11. ION’s 6-month campaign at TCM with its low-aqueous capture solvent removing CO2 from natural gas-fired and residue fluid catalytic cracker flue gases (2018)
E.E.B. Meuleman, A.R. Awtry, T.R. Silverman, S. Heldal, G.A. Staab, R. Kupfer, C. Panaccione, R. Brown, J.S. Atcheson, A.E. Brown
ION Engineering, Boulder, CO, 80301 USA
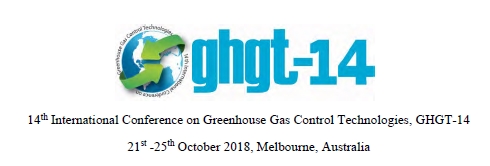
ION Engineering’s (ION) advanced solvent is one of the leading second-generation solvent systems currently under development for post-combustion carbon dioxide (CO2) capture. This paper discusses the results obtained at CO2 Technology Centre Mongstad (TCM) in Mongstad, Norway between September 2016 and April 2017, where ION captured over 14,800 tonnes of CO2 throughout the 2,775-hour testing campaign. The testing was done on flue gases from a natural gas-fired combined cycle heat and power facility (CHP) and a residue fluid catalytic cracker (RFCC) from the adjacent Statoil refinery at a scale comparable to 12 MWe. The CO2 concentrations in both flue gas types could be varied using recycle from the stripper or dilution by air. In this work, CO2 concentration settings of between 3.6% and 15.0% were tested. In the TCM plant, which is not optimized for ION’s solvent system, ION achieved a specific reboiler duty (SRD) as low as 3.2 MJ/kg CO2 during the testing at TCM while demonstrating 90% capture efficiency with low emissions and low corrosion. Furthermore, testing showed capturing 98% of the CO2 with ION’s solvent results in only a 10% increase in energy consumption. The results from ION’s campaign at TCM were then used to validate the ION process model in ProTreat® to a high accuracy. Subsequent process design optimization shows ION’s solvent is capable of an SRD of less than 2.5 MJ/kg CO2 when incorporating ION’s key process operations. Throughout pilot testing, ION has confirmed its understanding of process improvements and analytics that will enable successful operation of its solvent system at significantly lower L/G circulation rates, packing heights, and regeneration energies than traditional baseline mono-ethanolamine (MEA). ION anticipates that the recently completed demonstration at TCM, along with future projects, will facilitate further advancements in the field of CO2 capture and deployment of ION’s technology.
Many research organizations and companies are developing and investigating carbon capture technologies to reduce the quantity of CO2 emitted into the atmosphere from industrial emissions. The increased CO2 levels in the atmosphere are attributed mainly to emissions from large point sources including fossil fuel power generation and other industrial facilities. Solvent-based CO2 capture technologies that interface with flue gas are most common for post-combustion processes and represent the most promising technology for retrofitting existing power plants.
Throughout small-scale pilot testing with coal and natural gas-fired flue gas, bench-scale pilot and laboratory testing with ION’s proprietary solvent, ION has consistently demonstrated significant reductions in regeneration energy requirements in comparison to traditional aqueous mono-ethanolamine (MEA). This reduction is directly correlated to ION’s physiochemical solvent characteristics, which include higher carrying capacity, a lower specific heat capacity, and advanced process design.
ION is rapidly developing its technology by leveraging existing facilities with several global and local partners. In 2013, ION completed a proof-of-principle campaign at the University of North Dakota Energy & Environmental Research Center (EERC) at the 0.25 MWe scale, testing on both coal and natural gas-fired flue gas.1,2 In 2015, ION collaborated with Southern Company to perform parametric and steady-state operations at the National Carbon Capture Center’s Pilot Solvent Test Unit (NCCC, PSTU), a 0.5 MWe coal-fired post-combustion testing facility located in Wilsonville, Alabama, USA.3-6
Following the successful campaign at the NCCC, ION tested its solvent in the Amine Plant at CO2 Technology Centre Mongstad (TCM). This TCM facility provides an absorber-stripper configuration for amine-based technologies to test carbon capture from a slipstream of flue gas from either a natural gas-fired combined heat and power (CHP) plant or residue fluid catalytic cracker (RFCC). TCM is currently the largest facility for advanced testing of CO2 capture technologies in the world. Carbon capture technologies demonstrated at TCM can readily be scaled up to commercial industry levels.
Before ION’s test campaign at TCM, TCM executed two separate campaigns to baseline the Amine Plant utilizing a 30 wt-% MEA capture solvent on flue gas from the CHP plant. In 2014, the baseline campaign utilized 3.5% CO2 concentration in the flue gas, flowing at 47,000 Sm3/hr and targeted 90% capture efficiency. The resulting SRD from the optimization of run conditions was 4.1 MJ/kg CO2,7 which was independently validated by Electric Power Research Institute (EPRI).
In 2015, the baseline campaign was repeated to demonstrate improved performance due to the incorporation of antifoam into the 30 wt-% MEA solvent. The need for antifoam became apparent after reviewing the data from the previous baseline campaign, where the stripper temperatures and pressures were very erratic, indicating foaming. The flue gas was still 3.5% CO2 with a flow rate of 60,000 Sm3/hr and achieved a capture efficiency of 83.4%. Under these conditions, and with antifoam addition to the solvent, the SRD was 3.62 MJ/kg CO2, which is now considered as the baseline case moving forward.8,9
The ION test campaign at TCM was divided into two consecutive campaigns. The first campaign involved testing on flue gas from the adjacent natural-gas fired CHP plant. The second campaign was testing with RFCC flue gas, which closely approximates the composition of coal-fired flue gas. Fig. 1 shows the primary constituents of each of the flue gases available at TCM.8
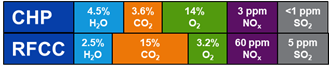
Fig. 1. Comparison of flue gas composition between CHP and RFCC sources.
The Amine Plant at TCM has the capability to recycle captured CO2 back into the flue gas to increase the CO2 concentration in CHP flue gas from 3.6 vol-% up to 14 vol-%. Similarly, the RFCC flue gas can be diluted with air to drop the CO2 concentration from 15% down to 4%.8 With this flexibility, the CO2 concentration of either flue gas can be adjusted to a value that closely approximates flue gas from a coal-fired power plant (ION typically uses 12.5 vol-% when simulating flue gas from a coal-fired power plant). The benefit of using CHP flue gas for amine-based carbon capture is that the NOx and SO2 concentrations are lower and do not contaminate the solvent. The RFCC flue gas more closely approximates coal-fired flue gas, not only in CO2 but also in O2, NOx, and SO2. The primary difference between RFCC flue gas at TCM and flue gas from coal plants is the lack of fly-ash and the presence of sulfuric acid mists or aerosols. Once TCM installed and commissioned a Brownian Demister later in ION’s campaign to address aerosol inflow, the RFCC gas at TCM was an excellent representation of coal-derived flue gas.
Beginning the testing campaign with CHP gas in October 2016, ION tested flue gas with a CO2 concentration of 4 vol-% and gradually worked up to 12.5 vol-%, using captured CO2 recycle, in preparation for testing with the RFCC flue gas by February 2017. ION classified the capture efficiency, specific reboiler duty, and optimal L/G as primary performance metrics and they were all studied during both the CHP and the RFCC campaigns. Also, secondary performance indicators of emissions, breakdown rates, and solvent make-up rates were studied during both campaigns. ION’s CHP campaign lasted from mid-October 2016 until mid-February 2017. The RFCC campaign immediately then began and concluded at the end of April 2017. The solvent was changed out at the start of the RFCC campaign to evaluate the above-mentioned secondary metrics based on the same starting conditions of the solvent.
Fig. 2 shows the process flow diagram for the TCM Amine Plant.8 The flue gas has a specified capacity and minimum turndown of 67,200 Sm3/hr, and 25,000 Sm3/hr, respectively, for the portion of the testing using the CHP plant as the feed source for the flue gas. The ION testing on CHP flue gas testing utilized a gas flow rate of 50,000 Sm3/hr. The flue gas feed used for the RFCC campaign was supplied by the refinery and has a specific capacity and minimum turndown of 60,000 Sm3/hr and 20,000 Sm3/hr, respectively. After the installation of the BD filter, the maximum gas flow rate from the refinery was about 37,000 Sm3/hr, and ION typically used a flow of 35,000 Sm3/hr. The Direct Contact Coolers (DCC) for each flue gas source were used to cool the incoming flue gas down to the target of 20-25 °C and saturate the flue gas with water vapor. This is typical conditioning of the flue gas prior to introduction into the absorber column. The absorber is a rectangular polypropylene-lined concrete column with a cross- section of 3.55 m x 2.00 m and a height of 62 meters (m). The amine-flue gas contact area in the absorber consists of three beds of stainless-steel (SS) structured packing with a total height of 24 m across three beds, where the lower bed has a height of 12 m, and the middle and upper are both 6 m tall. ION ran experiments utilizing various amounts of packing height throughout the test campaign.9
Above the upper part of the absorber section, two water wash sections are installed with the purpose to remove any carryover solvent vapors prior to venting to the atmosphere. Both of the water washes consist of a 3 m section of SS structured packing and were also used to maintain the water balance in the system by adjusting the circulating water temperature of the upper and lower water-wash sections as the scrubbed flue gas exits the column.9 While the lower water-wash was always operated as a typical water wash system, the upper water wash had the flexibility to be operated as either a water wash section or as an acid wash for the tests presented in this paper. The option of adding acid to the upper wash section at TCM enables technology developers to neutralize any solvent vapors to keep emissions below the acceptable limits established by TCM. The consequence of utilizing the upper wash section as an acid wash, however, is that any amine emissions captured cannot be returned back to the system which directly affects the solvent make-up rates. It is therefore desirable to test the effectiveness and need for an acid wash during the campaign but to strive for a twofold water wash system during normal operation.
ION installed two Multi-component Liquid Analyzers (MLA), one on each of the rich and lean solvent streams (not shown in Fig. 2.) in order to monitor near real-time solvent composition. The data from the MLA was used to add makeup solvent and maintain a stable water balance. Additionally, the MLA provided CO2 loading information about the solvent and process changes could be evaluated in near real-time, thereby providing critical information on reaching steady-state operation.10 The rich solvent then passes through a liquid-liquid heat exchanger to the regeneration side of the process. This heat exchanger transfers heat from the hot, lean solvent into the cold CO2-rich solvent, often referred to as the lean-rich cross exchanger. TCM has two stripper/reboiler systems (CHP and RFCC) available to recover the captured CO2 and return CO2-lean solvent back to the absorber. The CHP stripper was designed to process the amount of CO2 that is generally captured from a flue gas containing 3.5-6% CO2.
The larger RFCC stripper/reboiler was used to recover the captured CO2 and return CO2-lean solvent back to the absorber when testing was performed on flue gas with CO2 content above 6 vol-% (CHP + recycled CO2, or RFCC with and without air dilution).
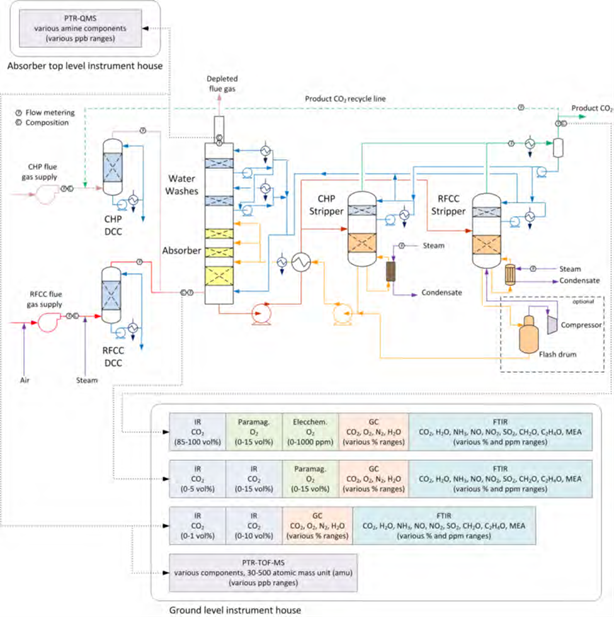
Fig. 2. The TCM amine plant with two flue gas sources, CHP and RFCC, and the corresponding two strippers. Flue gas analysers and flow meters are located at absorber inlet (I), outlet/depleted flue gas (II) and CO2 product (III). The dotted green line shows that CO2 can be recycled back to the absorber inlet for tests at elevated CO2 concentration in the flue gas flow. (Figure from Gjernes et al., Procedia GHGT-13, 2017).
Aside from the water washes on the absorber column, and the DCCs, there were two other processes that used cooling water. The overhead condenser, located on a common line that was shared by the CHP and RFCC strippers, was used to knock down the water content of the CO2 product gas. This was typically operated to cool the product gas to around 20 °C. Additionally, a trim cooler was present after the lean-rich cross exchanger which allowed for control of the solvent temperature entering the absorber.
ION has made definite conclusions from the data obtained from this campaign. Namely, ION’s solvent outperformed TCM’s MEA base cases7,9 which are summarized in Table 1, in a facility not optimized for ION’s solvent.
During a parametric study using CHP flue gas, the best-case achieved by ION at 3.5 vol-% CO2 was 3.37 MJ/kg CO2 with 50,000 Sm3/hr flue gas flow rate. This represents a reduction of approximately 10% in steam energy compared to the base MEA case at TCM (3.62 MJ/kg CO2),9 and was achieved without the need for additives to control foaming.
MEA (2014) | MEA (2015) | MEA + Antifoam (2015) | ION (2016) | |
CO2 Concentration, % | 3.6 | 3.6 | 3.6 | 3.5 |
Capture, % | 90.0 | 83.5 | 87.4 | 91.8 |
SRD, MJ/kg CO2 | 4.10 | 3.90 | 3.62 | 3.37 |
Table 1 – Comparison of ION CHP results at 3.5% CO2 to MEA base cases at TCM.
By adjusting the flow rate of already-captured CO2 from the stripper column and routing it to the inlet of the absorber, ION obtained testing conditions of four intermediate CO2 concentrations in the flue gas while working the CO2 concentration up to mimic what would be expected at a coal-fired power plant (11-15%). With 6.1% CO2 in a 50,000 Sm3/hr flue gas flow, the lowest SRD demonstrated was 3.24 MJ/kg CO2. Increasing the concentration up to 9.2% CO2 in the flue gas resulted in an SRD of 3.23 MJ/kg CO2. The final step up to 13.1% CO2 in the flue gas resulted in an SRD of 3.33 MJ/kg CO2. At the time of preparing this paper, there are no known published MEA baseline cases at elevated CO2 concentrations against which to compare these results. Also, these results do not represent the optimal run conditions for each CO2 concentration tested, as no optimization experiments were conducted.
Table 2 shows the key performance indicators (KPI) for a select group of tests that were executed during the CHP campaign. Each of the work packages listed in the table, apart from Aged-0, show the best-operating conditions at each of the CO2 concentrations utilized during the CHP campaign with respect to the SRD. Further optimization at each of the flue gas concentrations would likely have resulted in better performance. The test marked as Aged-0 was conducted using CHP gas but after the RFCC campaign had concluded; therefore, the experiment was performed with an aged solvent. This test was performed as a repeat of Base-0 but using the aged solvent (where Base-0 was taken on near virgin solvent). The results from Base-0 and Aged-0 can be compared to the MEA based case performed at TCM, where the SRD was determined to be 3.62 MJ/kg CO2 during the 2015 TCM baseline campaign. The water and lean CO2 content of the solvent were constant in the two experiments, meaning the active components were reduced in content by the number of breakdown products in the solvent. The results of this last test, compared to those of Base- 0, show the presence of the breakdown products in the solvent resulted in a 5% decrease in performance.
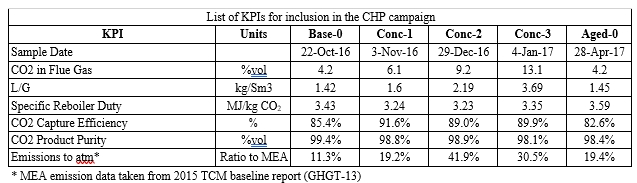
Table 2 – Table of operating conditions and resulting KPI of crucial tests performed during the CHP campaign. Base-0 test conditions are with pure ION solvent and should be compared with the Aged-0 test.
Emissions were relatively low during the CHP campaign when testing on flue gas with low CO2 concentrations (3.5-6.0 vol-%). However, when the CO2 concentration was increased towards 13 vol-%, the maximum absorber temperature increased; the higher temperature in the absorber resulted in greater evaporative solvent losses, which contributed to slightly higher emissions.
Table 3 compares the solvent and breakdown product emissions from ION’s CHP campaign with the 2015 TCM MEA campaign.8 The table demonstrates the emissions of one CO2 concentration of the inlet flue gas for MEA and compares it to four different CO2 concentrations of the inlet flue gas for ION’s campaign. The ION solvent results compare very favourably with the MEA base case’s total emissions (solvent and breakdown) of 20.8 ppm when utilized under similar and more aggressive operating conditions.

Table 3. CHP emission comparison to the TCM MEA campaign.
The ION campaign using RFCC flue gas was performed while mixing air with the flue gas to achieve a stable CO2 concentration of 12.5 vol-%. As a result of air mixing the O2 concentration increased from 4.5 vol-% of the raw RFCC gas to 7.0 vol-%. The solvent used in the CHP campaign was removed, and the RFCC campaign proceeded with a pure solvent in the system. The solvent change-out allowed for distinguishing solvent breakdown products, solvent make-up rates, and emission effects between the two flue gas sources (see Fig. 1). ION’s RFCC campaign began on February 20, 2017, immediately following the successful demonstration of 90% capture of CO2 from CHP (+ recycle) flue gas at 13.1 vol-% CO2 concentration. Due to emission issues, in the absence of the BD filter, TCM had never operated with RFCC gas for prolonged periods of time before ION’s campaign, and as such at the time of this paper’s submission there is no baseline to compare ION’s results to on RFCC flue gas.
Table 4 shows the KPIs for select tests performed during the RFCC campaign. The Base-0 test was part of a U- curve series of tests and represented the minimum SRD. This condition was repeated March 4-6, 2017 (Base-1), and again March 14-16, 2017 (Base-2), to build up run times under these conditions and evaluate the reproducibility of the results. The three EPRI tests are the second series of tests that were conducted for several days under constant operating conditions. The EPRI tests were conducted when EPRI was on site to provide third-party verification of testing procedures, telemetry, and lab analysis.
The remaining tests included in Table 4 are “Low SRD”, which is the test that achieved the lowest SRD of all the tests conditions performed during the RFCC campaign. The operating conditions that were established in “Low SRD were repeated in the EPRI tests. Finally, test “Conc-1” was included in the list of main experiments as it was the non- optimized removal for flue gas with 14.5 vol-% CO2 concentration.

Table 4 – Table of operating conditions and resulting KPI of key tests performed during the RFCC campaign.
All of the testing during ION’s RFCC campaign was carried out with 18 m of packing in the absorber column. The consequence of using 18 m instead of 24 m of packing is that the residence time of the solvent in the absorber is lower, leading to higher lean flow rates for similar capture efficiencies. With the utilization of more packing, the flow rate would have been reduced to achieve the same residence time, and the energy lost to heating solvent in the stripper would be reduced per tCO2 captured. However, a benefit of minimizing packing height is a reduction in capital expenditures.
ION completed an extensive set of parametric tests during the RFCC campaign. The results of these tests have demonstrated the optimum L/G for obtaining low SRDs. The best SRD achieved was 3.25 MJ/kg CO2, which was achieved at the highest tested operating pressure in the stripper. Operating at this higher pressure required more steam to the stripper sump, where the stripper sump temperature also increased. Reducing the pressure of the stripper led to higher water vapor losses and, as expected, an increase in SRD.
Typically, during the RFCC campaign where the CO2 concentration was 12.5 vol-%, the maximum absorber temperature increased up to 78 °C, which is the maximum temperature recorded during the entire ION test campaign. This higher temperature in the absorber resulted in greater vapor-liquid equilibrium (VLE) losses, which contributed to higher emissions passing through the water washes and leaving the absorber stack. Consequently, the acid wash was utilized briefly in the RFCC campaign to assist in reducing emissions until operational controls could be determined that assisted in maintaining low emissions.
The RFCC campaign started up on Feb 21, 2017, and ran through April 28, 2017, where the Amine Plant was available for testing to ION for 1,346 hours of 1,427 hours. ION was successfully testing for 1,222 hours; there were stoppages of 7 hours due to emissions, and planned stoppages for 115 hours for process changes. These durations led to an on-stream factor of 99.3% when taking into account only issues related to the use of ION’s proprietary solvent.
Optimization experiments were conducted in both the CHP and RFCC campaigns to determine the run conditions at which the best energetics could be achieved for each flue gas. Fig. 3 shows the results of two of these optimization curves where the CHP flue gas at 4.0 vol-% CO2 and RFCC flue gas at 12.5 vol-% CO2. The CHP data was acquired using the smaller CHP stripper. The final difference between the two sets is that the RFCC testing was performed at 35,000 Sm3/hr gas flow rate, which is lower than the 50,000 Sm3/hr flow rate used for CHP testing. The slower flow rate leads to more residence time in the absorber and improves the capture of CO2 by the solvent.
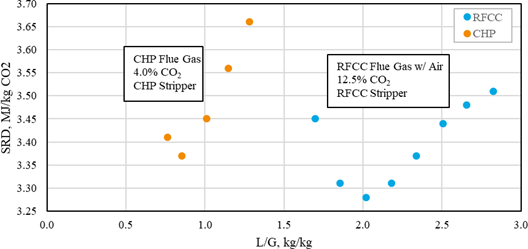
Fig. 3. – U-curves generated for CHP flue gas and RFCC flue gas.
ION conducted a test to evaluate various capture efficiencies with fixed L/G, while only changing the steam flow to the reboiler heat exchanger (HEX). This test included operating conditions where the CO2 capture efficiency was increased up to 98% in order to evaluate the cost of high capture rates. In Fig. 4 below, each point is increased stripper sump temperature (while holding all other parameters nearly constant) and the results of SRD and capture efficiency are plotted connecting the increasing sump temperatures. The capture efficiency increases by increasing the carrying capacity of the solvent (further leaning the solvent at the higher temperature). Simultaneously, the variation of SRD for each sump temperature suggests that there is an optimum capture efficiency at a particular L/G that reduces the steam flow rate to the system; the optimum capture rate is around 85% in this example. The higher SRD at the lower temperatures (left side of the graph below) is due to the energy losses associated with the penalty of re-heating the solvent at the fixed solvent flow rate. Just like the traditional U-curve plots, this data demonstrates the optimal capture efficiency (and required SST) for a particular L/G. Although not every data point is the result of an optimized setting the graph indicates that for ION’s solvent when the capture efficiency is increased from 90% to 98%, there is only about 10% increase in SRD.

Fig. 4. – Plot of SRD as a function of capture efficiency while increasing steam flow to the reboiler (increasing the SST) and holding L/G constant (i.e., a hockey stick plot).
The evaluation of the heat stable salts (HSS) formation rates in the solvent can provide information on the dominant degradation pathways for both the CHP and RFCC campaigns. The concentrations are plotted against the total CO2 captured by the solvent in each of the campaigns. Fig. 5 shows the results of the solvent analysis on four individual HSS throughout both campaigns: Oxidation Products 1, 2, 3, and nitrate. The data were evaluated with the expectation that the CHP campaign would show more oxidative degradation than the RFCC campaign due to the higher O2 concentration in the CHP flue gas.
Starting with Oxidation Product 1 in Fig. 5, the formation rate as a function of tonnes of CO2 captured is very similar for both the CHP and RFCC flue gas sources, where the accumulation of Oxidation Product 1 is slightly higher with the RFCC flue gas. Oxidation Product 2 show a significantly higher accumulation rate (relative to the amount of CO2 captured) during the CHP campaign where the oxygen content in the flue gas is two to three times higher than that of the RFCC flue gas. Oxidation product 2 is an oxidative decomposition product of the solvent and can thermally decompose to Oxidation Product 3 and CO2. Therefore, it makes sense that the accumulation of oxidation product 3 increases at a faster rate in the CHP campaign where there is more Oxidation Product 2. Finally, the nitrate comparison is shown in Fig. 5. The NOx concentration in the CHP flue gas is significantly lower (<5ppm)8 than what is present in the RFCC flue gas (60ppm)8 and the two charts show the effect of the higher concentration. A percentage of NOx is captured by the solvent, and the end products are nitrate HSS; thus, as was expected, the nitrate HSS values are elevated in the RFCC results.
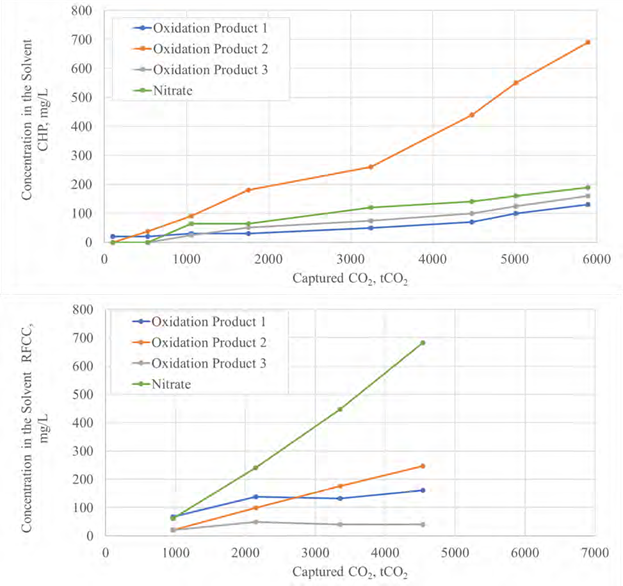
Fig. 5. HSS formation for the CHP (top) and RFCC (bottom) campaigns as a function of total CO2 captured.
TCM installed several corrosion coupons into the system to evaluate the ION solvent’s impact on typical industrial materials. The coupons were installed at two locations: one in the rich stream, just after the LRXC on the stripper side (hot rich solvent) and the second one was in the lean stream, just prior to the LRXC (hot lean solvent). Table 5 shows the results from this corrosion study.
The corrosion coupons were installed prior to the start of testing and left in place throughout the entire ION test campaign (including down times and periods where TCM was upgrading the system). They were removed after the campaign and evaluated to determine weight loss of the materials. As can be seen in Table 5, the carbon steels tested, S235 carbon steel (similar to C1010 carbon steel) and A106 Gr B (pipe grade carbon steel) had no remaining coupons at the conclusion of the testing in either installed location. By way of comparison, ION also utilized a carbon steel coupon in the NCCC test campaign of a very similar variety to S235 (C1010). and has included those results for comparison in Table 5.
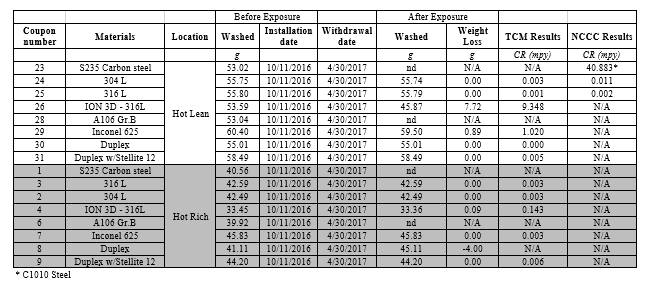
Two other samples were evaluated at TCM that can directly be compared to the results obtained during the NCCC test campaign. The 304L and 316L samples in the hot lean solvent showed similar low corrosion rates similar to what was seen at NCCC. The other alloys tested with coupons include Inconel 625, and two Duplex coupons. The Inconel alloy had a corrosion rate (CR) of 1.0 mils/yr in the hot lean solvent and an insignificantly small CR in the hot rich solvent. The Duplex coupon, which is the material used in constructing the Amine Plant, also showed little to no corrosion.
In addition to these standard materials, ION provided four unique coupons (labelled as ION 3D – 316L in Table 5) which were 3D printed by Lawrence Livermore National Laboratory (LLNL) using 316L stainless steel material. Fig. 6 shows the images of the 3D printed coupons provided by LLNL, where a single print job was used to create the coupons, that were cut into slices according to the dimensions required for insertion into coupon holder at TCM. Only two coupons were used in the campaign, and both coupons had a portion of the surface printed as a textured lattice seen in Fig. 6. ION is investigating 3D printed materials for possible use in future development work.
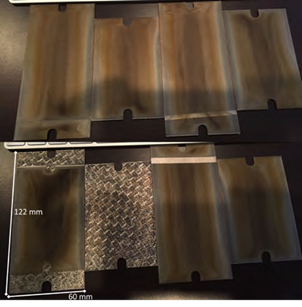
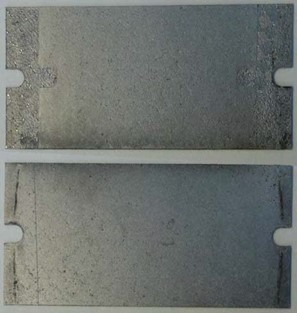
Fig. 7. – 3D printed coupon made of 316L stainless steel. This coupon was installed in the hot lean solvent line. These photos show the front and back of the coupon after exposure to the solvent throughout the ION test campaign.
As can be seen in Fig. 7, the 3D printed coupon installed on the hot lean solvent flow showed appreciable corrosion, with a CR of 9.4 mils/yr. The stock 316L coupon showed no corrosion under the same conditions (see results in Table 5). This supports the concern that the more porous 3D printed material is subject to advanced corrosion rates when exposed to hot lean solvent. Fig. 7 shows the hot-lean coupon after the ION test campaign, where the texture at the ends of the coupon has evidently been reduced. The porosity of the coupon can also be more easily seen in this figure. The data for the coupon in the hot rich solvent indicates that this location in the process is not as corrosive as the hot lean location. There is still a measurable loss of material (CR = 0.1 mils/yr), but it is two orders of magnitude smaller than the hot lean location. Fig. 8 shows the images of the coupon installed in the hot rich solvent and, unlike the hot lean location, the coupon appears very near the original condition. Additional exposure of these coupons at other locations in the Amine Plant will aid in determining if this material is suitable for use in an amine-based carbon capture plant.
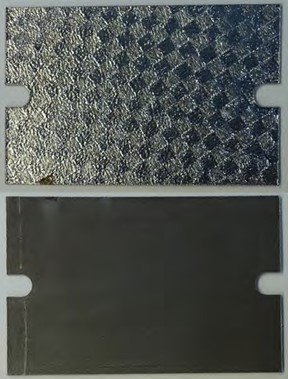
Fig. 8. – 3D printed coupon made of 316L stainless steel. This coupon was installed in the hot rich solvent line. These photos show the front and back of the coupon after exposure to the solvent throughout the ION test campaign.
One of the key benefits of testing at TCM is to obtain the telemetry and key performance indicators from steady state operations can be used to validate ION’s process model. The validation of this process model is more important in advancing the case for a commercial system based on ION’s advanced solvent than the demonstrated test results on TCM’s 12 MWe pilot plant.
The empirical results from testing on an existing plant, where only minor modifications were implemented when incorporating ION’s advanced solvent, will not yield the energy savings that have been shown in the ION optimized design process model. The primary obstacle in achieving the low SRDs is that there is not enough capability in the stripper to prevent excess energy (via steam) from leaving the stripper to the condenser. For ION’s high carrying capacity solvent, a cold-rich bypass (CRB) strategy is needed to keep the energy in the system.11 Additionally, TCM does not currently have the capability for solvent cooling in the absorber via an inter-stage cooling system. This cooling increases the uptake of the CO2 in the absorber, and further increases the carrying capacity of the solvent.
ION has built a model of the TCM process in ProTreat® and modeled the capture processes using the same parameters that were tested in the field.12 The following section demonstrates how the test results at TCM were compared against the results from the process model, in order to verify the accuracy of the model and build confidence that a custom-built plant would achieve the designed performance of below 2.4 MJ/kg CO2.
During the TCM campaign, ION tested over 150 operating configurations with 76 of those configurations being on RFCC flue gas. The scatter plots in Fig. 8 show the diversity of operating conditions that ION covered in the RFCC test campaign. ION selected 51 random operating conditions to simulate in ProTreat® to generate model results for comparison. In Fig. 9 are highlighted markers (orange) indicating the operating conditions of the 11 experiments that were used to generate a parity plot shown in Fig. 10. These 11 experiments were selected to cover a wide range of testing conditions and Fig. 10 shows the resulting parity plot, where the results of the model are compared to the empirical data. The ProTreat® process model successfully predicts the key parameters such as densities, capture rate, SRD, working capacity, and stripper sump temperature. From these results, the data has demonstrated how well the actual and modeled results converge over this wide range of operating conditions. This allows ION to incorporate its custom process operations and confidently design commercial plants that provide significant cost-savings that are required for commercial deployment.
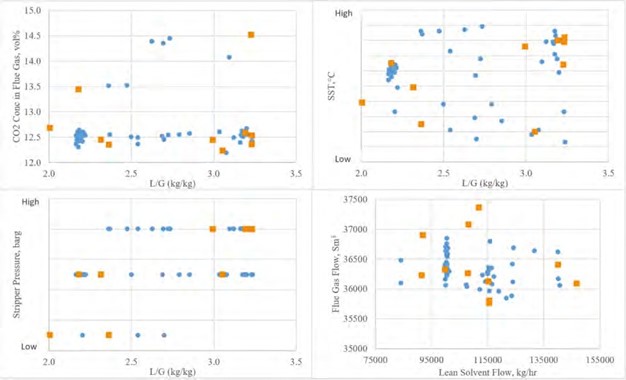
Fig. 9. – Scatter plots showing the range of variables tested on RFCC flue gas. The orange markers represent the 11 experiments that are used to generate the parity plot.
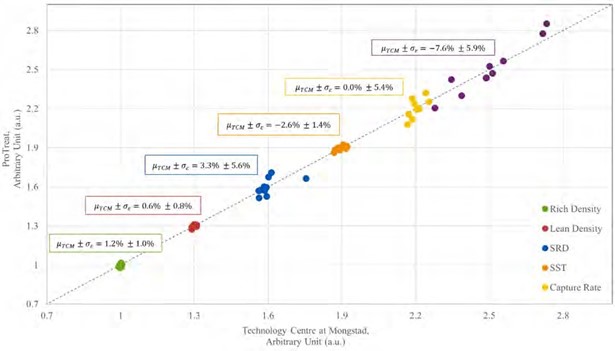
ION is very encouraged by the results of both the CHP and RFCC campaigns executed at TCM. The following are the main findings from the more than 2,750 hours of operation, where 150 test settings led to capturing well over 14,000 tCO2.
The CHP campaign concluded with optimization testing in April 2017 with aged ION solvent and found that under optimal operating conditions the best achieved specific reboiler duty (SRD) was 3.37 MJ/kg CO2 for scrubbing
4.0 vol-% CO2 flue gas. This represents a reduction of 15% in steam energy compared to the base case of MEA without anti-foam at TCM (3.9 MJ/kgCO2) and approximately 10% when compared to the base case of MEA with anti-foam (3.62 MJ/kgCO2). ION’s results were achieved without the need for additives to control foaming.
The RFCC campaign produced a low SRD of 3.25 MJ/kg CO2 when scrubbing 12.5 vol-% CO2 flue gas after optimization of operating parameters. At the time of this reporting, TCM has yet to publish MEA baseline testing on RFCC flue gas that might be used for comparison.
ION has concluded from the results at TCM that its module in the ProTreat® process model accurately predicts the performance of its solvent over a wide operating window. A close investigation of the rich and lean loadings indicates a slight underprediction of the working capacity, and these findings have led ION to conclude that its commercial- scale plant designs provided conservative estimates of actual plant performance; the current ProTreat® model resulted in process designs with an energy consumption of 2.4 MJ/kgCO2.
The corrosion coupon analysis showed that carbon steel coupons installed in the process (both rich and lean locations) were not recovered, which indicates high corrosion rate of these materials. The 304L and 316L stainless steel, as well as the Duplex and Inconel specialty metals all had acceptable corrosion rates (<0.01 mils/yr). The only degradation occurring was noticeable on the Inconel coupon in the hot lean solvent (~1 mils/yr).
ION implemented an online liquid monitoring system for real-time analysis of solvent, water, and CO2. Overall, the MLA performed excellently with precise detection of near-real-time trends, where changes with increments of
0.5 wt-% could be observed. With these promising results in the initial pilot release, ION believes the MLA to be a useful and vital tool for both monitoring liquid compositions as well as providing a mechanism to automate and optimize the control of CO2 capture processes.
ION has conducted a thoughtful, comprehensive, and successful campaign in close collaboration with TCM. CO2 was successfully removed and captured for extended periods of time from CHP as well as RFCC gas. Throughout pilot testing, ION has confirmed its understanding of process improvements and analytics that will enable successful operation at significantly lower L/G circulation rates, packing heights and regeneration energies than MEA. ION’s process design tool has been validated to a high accuracy that allows ION to incorporate its custom process operations. ION anticipates that the recently completed demonstration at TCM, along with future projects, will directly impact the state-of-the-art of CO2 solvent technologies and facilitate advancement of CO2 capture towards commercialization and widespread implementation of ION technology.
This material is based upon work supported by the U.S. Department of Energy National Energy Technology Laboratory (DOE-NETL) under cooperative award number DE-FE0013303. ION would also like to wholeheartedly thank the teams at TCM and their stakeholders for their hospitality and support throughout ION’s campaign. LLNL is kindly acknowledged for providing 3D-printed coupons for corrosion testing.
- Brown A, Brown N, Heller G, Staab G, Silverman T, Kupfer R, Brown R. Evaluating the Impact of ION’s CO2 Capture Technology on a Sub-Critical Pulverized Coal Power Plant, EUEC Conference Proceedings, NM, USA; 2014
- Brown N, Heller G, Staab G, Silverman T, Kupfer R, Brown R, Brown A. ION Advanced Solvent System for CO2 Capture, DOE-NETL CO2 Capture Technology Project Review Meeting, Conference Proceedings, PA, USA; 2014.
- Brown N, Heller G, Staab G, Silverman T, Kupfer R, Brown R, Brown A. Novel advanced solvent-based carbon capture pilot demonstration at the National Carbon Capture Center, Energy Procedia 2017; 114:1075-1086.
- Meuleman E, Brown N, Panaccione C, Staab G, Silverman T, Heller G, Brown A. Novel Advanced Solvent-based CO2 Capture Pilot Plant demonstration; ION at NCCC, The 41st International Technical Conference on Clean Coal & Fuel Systems, Clearwater FL; 2016.
- Meuleman E, Brown N, Panaccione C, Staab G, Silverman T, Heller G, Brown A. Novel Advanced Solvent-based CO2 Capture Pilot Demonstration – Fast-tracking the development & scale-up, ECI CO2 Summit II: Technologies & Opportunities, Santa Ana Pueblo, NM; 2016.
- Meuleman E, Silverman T, Staab G, Heller G, Brown N, Brown R, Kupfer R, Atcheson J, Brown A. ION Advanced Solvent CO2 Capture Pilot Project, DOE-NETL CO2 Capture Technology Project Review Meeting, Conference Proceedings, PA, USA; 2016.
- Hamborg ES, et al. Results from MEA testing at the CO2 Technology Centre Mongstad. Part II: Verification of baseline results. GHGT-12, Energy Procedia 2014; 63:5994-6011.
- Morken AK, Pedersen S, et al. Degradation and Emission Results of Amine Plant Operations from MEA Testing at the CO2 Technology Centre Mongstad, GHGT-13, Energy Procedia 2017; 114:1245-1262.
- Gjernes E, et al. Results from 30 wt% MEA performance testing at the CO2 Technology Centre Mongstad. GHGT-14, Energy Procedia 2017; 114:1146-1157.
- Panaccione C, Staab G, Awtry A, Kupfer R, Silverman T, Brown R, Atcheson J, Meuleman E, Brown A. Multi-component liquid analyser during steady-state and dynamic CO2 capture operations: Near real-time feedback in industrialized environment, GHGT-14 Proceedings, Melbourne, Australia; 2018
- Cousins A, et al. Model verification and evaluation of the rich-split process modification at an Australian-based post-combustion CO2 capture pilot plant, Greenhouse Gas Sci Technol. 2012; 2:329-345.
- Brown N, Staab G, Silverman T, Heller G, Kupfer R, Panaccione C, Brown A. ProTreat® simulation accurately represents experimental results for post-combustion carbon dioxide capture with novel mixed amine solvent in real process environment, Energy Procedia 2017; 114:1380- 1387.