10. Results of the fourth Technology Centre Mongstad campaign: LVC testing (2019)
Philip Loldrup Fosbøla,⁎, Randi Neerupa, Susana Almeidaa, Amirali Rezazadeha, Jozsef Gaspara, Anette Beate Nesse Knarvikb, Nina Enaasen Fløb
aCenter for Energy Resources Engineering (CERE), Department of Chemical Engineering, Technical University of Denmark (DTU), Søltofts Plads, Building 229, DK-2800 Kongens Lyngby, Denmark bTechnology Centre Mongstad (TCM DA), 5954 Mongstad, Norway
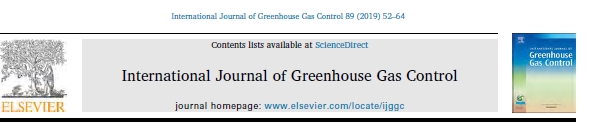
Received 3 October 2018; Received in revised form 24 June 2019; Accepted 27 June 2019
Available online 22 August 2019
1750-5836/ © 2019 Elsevier Ltd. All rights reserved.
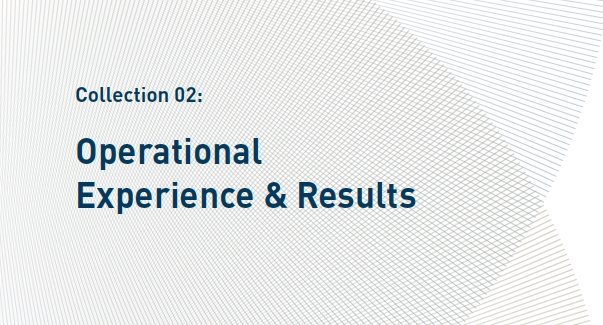
The lean vapor compressor (LVC) unit at Technology Centre Mongstad (TCM), Norway has been tested using 30 wt% monoethanol amine (MEA) and flue gas from the combined cycle gas turbine (CCGT) based combined heat and power (CHP) plant. The aim was to study the impact of LVC on the CO2 capture efficiency and energy profile of the TCM plant. 16 cases have been tested with and without LVC, and with various process parameters such as LVC pressure, solvent flow, inlet flue gas CO2 concentration, and stripper pressure. Absorber and stripper process conditions were recorded during these tests. The operation of the TCM amine plant was very steady. Standard deviation and reproducibility of the various process parameters were satisfactory.
Overall, the LVC results are as expected. A clear trend shows lower operating LVC pressure gives less specific reboiler energy consumption. A maximum thermal energy reduction of 25% was obtained when applying LVC at the expense of a typical LVC electrical energy consumption of 0.1 to 0.2 GJ electric/ton CO2. Additional results show that the specific reboiler duty (SRD) may have a characteristic non-linear dependence on solvent flow rate. Higher stripper pressure may decrease the specific reboiler duty and be beneficial to the thermal power used in the plant at the expense of increased LVC electrical power consumption.
Lower SRD was obtained when increasing the inlet flue gas CO2 concentrations both with and without LVC. For the LVC cases, no significant indication of additional energy requirement was observed when increasing the CO2 capture rate. The LVC power consumption in this study was to a large extend conservative due to a specific LVC design chosen. The presented results will help to enhance the accuracy of future CO2 capture engineering designs.
This article is behind a paywall. For futher information: https://www.sciencedirect.com/science/article/abs/pii/S1750583618307552?via%3Dihub