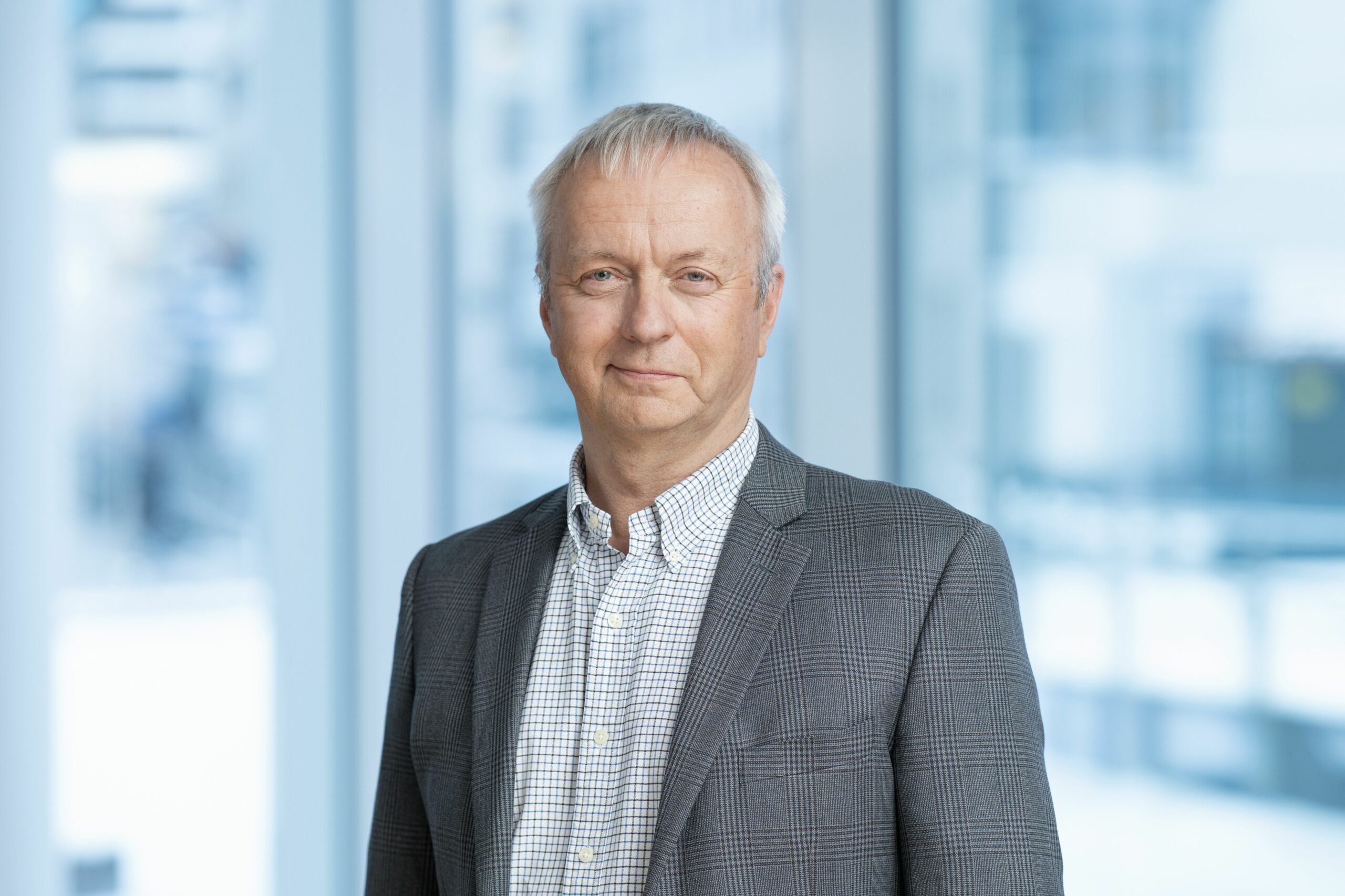
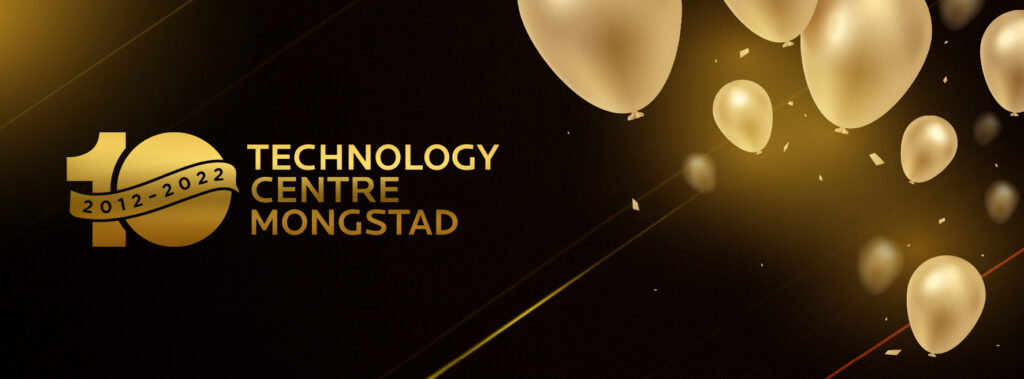
He is responsible for modifications to the facility
Kjetil Hantveit was involved in building the plant and made a come-back in 2014 in the position of Modification Manager.
Technology Centre Mongstad (TCM) has a 10-year anniversary in 2022. We celebrate ourselves with interviews with people who in various ways have had impact on the business in these years.
– Why did you apply for a position at TCM?
– I got a phone call from former project leader Sjur Brandtun to take the position as leader for modifications at TCM while I worked on a project for Equinor in the North Sea. It was tempting, and not long after I recieved a proposal for a contract. The motivation for saying yes was that I knew the skills at TCM from the construction period, and knew I got to work in teams with good people. In addition, there was also jubilation at home since this meant that I would get a job within normal working hours. Travel from the farm on Hantveit in Gulen on the north side of Fensfjorden has never been a problem. February 1, 2014, I was ready for duty.
– How was your first meeting with TCM?
– I remember it was nice to greet old acquaintances in the modification department and those who had started there after the facility was put in operation. They took me on a tour of the plant and explained what had happened in the first two years. Then we sat down and discussed the tasks we had ahead of us. It was a good day for a «half-newcomer».
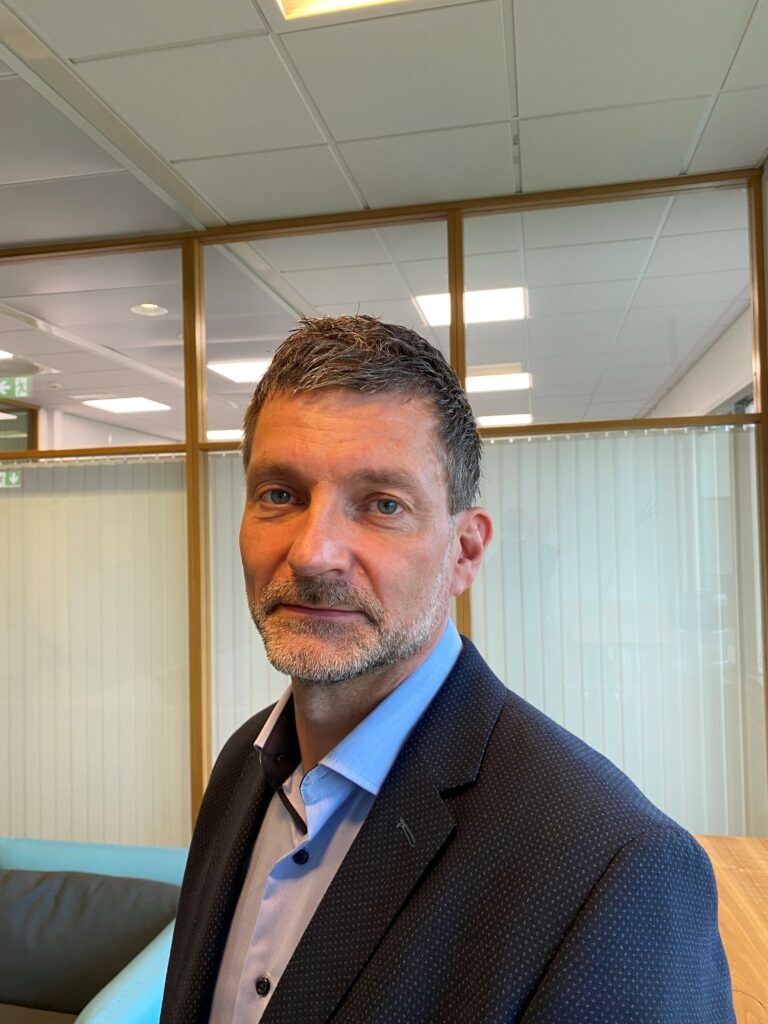
Kjetil Hantveit leads the work with modifications at TCM’s plant and is member of the leadership for the company.
– What will you highlight as the most rewarding and interesting work you took part in at TCM?
– At TCM, every activity and test campaigns live their own lives. What has made the job interesting is that we have managed to make the adjustments to the plant that are necessary for every new technology that has been tested. Thus, there will be groundbreaking work every time, and I can honestly say that no one has left here without having been allowed to do what they had planned before they arrived. Sometimes problems arise that are solved ad hoc. We manage to solve them with strong will and good effort, and excellent collaboration with the technology suppliers. That they get to test what they have to within their schedules, and are satisfied with the results, is incredibly satisfying both for me and the entire TCM team.
– Are there projects or events you remember back with special joy?
– In the first operational period, there were challenges to test with both flue gas sources from the refinery in the amine plant, ie both flue gas with about 3.5 percent and about 20 percent CO2 content. We thought that installing a new large filter allowing filtration of particles before the gases entered the process would be a good solution, but the professional bodies we sought advice from were sceptical. They thought the filter would clogged up quickly. But despite that, we chose to go for the solution we had in mind. We first did a pilot to see how it went, and it worked well. Then we were happy – and a little proud. The filter we obtained six years ago is still in use today.
– What do you think is most challenging about your work at TCM?
– For me personally, the job at TCM has been a long professional upswing. But for TCM as a company, it is a problem that the funding allocated for each operating period are limited to short periods. This makes it difficult to plan activities far in advance. It also makes it demanding to recruit new people and keep the ones we have. For TCM, it is also a challenge that the plant is no longer new but has been in operation for ten years. When operations are only guaranteed for three years in a row, it will be difficult to get approval for technical upgrades. They are needed for TCM to maintain its position as a world leader in testing CO2 capture technologies.
– When you tell your friends and acquaintances about the business at TCM, what do you emphasize as the most important utility value?
– Then I say that as long as one believes that the changes in nature and the environment are created by man, then we must use everything we have in the toolbox to stop development. Carbon capture and storage is one of these tools. The fact that we in Norway have the world’s largest test centre for technologies and cutting-edge expertise in the field is not only of great value nationally – but for the global climate challenge.
So we in our country throughout all ten years have struggled with the fact that the plan for TCM was to get full-scale purification of CO2 from the thermal power plant at Mongstad, of which there was none. Exactly that has not taken hold in the same way internationally. The ones I surround myself with know about and understand what we are doing. But I hope the marking of ten years of operation can make it better known among most Norwegians that testing at TCM is a prerequisite for safe capture of CO2.
– What is your wish for TCM the next ten years?
– Until now, TCM has been a “catch and release” facility. My wish is that in the years to come we can also take CO2 which are caught and make use of it as an input factor in various industrial productions. Here, with our expertise, we can be a driving force and catalyst to help those who have good ideas. At the same time, testing of new technologies must continue. As in the automobile industry, we work to reduce emissions and present increasingly energy-efficient solutions, and that takes time. TCM has such an absolute future ahead of it!
Name: Kjetil Hantveit
Age: 45
Education: Certificate in electrical engineering, as well as ambulance driver
Marital status: Partner, three children
Affiliation with TCM: Responsible for mechanical completion of the facility 2009 – 2011, Manager of the modification department 2014 – , member of the leader group 2020 –
Present position: Modification Manager at TCM, hired from Omega Power
– When you generally look back on 10 years of business at TCM, what do people that worked at TCM or still are working there have particular reason to be most proud of?
– I mean one should be careful about feeling successful. Success is best measured in praise from others. But that we have managed to get companies and research institutions from large parts of the world to come to Mongstad is an achievement. This is not only due to the fact that the test facilities are good, but that they are received by people who really know what they are doing and help them further along the way. One should keep in mind that even though the test campaigns are subsidized by the owners of TCM, it is not free to come here. Norway is a high-cost country, and the expenses they have to get equipment and personnel to Mongstad are not small. The fact that they are still investing resources in testing and cooperation with TCM in the US, Asia and Europe is proof that we are useful and have good offers.
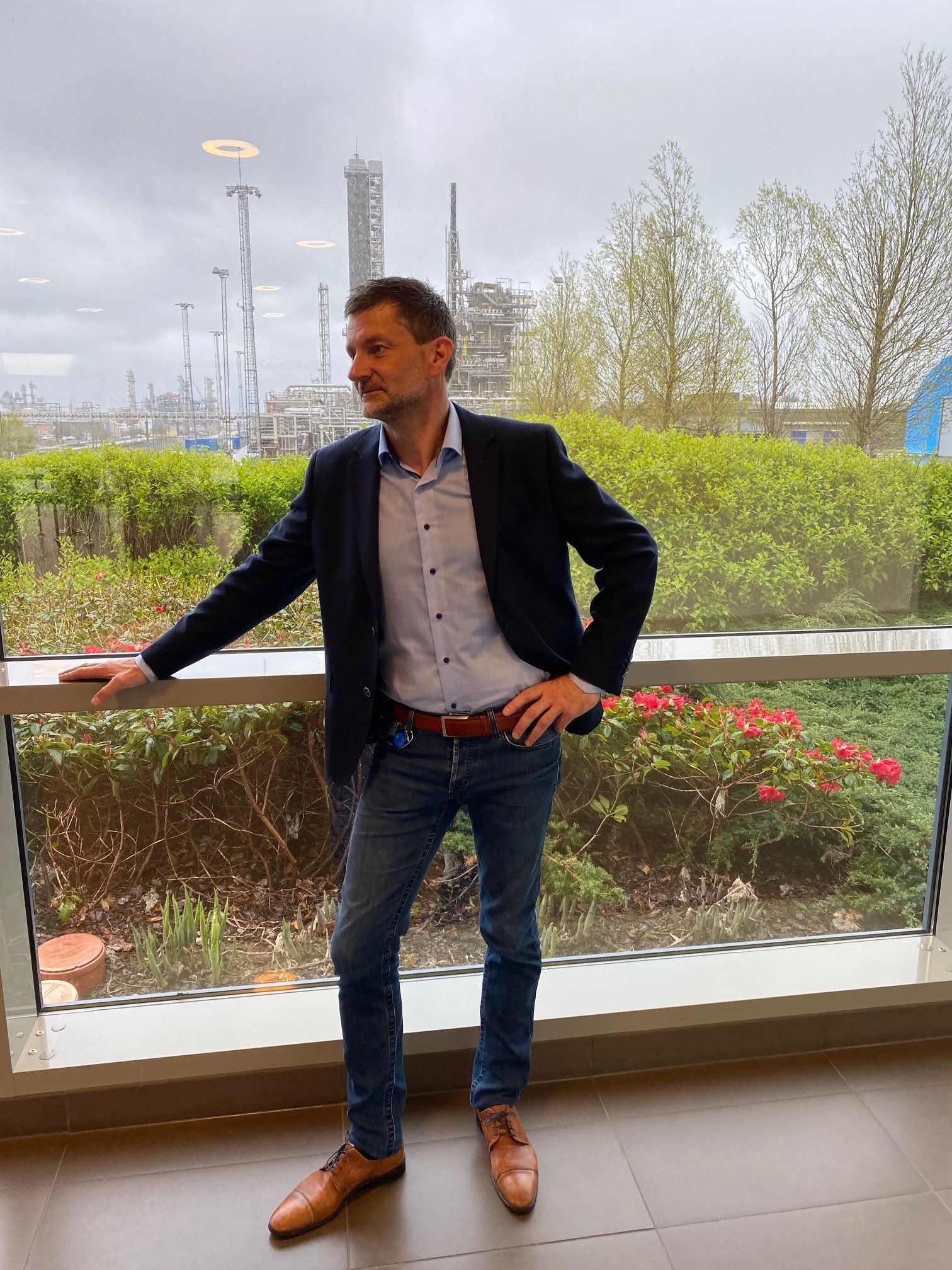
Kjetil Hantveit has busy days at TCM.
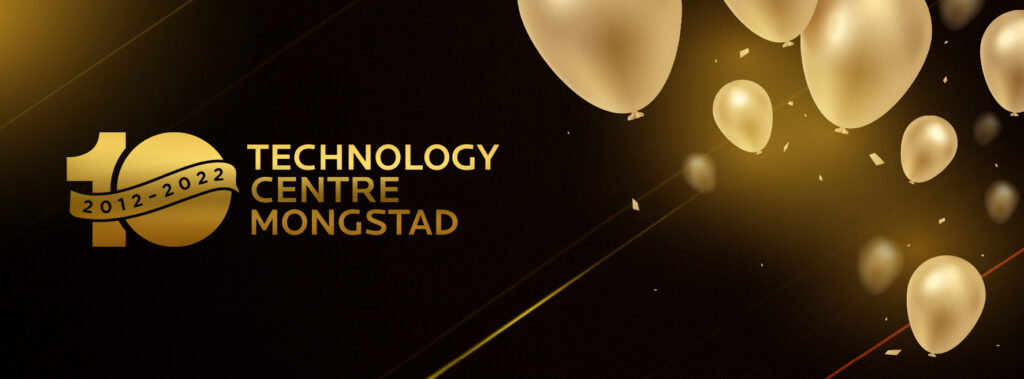