1. 18 Years of public-private partnership for developing post-combustion CO2 capture at Technology Centre Mongstad in Norway (2024)
G.M. de Koeijera*, E. Gjernesb, S. Pedersena, C. Ehrhornc, S. Jouenned, V. Pugnetd, R. Cadourse, S.I. Sembb, M.I. Shahf
aEquinor, Forusbeen 50, 4035 Stavanger, Norway
*Corresponding author. Tel.: +47 90981326, E-mail address: gdek@equinor.com
bGassnova SF, Dokkvegen 11, 3920 Porsgrunn, Norway
c A/S Norske Shell, Løkkeveien 103, 4007 Stavanger, Norway
dTotalEnergies OneTech, CSTJF EB 437, Avenue Larribau, F-64018 Pau Cedex, France
eTotalEnergies OneTech, Tour Coupole, 2 place Jean Millier, 92078 Paris La Défense Cedex, France
fTCM DA, Mongstad 71A, 5954 Mongstad
This paper has reviewed the 18 years of technology development done at Technology Centre Mongstad (TCM) from the perspective of the companies financing its activities. TCM is the world’s largest and most flexible open test center for post-combustion CO2 capture technologies. The current owners of TCM are Gassnova (representing the Norwegian State), Equinor, Shell and TotalEnergies. The ambitions for this public-private partnership were and still are:
- Develop technologies for CO2 capture capable of wide national and international deployment
- Reduce cost and technical, environmental and financial risks related to large scale CO2 capture
- Test, verify and demonstrate CO2 capture technology owned and marketed by vendors
- Encourage the development of a market for such technology
The first achievement was the design, construction and start-up. An important milestone was the world’s first emission permit that included the health risk due to nitrosamines and nitramines. Next 8 commercial technology vendors have matured their technology in the large demonstration units, increasing the competition and diversity. Moreover, many open campaigns have contributed to significant knowledge sharing. Nearly 70 scientific papers provide solid evidence on benchmarks, energy performance, emissions, degradation, corrosion, CO2 product composition and cost reduction. TCM has had cooperation with a multitude of universities and research institutes. Finally, the site for emerging technologies has increased the diversity even more by allowing a larger variety of less mature technologies to be developed. Most of the initial ambitions are fulfilled, and there are still opportunities for continuing supporting CO2 capture development at TCM.
Keywords: post-combustion; amine; Mongstad; review; ambitions; public-private partnership
Technology Centre Mongstad (TCM) is the world’s largest and most flexible open test center for post-combustion CO2 capture technologies. The idea to build such a center was initiated in 2006 in relation to a new Combined Heat and Power (CHP) plant at Equinor’s Mongstad refinery on the West coast of Norway. The investment decision was taken in 2009 and operations started in 2012. This public-private partnership will celebrate 18 years with technology development experience in 2024. The aim of this paper is to review the technology development done from the perspective of the companies financing its activities, which will be referred as owners in this paper. The current owners of TCM are Gassnova (representing the Norwegian State), Equinor (previously Statoil and StatoilHydro), Shell and TotalEnergies (previously Total). As part of their broader CCS strategies, the latter three companies are possible buyers and operators of capture technology from various vendors. The owners’ group has changed over time. Gassnova, Equinor and Shell have been owners all 18 years. In the design phase up to the investment decision DONG (now Ørsted) and Vattenfall were also partners. Sasol joined during construction and left after 5 years of operation. TotalEnergies joined in 2017.
In a paper from 2009 [1], the owners’ ambitions were published. These were and still are as follows:
- Develop technologies for CO2 capture capable of wide national and international deployment
- Reduce cost and technical, environmental and financial risks related to large scale CO2 capture
- Test, verify and demonstrate CO2 capture technology owned and marketed by vendors
- Encourage the development of a market for such technology
As can be read in this paper, most of these ambitions are fulfilled, while there are still viable options for more. TCM has contributed actively to the development of CO2 capture technologies and the market. In the following chapters, the main results will be discussed one by one, finalized by a discussion on how the owners assess the value of TCM. A general aim of TCM was to get high quality and well endorsed numbers. TCM has called upon experts with high and specialized competence. TCM uses more sensors, higher accuracy measurements and more methods than usual, including multiple reviews and independent assessments. Over time, a multitude of universities and research institutes have cooperated with TCM. The owners hope that this extra effort will ultimately contribute to increased trust in CO2 capture as a climate change mitigation technology. An important boundary condition for all the results was that an attractive cost sharing model for all contributors and stakeholders was established. Most test campaign costs are split between TCM owners and vendors. Some campaigns have also been partly funded by Norwegian and European R&D programs. The US Department of Energy has supported various campaigns through a US-Norway Memorandum of Understanding. There has been development towards larger contribution from technology vendors. To illustrate the size and ambition of TCM, its annual operating costs are in 2023 around 200 million NOK [2]. And below in Figure 1 a photograph and a 3D rendering of TCM is shown to illustrate the size and complexity.
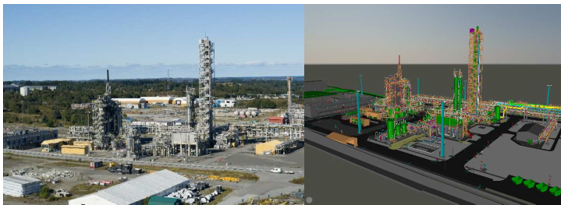
Fig. 1. Picture (source: TCM DA) and 3D model image of TCM.
The design of TCM consists of an amine unit, a chilled ammonia process (CAP) unit, utilities, and a site for emerging technologies (SET). The flue gas is delivered by pipes on a piperack from a Combined Heat and Power plant (CHP, up to 3.6 vol% CO2 and 60 000 Sm3/h) and a Residue Fluidized Catalytic Cracker (RFCC, up to 13 vol% CO2 and 50 000 Sm3/h with SOx, NOx and particulates). All elements were successfully designed, constructed, and put into operation in the period 2009-2014. The first start-up was in August 2012. More detailed description of the results and design can be found later in this paper. A list of public papers and reports can be found at the TCM website [3]. Due to all these features, TCM was and still is the world’s largest and most flexible test site for post-combustion CO2 capture. An important inspiration for TCM’s amine unit was the Esbjerg pilot in Denmark used for the CASTOR and CESAR projects [4]. TCM’s aim was to provide a meaningful scale-up and increase in flexibility relative to the Esbjerg pilot.
The amine unit was designed by SLB Capturi (formerly Aker Carbon Capture, and previously Aker Clean Carbon at the time of design and construction) and built by Aker Solutions. The design of the system was based on the use of monoethanolamine (MEA) as the primary solvent, with the flexibility to accommodate alternative solvents. Due to the varying CO2 concentrations, the flow rates of CO2 entering the absorber differ significantly, necessitating adjustments to the solvent circulation rate. To address this, two strippers were designed and constructed. The smaller stripper has a capture capacity of up to 3.5 tonnes CO2/h, primarily handling emissions from the combined heat and power (CHP) unit, while the larger stripper, with a capacity of 8.5 tonnes CO2/h, is mainly used for the residue fluid catalytic cracking (RFCC) unit. The absorber, a 67-meter-tall lined rectangular concrete structure, is designed for high operational flexibility, allowing lean amine to be introduced at three different heights. Additionally, the system features two water wash sections, with the upper section adaptable to serve as an acid wash when required.
Initial tests conducted on CHP exhaust in 2012 yielded results as anticipated, with further details provided later in this paper. However, upon switching to RFCC exhaust, an unacceptable increase in amine emissions to the atmosphere was observed. This was attributed to a combination of sulfuric acid aerosols and catalyst particles present in the
exhaust stream. Following extensive studies, it was decided to invest in a flexible Brownian Demister Unit (BDU) to mitigate the issue. The BDU reduces the number of aerosols and particles carried over with the flue gas to the absorber, effectively lowering amine emissions to acceptable levels. A partial bypass of the BDU allows for controlled particle content at the absorber inlet, facilitating detailed studies of this phenomenon.
Additional investments over the years have included an increase in water wash cooling capacity, enhanced flexibility of the water wash system, and instrumentation upgrades, such as the installation of a new Fourier-transform infrared spectroscopy (FTIR) and ion-molecule-reaction mass spectrometry (IMR-MS) equipment. An absorber intercooler was also added to improve performance. The most recent modification involved transitioning from turbine- fired flue gas sourced from a CHP to heater-fired flue gas from the Mongstad Heat Plant (MHP), both of which operate on natural gas. This shift resulted in a slight change in gas composition, with a higher CO2 concentration. However, through air dilution, the resulting flue gas remains comparable to that produced by gas-fired power plants.
The CAP unit was designed and built by Alstom. The intent of the unit was to mature this one specific post- combustion capture technology. The unit was successfully started up in 2014. The main results were published by Lombardo et al [5]. Currently the chilled ammonia technology is offered by Baker Hughes [6].
3. World’s first emission permit of an amine-based CO2 capture plant on exhaust with important health risk
During the design phase of TCM, increasing evidence emerged indicating that amine-based CO2 capture plants may pose a health risk due to the formation of nitrosamines and nitramines. These compounds, which are potentially carcinogenic, are formed through reactions between amines and NOx, both within the capture process and in the atmosphere. Human exposure can occur via inhalation or through contaminated drinking water, posing a risk to both the local population and plant workers, particularly during manual operations such as sampling and reclaiming. It was necessary to mitigate this risk, not only for the safe operation of TCM but also to set a precedent for risk management across the broader CCS industry. During the process up to the emission permit application, TCM conducted and contributed to:
- experiments on reaction kinetics of some relevant amines with NOx in the process and in atmosphere,
- detailed measurements of the composition of cleaned exhausts from other pilots,
- dispersion simulations with atmospheric reactions and sinks,
- studies on possible threshold values for nitrosamine and nitramine exposure in air and water,
- environmental baseline studies, and
- a worst case set of evidence-based assumptions enabling the use of the precautionary principle
The result was that the world’s first emission permit for an amine based post-combustion plant that included the above health risk was applied for and approved in 2012. The contribution of the Norwegian and international research community was essential. The important results are openly published [7, 8, 9]. This effort seems now to be a reference for many full-scale capture projects under development worldwide. The documented experience from TCM and other projects provides good evidence that this health risk can be mitigated.
Seven technology vendors have tested since 2012 their amine solvents in one or multiple campaigns in the generic amine plant. This represents a large variety in solvent properties and process design. All vendors gained in maturity because of their campaign at TCM. The Table below gives an overview based on publicly available information.
Table 1. Technology vendor campaigns at TCM
Technology vendor | Campaign years | Solvent names based on public information with references |
SLB Capturi | 2013-2014 | MEA, S21, S26 [10] |
Shell Cansolv | 2023, 2016, 2014-2015 | Upgraded solvent, DC201, DC-103 [11, 12, 13] |
Carbon Clean(1) | 2015-2016 | CDRMAx [14] |
ION Clean Energy (2) | 2023, 2016-2017 | ICE-31, ICE-21 [15] |
Fluor (2) | 2019 | New solvent [16] |
MHIENG | 2021 | KS-21 [17] |
RTI International(2) | 2022 | eCO2Sol [18] |
- Supported by former Department for Business, Energy & Industrial Strategy (UK), previously named CCSL
- Supported by the U.S. Department of Energy National Energy Technology Laboratory (DOE-NETL)
TCM has offered roughly the same unit, design and operational competence to all vendors. The unit was not always the exact same due to gradual upgrades, of which the intercooler in 2022 was the main functional one. Each vendor has made its own choices on what tests to prioritize. Any comparison of vendors based TCM’s results is not the purpose. The aim of TCM is to help each vendor as good as possible to mature its technology. It is the intention that the market through competition for construction projects will pick winners.
SBL Capturi initially designed TCM’s amine plant and included operation of the plant in the technical qualification program for the CO2 Capture Mongstad (CCM) in Norway [10]. The CCM project was cancelled in 2013. TCM was intended as an open access test center. Table 1 shows that Shell Cansolv was the first in the line of technology vendors to test their solvent at the amine plant. And by 2023 twelve vendor campaigns have been operated. So, the intention of being open to many vendors has been fulfilled.
The various test campaigns have typically utilized CO2 concentrations in the range of about 4 to 13%. The campaigns have investigated capture rate, energy demand, solvent-performance, emissions to air and corrosion and have also provided data relevant for process simulators and for establishing solvent baselines. Deep CO2 removal with capture rates above 99% has been demonstrated. The range of solvents that have been investigated includes also water lean solvents. Several of the vendors in Table 1 have also included campaigns at National Carbon Capture Center (NCCC, US) and/or SINTEF’s pilot and labs in Norway in their technology development programs, see RTI International’s efforts as an example [19]. All campaigns have been operated under TCM’s environmental permit. This provided valuable insight in the methodology that includes evaluating the solvents’ site-specific environmental performance ahead of testing as well as emission monitoring and reporting during the campaign.
During the last 10 years there has been a limited number of new CO2 capture plants been built. All seven vendors have, however, been selected for FEED (Front-End Engineering Design) studies for CO2 capture plants. Several of these vendors are also supplying capture technology to plants that have been built or have been selected for upcoming investment decisions.
The latest development is that an advanced solvent developed through a partnership involving the University of Texas at Austin (UT Austin) and Honeywell is set for engineering-scale testing in October 2024 in TCM’s amine unit [20]
In between technology vendor campaigns the owners executed so-called open campaigns, of which the content was largely determined by the owners. They are called open since most of the important results are published openly. The main objective and the opportunity for the owners in the open test campaigns was to produce knowledge and information that can be used in the open domain to reduce the cost, technical, environmental and financial risks of commercial scale deployment. The non-proprietary aqueous solvents Monoethanolamine (MEA, 30-40 wt%) and CESAR1 (blend of 2-amino-2-methyl-1-propanol (~3M) and piperazine (~1.5M)) were used. Collaboration with
industry and academia gave extra value to these campaigns. Projects supported by the EU, DOE and CLIMIT were significant parts of the work, while the owners still financed the largest share. It is worth noting that several projects aimed to understand the effects and options for acid aerosol and particulate control. Operating the plant over a very wide range of conditions with parametric testing gave unique insights on how operation impact the solvent quality, the degradation behavior, the corrosion tendency and the emissions to atmosphere. Important aspects and results from the owner’s campaigns are:
– Baselines established for MEA and CESAR1
– Experiences with solvent management and environmental impacts during long term operation of the plant
– Assessment of cost reduction potentials
– Sampling and analysis to provide high quality emission measurements
TCM contracted the Electric Power Research Institute (EPRI) to develop an independent verification protocol that was applied to produce the baselines [21, 22, 23, 24, 25]. Third-party measurements of flow and composition of the relevant streams for producing the heat and mass balances were performed by FORCE Technology [22]. This contributed to credibility in the assessments. High accuracy and precision in instruments and calculations of performance parameters were achieved. The published baselines have proven useful for both the academic and industrial environment. The four baselines are:
– MEA (30 wt%), CHP flue gas (4 vol% CO2, relatively clean flue gas)
– MEA (30 wt%), RFCC flue gas (13 vol% CO2, dirty flue gas with acid aerosols and catalyst particles)
– CESAR1, CHP flue gas (4 vol% CO2, relatively clean flue gas)
– CESAR1, RFCC flue gas (13 vol% CO2, dirty flue gas with acid aerosols and catalyst particles)
A long-term operation with MEA was executed in the period from June 2017 to July 2018 [25, 27, 28]. The operation was divided into several different test periods designed to meet the objectives of various research projects. Solvent management was a key objective for the overall campaign that included several reclaiming tests and feed and bleed events. This work identified key indicators and proposed corresponding threshold limits that should be adhered to for keeping the solvent and plant performance stable. An example of a valuable heuristic found in this campaign is to keep Fe-ion <5 mg/l for keeping the solvent functional. Thermal reclaiming was used. Reclaimer waste, ammonia and amine emissions to atmosphere were found to be the most important parameters for assessing the environmental impacts. Moreover, a benchmark for compact capture was also studied [29], but not as detailed as the main four baselines.
Data from the MEA test campaigns were used to evaluate potential cost reductions [30, 31, 32]. Experimentally verified improvements and other lessons learned from TCM operations were combined to estimate an overall cost saving potential in the range of 20 to 30 % points from the start of TCM and until the latest MEA test campaign. The metrics “cost of electricity” and “cost of CO2 avoided” were used in an internal standardized cost evaluation method. This exercise was carried out to help owners become better informed buyers of technology.
Imperial College London investigated dynamic operation modes and developed a start-up and shut-down protocol for power stations with CO2 capture. The effects of solvent inventory volumes, steam availability, solvent loading and temperature at start-up were among the studied parameters. This valuable work was also published in an IEAGHG report [33].
To develop state of the art emission sampling and analysis methods has always been a priority at TCM [34, 35, 36, 37, 38, 39]. Both manual sampling and on-line instruments are used. TCM has published emission data extensively from both MEA and CESAR1 campaigns. The collaboration with the University of Oslo has been important. Testing and development of sampling lines, sampling probes, sampling artefacts and instruments with low detection limits have been part of the activities.
A summary of the open campaigns is given in Table 2. The MEA campaigns have been executed in several time periods and are designated MEA1, MEA2, MEA3, MEA4 and MEA5 to distinguish between the different tasks and projects that have been carried out. Similarly, the CESAR1 campaigns are designated CESAR1-part 1 and CESAR1- part 2.
Table 2. Summary of open campaigns.
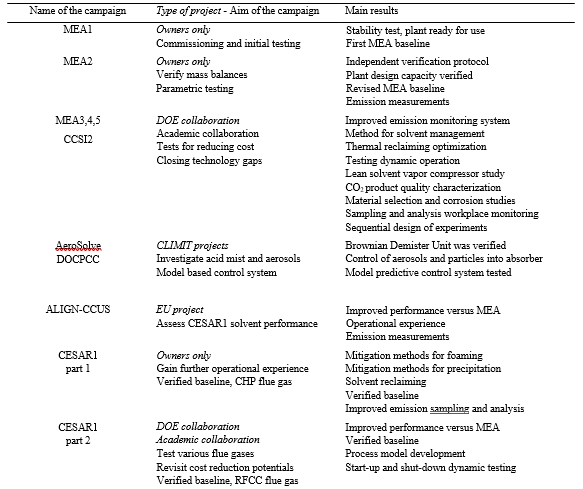
By being as open as possible TCM has provided the CCS community many high-quality results that are reviewed multiple times. Many issues that used to be the sole domain of a few commercial vendors were published and provided benchmarks. The open campaigns also spurred new research, both at TCM and at other pilot and laboratories. The open campaign concept is planned to be continued. TCM’s next CESAR1 campaign may be part of the Horizon Europe Innovation Action funded project AURORA. Target applications are the refining, cement and materials recycling industries. This project is managed by SINTEF and will seek to optimize and qualify the solvent for commercial deployment [40].
The so-called site for emerging technologies (SET), where smaller post-combustion pilots can be tested was started in 2021. TCM’s owners pre-invested in access to both flue gasses, all utilities except steam, connection to the vent stack, paving and civil connection. This site allows testing next generation, less mature technologies such as membranes, adsorption or new solvents, while benefiting from the expertise of TCM on operations, maintenance, emissions etc. The site for emerging technologies enables to feed pilots with the two flue gas sources from the CHP (now MHP) and RFCC. It has so far attracted five test campaigns, all of them being part of DOE or EU funded projects. MTR and TDA completed the first two campaigns from June 2021 to March 2022. They demonstrated the scale- up the design and the performances of their technology. In 2023, SAIPEM and PROSPIN compared conventional absorber with rotating packed bed with an enzymatic accelerated carbonate solvent. Adsorbent based technologies developed through MOF4Air project and by Innosepra were also tested.
From these first test campaigns, vendors demonstrated the performances of their technologies in containerized design on real flue gas at scales ranging from 1 to 20 tCO2/day, with a focus on the CO2 capture rate, the CO2 product composition and long-term testing. These results are then generally used to update techno-economic assessments (TEA) and increase the maturity of the technology. For most of them, the change in scale provided them opportunities for improving the performance and reliability of their technology. In that sense, the SET can also be viewed, as a good training site to learn how to operate the units better, but also consider more robust design and select better pieces of equipment for the technology in its next upscaling phase. The Table below gives an overview.
Table 3. Campaigns at site for emerging technologies.
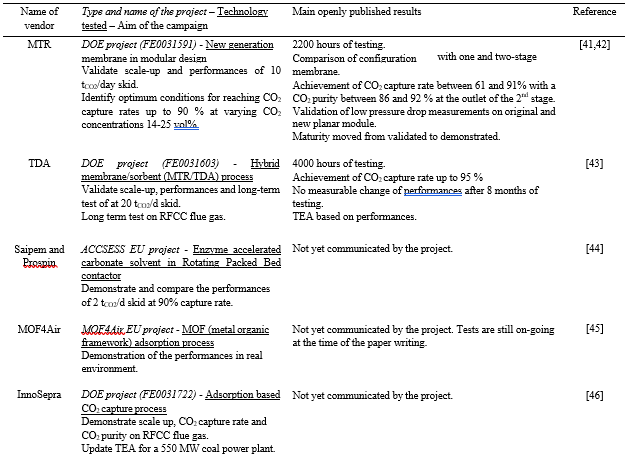
In conclusion, TCM’s SET provides a unique testing ground for less mature technologies where vendors can benefit from the expertise of TCM technical competence, which is very much derived from the operation of the amine plant. The plans for the future include a campaign by Svante to further validate its technology [47].
Knowledge sharing where possible has been an overarching aim of TCM. For this purpose, TCM has conducted the previously discussed open scientific campaigns, with non-proprietary solvents (MEA and CESAR-1) since 2013. These campaigns were conducted to address typical technical pitfalls observed in CCS projects. Since 2020, the results and experience from over 20,000 hours of non-proprietary solvent testing at TCM has been used to develop TCM’s Advisory Services as an additional tool for knowledge sharing.
TCM’s Advisory Services are facilitating the “translation” of the afore mentioned knowledge from the TCM scale to the industrial projects. Reports summarizing key learnings, tailor-made advisory projects and workshops are some of the ways that are serving as the vehicle that transfers knowledge. But the most convincing contribution to knowledge sharing are the nearly 70 scientific papers that have been published by TCM, research partners, technology vendors, and TCM owners [3], covering all aspects of the original ambitions. Not only the owners themselves have used them actively, but also the many in the CCS community.
The above discussed achievements are the visible and documented results. But TCM’s owners are value oriented and see several other benefits. The 13 vendors who have been at TCM have created a diversity and competition in the market. Today, TCM’s owners and the CCS industry as a whole have a broader choice of vendors for their specific capture projects. All TCM’s vendors are active in the CO2 capture business, which includes R&D, engineering studies, licensing and construction. Next, the owners have first-hand access to high quality and reliable results, enabling them to evaluate technologies and projects. These results have shown to be a good basis for writing project specifications, procurement documents and negotiating guarantees on OPEX/CAPEX. In this context, the ownership of intellectual property remains with the vendor. Confidentiality is regulated through test agreements with each vendor. For owners who license their own CO2 capture technologies or have any other close relationship to a vendor ringfencing of intellectual property has been used as a tool to mitigate contamination. Finally, the industrial owners of TCM also pursue CO2 transport and storage projects. TCM’s contribution to the post-combustion field will benefit forthcoming projects within e.g. steel, cement and waste to energy sectors. And this may eventually result in increased volumes in the CO2 transport and storage market. For this aspect TCM’s learnings on CO2 product specifications has also been useful. TCM has shown to be very important in the Norwegian CCS project “Longship”, which is under construction. Both capture plants within this project, Heidelberg Materials cement factory in Brevik and Hafslund Oslo Celsio waste-to-energy plant at Klemetsrud have chosen independently vendors that have tested their technology at TCM. Moreover, the construction projects benefited from regular experience transfer.
TCM has done and will continue to do campaigns to investigate and derisk most aspects of post-combustion capture related to energy demand, performances, solvent management, emissions, CO2 product purity and operational issues. Several new challenges have emerged, and new challenges will likely surface as the technologies are being deployed, to which TCM can contribute. Today, new post-combustion technologies like non-amine liquids, adsorbents, membranes, liquefaction, anti-sublimation are promising, but not proven. TCM is well equipped to test novel technologies other than conventional amines with the site for emerging technologies. Secondly, dispatchable and load following operation of power plants (covering the gaps that wind and solar leave behind) have become a more and more attractive business case. All in all, we can conclude that TCM has met its initial ambitions and is still delivering at the service of the whole CCS industry. From now, TCM is evolving in its business model. And there is a clear expectation that technology vendors and business projects take over gradually more of the financing, along with the commercial maturation of CCS.
This paper has reviewed the technology development done at Technology Centre Mongstad (TCM) from the perspective of the financing companies. Most of the initial ambitions are fulfilled since TCM has shown to have contributed actively to the development of CO2 capture technologies and market. First of all, the world’s largest test site for post-combustion CO2 capture technology was designed, built and started up. Next eight commercial technology vendors (seven amine based and one chilled ammonia based) have matured their technology in the large demonstration units, increasing the competition and diversity. Moreover, many open campaigns and derived advisory services have contributed to significant knowledge sharing. The nearly 70 scientific papers are the prime evidence. Finally, the site for emerging technologies has increased the diversity even more by allowing a larger variety and less mature technologies to be developed. Building on the already very useful results, there are still opportunities for continuing supporting CO2 capture deployment at TCM today. In conclusion, TCM is a successful public-private partnership on the development of a climate change mitigation technology.
TCM is currently financed by Gassnova (on behalf of Norwegian State), Equinor, Shell, TotalEnergies, technology vendors, research partners, EU, US DoE and Norwegian research programs.
1 De Koeijer G, Enge YO, Thebault C, Berg S, Lindland J, Overå SJ. European CO2 test centre Mongstad–Testing, verification and demonstration of post-combustion technologies. Energy Procedia 2009;1:1321-6. https://doi.org/10.1016/j.egypro.2009.01.173
2 TCM DA website on Transparency Act. https://tcmda.com/about-tcm#transparency_act- (accesssed September 2024)
3 TCM DA website with overview of publications. https://tcmda.com/publications/ (accessed September 2024)
4 Knudsen JN, Jensen JN, Vilhelmsen P, Biede O. First year operation experience with a 1 t/h CO2 absorption pilot plant at Esbjerg coal-fired power plant. Proceedings of European Congress of Chemical Engineering (ECCE-6) Copenhagen 2007
5 Lombardo G, Agarwal R, Askander J. Chilled Ammonia Process at Technology Center Mongstad – First Result, Energy Procedia. 2014;51: 31–9. https://doi.org/10.1016/j.egypro.2014.07.004
6 Baker Hughes website on Chilled Ammonia. https://www.bakerhughes.com/process-solutions/chilled-ammonia-process (accesssed September 2024)
7 De Koeijer G, Talstad VR, Nepstad S, Tønnessen D, Falk-Pedersen O, Mareee Y, Nielsen C. Health risk analysis for emissions to air from CO2 Technology Centre Mongstad. International Journal of Greenhouse Gas Control 2013;18:200-7. https://doi.org/10.1016/j.ijggc.2013.07.010
8 Gassnova website on HSE studies for health and environmental challenges. https://ccsnorway.com/hse-studies/ (accessed September 2024)
9 TCM DA website. https://tcmda.com/studies-with-focus-on-amine-components (accessed September 2024)
10 Gorset O, Knudsen JN, Bade OM, Askestad I. Results from testing of Aker Solutions advanced amine solvents at CO2 Technology Centre Mongstad, Energy Procedia 2014;63:6267–80. https://doi.org/10.1016/j.egypro.2014.11.658
11 Shell website, Shell to test carbon capture technology at Technology Centre Mongstad in Norway. https://www.shell.com/business- customers/catalysts-technologies/resources-library/trade-release-shell-to-test-carbon-capture-technology-at-techno.html (accessed September 2024)
12 IEA GHG website. Campbell M. Cansolv DC-201 Testing at TCM: Impact of degradation inhibitor on degradation rate and emissions. https://az659834.vo.msecnd.net/eventsairwesteuprod/production-ieaghg-public/1cbc121c4e694be5a2c922dfe1311cc0 (accessed September 2024)
13 Shell website. Behind Shell Technologies: CANSOLV CO2 Capture with Dr. Paul-Emmanuel Just and Karl Stephenne. https://www.shell.com/business-customers/catalysts-technologies/resources-library/behind-shell-technologies-cansolv-co2-capture-with- paul-emmanuel-just-and-karl-stephenne.html (accessed September 2024)
14 Bumb P, Patkar A, Mather R, Kumar R, Hall J, Morton F, Anthony J. Field Demonstration of Advanced CDRMax Solvent at the US-DOE’s National Carbon Capture Centre and the CO2 Technology Centre Mongstad DA, Norway, Energy Procedia 2017;114:1087-99. https://doi.org/10.1016/j.egypro.2017.03.1261
15 TCM DA website on ION. “TCM Is Unrivaled!”, https://tcmda.com/news/ion-tcm-is-unrivaled (accessed September 2024)
16 NETL DOE website on Fluor Solvent Testing at Technology Center Mongstad (Project 70814). https://netl.doe.gov/sites/default/files/netl- file/S-Readdy-PNNL-Solvent-Testing-at-TCM.pdf (accessed September 2024)
17 MHI website. Mitsubishi Heavy Industries Engineering Successfully Completes Testing of New “KS-21TM” Solvent for CO2 Capture. https://www.mhi.com/news/211019.html (accessed September 2024)
18 TCM DA website. RTI is testing at TCM: So far, so good! https://tcmda.com/news/rti-is-testing-at-tcm-so-far-so-good (accessed September 2024)
19 NETL DOE website. Project landing page. Engineering Scale Testing of Transformational Non-Aqueous Solvent-Based Carbon Dioxide Capture Process at Technology Centre Mongstad. https://netl.doe.gov/project-information?p=FE0031590 (accessed September 2024)
20 NETL DOE website. “Carbon Capture Solvent Technology To Be Tested at World’s Largest Test Facility”. https://netl.doe.gov/node/14238 (accessed October 2024)
21 Hamborg ES, Smith V, Cents T, Brigman N, Falk-Pedersen O, De Cazanove T, Chhaganlal M, Feste JK, Ullestad Ø, Ulvatn H, Gorset O, Askestad I, Gram LK, Fostås BF, Shah MI, Maxson A, Thimsen D. Results from MEA testing at the CO2 Technology Centre Mongstad. Part II: Verification of baseline results. Energy Procedia 2014;63:5994-6011. https://doi.org/10.1016/j.egypro.2014.11.634
22 Faramarzi L, Thimsen D, Hume S, Maxson A, Watson G, Pedersen S, Gjernes E, Fostås BF, Lombardo G, Cents T, Morken AK, Shah MI, de Cazenove T, Hamborg ES. Results from MEA testing at the CO2 Technology Centre Mongstad: Verification of baseline results in 2015, Energy Procedia. 2017;114:1128-45. https://doi.org/10.1016/j.egypro.2017.03.1271
23 Hume S, Shah MI, Lombardo G, de Cazenove T, Feste JK, Maxson A, Benquet C. Results from MEA Testing at the CO2 Technology Centre Mongstad. Verification of Residual Fluid Catalytic Cracker (RFCC) Baseline Results. Proceedings of the 15th Greenhouse Gas Control Technologies Conference 2021. http://dx.doi.org/10.2139/ssrn.3821037
24 Hume, SA, Shah MI, Lombardo G, Kleppe ER. Results from Cesar-1 Testing with Combined Heat and Power (CHP) Flue Gas at the CO2 Technology Centre Mongstad. 2021 Presented at Trondheim Conference on CO2 Capture, Transport and Storage https://hdl.handle.net/11250/2786512
25 Hume SA, McMaster B, Drageset A, Shah MI, Kleppe ER, Campbell M. Results from CESAR1 testing at the CO2 Technology Centre Mongstad. Verification of Residue Fluid Catalytic Cracker (RFCC) baseline results. 2022 Presented at the 16th Greenhouse Gas Control Technologies Conference, Lyon, France. http://dx.doi.org/10.2139/ssrn.4280571
26 Morken AK, Pedersen S, Nesse SO, Flø NE, Johnsen K, Feste JK, de Cazenove T, Faramarzi L, Vernstad K. CO2 capture with monoethanolamine: Solvent management and environmental impacts during long term operation at the Technology Centre Mongstad (TCM). International Journal of Greenhouse Gas Control, 2019;82:175-83. https://doi.org/10.1016/j.ijggc.2018.12.018
27 Gardarsdottir S, Faramarzi L, Jordal K, Campbell M. Critical Knowledge for CO2-Intensive Industries to Implement Amine-Based Carbon Capture. Proceedings of the 15th Greenhouse Gas Control Technologies Conference 2021. http://dx.doi.org/10.2139/ssrn.3813495
28 Johnsen K, Romslo KE, Faramarzi L, Benquet C, Gjernes E, De Koeijer G, de Cazenove T, Morken AK, Flø NE, Shah MI, Aronsson M, Ullestad Ø. CO2 Product Quality: Assessment of the Range and Level of Impurities in the CO2 product Stream from MEA Testing at Technology Centre Mongstad (TCM). 14th Greenhouse Gas Control Technologies Conference Melbourne 2018, https://ssrn.com/abstract=3365995
29 De Koeijer G, Benquet C, Knarvik ABN, Gjernes E, Pedersen S, Hvidsten OA, A Benchmark for Compact CO2 Capture Plant Designs by Monoethanolamine Solvent Testing at Technology Centre Mongstad, Proceedings of the 15th Greenhouse Gas Control Technologies Conference 2021. https://papers.ssrn.com/sol3/papers.cfm?abstract_id=3813201
30 Gjernes E, Pedersen S, Jain D, Åsen KI, Hvidsten OA, de Koeijer G, Faramarzi L, de Cazenove T. Documenting Modes of Operation with Cost Saving Potential at the Technology Centre Mongstad. 14th Greenhouse Gas Control Technologies Conference Melbourne 2018. https://ssrn.com/abstract=3366235
31 Shah MI, Silva E, Gjernes E, Åsen KI. Cost Reduction Study for MEA based CCGT Post-Combustion CO2 Capture at Technology Center Mongstad. Proceedings of the 15th Greenhouse Gas Control Technologies Conference 2021. http://dx.doi.org/10.2139/ssrn.3821061
32 Putta KR, Saldana D, Campbell M, Shah MI. Development of CO2 capture process cost baseline for 555 MWe NGCC power plant using standard MEA solution. Presented at the 16th Greenhouse Gas Control Technologies Conference 2022. http://dx.doi.org/10.2139/ssrn.4279671
33 Bui M, Mac Dowell N. Start-up and Shutdown Protocol for Natural Gas-fired Power Stations with CO2 Capture. 2022 IEAGHG Report IEA/CON/20/272. https://ieaghg.org/publications/start-up-and-shutdown-protocol-for-natural-gas-fired-power-stations-with-co2-capture/
34 Zhu L, Schade GW, Nielsen CJ. Real-Time Monitoring of Emissions from Monoethanolamine-Based Industrial Scale Carbon Capture Facilities, Environ. Sci. Technol. 2013;47:14306−14. https://doi.org/10.1021/es4035045
35 Morken AK, Nenseter B, Pedersen S, Chhaganlal M, Feste JK, Tyborgnes RB, Ullestad Ø, Ulvatn H, Zhu L, Mikoviny T, Wisthaler A, Cents T, Bade OM, Knudsen J, de Koeijer G, Falk-Pedersen O, Hamborg ES. Emission results of amine plant operations from MEA testing at the CO2 Technology Centre Mongstad, Energy Procedia 2014;63:6023–38. https://doi.org/10.1016/j.egypro.2014.11.636
36 Morken AK, Pedersen S, Kleppe ER, Wisthaler A, Vernstad K, Ullestad Ø, Flø NE, Faramarzi L, Hamborg ES. Degradation and Emission Results of Amine Plant Operations from MEA Testing at the CO2 Technology Centre Mongstad. Energy Procedia 2017;114:1245-62. https://doi.org/10.1016/j.egypro.2017.03.1379
37 Zhu L, Mikoviny T, Morken AK, Tan W, Wisthaler A. A compact and easy-to-use mass spectrometer for online monitoring of amines in the flue gas of a post-combustion carbon capture plant. International Journal of Greenhouse Gas Control 2018;78:349-53, https://doi.org/10.1016/j.ijggc.2018.09.003
38 Languille B, Drageset A, Mikoviny T, Zardin E, Benquet C, Ullestad Ø, Aronson M, Kleppe ER, Wisthaler A. Best practices for the measurement of 2-amino-2-methyl-1-propanol, piperazine and their degradation products in amine plant emissions. Proceedings of the 15th Greenhouse Gas Control Technologies Conference 2021. http://dx.doi.org/10.2139/ssrn.3812339
39 Drageset A, Ullestad Ø, Kleppe ER, McMaster B, Aronsson M, Olsen JA. Real-time monitoring of 2-amino-2-methylpropan-1-ol and piperazine emissions to air from TCM post combustion CO2 capture plant during treatment of RFCC flue gas. Presented at the 16th Greenhouse Gas Control Technologies Conference 2022. http://dx.doi.org/10.2139/ssrn.4276745
40 Aurora website, https://aurora-heu.eu/wp-content/uploads/2024/04/GHGT-17-CESAR1-degradation.pd (Accessed September 2024)
41 Batoon, V, Borsaly, A, Casillas, C, Hofmann, T, Huang, I, Kniep, J, Westling, E. Scale-Up Testing of Advanced Polaris™ Membrane CO2 Capture Technology. Proceedings of the 16th Greenhouse Gas Control Technologies Conference 2022. https://papers.ssrn.com/sol3/papers.cfm?abstract_id=4281208
42 Merkel, T, Salim, W, Casillas, C, Borsaly, A, Kniep, J, Westling, E, Sun, Z . Scale-up Testing of Advanced Polaris Membrane in CO2 Capture Technology. 2023 Technical report No. 383 U.S. Department of Energy Office of Scientific and Technical Information. https://www.osti.gov/biblio/1995006
43 Gribble, D, Hohman, J, Jayaraman, A, Hofmann, T, Kniep, J, Merkel, T, Alptekin, G. Demo-scale testing of a hybrid membrane-sorbent system for post-combustion CO2 capture. Proceedings of the 16th Greenhouse Gas Control Technologies Conference 2022. https://papers.ssrn.com/sol3/papers.cfm?abstract_id=4295185
44 M Montañés, R, Jordal, K, Schiesari, F, Anantharaman, R, Brunsvold, A, Mazzotti, M, Frieling, H. ACCSESS Project: Providing access to cost-efficient, replicable, safe and flexible CCUS. Proceedings of the 16th Greenhouse Gas Control Technologies Conference 2022. https://papers.ssrn.com/sol3/papers.cfm?abstract_id=4282876
45 Heymans, N, Duprez, ME, De Weireld, G. MOF4AIR project (H2020): Metal Organic Frameworks for carbon dioxide Adsorption processes in power production and energy Intensive industries. Proceedings of the 15th Greenhouse Gas Control Technologies Conference 2021. https://papers.ssrn.com/sol3/papers.cfm?abstract_id=3821559
46 Jais, R, Lemcoff, N. Transformational sorbent-based process for a substantial reduction in the cost of CO2 capture. Presentation at National Energy Technology Laboratory Carbon Management Project Review Meeting 2023. https://netl.doe.gov/sites/default/files/netl- file/23CM_PSCC30_Jain.pdf
47 TCM DA website. Svante to Test Groundbreaking Carbon Capture Filter Technology at TCM. https://tcmda.com/news/svante-to-test- groundbreaking-carbon-capture-filter-technology-at-tcm (accesse