CO2 Capture from SMR type flue gas using CESAR1 solvent at Technology Centre Mongstad (2022)
Sundus Akhtera*, Ahmad Wakaaa, Anette Knarvika,b, Erik Gjernesc, Ida M. Bernhardsenb, Muhammad I. Shaha,c
aTechnology Centre Mongstad, 5954 Mongstad, Norway bEquinor ASA, PO Box 8500, 4035 Stavanger, Norway cGassnova SF, Dokkvegen 11, 3920 Porsgrunn, Norway
Abstract
The Technology Centre Mongstad (TCM DA) in Norway has investigated the CO2 capture performance with the non-proprietary CESAR1 solvent for flue gases with CO2 concentration like that of a SMR (steam methane reforming) furnace. The basis for this investigation is Equinor’s SMR unit at Tjeldbergodden methanol plant. Specific reboiler duty (SRD) is reported for 90% CO2 capture from flue gases with 10 and 15 vol% (dry) CO2 content when using 12 and 18 m absorber packing height. Tests at 10 vol% (dry) CO2 content confirmed that SRD levels below 4 GJ/ton CO2 are achievable with only 12 m absorber packing height, but lower SRD values are achieved with 18 m absorber packing height. This illustrates that a more compact absorber will give lower CAPEX at the expense of a higher heat requirement for the CO2 stripper. During the tests, precipitation was observed in the absorber packing despite that the overall absorber condition were unfavorable for this to occur. Also, foaming in stripper was observed and mitigated by the use of anti-foam.
1. Introduction
The Technology Centre Mongstad (TCM DA), established in 2012, is one of the world’s largest facilities to test, verify and demonstrate different post combustion carbon dioxide capture (PCC) technologies. The company is a joint venture between Gassnova (the Norwegian state), Equinor, Shell and Total Energies with a common vision to facilitate development of carbon capture and storage (CCS) for the wide deployment of large-scale carbon capture technologies across industries. The facility is located next to the Equinor refinery in Mongstad providing two types of flue gas sources: (1) combined cycle gas turbine (CCGT) based heat and power plant flue gas (CHP) and (2) residual fluid catalytic cracker (RFCC) flue gas. The different flue gas sources enable TCM to mimic flue gases from different industries such as waste incineration, gas processing, steam reforming and oil refining.
Since the start-up in 2012, TCM has gained valuable knowledge and experience with the use of the non-proprietary solvents monoethanolamine (MEA) and CESAR1 for CO2 capture. CESAR1 is a blend of 27 wt% 2-Amino-2- methylpropanol (AMP) and 13 wt% piperazine (PZ) and is considered to be a better solvent than MEA in terms of
thermal energy and stability [1,2]. CESAR1 was first tested at TCM as a part of the ALIGN-CCUS campaign in 2019 where the energy demand was found to be around 10% lower than that of 30 wt% MEA. Although the comparison is not straightforward, the tests provided valuable learnings with this solvent [3,4]. To further explore the solvent’s potential, the owners of TCM DA performed two campaigns with CESAR1 from April to December 2020. The goal of the campaigns was to carry out long term operation with this solvent, close knowledge gaps on the solvent performance with different flue gas compositions, to understand cost reduction potential of CO2 capture with CESAR1 and perform thermal reclaiming [5] of the solvent.
This paper presents results from the part of the CESAR1 owner’s campaign which was carried out to understand the CESAR1 solvent’s potential for CO2 capture from steam methane reformer (SMR) flue gas. Steam methane reforming is a key technology for converting natural gas to synthesis gas and is the dominant technology for hydrogen production. In this work, the CO2 concentration was varied from 10 to 15 vol% (dry). The CO2 concentration of 10 vol% mimic the SMR flue gas at the Equinor methanol plant at Tjeldbergodden [6]. The methanol plant at Tjeldbergodden is the largest in Europe. It produces approximately 900,000 tonnes of methanol per year and accounts for around 25% of total European methanol production. The methanol is produced using natural gas and pure oxygen as raw material. Natural gas is converted to synthesis gas by combined reforming (i.e. steam methane reforming followed by autothermal reforming) and the resulting synthesis gas is converted to methanol. Currently, the methanol plant at Tjeldbergodden emits around 300,000 tonnes CO2 per year. As most of this CO2 is generated in the SMR furnace by combustion of fuel, there is a considerable potential for CO2 reduction. The fuel combusted in the SMR is a mixture of natural gas and purge gas from the synthesis gas, and the composition of the SMR flue gas will depend on the purge gas rate, and composition of the natural gas.
The first part of this paper presents the energy performance obtained with the CESAR1 solvent when varying the CO2 concentration, absorber packing height and flow rates, while maintaining 90% CO2 capture. The second part of the paper describes operational experiences with CESAR1 solvent at TCM.
2. Assessment of CESAR1 performance with SMR flue gas
2.1 TCM amine plant description
Figure 1 shows a simplified illustration of the TCM amine plant in CHP mode. Flue gas from the blower is conditioned and saturated with water to the required temperature (normally 20-50 °C) in the direct contact cooler (DCC). CO2 is captured in the absorber by the lean amine flowing downwards counter current with the flue gas. The depleted flue gas passes through two water wash stages before being emitted to the atmosphere. Rich amine from the absorber is pumped through the rich/lean cross plate heat exchanger to the stripper where the CO2 is released using a steam-heated reboiler. The lean amine is then pumped back to the absorber.
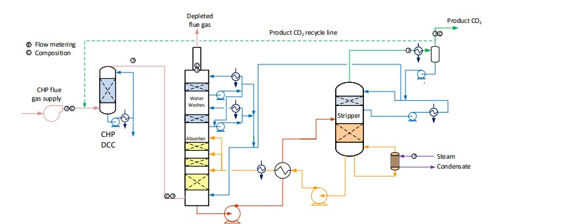
The plant is flexible and offers the possibility to test several different configurations and a wide range of flue gas flow rates and compositions. Two strippers are available with capacities up to about 3,500 and 8,000 kg CO2/h. The latter, named RFCC stripper, was in operation during the present test program. The lean amine solvent can be fed at various solvent flow rates utilizing 12, 18 or 24 m of the absorber structured packed bed (highlighted in yellow in Figure 1). The CO2 content in the flue gas can be increased by recycling captured CO2 to DCC inlet. A more detailed description of the amine plant is available elsewhere [7,8].
2.2 CESAR1 campaign mimicking SMR flue gas
The three phases A, B and C of the test program are presented in Table 1. The plant was operated to capture 90% CO2 from a flue gas with 10 to 15 vol% (dry) CO2, i.e. mimicking SMR flue gas. For each phase, the objective was to determine the optimal specific reboiler duty (SRD) by varying the solvent circulation rate.
The tests in Phase A were performed at 18 m absorber packing height to find the lowest possible SRD. In phase B, the packing height was reduced to 12 m. This was made to illustrate the consequence of utilizing a more compact absorber that reduces CAPEX at the expense of increased heat requirement and OPEX. During phase C, tests were conducted at 18 m and at a higher CO2 concentration to better understand the impact of flue gas CO2 concentration at a target capture rate of 90%. All tests were made with CHP flue gas including CO2 recycling and with the RFCC stripper in operation. CO2 recycling increased the CO2 content in the flue gas into the absorber from about 4 to 10 and 15 vol% (dry). The target CESAR1 solvent concentration during the campaign was 40 wt% comprising 27 wt% AMP and 13 wt% Piperazine. This concentration was similar as used in the previous ALIGN-CCUS campaign at TCM [4], however, variations occurred both in total amine concentration and Piperazine and AMP ratio. Calibration and validation of analysers were carried out before and during the campaign to ensure good data quality on solvent performance and compliance with emission permit.
Table 1 Operational parameters for tests mimicking SMR flue gas.
Phase | Abs. pack height [m] | Inlet CO2 conc. [Dry vol%] | Flue gas x 1000 [Sm3/h] | Flue gas temp. [oC] | L/G [kg/Sm3] | CO2 cap. [%] | CO2 cap.1 [kg/h] |
A | 18 | 10 | 48 | 35-37 | 1.7-2.3 | 90 | 7,560 |
B | 12 | 10 | 48 | 38 | 1.9-3.2 | 90 | 7,500 |
C | 18 | 15 | 34 | 40 | 2.9-3.8 | 90 | 7,940 |
1Captured CO2 for test A5, B7* and C7.
The amount of CO2 being captured can be calculated based on either the mass balance over the absorber; i.e. CO2 in versus CO2 out of the absorber or on the CO2 mass flow out of the stripper. The results presented here are based on the latter. The CO2 capture rate is then calculated as mass flow of captured CO2 versus the CO2 mass flow into the absorber. SRD is calculated based on the steam side enthalpy difference over the reboiler heat exchanger divided by the amount of captured CO2. TCM is well equipped with multiple analysers and flow meters for each of the three gas flows. The present analysis is made using the same selection of analysers and flow meters as [9].
Each test was operated up to 24 hours targeting stable operation and each of the data points presented in Figure 2 to Figure 4 represent an average over typical 2 hours of stable operation within that test interval. The data quality may be affected by steam quality and moisture in the CO2 product flow out of the stripper. For phase A and part of phase B, steam temperature into the reboiler heat exchanger was close to saturation temperature and thus introduced some uncertainty on the steam quality. It should be noted that for phase A, B and C, the measured moisture content out of the stripper fluctuated rather lively.
2.3 Results from flue gas with 10 vol% CO2
The energy required to capture 90% of the CO2 from the CHP flue gas with recycling to mimic 10 vol% SMR
furnace type of flue gas was determined during phase A and B tests.
Figure 2 (a) shows SRD at 90% capture rate for phase A tests utilising 18 m packing height. During the tests the flue gas flow rate was kept constant at 48,000 Sm3/h, while the solvent flow rate was varied. The optimum steam consumption achieved for tests A5 and A1 were approximatively the same, i.e. 3.2 GJ/ton CO2 at lowest L/G ratio around 1.9 kg/Sm3, at lean solvent flow rates 90,800 kg/h and 92,100 kg/h, respectively. Note that A1 test was conducted at 35 °C while A5 tests was carried out at 37 °C. The increase in temperature was applied to control precipitation in the absorber. As experienced from previous campaigns [4], increasing the flue gas inlet temperature has a negative effect on the SRD. However, Figure 2 (a) shows that SRD during A5 test is slightly lower than A1 test. This may be due to instability in the plant operation during A1 test and since calibration was not performed for the IR-high instrument at absorber inlet. The IR-high instrument showed higher values while the actual CO2 concentration during A1 test was 9.5 vol% (dry). Calibration was made after the A1 test and point A5 is considered as the optimum for the phase A tests. After the B series the A5 test was repeated with an SRD of 3.3 GJ/ton CO2. This illustrates reduced reproducibility due to minor changes in operational conditions etc.
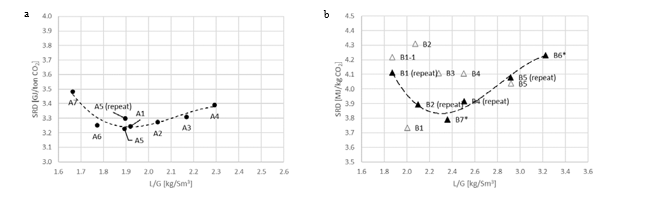
Phase B utilised 12 m absorber packing height while maintaining capture rate at 90% as well as flue gas flow at 48,000 Sm3/h. SRD plotted against L/G ratio for tests from phase B is shown in Figure 2 (b). During the B1-1 and B2 tests, there was an issue with controlling the steam temperature and pressure to the RFCC reboiler resulting in lower CO2 capture rate. In addition, precipitation was observed and there were frequent foaming issues in the stripper packing which led to a poor stripper performance. Several measures were taken such as increasing the flue gas inlet temperature from 37 °C to 38 °C, to be within the precipitation free zone, or even flushing the absorber sometimes to remove precipitation, and addition of antifoam to reverse the foaming in the stripper. Since the initial results of phase B tests were not satisfactory and the variation in the SRD values was small ranging from 4.0 to 4.3 GJ/ton CO2, phase B repeat tests were carried out including two new tests B6* and B7*. B1 in Figure 2 has a low SRD but the test was at only 85% capture rate. When considering B1 (repeat), B2 (repeat), B4 (repeat), B5 (repeat), B6* and B7* tests, the SRD values were in the range 3.8 – 4.2 GJ/ton CO2. The minimum energy penalty achieved during phase B repeat was
3.8 GJ/ton CO2 at 113,300 kg/h lean solvent circulation rate and at L/G ratio around 2.4 kg/Sm3 during B7* test. This test series has also two more test points confirming that SRD below 4 GJ/ton CO2 is achievable utilising 12 m absorber packing.
2.4 Comparison of absorber packing height
Using results from phase A and phase B, the effect of packing height on energy performance when operating with SMR type flue gas (10 vol% dry CO2) can be assessed as shown in Figure 3. Reducing the packing height from 18 to 12 m gives an increase in SRD when comparing the optimum test points, i.e. from 18 m series A5 with an SRD 3.2 GJ/ton CO2 to the 12 m series B7* with an SRD 3.8 GJ/ton CO2. There is also a corresponding increase in the optimum L/G ratio from 1.9 to 2.4 kg/Sm3. First of all, this illustrates that selecting a more compact absorber that can reduce CAPEX will have a consequence on the OPEX through increased heat requirement for the CO2 stripper as well as increased pumping power for solvent circulation. Thus, a shorter absorption column may be beneficial for installations with limited space available or if low-cost thermal energy is available.
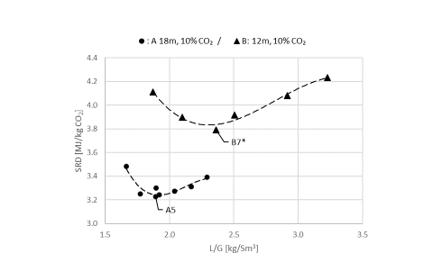
- Results from flue gas with 15 vol% CO2
2.5Results from flue gas with 15 vol% CO2
During phase C the CO2 level in the flue gas into the absorber was increased to 15 vol% (dry) and in order to be within the design of the stripper, the flue gas flow is decreased to 34,000 Sm3/h. SRD plotted against L/G ratio for tests from phase C at 18 m packing height and 90% capture rate is shown in Figure 4. The SRD values were in the range 3.2- 3.5 GJ/ton CO2. The minimum energy penalty achieved during phase C was 3.2 GJ/ton CO2 at 98,400 kg/h lean solvent circulation rate and at L/G ratio around 2.9 kg/Sm3 during C7 test. The SRD level is similar to test A5 above, however, lower L/G ratios were not explored due to time constraints so the optimal case could be even further to the left of the lowest SRD value achieved from C7 test.
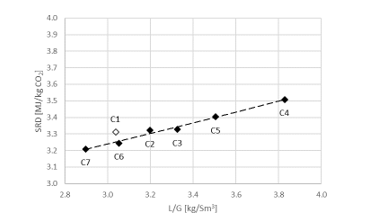
3. Operational experience
3.1 Precipitation in the lower absorber packing and mitigating actions
According to TCM’s laboratory tests prior to ALIGN-CCUS campaign, CESAR1 solvent should not precipitate at planned absorber operation conditions [4]. However, at TCM precipitation has turned out to be a reoccurring issue with the CESAR1 solvent. The TCM absorber design is with rectangular cross-section and both temperature and concentrations may vary and create local conditions for CESAR1 to precipitate. Already during the ALIGN-CCUS campaign TCM gained knowledge under which conditions precipitation can occur, how to handle and dissolve precipitates.
Precipitation was most easily detected by increase in the pressure drop in the lower absorber packing. If larger amounts of solvent precipitate, it can also be noticed by significant decrease in the solvent concentration. At stable operation, without precipitation, the lower packing pressure drop is stable (+/- 0.1 mbar), and variations are mainly caused by changes in lean solvent or flue gas flow rates.
With precipitation two pressure drop profiles in absorber lower bed are observed:
- Continuous fast increase of the pressure drop (100% increase in few hours).
- Unstable and increasing or decreasing pressure drop (+/- 1 to 2 mbar) at stable absorber operation or with slight variations of operation parameters.
During normal operation without precipitation, the four temperature sensors at the same elevation at the bottom of the lower absorber packing usually indicate a deviation of +/- 5 °C, and the temperature close to the absorber wall is higher than the other locations (unless no reaction is occurring). This deviation is most likely caused by higher local CO2 loading and may indicate a poor distribution close to the walls in normal operation.
With precipitation the temperature sensors often indicate similar temperatures (+/- 1 °C in some cases). However, with high precipitation (pressure drop profile 1), flooding may occur on the whole packing area, causing a uniform temperature of the packing. Significant modification of the operation parameters or absorber flushing is required in order to control the pressure drop. In case of pressure drop profiles 2, an increase or decrease of the pressure drop is also observed at several tests at almost identical parameters, despite of better conditions for avoiding precipitation. This is likely caused by the local accumulation of precipitation close to the wall as the concrete absorber walls are not insulated and poor gas distribution is expected at the corners and walls.
During the start of phase A at 18 m absorber packing height, 10 vol% (dry) CO2 concentration and 90% CO2 capture rate, there was a slight increase in the differential pressure in the lower absorber bed which indicated that precipitation might be occurring. This was dealt with by increasing the flue gas inlet temperature from 35 °C to 37 °C in attempt to avoid precipitation. Although a higher flue gas inlet temperature negatively impact the steam consumption, it was prioritized to run tests at higher temperatures in order to avoid precipitation. However, towards the end of phase A tests and despite the increased temperature, the pressure drop across the lower absorber packing was increased drastically from 7 to 14 mbar indicating a significant precipitation event. An absorber flushing was required to dissolve the precipitate. This was carried out by turning off the flue gas feed blower and increasing both the lean solvent flow rate and temperature. As a result of the flush test, the differential pressure in the lower absorber bed was reduced to 7 mbar indicating that the precipitate had been cleared. The measured and the calculated pressure drop during phase A testing are shown in Figure 5 (a).
During phase C tests at 18 m packing height, 15 vol% CO2 (dry) in the flue gas and 90% CO2 capture rate, the increasing differential pressure in the lower absorber packing was a recurring issue even if maintaining a high flue gas temperature of 40 °C. Therefore, two tests were dedicated to investigating further the differential pressure rise, see Figure 5 (b). The first test was run to provoke the differential pressure to be increased. During this test, the pressure drop increased from 4 mbar to 7 mbar. In the second test the water which is usually dumped to the absorber sump from the lower water wash was led to the 3rd water wash (the unused upper absorber bed) instead to see if this could affect positively on the differential pressure in the lower absorber bed (i.e. by contributing to diluting and flushing). However, the effect on the pressure drop was limited, and the differential pressure stabilized at 5.9 mbar as shown in Figure 5 (b).
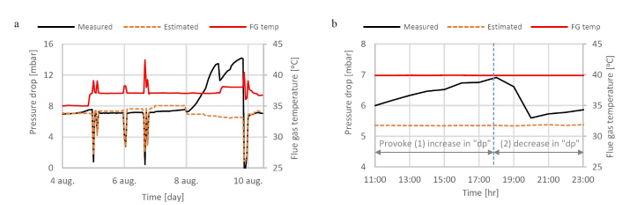
3.2 Foaming evidence in the RFCC stripper during tests mimicking SMR flue gas
Analyses of the stripper temperature profiles at TCM revealed that CESAR1 solvent tends to foam, and this depends on several factors that may vary in the plant operation. At times stripper profiles show that foaming may start some hours after plant start-up, even with a fresh solvent and may be increased or decreased. Operation parameters that are suspected to cause and/or influence the formation of foam are mostly not predictable or repeatable. Among these, the high stripper temperature and consequently high evaporation rate of solvent at the bottom of the stripper packing. Other potential reasons for formation of foam could be impurities in flue gas, solvent properties, particles of solids and corrosion, and design of stripper column internals.
The main consequence of foaming observed is unstable stripper operation. Hence, foaming leads to decreased stripper efficiency and thereby not allowing to achieve optimal test conditions. As foaming has a direct impact on the regenerator performance, more steam will be needed to regenerate the solvent and achieve the target CO2 capture rate. Hence, the specific reboiler duty SRD values can increase by 0.1 GJ/ton CO2 up to 0.25 GJ/ton CO2 in the worst cases of foaming.
Foaming in the RFCC stripper was an intermittent issue throughout the test program particularly during original phase B tests at 12 m absorber packing height (see section 2.3). As the results from these tests were not promising due to several periods of high foaming or flow maldistribution, phase B tests were repeated to reverse the foaming issue by injecting a small amount of antifoam. Although foaming during phase B repeat and phase C was limited, a 2 liter of antifoam addition was able to remove the strong foaming tendency and led to lower steam requirements in the stripper reboiler and consequently lower energy numbers (SRD). However, the duration of antifoam effect is variable and could be limited to only a few hours.
Based on literature [10] excessive antifoam dosing is not recommended as its function can be reversed and be a foam promoter. Future CESAR1 tests at TCM may confirm the minimum injection rate and if lower injection rates at short intervals reduce the risk of excessive antifoam dosing. It is also recommended to minimize risks of local high gas flow or liquid flow in the stripper packing by ensuring a suitable vapor flow distribution from the stripper reboiler to the stripper packing.
Future CESAR1 tests might also consider testing the solvent at relevant temperature, pressure and packing with representative flue gas to be able to confirm the eventual impact of specific decomposition products to foaming. If foaming is caused by impurities or degradation products, then it could be possible that activated carbon bed operation and/or thermal reclaimer unit can help to reduce foaming tendency.
Conclusion
The three test series (phase A, B and C) discussed above with CESAR1 solvent showed interesting results for 90% CO2 capture from flue gases with comparable levels of CO2 to that of a SMR furnace. At 10 vol% (dry) CO2 the minimum SRD was found to be 3.2 GJ/ton CO2 when utilizing 18 m absorber packing. For the same flue gas conditions
but with absorber packing height reduced to 12 m, the minimum SRD became 3.8 GJ/ton CO2. This test series has two more test points confirming that SRD below 4 GJ/ton CO2 is achievable with only 12 m absorber packing. The 18 and 12 m cases with 10 vol% CO2 illustrate the consequence of utilizing a more compact absorber that reduces capex at the expense of increased heat requirement for the CO2 stripper. The third test series was operated at 18 m absorber packing with CO2 in flue gas increased to 15 vol% CO2 (dry). Similar SRD level as the corresponding 10 vol% CO2 case was found. However, the minimum SRD was likely not demonstrated since the point where SRD stops decreasing when decreasing L/G had not been reached.
During the test program there was precipitation in the lower absorber packing in spite of that the conditions in the absorber should not be favorable for this to occur. Precipitation was mitigated by increasing the flue gas inlet temperature and flushing of the absorber was also required. The cause may be related to the absorber design and local zones with poor gas distribution at lower temperature close to the absorber walls as well as corners. Foaming was observed in the stripper and introduced unstable stripper performance and less efficient stripping. Injection of anti- foam reduced the foaming tendency, but the effect was temporary. Better understanding of the onset of precipitation and foaming should be included in future CESAR1 tests at TCM.
The basis for this investigation is Equinor’s SMR unit at Tjeldbergodden methanol plant which is the largest methanol plant in Europe. The test campaign provides value to the industry as it helps to reduce both technical and financial uncertainty associated with CO2 capture. The campaign results give an indication on what SRD values one might expect when operating a CO2 capture plant.
Acknowledgments
The authors gratefully acknowledge the staff of TCM DA, Gassnova, Equinor, Shell and TotalEnergies for their contribution and work at the TCM DA facility. The authors also gratefully acknowledge Gassnova, Equinor, Shell, and TotalEnergies as the owners of TCM DA for their financial support and contributions.
References
- Further Assessment of Emerging CO2 Capture Technologies for the Power Sector and their Potential to Reduce Costs: IEAGHG Technical Report, 09. 2019.
- G. Wiechers, P. Moser, C. Benquet, J. Gibbons, J. Monteiro, A. Hartono, K-. A. Solli, H. Knuutila, Guidelines for effective solvent management, Deliverable Nr. D1.2.6, ALIGN-CCUS.
- Accelerating Low carbon Industrial Growth through CCUS: ALIGN-CCUS, project homepage https://www.alignccus.eu/, website accessed: 15.11.2021.
- C. Benquet, A. Knarvik, E. Gjernes, O. A. Hvidsten, E. R. Kleppe, S. Akhter, First Process Results and Operational Experience with CESAR1 Solvent at TCM with High Capture Rates (ALIGN-CCUS Project), 15th International Conference on Greenhouse Gas Control Technologies,GHGT-15, 15th-18th March 2021 Abu Dhabi, UAE. http://dx.doi.org/10.2139/ssrn.3814712
- M.Campbell, S. Akhter, A. Knarvik, M. Zeeshan, A. Wakaa, CESAR1 solvent degradation and thermal reclaiming results from TCM testing. To be presented at the GHGT-16 Conference: 23 – 27 October 2022, Lyon, France.
- Equinor onshore facilities, Tjeldbergodden industrial facility, https://www.equinor.com/energy/onshore-facilities, website accessed: 26.08.2022.
- E. Gjernes, S. Pedersen, T. Cents, G. Watson, B.F. Fostås, M.I. Shah, G. Lombardo, C. Desvignes, N.E. Flø, A.K. Morken, T. de Cazenove,L. Faramarzi, E.S. Hamborg, Results from 30 wt% MEA performance testing at the CO2 Technology Centre Mongstad, Energy Procedia, 114, 2017, 1146-1157, https://doi.org/10.1016/j.egypro.2017.03.1276
- M.I. Shah, G. Lombardo, B.F. Fostås, C. Benquet, A.K. Morken, T. de Cazenove, CO2 Capture from RFCC Flue Gas with 30w% MEA at Technology Centre Mongstad, Process Optimization and Performance Comparison, 14th Greenhouse Gas Control Technologies Conference Melbourne 21-26 October 2018 (GHGT-14), https://ssrn.com/abstract=3366149
- M.I. Shah, E. Silva, E. Gjernes, K.I. Åsen, Cost Reduction Study for MEA based CCGT Post-Combustion CO2 Capture at Technology Center Mongstad. Proceedings of the 15th Greenhouse Gas Control Technologies Conference 15-18 March 2021, Abu Dhabi, UAE. http://dx.doi.org/10.2139/ssrn.3821061
- [10]A.M. Al-Dhafeeri, H.A. Nasr-El-Din, Characteristics of high-permeability zones using core analysis, and production logging data. J Pet Sci Eng – J PET SCI Eng 2007;55:18–36. https://doi.org/10.1016/j.petrol.2006.04.019.
Critical Knowledge for CO2 - Intensive Industries to Implement Amine-Based Carbon Capture (2021)
Stefania Osk Gardarsdottir1, Leila Faramarzi2,3, Kristin Jordal1,Matthew Campbell2
1SINTEF Energy AS, PO Box 4761 Torgarden, 7465 Trondheim, Norway 2Technology Centre Mongstad, 5954 Mongstad, Norway 3Vallourec, 27, Avenue du Général Leclerc, 92100 Boulogne Billancourt
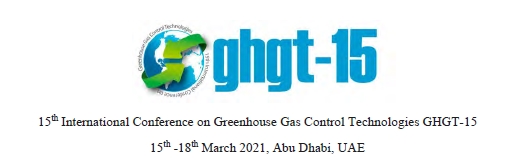
Abstract
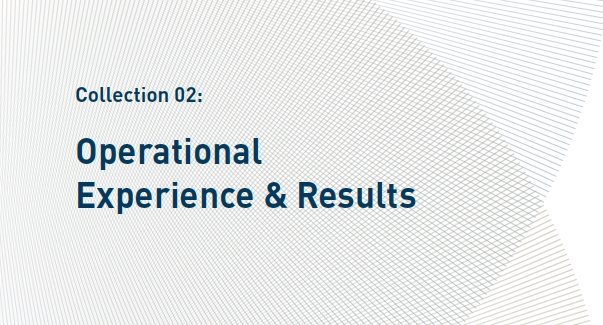
This paper has been written to provide some decarbonization guidelines and recommendations for different CO2 intensive industrial applications, such as, Cement, Oil Refineries, Waste to Energy, Steel, H2 Production, Aluminum and Pulp & Paper. Relevant information has been provided for any potential project targeting a significant reduction in CO2 emissions. The importance of flue gas characterization has been indicated, including which typical components in the flue gas should be measured, which are important for properly planning and designing a CO2 capture project. Additionally, based on Technology Centre Mongstad (TCM) experience with both clean flue gas (CCGT) and more contaminated flue gas (RFCC), recommendations are given for the importance of good solvent hygiene and maintaining low amine emissions to the stack and surrounding environment. It is expected that each of the industrial applications described will lie somewhere between the CCGT and RFCC in terms of flue gas cleanliness. It has also been demonstrated that material integrity of a CO2 capture plant can be compromised if solvent hygiene is not maintained. Also, how the material integrity and selection can have considerable impact on CO2 capture plant cost and reliability of operation.
1. Introduction
The importance of CO2 abatement to curb global warming is becoming increasingly evident. In “A Clean Planet for All, the new European strategic vision for a prosperous, modern, competitive and climate-neutral economy”, it is stated that deployment of carbon capture and storage (CCS) is necessary for tackling CO2 emissions that cannot be cut through e.g. increasing energy efficiency and renewables [1].
CO2 capture and storage (CCS) is one way to cut CO2 emissions in carbon-intensive industries, which account for around a quarter of global direct CO2 emissions [2]. For some industry sub-sectors, as in the case of e.g. cement production, CCS is the only option to realize deep emission cuts [3]. CO2 capture with amines is the most mature technology and is already deployed at scale e.g., at Boundary Dam (Coal-fired power plant, Canada). Furthermore, capture with amines is currently progressing towards realization at industrial scale in several emerging European CCUS (carbon capture, utilization, and storage) projects e.g., AVR Waste to Energy, Heidelberg Materials Heidelberg Cement, and Fortum Oslo Varme Waste to Energy.
It is important that these and other initial industrial-scale capture projects are implemented in a successful manner, to create positive momentum and lay a foundation for additional successful projects, which is key for deploying full
Electronic copy available here.
CCUS value chains. The “learning and experience” effect from the early projects will help to optimize and de-risk operations of the forthcoming ones. And like other chemical industries, building up experience together with continued R&D will result in project cost improvements. Also, with accumulation of operational experience in capturing smaller volumes of CO2 (a strategy followed by several emission sources across Europe), it will become possible to increase captured CO2 volumes.
There are various technology suppliers in the market, offering amine technologies to CO2-intensive industries with limited commercial experience in the field of CO2 capture. The CO2-intensive industries must be enabled to make an informed choice of a technology that suits their specific application. Such industries must also be aware how the operation of an installed amine plant can affect the overall OPEX and environmental footprint of their entire production.
Against this background, the aim of the present paper is to summarize the experience from Technology Centre Mongstad (TCM) and SINTEF regarding 1) CO2 capture integration into CO2-intensive industries; 2) Importance of proper flue gas characterization; 3) Solvent hygiene, material integrity and cost; 4) Emissions from amine plants.
2. Requirements for Integration of CO2 capture in energy-intensive industry
Considering industry sub-sectors, steel, cement, and petrochemicals (e.g., oil refineries and H2 production) account for about 70% of direct industrial CO2 emissions. Examples of key characteristics relevant for amine-based CO2 capture for these industries as well as several other important industry sub-sectors are listed in Table 1.
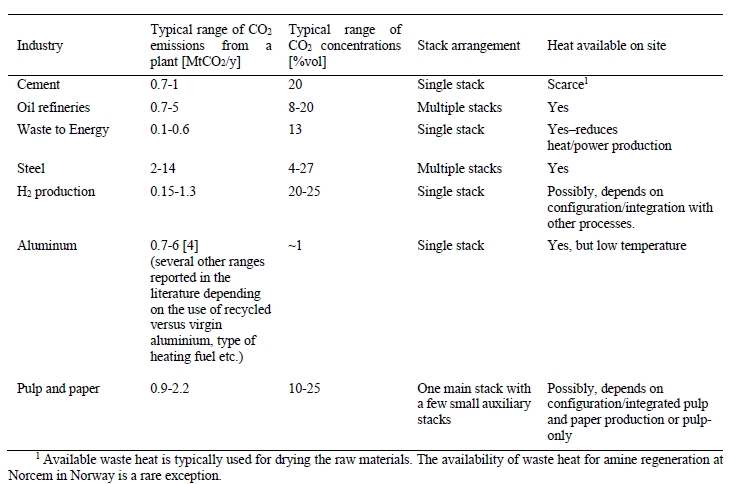
Table 1. Overview of characteristics of key energy-intensive industries relevant for CO2 capture.
Amine-based CO2 absorption primarily requires energy in the form of heat, for stripping CO2 from the solvent, and electricity, to drive pumps and fans. The cost of heat, most often in the form of steam, is generally the largest cost factor of the CO2 absorption process. Therefore, any excess heat of sufficient quality available on the industry plant site can potentially improve the economics of the CO2 absorption process considerably. For use of available excess heat, in addition to having sufficient quality, the properties of the heat-carrying fluid will be pivotal and will affect the cost and space required for heat exchangers.
Furthermore, for near-and medium-term deployment of CCS, retrofittable CO2 capture options are essential for brownfield industrial installations. In the CEMCAP project [4] several factors were defined to analyze retrofitting cement facilities with CO2 capture; Furthermore, for near-and medium-term deployment of CCS, retrofittable CO2 capture options are essential for brownfield industrial installations. The implication that several of these factors can have on the plant economics has recently been discussed in the work of Roussanaly, Berghout [5];
2.1 Impact on production of the key product
For any energy-intensive industry, producing a high-quality product is the number one priority. It is therefore of highest importance that the integration of the CO2 capture process does not impact the product quality and overall operability of the industrial plant. This could be a challenge for CO2 capture technologies requiring deep integration with the industry plant’s core processes. For end-of-pipe technologies, such as amine CO2 absorption, this is generally not considered a challenge for neither retrofit nor greenfield applications.
2.2 Equipment and footprint
Space requirement of CO2 capture equipment can be a significant challenge for industrial sites, especially brownfield industrial sites which have not been designed to accommodate CO2 capture equipment with a significant footprint. Thus, modifications to the existing plant or compromises in design, resulting in sub-optimal layout of the capture process, e.g., replacing existing process units, re-routing flue-gas streams or placing parts of the CO2 capture process in different locations, might be required. Constraints for available space are inherently case-specific, although some industry sub-sectors such as oil refineries often have spatial constraints around the stacks. In the case of CO2 absorption, the process offers some flexibility with respect to process layout and in locating different parts of the process in different places, as illustrated by Roussanaly, Berghout [6]. This could e.g., mean locating the absorber section close to the flue gas source, while placing the CO2 regeneration (stripper section) and CO2 conditioning (compression or liquefaction) further away from the flue gas source.
2.3 Utilities and services
Considerations must be made for any additional utilities and services required for operating the CO2 capture process, including additional electric power, steam or fuel to power steam boilers and chemicals. Both electricity and heat/fuel considerations are highly relevant for CO2 absorption systems. For industrial applications, additional electricity demand can be a challenge for the local electric grid capacity. Also, if no steam is available on site, a dedicated steam boiler is required to operate a capture process. If no or insufficient waste heat is available for steam generation on site, new fuel handling systems might have to be installed or the capacity of existing systems expanded.
2.4 Introduction of new chemicals/subsystems
In many cases, including amine absorption, installing a CO2 capture system will introduce handling of new chemicals or subsystems at the industrial plant. Consequently, new routines and procedures with respect to operation and safety will have to be implemented and new permits might have to be acquired from the local authorities with respect to possible emissions to air and water. For amine-based CO2 absorption, handling of the amine solvent itself and its degradation products will in most cases be a new procedure to the industrial plant. Thus, careful considerations must be made and a close dialogue to be kept with the appropriate authorities for permitting and monitoring purposes. Over-the-fence solutions for steam supply and/or amine capture operation may be a solution for some industrial sites, in which case the CO2-intensive industry should aim to be an informed procurer of such solutions.
2.5 Available operational experience
Technology maturity and consequently, available operational experience, is an important factor when it comes to limiting both technical and economic risks. Previous experiences from the same industry segment as well as from other applications should be considered in any technology assessments, whether for retrofit or greenfield applications. However, care must be taken when considering technology maturity and lessons learned from one sector to the other, and perhaps especially from power sector applications to energy-intensive industries as considerations regarding e.g., operability and product quality are industry- and site-specific, and impurities in flue gases are likely to differ between industrial segments.
3. Importance of flue gas characterization for different industries
TCM has considerable experience testing flue gases from two different sources: (1) CCGT flue gas & (2) RFCC flue gas [12]. The CCGT flue gas is the clean flue gas with signficantly lesser amounts of contaminants. Whereas the RFCC has signficantly higher impurities and is considered a more contaminated flue gas. It is believed that the TCM learnings from both gas streams can be extremely relevant for the array of different industry applications which are looking into CO2 capture, as presented in Table 1 above. A simplistic perspective can be that TCM has operational experience which covers a wide range of flue gas compositions, where most industrial applications will fall somewhere within this range. This section will provide an overview of the important flue gas components which should be determined for any potential CO2 capture project. It is recommended for the project owner to provide accurate information to the CCS technology suppliers who are considered for a given project.
For any CO2 capture project one of the most important aspects to understand is the composition of the flue gas that is targeted for CO2 capture. There can exist a wide range of compositional variation in flue gases from different applications that can strongly impact the design effectiveness for a CO2 capture plant. Therefore, it is recommended for the project and host site to adequately characterize the proposed flue gas stream(s). This section provides a list of important components which should be measured for any CO2 capture project. If further details are needed TCM can support with more extensive details. The recommendations provided below are most relevant for solvent-oriented technologies. If other CO2 capture technologies are considered, such as membranes some components may have different levels of importance.
- CO2 – Carbon Dioxide
It is possible that the CO2 concentration in flue gas can vary signficantly, therefore, to allow for an adequate capture plant design an accurate CO2 measurement will be needed. Typically, the capture plant should be designed for a target steady state capture rate (i.e., 90 % or 95 %) and the design capture rate should consider the expected minimum and maximum CO2 concentrations within the flue gas. - O2 – Oxygen
The concentration of O2 is also important as it can impact amine solvent degradation [10]. It is a component which should be measured for any flue gas streams which require decarbonization. When calculating the amine loss rate through degradation the maximum level of O2 in the flue gas should be considered. - SO2 – Sulfur dioxide
All SO2 entering the absorption column will be captured by the amine solvent, this will form amine sulfate and amine sulphite salts. The formation of these salts will gradually reduce the solvent scrubbing capacity for carbon dioxide and will require amine purification. Therefore, accurate measurements of SO2 in the ppmv range should be performed. - NO and NO2 – Nitric oxide & Nitrogen dioxide
For CO2 capture processes it is very important to measure the NO2 concentration in the flue gas entering the absorber since NO2 will react with secondary amines to form nitrosamines. It should be mentioned that primary and tertiary amines can degrade into secondary amines which can also lead to nitrosamine formation. A measurement on NO should also be made but this will have a signficantly lesser impact on CO2 capture performance as typically all NO will slip through the absorber. - SO3 – Sulfur trioxide
The measurement of SO3 entering the absorber can be a good indication of total acid mist. This is important for CO2 capture design as flue gases with high acid mist will lead to high aerosol concentrations, which will translate into potentially high amine emissions carried out of the absorber as aerosols. - Fly ash
The composition, concentration, and size of fly ash in the flue gas is important when designing a CO2 capture plant. It is important to measure fly ash, catalyst, and non-soluble salts. These particles can promote higher amine emissions. Also, it is possible that fly ash metals can dissolve in the CO2 capture solvent which can lead to degradation and higher amine losses. - Total Particulates
Total particulates can be considered as the combination of particles, this can include both H2SO4 aerosols and fly ash depending on size distributions. Understanding total particulates concentration is important to determine the likelihood of exceedingly high amine emissions. - HCl – HF and other acidic components
Acid components can gradually accumulate in the solvent and reduce overall scrubbing efficiency for CO2 capture (i.e., acting like SO2). However, special attention is required for strong acids such as HCL and HF as the concentration of these components can signficantly affect material selection philosophy and the resulting capture plant capital expenditures. - NH3 – Ammonia
It is important to understand the concentration entering absorber, as many amine processes will yield an additional formation of ammonia, through amine degradation. Also, there typically exists an emission permit for ammonia and therefore concentration entering the absorber should be measured. - CO – Carbon Monoxide
The presence of CO can lead to formic acid and formate production which can increase amine degradation. - Heavy Metals
Heavy metals in the flue gas will accumulate and result in increased heavy metal concentration in the solvent.
Iron is one of the heavy metals which can lead to and catalyse higher solvent degradation. - H2O
Water is interesting for summing up all components and for converting between wet and dry basis. Also, for knowing the dew point at battery limit which is important for design and material selection of ducts.
With reference to SOX, NOX and dust – environmental legislation provides limits, thus an interesting point when evaluating capture technologies is to what extent various technologies need additional polishing of these components. This is of interest for those developing robust capture technologies.
4. Solvent hygiene, material integrity, plant corrosion and cost of CO2 capture
Various economic models are used to estimate the cost of full CCS value chains. Often the overall cost of the chain is expressed as cost of carbon ($/tCO2) which may refer to the CO2 avoided, captured or abated [6]. As industrial experience in CCS grows, it is expected that traditional costing method used in chemical industry which includes estimation of capital and operating costs will be more widely used. The accuracy of the traditional method will increase with the growth of CCS cost database and availability of reference cases.
Various parameters will affect the cost of CCS including fuel prices, capital cost and cost of compliance with regulatory requirements like monitoring the CO2 storage sites. However, though there are significant uncertainties in available methods, the consensus is that for most large emission sources, cost of capturing CO2 is the largest component of the CCS cost.
Most capture cost studies are based on the current commercially viable technology i.e., the amine process. Often a substantial portion of the overall operational cost of capture is attributed to the energy requirements for capture and then compression of the CO2 to the pressure required by the transportation infrastructure. However, energy requirement for the capture process is largely dependent on site-specific circumstances such as availability of waste heat [7]. Also, CO2 concentration and pressure of the flue gas play central roles in cost of capture. Industrial processes emit flue gases that are very diverse in pressure and CO2 content. Where a relatively pure flue gas is available (e.g., ammonia and fertilizer production, natural gas processing) the cost of capture can be significantly lower than capture from fossil-based power production [8].
However, present cost studies have not sufficiently addressed the operational costs due to loss of amine carried with the depleted flue gas, amine degradation in the liquid phase and damages to the plant integrity due to fouling, corrosion and consequently equipment failure. TCM has observed a strong connection between maintaining the solvent hygiene and a) reducing the need to make-up or replace the solvent, b) minimizing amine emissions and c) avoiding corrosion in the capture plant. Most of the results were presented previously [9,10]. In the following sections, it is discussed how lack of amine hygiene can lead to severe increase of operational cost and endanger the integrity of the capture facility due to corrosion.
It has also been observed that very little has been done to research and develop materials that are potentially cheaper than stainless steel (used in construction of the few existing capture plants) but also resistant to corrosive conditions of CO2 capture. Hence, the operational conditions that must be considered in developing metal grades or innovative non-metallic materials are presented.
4.1 Amine systems in carbon capture versus amine processes in oil and gas industry
Amine processes have a long history in oil and gas applications with a wealth of accumulated experience in material selection. Often analogies are made between amine processes in natural gas processing and CO2 capture from industrial flue gases. Yet, capture processes present specific aspects that must be considered in material performance and selection.
Flue gases from combustion processes often contain high oxygen concentrations. The flue gases from TCM contain 3-8 % (RFCC) and up to 14 % (CCGT) oxygen. Oxygen not only corrodes metals through oxidative corrosion but can degrade amines through oxidative degradation mechanisms. Degraded amines can be a cocktail of non-volatile organic compounds, heat-stable salts and sometimes suspended solids. Degradation products can in turn increase the corrosivity of the aqueous amine solution. High levels of oxygen and presence of impurities can have detrimental effects on the metallurgy of the amine plants for CO2 capture. Corrosion can be more severe at locations where CO2 is flashed from rich amine streams and where temperature and flow turbulence are significant. An example is the stripper reboiler where usually pitting and grooving corrosion occurs. TCM experienced this first-hand when one of the two reboilers at the amine plant i.e., CCGT (CHP) reboiler got severely corroded and had to be replaced.
In commercial scale CO2 capture plants, such equipment failure must be prevented by stringent solvent management regimes and close monitoring of metal content in the amine solvents. Solvent analysis for degradation products and metal contents is costly but it should not be skipped. The consequence of undermining solvent hygiene is not only deterioration of capture performance but irreversible damages to the plant integrity and increased costs.
4.2 Corrosion Incident at TCM
In 2017, TCM experienced severe corrosion in the CCGT (CHP) stripper reboiler shortly after starting a new monoethanolamine campaign named MEA-3. Before this test campaign, no signficantly signs of corrosion were observed in the process equipment since the amine facility was inaugurated in May 2012.
MEA-3 commenced on 9th of June 2017. The amine plant was thoroughly washed and flushed before the campaign started. At TCM, the metal content in amine solvents is analysed and monitored on a weekly basis (a minimum of once a week). During MEA-3, the first unusual increase of metals in the solvent was observed on 6th of July when the total metal content (Fe, Ni, Cr, Mo) reached 59 mg/kg, whereas the previous analysis on July 3rd only showed a total of 1.1 mg/kg metals. It is important to note that in only three days there was a sharp increase in dissolved metals, signifying the rapid development of metal dissolution. Such large number of dissolved metals was unprecedented at TCM. In the MEA-2 campaign in 2015, the maximum total metal concentration was 25 mg/kg (Mo was not even detected) and it happened at the end of the campaign after 77 days of continuous operations [11].
The detailed solvent analysis including degradation products, heat stable salts and metals along with process conditions for MEA-3 were presented previously [9,10]. The typical range of temperatures and flow velocities at the TCM amine plant are presented in Table 2. This is a low-pressure process where across the plant, pressure is about 1- 2 barg.
Parameter | Hot lean solvent | Hot rich solvent | Cold lean solvent | Cold rich solvent | Stripper overhead vapor |
Normal operating temperature [°C] | 120 | 110-115 | 30-55 | 35-50 | 90-100 |
Max operating temperature [°C] | 123 | 118 | 72 | 70 | 117 |
Phase | Liquid* | Liquid** | Liquid | Liquid | Vapor*** |
Flow rate [ton/h] | 30-220 | 35-235 | 30-220 | 35-235 | 2.5-10 |
Pipe size [inch] | 8 | 6 | 8 | 6 | 12 |
Pipe flow velocity [m/s] | 0.3-1.9 | 0.5-3.6 | 0.3-1.9 | 0.5-3.6 | 4-18 |
Table 2. Typical range of temperatures and flow velocities at the TCM amine plant.
*The hot lean solvent might contain entrained bubbles from the desorption process.
** The hot rich solvent might flash in the lean/rich cross heat exchanger (two-phase flow is possible).
*** The stripper overhead vapor is at dewpoint and might contain droplets of condensed water.
4.3 The cause of corrosion incident
Given the vulnerability of MEA to oxidative degradation, potassium bisulfite (at 32 wt% aqueous solution strength) was used as an oxygen scavenger in the initial phase of MEA-3. The rate of injection was adjusted to keep a reasonable buffer of the scavenging agent (SO 2-) in the inventory i.e., 500-1000 mg/kg. The injection rate was kept at approximately 11 L/min.
On 6th to 7th July 2017, the solvent was reclaimed. The main purpose of reclaiming was to remove the large amount of sulfate accumulated in the amine at the time as the result of potassium bisulfite injection. At this point in time, the total sulfate/sulfite concentration was approximately 5 wt% i.e., very large salt concentration in the plant inventory. However, surprisingly the plant performance was intact until this point and hence normal operations were continued to observe the process performance as concentration of heat-stable salts increased in the solution. TCM advises against running the capture process at high heat-stable salt concentration. However, these tests created the opportunity to observe the adverse impact of accumulation of contaminants at a large-scale amine plant. The first alarming sign (observed on July 5th) was sudden salt precipitation in the cold lean solvent line including valves and sampling lines.
Operating with the MEA solvent was continued until first of July 2018. However, in this paper only the early period is discussed, where rapid changes in the plant situation led to detection of a leak in the CCGT (CHP) reboiler. Figure 1 is the graphic representation of this period. During this time, the plant was mostly run on CCGT flue gas containing 4% of CO2 except for the period shown in green where CO2 % was between 8% to 13%.
The analysis of 10th of July after the solvent was reclaimed showed 31 mg/kg of metals in the aqueous amine, suggesting that there was a reduction in metal concentration after reclaiming, as some metals are taken out of the amine circuit through reclaimer bottom sludge. One key learning of MEA-3 was to take samples before ending the reclaiming process to ensure that metal concentrations are reduced to the lowest achievable level. As a rule of thumb TCM advices removal of all metals down to detection limit. Failing to do so means that the remaining dissolved metals will potentially catalyse solvent degradation and thus corrosion mechanisms.

4.4 The Inspection
The entire amine plant was emptied, cleaned, and inspected just after the leak was detected but here, the focus is on the inspection of the leaking reboiler. After initial inhouse inspections at TCM’s mechanic workshop, the reboiler was sent to its supplier for further investigations. The CCGT (CHP) reboiler was a shell welded plate type heat exchanger. The schematics of the design is shown in Figure 2. The entire reboiler was made of 316 stainless-steel material.
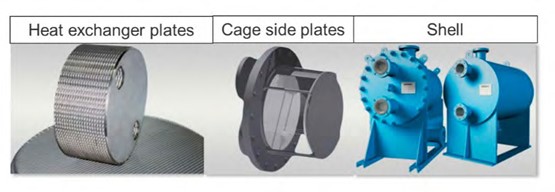
One leaking hole in the plates was leaking from the amine side. The welded plate stack where the leaking section was identified was cut. Figure 3 shows a significant layer of corrosion product deposits on the amine side of the plates. The leakage point was studied in more detail, and it was found that the defect formed on amine side was likely to be caused by flow induced corrosion/erosion.
On the shell-side (Figure 4) deposits were observed within flow lines, and a pattern implying that the flow has not been uniform, indicating that some of the plates were plugged. Also, corrosion products were mainly observed on amine outlet (bottom part of Figure 4), whereas the inlet spool was relatively clean.
Cage-side plates were also inspected. Here, flow pattern corresponding to the pattern observed on the shell was found. Also, one of the plates suffered from substantial plastic deformation as shown in Figure 5. This deformation indicated abnormally high localized pressure from the inside of the cage, which again fits with the theory that heat exchanger plates were partially plugged. Subsequently, analysis of the corroded plates was performed at Equinor’s material laboratory in Porsgrunn, Norway. The morphology of the plates showed that on average the thickness was reduced by 200-250 µm in most of the surface, indicating general corrosion/erosion.
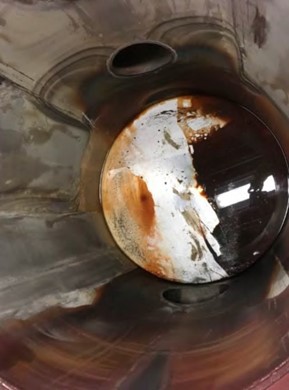
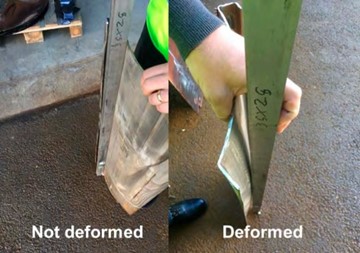
4.5 The Root Cause
Although various pathways were hypothesized as the cause for this severe corrosion incident, it was concluded that the most plausible pathway was the following:
Gaps between heat exchanger plates were partially filled with salts, solids, and precipitates. The amine flow was therefore restricted and maldistributed in the reboiler plates. Then, pressure increased locally inside the remaining passage causing plastic deformation of cage plates. Locally high wall shear stress in the remaining passage combined with presence of particles resulted in:
- Erosion of the oxide layer at surface of the 316L plates still exposed to amine
- Erosion and corrosion occurred to the 316L exposed plates (~ 200-250 µm corroded in average on the investigated plates)
- Erosion/corrosion was emphasized locally close to contact point between plates due to higher wall shear stress
- (At least) One leakage occurred due to this mechanism
Theoretically, austenitic stainless-steel type 316L is supposed to resist hot amines even in presence of bisulphites, sulphites, and sulphates. The reason is that it has a thin chrome oxide protective layer at its surface which protects it against corrosion. The corrosion protection of the material disappears if the chrome oxide layer is removed and if there is no oxygen to form it again. It was therefore assumed that the oxide layer was removed in presence of abrasive agents like particles. The use of oxygen scavenger prohibited any possible re-formation of the protective oxide layer. General corrosion then occurred on the 316L stainless steel plates.
4.6 Key Learnings
The TCM CHP reboiler failure due to corrosion demonstrates weakness of SS 316L for the (plate and frame) reboiler design at specific operational conditions when salt precipitation was observed in the plant. This does not necessarily indicate a general need for higher grade materials with more corrosion resistance for this equipment.
For the CHP reboiler, the amount of accumulated deposits over the years, was not known prior to the corrosion incident in 2017. However, the observations during subsequent plant inspections, showed that no or very limited corrosion had occurred on SS 316L test coupons localized close to the rebolier. The reboiler corrosion was therefore a very local phenomenon related to conditions that affected the reboiler plates only, which is supported by no other signs of corrosion detected on surrounding equipment or on the inlet/outlet pipelines.
TCM could not conclude if a more corrosion-resistant material exposed to the given conditions would stand the same conditions. But the overall conclusion was that failure would most likely avoided by maintaining the heat-stable salts concentration below the recommended level of 1.5 weight % reported by TCM elsewhere [10].
Reclaiming (amine purification) processes must be used to remove heat-stable salts, degradation products and dissolved metals; in short to maintain amine hygiene. Stringent solvent management (hygiene preservation) results in smooth operations, reduced amine loss and replacement, reduced heat exchanger fouling, reduced amine unit operating costs, fewer shutdowns and hence increased chance of meeting emission reduction targets.
5. Overview of emissions and environmental impact for different industries
At Technology Centre Mongstad (TCM) amine emission monitoring and abatement are of utmost importance. The aim is to ensure that the established TCM emission permit is respected and to develop learnings and a knowledge base which can be applied to commercial scale CCS projects. TCM is regulated under an emission permit from the Norwegian environmental authority (Miljødirektoratet). The emission permit regulates the amine plant’s emissions to air for ammonia (NH3), Amines (primary, secondary and tertiary) and aldehydes. Table 3 below shows the allowable emission limits applicable from the TCM amine plant.
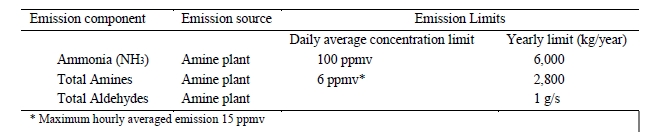
Table 3. TCM Amine plant applicable emission permit.
It is required that all amine solvents tested at TCM comply with the above emission permit, this is the case for open-source solvents, such as MEA and CESAR-1, but also for proprietary solvents. For each amine solvent tested at TCM, a rigorous assessment was needed to confirm safe levels of amine and amine degradation product emissions. The investigation included calculations for expected emissions from stack and appropriate atmospheric chemistry and dispersion modelling to ensure low impact on environment and immediate surroundings. The emission permit applicable for TCM amine plant is to allow TCM to tests different process parameters and process configuration, therefore this information in the table should be used with care as for a commercial scale plant the amine emission could potentially be stricter in terms of concentration (ppmv) of amine to air. It should be noted that TCM has an expert division which is responsible for emission permitting, atmospheric chemistry and dispersion modelling. If further information is needed to help define permits for commercial projects, TCM can provide direct support.
The main flue gas contaminant which signficantly impacts amine emissions to the stack is the concentration of total aerosol in the flue gas entering the absorber. Table 4 summarizes the difference in aerosol concentration for clean flue gas (CCGT) versus contaminated flue gas (RFCC). Depending on the industry of interest it is likely that the total aerosol concentration will lie somewhere between these two extremes. As can be seen the unfiltered RFCC flue gas has 300 to 500 times more aerosols as compared to the CCGT flue gas.
Main parameters | Units | RFCC flue gas (unfiltered) | CCGT flue gas (unfiltered) |
Number concentration | Part./cm3 | 15,000,000 – 25,000,000 | ~50,000 |
Size distribution | mm | 0.01 to 10 | N/A |
Weight concentration | Mg/Sm3 | 1,000 to 5,000 | N/A |
Reference [12] |
Table 4. Aerosol concentration for TCM RFCC and CCGT flue gases.
After the above learning was made, TCM implemented an aerosol abatement option to ensure signficantly low levels of aerosols were entering the absorption column. The mitigation measure was a BDU (Brownian Demister Unit) installed upstream of the absorber column to ensure relatively clean flue gas enters the absorber. The amine emissions for RFCC flue gas test with the BDU filter are in the same order of magnitude of amine emission for the CCGT flue gas.
Table 5 summarizes the MEA emission results for testing on average at TCM for these two different flue gases. Notice the testing with RFCC flue gas (unfiltered) with no aerosol abatements was evaluated only for a short duration due to the high observed amine emission. As can be seen signficantly higher MEA emissions were observed for the RFCC (unfiltered) flue gas as compared to CCGT. It is likely that other contaminated flue gas sources can have similar impact of aerosols on amine emissions if no aerosol abatement is performed. After the above learning was made, TCM implemented an aerosol abatement option to ensure signficantly low levels of aerosols were entering the absorption column. The mitigation measure was a BDU (Brownian Demister Unit) installed upstream of the absorber column to ensure relatively clean flue gas enters the absorber. The amine emissions for RFCC flue gas test with the BDU filter are in the same order of magnitude of amine emission for the CCGT flue gas.
Flue gas | MEA emissions (ppmv) | References |
RFCC (unfiltered) | 20 to +100 | [13] |
CCGT (unfiltered) | 0 to 0.4 | [14] |
RFCC (with BDU filter) | 1 to 3 | [13] |
Table 5. MEA Emissions for TCM RFCC and CCGT flue gases.
In the design and planning phase for any CO2 capture project it will be necessary to understand the total aerosol concentration entering the absorption tower and to make sure appropriate aerosol abatement options are in place, otherwise emission permits will be breached. Also, it should be mentioned that standard water wash and acid wash section will not be effective in capturing amine emissions induced by aerosols. Different technology vendors may have different abatement options other than BDU, which is fine, however appropriate technology verifications should be made before implementing for full scale projects.
6. Conclusions
This paper provides information and recommendations that should be considered for any potential CO2 capture project. This includes projects developed for a wide range of CO2 intensive industrial applications, where typical data has been provided for inlet CO2 concentrations, CO2 emissions per year. Also, guidelines have been presented for the impact of CO2 capture on industrial production rates, plant layout, utilities and handling of amine-based solvents. Also, it has been shown how the impurities within a flue gas can signficantly impact amine-based solvent degradation/make-up and stack emissions. Several impurities were described and the two most impactful components NO2 and total particulates (aerosols) were highlighted. Experience and results have been shared for testing at TCM with clean flue gas (CCGT) and contaminated flue gas (RFCC). It can be concluded for any contaminated flue gas with a significant concentration of aerosols that proper gas cleaning/filtration will be needed, otherwise amine emissions would be too high, and regulators would not grant the necessary environmental permits. Lastly, an explanation has been given for the cause of a significant corrosion incident which has occurred at TCM during a Monoethanolamine (MEA) test campaign. A recommendation from this test campaign is to ensure solvent hygiene is of prime focus for any CO2 capture project. More specifically, to ensure a sufficient amine purification technology is available on site to maintain a sufficiently low steady state level of amine degradation products, salts and metals.
7. References
- European Commission, A Clean Planet for all – A European strategic long-term vision for a prosperous,modern, competitive and climate neutral economy. 2018: Brussels.
- IEA and CSI, Technology Roadmap – Low-Carbon Transition in the Cement Industry. Interntational Energy Agency (IEA) and Cement Sustainability Initiative (CSI). 2018
- Dietz, S., V. Jahn, and J. Noels, Carbon Performance Assessment of aluminium producers: note on methodology. 2019.
- Voldsund, M., et al., Comparison of Technologies for CO2 Capture from Cement Production—Part 1:Technical Evaluation. Energies, 2019. 12(3): p. 559.
- Roussanaly, S., et al., Towards improved cost evaluation of Carbon Capture and Storage from industry. Submitted to International Journal of Greenhouse Gas Control, 2020.
- S. Budinis, S. Krevor, N. Mac Dowellb, N. Brandon, A. Hawkes, An assessment of CCS costs, barriers and potential, Energy Strategy Reviews 22, 61-81. 2018.
- W.S. Amarasinghe, I. Husum, L.A. Tokheim, Waste heat availability in the raw meal department of a cement plant, Case Studies in Thermal Engineering 11, 1-142. 2018.
- P. Zakkour, G. Cook, CCS roadmap for industry: High-purity CO2 sources, Sectoral Assessment, CCS Industry Roadmap, Final Draft Sectoral Assessment, Carbon Counts (2010).
- N.E. Flø, L. Faramarzi, F. Iversen, E. R. Kleppe, B. Graver, H. N. Bryntesen, K. Johnsen, Assessment of material selection for the CO2 absorption process with aqueous MEA solution based on results from corrosion monitoring at Technology Centre Mongstad, International Journal of Greenhouse Gas Control 84 (2019) 91-110.
- A.K. Morken, S. Pedersen, S.O. Nesse, N.E. Flø, K. Johnsen, J.K. Feste, T. de Cazenove, L. Faramarzi, K. Vernstad, CO2 capture with monoethanolamine: Solvent management and environmental impacts during long term operation at the Technology Centre Mongstad (TCM), International Journal of Greenhouse Gas Control 82 (2019) 175-183.
- Flø N.E., Faramarzi L., de Cazenove T., Hvidsten O.A., Morken A.K., Hamborg E.S., Vernstad K., Watson G., Pedersen S., Cents T., Fostås B.F., Shah M.I., Lombardo G., Gjernes E., Results from MEA degradation and reclaiming processes at the CO2 Technology Centre Mongstad, Energy Procedia 114 ( 2017 ) 1307-1324.
- Lombardo et al, Results from testing of a Brownian diffusion filter for reducing the aerosol concentration in a residual fluidized catalytic cracker flue gas at the Technology Centre Mongstad – GHGT -14,2018.
- Shah et al, CO2 capture from RFCC flue gas with 30 wt % MEA at Technology Centre Mongstad, process optimization and performance comparison, GHGT-14.
- Morken et al, Emission results of amine plant operations from MEA testing at CO2 Technology Centre Mongstad, GHGT-12.
First Process Results and Operational Experience with CESAR1 Solvent at TCM with High Capture Rates (ALIGN- CCUS Project) (2021)
Christophe Benqueta,b*, Anette Knarvikb, Erik Gjernesc, Odd Arne Hvidstenb, Eirik Romslo Kleppeb, Sundus Akhterb
aTotal E&P Norge, Finnestadveien 44, Dusavik, 4029 Stavanger, Norway bTechnology Centre Mongstad, 5954 Mongstad, Norway cGassnova SF, Dokkvegen 10, 3920 Porsgrunn, Norway
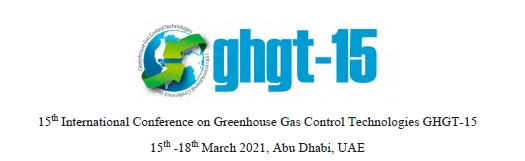
Abstract
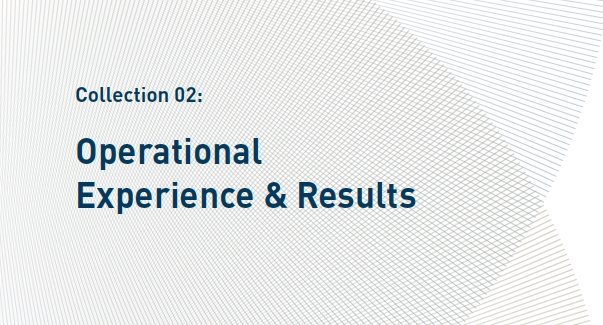
In 2019, the Technology Centre Mongstad (TCM) operated, in the frame of ALIGN-CCUS project, a test campaign using CESAR1 solvent, a blend of AMP and PZ. The main objective was to demonstrate CESAR1 operability and performance at large scale and produce knowledge that can be used to enhance the deployment of post-combustion capture at commercial scale. Tests were carried out on CCGT flue gas and varying process conditions and plant configurations. The current paper presents an overview of the test campaign and reports on energy performance, solvent consumption and operational experience. The CESAR1 solvent was found to require less energy than 30 wt% MEA considered as the reference. Although PZ degrades easily in presence of NO2, the solvent consumption was kept low over the campaign. Solvent precipitation in the absorber was experienced in severe conditions. Successful mitigating actions were applied to reverse it and operating procedures were developed to avoid it.
1. Introduction
The Technology Centre Mongstad (TCM) is the world’s leading facility for verifying and improving CO2 capture technologies. TCM is located at Mongstad, one of Norway’s most complex industrial facilities, next to the Mongstad refinery operated by Equinor. TCM has been operating since autumn 2012, providing an arena for qualification of CO2 capture technologies on an industrial scale. TCM is owned by Gassnova (on behalf of the Norwegian state), Equinor (formerly Statoil), Shell and Total. In 2019, TCM executed a test campaign with a non-proprietary solvent called CESAR1 in the frame of the ALIGN-CCUS project.
ALIGN-CCUS (Accelerating Low CarboN Industrial Growth through Carbon Capture Utilisation and Storage) is a project from the first ERA-NET Co-fund ACT program. In this program nine European countries, together with the European Union Horizon 2020 program are joining forces for research and actions. The ALIGN consortium involves 31 partners from industry, research and academia and has considerable involvement of industrial companies and an enterprise organization. The ALIGN-CCUS (ALIGN) project aims to accelerate the transition of current industry and power sectors into a future of continued economic activity and low-carbon emissions, in which carbon capture, utilization and storage (CCUS) plays an essential role. For the optimization and cost reduction of post-combustion capture (PCC) technology, the consortium realizes testing programs at four different pilot plants and testing facilities: the Technology Centre Mongstad (NOR), the SINTEF pilot rig at Tiller, Trondheim (NOR), RWE’s Coal Innovation Centre at Niederaussem (DE) and the PACT facilities at Sheffield (UK). Collaboration of TCM with ALIGN-CCUS project is significant in bridging the knowledge gaps, and reducing HSE, technical and financial risks of technology deployment at large scale.
The test campaign has been carried out from September 2019 to January 2020 with a blend of aqueous 2-Amino- 2-methylpropan-1-ol (AMP) and Piperazine (PZ). The amine concentrations were respectively 27 wt% and 13 wt%. This blend is called CESAR1 and has been developed during a former EU project (CESAR). This non-proprietary solvent is known to perform better than generic aqueous 30 wt% MEA and has been proposed by IEAGHG as their new benchmark [1]. It has potentially lower thermal energy consumption and lower solvent degradation rates than generic MEA. On the downside, AMP is volatile and may lead to relatively high emissions. In addition, PZ is a toxic compound and can also lead to precipitation at both very high and low CO2 loading, in combination with other process parameters like temperature of the solvent and flus gas. The purpose of the test campaign was to develop knowledge related to emissions, degradation and safe operation in industrial environment with the CESAR1 solvent.
This paper describes in the first part the parametric testing performed in different configurations of the amine plant. Optimum performances were determined by varying the liquid to gas ratio at capture rates from 85% up to 98%. This high capture rate was selected as high capture rate, close to 100%, are expected in the near future. The absorber was operated with 12, 18 or 24m of packing. For this work, the TCM amine plant was operated with flue gas from the Equinor’s CCGT plant at Mongstad. The second part describes TCM operational experience with the CESAR1 solvent.
Nomenclature | |||
AMP | 2-Amino-2-methylpropan-1-ol | ppmv | Parts per million by volume |
Capex | Capital expenditure | PZ | Piperazine |
CCGT | Combined Cycle Gas Turbine | RFCC | Refinery Fluid Catalytic Cracking |
CHP | Combined Heat and Power | SCR | Selective Catalytic Reduction of NOx |
DCC | Direct Contact Cooler | Sm3/h | Standard conditions: 101.325 kPa and 15°C |
HSE | Health, Safety and Environment | SRD | Specific Reboiler Duty |
MEA | Monoethanolamine | TCM | Technology Centre Mongstad |
Opex | Operational expenditure | wt% | weight percent |
2. Initial assessment of CESAR1 performance at TCM
2.1 TCM amine plant
The amine plant is a generic and highly flexible CO2 capture plant designed and constructed by Aker Solutions and Kværner. The amine plant captures CO2 either from CCGT flue gas with a design CO2 production capacity of 80 tonnes/day or from RFCC flue gas with a capacity of 200 tonnes/say. The ALIGN-CCUS campaign has been performed with CCGT flue gas. The plant was lined up with the CHP DCC and CHP stripper. Figure 1 given below shows a simplified process flow diagram of TCM amine plant. Flue gas from the blower is conditioned and saturated with water to the required temperature (normally 20-50°C) in the DCC. The lean amine solvent can be fed either at 12m, 18m or 24m to the absorber structured packed bed (highlighted in yellow in Figure 1). Rich amine from the absorber is pumped through the rich/lean cross plate heat exchanger to the top of CHP stripper. A slip stream of the cold rich amine is bypassed upstream the heat exchanger to the stripper overhead. A more detailed description of the amine plant is available elsewhere [2,3]
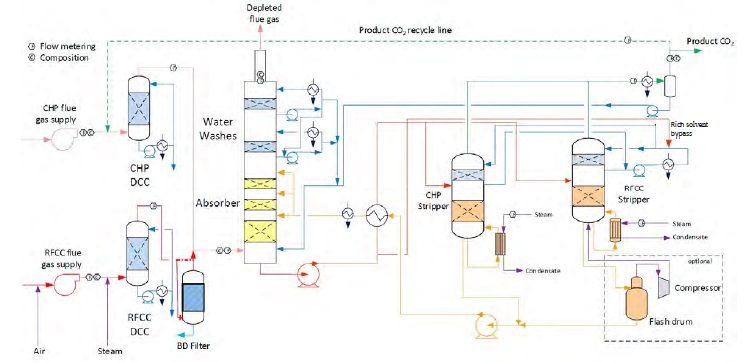
Figure 1. TCM Amine plant flowsheet.
2.2 Test plan description
The test campaign started on September 12th, 2019. The storage tank was filled with 26 tonnes of a concentrated aqueous mixture of AMP (48.0 wt%) and PZ (23.7 wt%) supplied by Brenntag. The solvent was diluted with demineralized water to reach the targeted concentration of 27 wt% of AMP and 13 wt% of PZ (AMP/PZ ratio of 2.1). The actual concentrations of AMP and PZ after dilution were respectively 25.37 and 12.41 wt%. The amine concentration has been adjusted continuously over the test campaign, depending on operating conditions, to maintain the amine concentration. The amine plant has been operated for more than 1500 hours until the 10th of January. The test plan has been adjusted throughout the campaign based on the results and may be found in Table 1. In every test, the flue gas flow rate and solvent flow rate were kept constant and the steam flowrate was adjusted to reach the targeted capture rate.
The test campaign started with the phase A at 90% capture rate. The tests were run with a flue gas temperature at the absorber inlet of 30°C, 24 meters of packing in the absorber. Phase B was a repeat of phase A with a higher capture rate, targeted at 98%. Precipitation was observed in the lower section of the absorber because of low flue gas temperature and high CO2 loading in the rich solvent (see section 3.2). As the flue gas temperature affects the capture plant thermal performance, tests from phases A and B were repeated later with a flue gas temperature at 40°C (respectively phases AA and BB).
Performance tests with 18 m of packing were carried out with a flue gas at 40°C in phases C and D, respectively at 90 and 98% capture rates. Tests with 12 m of packing were conducted in phase E with 90% of CO2 captured. A higher capture rate was not achievable here due to maximum capacity of the CHP reboiler and the CHP stripper.
# | Abs. pack | Flue gas x 1000 | Flue gas temperature | CO2 wet abs inlet | L/G | CO2 Capture |
[m] | [Sm3/h] | [°C] | % | [kg/Sm3] | % | |
A | 24 | 50 – 59 | 30 | ~ 3.5 | 0.6 – 1.2 | 90 |
AA | 24 | 50 – 60 | 40 | ~ 3.5 | 0.6 – 0.9 | 90 |
B | 24 | 50 | 30 | ~ 3.5 | 0.7 – 1.2 | 98 |
BB | 24 | 50-59 | 40 | ~ 3.5 | 0.7 – 0.9 | 95-98 |
C | 18 | 50 – 59 | 40 | ~ 3.5 | 0.7 – 1.2 | 90 |
D | 18 | 50 | 30-40 | ~ 3.5 | 0.7 – 1.2 | 98 |
E | 12 | 50 | 40 | ~ 3.5 | 0.8 – 1.3 | 90 |
K | 18-24 | 59 | 40 | ~ 3.5 | 0.6 – 0.8 | 85 |
F | 18 | 59 | 40 | ~ 3.5 | 0.7 | 90 |
MEA 2 | 24 | 47 | 30 | 3.6 | 0.9 | 87 |
MEA Base | 24 | 59 | 30 | 3.6 | 1.0 | 84 |
Table 1. Operational parameters for the TCM ALIGN-CCUS test campaign and the MEA test cases MEA 2 and MEA Base [2, 4]. Stripper pressure was set at 0.9 barg except for the F series where it varied from 0.5 to 1.6 barg.
In phase F, the plant was operated with 18 m of packing and 90% capture rate, at the optimal liquid-to-gas ratio (L/G) from phase C tests. The purpose was here to assess the effect of the stripper pressure on the energy penalty of CESAR1 solvent. Working at higher pressure is beneficial for the CO2 compression step. The downside might be a higher degradation rate of the solvent provoked by the higher temperature in the reboiler.
The purpose of phase K was to compare the CESAR1 performance against MEA baseline conducted in TCM amine plant [4]. The operating conditions were kept as close as possible to MEA tests to make the comparison more relevant, except the flue gas temperature. Those tests were carried out with 18 and 24 meters of packing, while MEA baseline was at 24 meters. TCM amine plant has been designed to be flexible, based on generic MEA solvent. Compared to MEA, the optimum L/G ratio with CESAR1 is lower due to its higher working capacity. The optimized operating conditions with CESAR1 were found to be very close to the limit of the operating window of the stripper due to very low amine circulation rate and hence low wetting of the packing. The amine pumps and stripper are oversized for this type of solvent. The best performances are achieved at the minimum flowrate delivered by the amine pumps (35,000 kg/h) and below the turndown capacity of stripper. The CHP stripper is designed for a minimum liquid flow rate of 42,000 kg/h. Hence, the performance may be affected by the plant design.
TCM used the same calculation method to assess the performance of the CESAR1 solvent as in [2] that also presents a detailed description of the methodology and the instruments used. The capture rate is calculated over the absorber. The energy demand is based on the energy brought to the reboiler and is called the specific reboiler duty (SRD).
2.3 Results from tests at 90% capture rate
Figure 2 shows the energy consumption required to capture 90% of the CO2 from the CCGT flue gas. The best performance is achieved with 24 m of packed bed. The plot shows better results with flue gas temperature at 30°C compared to 40°C (A vs AA series). The minimum steam consumption is around 3.1 MJ/kg CO2 which is significantly lower compared to 30 wt% MEA solvent tested at TCM. The optimum is found at the lowest L/G ratio, i.e. 0.7 kg/Sm3.
The steam consumption increases by approximately 15% when the flue gas temperature goes up to 40°C. However, the plant cannot be operated at 30°C for a long period of time because of precipitation of CESAR1 solvent in the absorber. The energy consumption is partially dependent on flue gas temperature, this indicates a room for improvement either by adjusting the flue gas temperature and/or the amine concentration.
Reducing the packing height from 24 to 18 meters does not impact the steam demand (AA vs C series). The upper 6 meters of packing are not necessary to capture 90% of the CO2 . With a shorter absorption section (12 meters, E series), the energy demand increases significantly. The SRD at optimum conditions is 25% higher, corresponding to an L/G ratio between 1.0 and 1.1 kg/Sm3. A short absorption column is not suitable to achieve low energy consumption but may be beneficial for projects where cheaper thermal energy is available or lower CO2 capture rate is targeted. CESAR1 results are compared to TCM operation with 30% MEA at 47,000 Sm3/h flue gas flow [2], see also Table 1. The left part of Figure 2 shows that operation with CESAR1 resulted in lower SRD values at lower liquid to gas ratios compared to the MEA 2 case. The right part of Figure 2 shows CO2 concentration into the absorber and lean amine loading. The AA and MEA 2 cases are at a higher CO2 level than the other cases. Lean loading is, as expected, decreasing for decreasing L/G ratios.
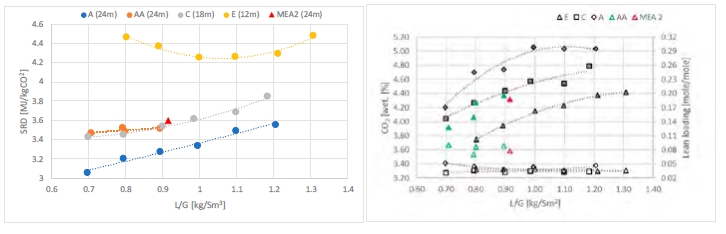
Figure 2. Left: Specific reboiler duty versus liquid to gas ratio for CESAR1 test series and MEA 2. The CO2 capture rate is around 90% and flue gas flow into the absorber 50,000 Sm3/h. Case A and MEA 2 are with 30°C flue gas temperature while rest of the cases are at 40°C – Right: CO2 concentration (wet) into the absorber and lean amine loading for CESAR1 test series and MEA 2 [2]. Open symbols are for CO2 concentration and left y-axis and filled symbols for lean loading and right y-axis.
2.4 Results from test at 98% capture rate
Figure 3 shows the energy demand to achieve 98% capture rate. The lowest energy consumption is achieved with
flue gas at 30°C and 24 meters of packing (B series). Operating conditions being very close to A series, precipitation
was also experienced. Flue gas temperature was adjusted to 40°C (BB series) leading to a 15% higher steam
consumption. The optimum case in BB series is not found at the lowest L/G ratio, but at 0.8 kg/Sm3. With an absorption section of 18 meters, contrary to the 90% capture rate cases, the energy demand is slightly higher. With an absorptionsection of 12 meters, the 98% capture rate was not achieved. The limitation is coming from the lean loading. The lean solvent is not lean enough to reach such a high capture rate despite the maximum steam flow rate in the reboiler.
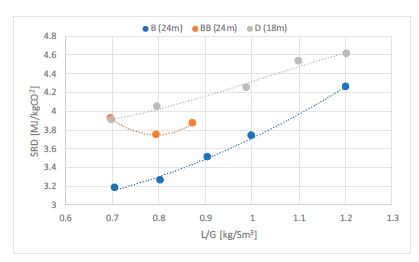
Figure 3. Specific reboiler duty versus liquid to gas ratio for CESAR1 test series B (blue), BB (orange) and D (grey). The CO2 capture rate is around 98% and flue gas flow into the absorber 50,000 Sm3/h. Case B is with 30°C flue gas temperature while the rest of the cases are at 40°C.
2.5 Variation of capture rate
The energy needed to capture either 85% or 90% of CO2 is very similar as shown in Figure 4. This observation is valid at both packing heights (18 or 24 meters). There is a gap in energy consumption to reach 98% capture rate regardless the packing heights. However, it might still be acceptable in some cases where high capture rates are targeted. The increase in SRD to reach 98% capture rate is in the range 5-15% compared to 90% capture rate cases. The gap is larger with a shorter absorption bed (18 meters). While the capture rate in many projects was set around 90%, there is a new tendency to increase it above 95% and minimize the CO2 emitted [5]. The CESAR1 solvent shows a good ability to reach this target with a limited extra steam consumption. In Figure 4, CESAR1 tests are also compared to MEA base [4] which was operated at 30% MEA. The K-series and MEA base were operated at 59,000 Sm3/h flue gas flow, 24-meter absorber packing and at around 85% capture rate. The K series resulted in lower SRD values than MEA base at lower L/G ratios. Figure 5 shows corresponding values for CO2 concentration into the absorber and lean CO2 loading. The CO2 concentration was constant in CESAR1 tests around 3.4% while it was higher in MEA base. Higher the CO2 concentration lower the energy demand.
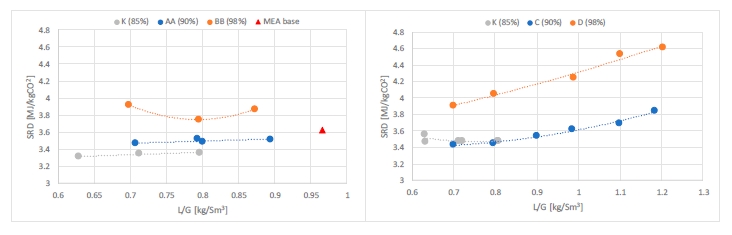
Figure 4. Specific reboiler duty versus liquid to gas ratio for CESAR1 tests and MEA base at 30% amine concentration [4]. The left figure shows results at 24 meters of packing while the right figure shows results at 18 meters of packing. Flue gas flows into the absorber in case K and MEA base are 59,000 Sm3/h while rest of the cases are at 50,000 Sm3/h. Capture rate varies from 85% to 98%.
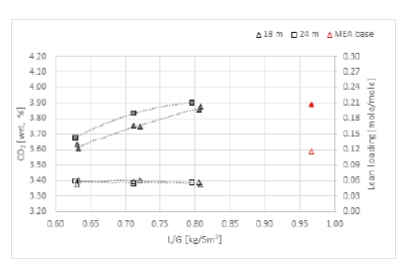
Figure 5. CO2 concentration (wet) into the absorber and lean amine loading for test series K (black) and MEA base (red) [4]. Open symbols are for CO2 concentration and left y-axis and filled symbols for lean loading and right y-axis.
2.6 Stripper pressure test
Based on results from phase C (18m of packing, 90% capture rate), the phase F was carried out to assess the effect of the stripper pressure on the performances. From a solvent management point of view, it is better to run the stripper at low pressure to reduce the stripper bottom temperature and hence, reduce the thermal degradation rate of the solvent. On the CO2 transport side, getting the CO2 at a higher pressure will be beneficial to reduce both Capex and Opex for CO2 compression. Based on optimal conditions from phase C, the stripper pressure was varied from 0.5 up to 1.6 barg. The flue gas flowrate was increased to 59,000 Sm3/h while keeping the L/G ratio at 0.7 kg/Sm3. This change in flue gas flow rates aims at increasing the liquid flow rate and improve the vapour-liquid traffic in the stripper, while remaining within the stripper overhead capacity. The specific reboiler duty presented in Figure 6 is plotted against the stripper pressure. The minimum energy consumption is found at 1.2 barg, where the stripper bottom temperature is 124°C, which might seem acceptable. However, long term tests are needed to quantify its effect on solvent degradation and consumption together with corrosion.
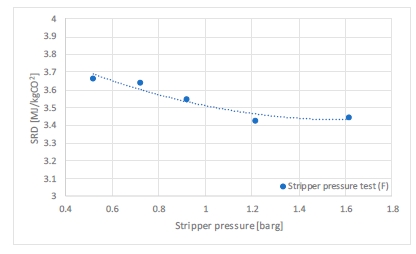
2.7 Solvent Management
In addition to the energy consumption, another important parameter to assess the performance of an amine-based capture technology is the solvent consumption. There are two main sources of solvent loss, one is from degradation, the other one is from emission to the atmosphere from the absorber stack. The solvent consumption depends mainly on the flue gas composition and impurities and on the operating conditions. An investigation of solvent degradation and emissions from TCM amine plant operated with MEA has previously been published [6]. The solvent loss during the CESAR1 campaign is based on parametric testing and might not represent the solvent loss for relatively stable operations applicable to commercial plants.
The thermal and oxidative degradation mechanisms for AMP and PZ have been explored separately [7-9]. According to the literature, the most common PZ degradation products are Piperazinol, Ethylene diamine (EDA), 2- oxopiperazine (OPZ), N-formyl piperazine (FPz), N-methylpiperazine (MPZ), Aminoethyl piperazine (AEP), Mononitrosopiprazine (MNPZ), Acetate, Oxalate, Ammonium, Ethylpiperazine (EPZ) and Ammonia. Other minor products include carboxylate ions, amides, glycolate, nitrite and nitrate. Most common AMP degradation products are 4, 4-dimethyl-2-oxazolidinone (DMOZD), 2, 4-Lutidine, Acetone and Formic acid.
The main areas of plant that facilitate degradation for any amine in post-combustion CO2 capture process are absorber sump, cross heat exchanger, reboiler, and reclaimer [7]. Thermal and oxidative degradation occur mainly due to the high temperature of the process, in the presence of dissolved oxygen, metals and free radicals [7].
With CESAR1 solvent, PZ was observed to be the most degraded amine. The main reaction was between NO2 coming from the flue gas and secondary amine functionality of the PZ to form Nitrosopiperazine. Nitrosamine concentration in the solvent has increased constantly through the campaign. Nitrosamines were not released in the stripper. Solvent reclaiming is the only way to wash them out. However, as long as the solvent performance are not affected, there is no specific risk associated to run the plant with non-volatile nitrosamines. Other degradation products include formic acid which was the major degradation product (see Figure 7) among the small chain organic acids. For the detailed analysis of solvent loss due to degradation and emission, the campaign was divided into Period 1 and 2. Duration for Period 1 with low NO2 (0.5 ppmv) was September 12, 2019 to October 12, 2019 and Period 2 with high NO2 (2.35 ppmv), was from October 12, 2019 to November 1, 2019). The NO2 concentration in Period 2 is considered high and was the result of no ammonia feed to the Selective Catalytic Reduction of NOx (SCR) in the CHP plant, upstream the amine plant.
A comprehensive lab schedule was set up, covering all analysis needed to follow up on the performance of the plant, emissions, corrosion and degradation. Samples were taken from lean amine and chemical analysis of the samples were performed to analyze the solvent condition. The calculations were based on wt% CO2, wt% AMP, wt% PZ, water content (Karl Fisher), degradation products and heat stable salts (HSS). The most common amine strength titration method (Total alkalinity) was developed for amine solutions with no contaminants. Non-volatile degradation products (DMOZD, 2,4 Lutidine, MNPZ, OPZ) were quantified and the formation and total accumulation determined for Period 1 and Period 2 are presented in Figure 7 and Table 2. The rates of formation of MNPZ and OPZ have increased in Period 2 as compared to Period 1, due to the increased NO2 concentration. Inventory variation for the testing period of Period 1 and Period 2 was evaluated based on the changes in total solvent alkalinity. Possible unquantified degradation products are formylpiperazine (FPZ), Acetylpiperazine (APZ) and unknown products with molar masses 55.057, 56.05 and 57.06 gram/mol were detected by PTR-ToF-MS. Further investigation would be needed to allow for quantification. Other factors include high levels of NOx and oxidative degradation catalyzed by increased iron concentration. Iron catalysis may also affect the formation of total formate and ammonia (both increase with increase in iron concentration) [8]. Alkalinity balance decreases as well with the increase in the concentration of iron in the solvent.
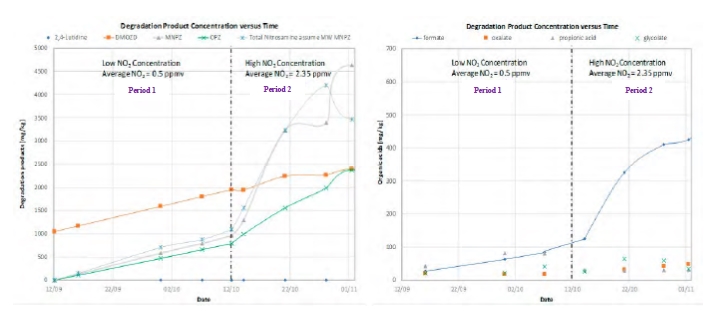
Figure 7. Degradation product concentration in Period 1 and Period 2 during CESAR-1 testing campaign (left). Degradation product concentration versus time showing increase in the concentration of formic acid or formate in Period 2 (right).
Parameters | Units | Period 1 | Period 2 |
Amine loss (Degradation products) | kg | 87.04 | 356.90 |
CO2 captured | kg | 1971.68 | 2112.05 |
Amine loss per ton of CO2 captured | kg amine/ton CO2 | 0.044 | 0.169 |
Total ammonia emissions to stack | kg/hr | 0.11 | 0.17 |
Total aldehyde emissions to stack | kg/hr | 0.029 | 0.035 |
AMP emissions to stack | kg | 135.2 | 68.3 |
PZ emissions to stack | kg | 2.8 | 1.5 |
Total amine loss to stack / ton of CO2 | kg amine/ton CO2 | 0.070 | 0.033 |
Total Amine loss per ton of CO2 captured (emissions + Degradation) | kg amine/ton CO2 | 0.114 | 0.202 |
Table 2. Total amine losses (emissions + degradation).
Atmospheric emissions were monitored throughout the campaign and are reported in a separate publication [10]. For the entire campaign, the piperazine emissions were in low ppb levels, even under high emissions testing. AMP emissions were in the range of 0.3 ppm to 2 ppm for standard U-curve tests, with high emissions tests yielding emission levels in the range of 6-9 ppm (e.g. reduced water wash efficiency). Nitrosamines were not detected in absorber stack even at ppb level. This topic will be addressed in an upcoming paper.
Based on emission and degradation, the average solvent loss has been estimated to be 0.16 kg amines/ton of CO2 for CCGT type of flue gas. This number represents 1600 hours of operation with a lot of parameters variating and it is considered to be in the low range of amine solvent loss. Similar or higher numbers were reported from test campaigns carried out at TCM [6, 11], e.g. MEA consumption was estimated around 1.5 kg amines/ton of CO2 during TCM MEA-2 campaign.
Successful solvent management includes setting strict threshold limits for the key indicators and applying reclaiming to keep the solvent as clean as possible. Proper solvent management has the potential to control solvent degradation and emissions and thus lower solvent consumption and reduce maintenance needs. From TCM’s operational experience, good solvent hygiene can be achieved by closely monitoring physical appearance of the solvent, together with degradation and emissions. An increase in ammonia emission will give a direct indication of solvent degradation and factors like NOx concentration in the flue gas and iron content can have a huge impact on solvent degradation. The solvent should be clear, light in color and the solvent mass balance should be closed. It is important to keep the solvent fresh, with low concentrations of degradation and corrosion products. Other important measures to improve the solvent hygiene can be solvent reclaiming.
3. Operational experience
3.1 Lab experiments, solvent supply and limits for operation
A set of laboratory experiments were carried out prior to purchase of solvent for three different purposes:
- Determine if the solvent components (AMP and PZ) should be ordered separately or pre-mixed.
- Supply information about solvent behavior and if it precipitates at various CO2 loading and temperature.
- Study at which levels of CO2 loading and temperature precipitation occurs.
For the first purpose, samples of 90% AMP, 68% PZ and a mixture with 53% AMP and 28% PZ were exposed to different temperatures. Piperazine precipitated when exposed to temperatures below 50°C. AMP and the AMP/PZ mixture samples did not form precipitate above 7°C. Based on the results, it was recommended to order the blend pre- mixed to avoid precipitation of pure piperazine in the solvent storage system.
For the second purpose, the AMP/PZ mixture was diluted to 27% AMP and 14% PZ and three samples of the mixture were prepared: one rich (0.73mole CO2/mole amine), one lean (0.10 mole CO2/mole amine) and one unloaded. These samples were each divided in three and exposed to 4°C, 25°C and 40°C. Precipitation occurred in all three rich samples and gel formed in the lean and unloaded samples at 4°C. The samples at 4°C are depicted in Figure 8, showing the two different changes observed in the samples at high, low and no loading. Further, the rich solvent sample was diluted with unloaded CESAR1 solvent to study closer at which levels of CO2 loading and temperature precipitation occurs. The results from the experiments with varying loading and temperature are given in Table 3. Overall, these experiments show that, at low loading, the solvent form a gel at low temperatures, while precipitation occurs at high loading and especially in combination with low temperatures. At the highest loading, precipitation occurs at all temperatures. An additional test was conducted on some of the samples to attempt to reverse the precipitation and gel formation. The gel vanished after heating to 40°C. All rich samples with 0.73 moles CO2/mole amine were heated to 55°C. The precipitate in these samples was not dissolved.
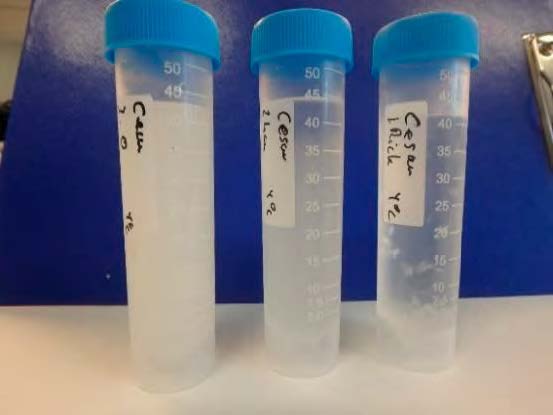
Figure 8. Samples of unloaded, lean (0.1 moles CO2/mole amine) and rich (0.73 moles CO2/mole amine) CESAR1 solvent at 4°C.The unloaded (left) and lean (middle) solvent form a gel, while precipitation is observed in the rich (right) sample.
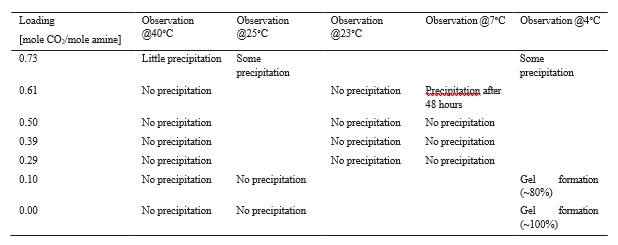
Table 3. Overview of observations made during the experiments where samples of different loading were exposed to different temperatures.
The mixed solvent was delivered at 72% amine concentration. As lab test showed gel formation in lean and unloaded solvent at low temperatures, the solvent was delivered at 40°C and storage tank temperature maintained at 45°C by circulating and heating the solvent. The plant was initially filled with solvent from the storage tank. Make- up from the tank has been added when needed. The lines from the tank to the plant have freeze protection but are not heated. To avoid gel formation in these lines, flushing with water after any transfer from tank to plant has been a part of the filling procedure. Even with water flush after each transfer, there have been some issues with plugging of the line. One part of the line is not possible to flush, and this is believed to be the cause of the plugging. Dilution of the solvent in the tank has been suggested as a mitigating action in order to reduce the risk of plugging the line.
The lab experiments indicate that both high loading and low temperatures should be avoided during operation. The main concern in case of precipitation was blocking of heat exchangers. The lab results were considered when operating the plant for parametric testing and during periods with standstill while the solvent was stored in the plant. The density measured on both lean and rich solvent flows could give indications of loading and the changes in density were monitored during the campaign.
Precipitation in absorber packing and mitigating actions
During phase A, the differential pressure in the lower absorber packing increased, as shown in Figure 9. The measured differential pressure is compared to a theoretical value for a given flue gas and solvent flow rate based on previous TCM experimental data. Lean solvent samples were analyzed for amine concentration and the amount of amine in the plant was calculated. The decrease in amines indicated that solvent was lost from the process and the plant was thoroughly checked for leakage without any findings. In the majority of the cases, the amount of amine in the plant is decreasing with increasing differential pressure, most significantly during phase B (98% capture rate). The increased differential pressure was then suspected to be caused by precipitation in the lower absorber packing. Phase B was followed by repetition of cases from phase A with higher solvent flow and lower capture rate than phase B, resulting in a decrease in the differential pressure. A mitigating actions test (MitAct in Figure 9) was done at higher solvent flow rate with increased lean solvent and flue gas temperatures to investigate if the differential pressure could be further reduced. After the mitigating actions test, the B1 test was repeated to verify the impact on the amine mass. Solvent analysis confirmed a significant increase in the amine mass compared to B1 (at the start of phase B), indicating that the lost solvent was precipitation that had been dissolved. As the differential pressure was still higher than the theoretically expected value, a long flushing without flue gas flow to the absorber was done. After the flushing, the differential pressure was back to the theoretically expected value and the amount of amine in the plant back to similar value as at the start of the campaign. It has been calculated that 5.7 tons of amines were precipitated at the end of phase B. This corresponds to roughly 29% of the total amine mass. In order to reduce the risk of precipitation in the absorber, the rest of the planned tests were operated at 40 °C flue gas inlet temperature. It can be observed that there is no differential pressure increase during the first InsVal (Instrument Validation) test, which was also operated with 40 °C flue gas inlet temperature.
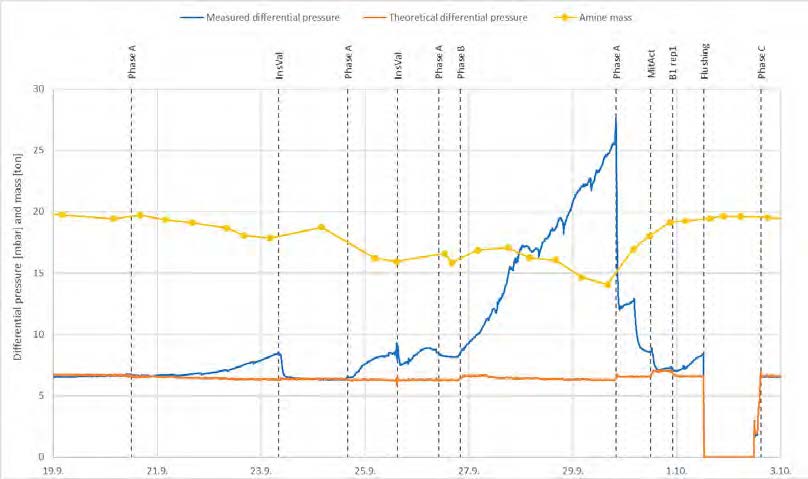
Figure 9. Total amine mass in the plant (yellow), measured (blue) and theoretical (orange) differential pressure in the lower absorber packing.
The density of the solvent, measured on lean and rich flow, did not indicate that precipitation should have been occurring during these initial phases. It is suspected that local differences in loading and temperature in the absorber can give local precipitation. Monitoring of the differential pressure in the absorber packing is recommended. Precipitation is believed to be caused by PZ. However, both AMP and PZ seem to precipitate as their ratio was kept constant during the precipitation periods.
4. Conclusions
The ALIGN-CCUS test campaign was the first TCM test campaign with CESAR1 solvent. The main objective of the campaign was to assess the performance of the solvent in terms of energy demand, emissions and solvent consumption. Some operational challenges have been experienced throughout the test campaign. The CESAR1 solvent is known to have better performance than MEA in terms of thermal energy and stability. This has been confirmed during this test campaign. The energy demand is lower by around 10% compared to 30 wt% MEA. However, the comparison is not straightforward. The MEA baseline was conducted before the rich bypass stream was implemented. In addition to the difference in amine concentration, PZ has two amine functions and can act as a promoter. The minimum flue gas temperature was 40°C with CESAR1 solvent because of precipitation at lower temperature in the absorber, while it was 30°C in MEA case. It was easy to reverse the precipitation by flushing the absorber with hot solvent at high flow rate, but this might be not optimal for a full-scale plant. The flue gas temperature strongly influences the steam consumption. It would be interesting to investigate mitigating actions to be able to lower the gas temperature. Although they were higher than in MEA case, the atmospheric amine emissions were kept low throughout the test campaign (below 1 ppmv). The high vapor pressure of AMP was the main cause of emissions. PZ emissions were found to be negligible with CCGT flue gas but could be strongly influenced by the presence of aerosols. The solvent consumption was found to be lower than MEA. The main loss comes from degradation. The PZ is very sensitive to NO2, it reacts to form nitrosamines. The nitrosamine concentration was high in the solvent but none of them were found in the absorber stack. The HSS concentration was kept low. The test campaign was successful and gave TCM valuable learnings.
Acknowledgements
The authors gratefully acknowledge the staff of TCM DA, Gassnova, Equinor, Shell and Total for their contribution and work at the TCM DA facility.
Acknowledgement ACT ALIGN-CCUS Project No 271501. This project has received funding from RVO (NL), FZJ/PtJ (DE), Gassnova (NO), UEFISCDI (RO), BEIS (UK) and is co-funded by the European Commission under the Horizon 2020 programme ACT, Grant Agreement No 691712 www.alignccus.eu.
References
- IEAGHG Technical Report 2019-09, Further Assessment of Emerging CO2 Capture Technologies for the Power Sector and their Potential to Reduce Costs
- Gjernes E, Pedersen S, Cents T, Watson G, Fostås BF, Shah MI, Lombardo G, Desvignes C, Flø NE, Morken AK, de Cazenove T, Faramarzi L, Hamborg ES. Results from 30 wt% MEA performance testing at the CO2 Technology Centre Mongstad. Energy Procedia, Volume 114, 2017, p 1146-1157.
- Shah MI, Lombardo G, Fostås B, Benquet C, Morken AK, de Cazenove T. CO2 capture from RFCC flue gas with 30 wt% MEA at Technology Centre Mongstad, process optimization and performance comparison. 14th Greenhouse Gas Control Technologies Conference Melbourne 21- 26 October 2018 (GHGT-14)
- Faramarzi L, Thimsen D, Hume S, Maxon A, Watson G, Pedersen S, Gjernes E, Fostås BF, Lombardo G, Cents T, Morken AK, Shah MI, de Cazenove T, Hamborg ES, Results from MEA Testing at the CO2 Technology Centre Mongstad: Verification of Baseline Results in 2015. Energy Procedia, Volume 114, 2017, p 1128-1145.
- IEA (2020), CCUS in Power, IEA, Paris https://www.iea.org/reports/ccus-in-power
- A.K. Morken, S. Pedersen, E.R. Kleppe, A. Wisthaler, K. Vernstad, Ø. Ullestad, N.E. Flø, L. Faramarzi, E. Steinseth Hamborg. Degradation and emission results of amine plant operations from MEA testing at the CO2 technology centre mongstad. Energy Procedia, 114 (2017), pp. 1245-1262
- Freeman, S.A., (PhD thesis). Thermal Degradation and Oxidation of Aqueous Piperazine for Carbon Dioxide Capture 2011. University of Texas at Austin.
- S.A. Mazari et al. 2014. Degradation study of piperazine, its blends and structural analogs for CO2 capture: A review. Int. J. Greenh. Gas Control 31, 214–228.
- Gouedard, C., et al., 2012. Amine degradation in CO2 capture. I. A review. Int. J. Greenh. Gas Control 10, 244.
- Languille B, Drageset A, Mikoviny T, Zardin E, Benquet C, Ullestad Ø, Aronson M, Kleppe ER, Wisthaler A. Atmospheric emissions of amino-methyl-propanol, piperazine and their degradation products during the 2019-20 ALIGN-CCUS campaign at the Technology Centre Mongstad. 15th International Conference on Greenhouse Gas Control Technologies Conference, 15th-18th March 2021 Abu Dhabi (GHGT-15).
Pending acceptation
- Gorset O, Knudsen JN, Bade OM, Askestad I. Results from testing of Aker Solutions advanced amine solvents at CO2 Technology Centre Mongstad, Energy Procedia, 63, 2014, 6267 – 6280
CO2 Capture and work environmental sampling at TCM - lessons learned (2021)
Alexander Reyes-Lingjerdea, Hans Thore Smedboldb, Audun Drageseta, Alexander Hålandd, Anne Kolstad Morkenc, Eirik Romslo Kleppea, Øyvind Ullestadac, Odd Arne Hvidstenac
aTechnology Centre Mongstad, 5954 Mongstad, Norway b Proactima AS, Richard Johnsens gate 4, 4021 Stavanger, Norway cEquinor ASA, Litlåsvegen 208, 5954 Mongstad, Norway dDepartment of Chemistry, University of Oslo, Sem Sælamds vei 26, 0371 Oslo, Norway
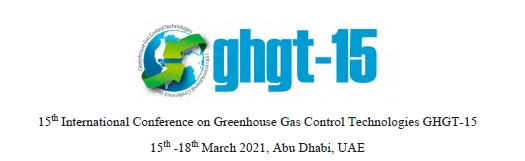
Abstract
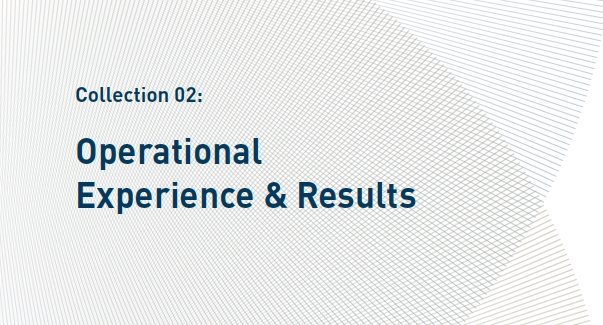
With almost a decade of operational experience from an amine-based post combustion carbon capture plant in Norway, Technology Centre Mongstad has under multiple occasions and operating scenarios monitored the work environment exposure risk for such facilities. Primary focus has been on concentrations of Nitrosodimethylamine in the work environmental atmosphere. This paper presents some findings from work environmental gas sapling collected between 2012 and 2020, where Thermosorb-N filters, impingers and PTR-MS were used for sampling. The main objective has been to investigate work environment exposure risk in a CO2 capture plant. The findings show that the median outdoor background concentration during the different test campaigns have been 0.2 ng/m3 (Arithmetic Mean 5.8 ng/m3, range <0.01 – 39 ng/m3). The average and maximum concentration represents 3% and 20% of the given Occupational Exposure Limit Value of 200 ng/m3 for NDMA, respectively. Our results suggest that Nitrosodimethylamine can be present at an amine-based CO2-capture test plant, but at acceptable concentrations. In conclusion, the design and operational conditions at Technology Centre Mongstad maintain exposure background levels for the working atmosphere at a satisfactory level.
1. Introduction
Technology Centre Mongstad (TCM) is one of the world’s largest and most flexible test centers for post combustion carbon capture technologies and is located next to the Equinor refinery in the western part of Norway. The refinery supplies two types of flue gases to TCM, using the Combined Cycle Gas Turbine (CCGT) based heat and power plant (CHP) and Residue fluid catalytic cracker (RFCC). The owners of TCM have conducted several non-proprietary test activities (often referred to as campaigns) especially on Monoethanolamine (MEA). In 2019 CESAR 1 solvent was introduced as a non-proprietary solvent. CESAR 1 is an aqueous amine solvent composed of AMP (2-Amino-2- methylpropan-1-ol) and PZ (piperazine).
The large number of participants from public sector, industrial, research and academic institutions involved in different test activities at TCM have provided new knowledge regarding CO2 capture and potential work environment exposure in an amine-based CO2 capture facility. Such data can be useful as background input before deployment of full-scale post-combustion capture (PCC).
Chemical exposure is considered one of the major work environmental risks for personnel at TCM. Therefore, risk assessments, classification and monitoring of chemical exposure is an important topic for TCM. During more than 7 years of operation, the Health Safety and Environmental Department (HSE) has identified several areas eligible for improvement regarding chemical exposure and chemical management. The risks are mainly related to use of the amine solvent and subsequent degradation products.
The CO2 absorption process based on amine technology is often described as a closed process. However, there are locations and operation from where amines and related degradation components can be released into the atmosphere. The amine absorption tower and CO2-stack are continuously emitting low quantities of amines and degradation components. TCM is required to have full control over these emissions. However, they can constitute a potential exposure source for personnel in close surroundings. Other areas of concern might be diffuse emission spots e.g. sumps, ventilation systems, liquid sampling cabinets and instruments.
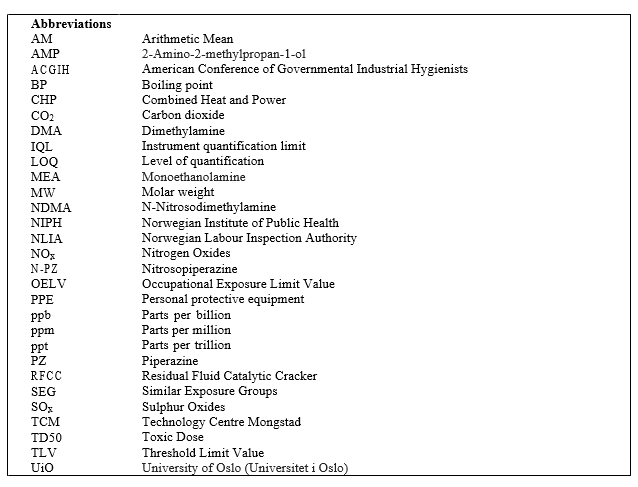
1.1 Amines and degradation components
In general, the main solvent in the CO2 capture process consists of one or a mixture of amines. In addition to carbon dioxide (CO2) and water the flue gas also contains Oxygen (O2), Nitrogen Oxides (NOx) and Sulphur Oxides (SOx), but in lower quantities. Carbamate is formed when the amine is exposed to CO2, this is a reversible reaction utilized in the capture process. However, the contaminants in the flue gas result in unwanted side products (degradation products) when reacting with the amine solvent. In particular, reaction with NOx will form nitrosamines, especially NO2, while the oxidative degradation for MEA will result in aldehydes, which are components of high environmental and health concerns. This degradation process is described in more detail in Morken et al [3].
At the start-up of TCM, the Norwegian Institute of Public Health (NIPH) published a report regarding health effects of amines and its derivatives. The report recommends limit exposure levels for the population to ensure a minimal or negligible risk of cancer. Calculated risk (level for cancer of 1 in 10-6 after lifelong exposure) for N- Nitrosodimethylamine (NDMA) should be applied to the total amount of nitrosamines and nitramines. The total amount of nitrosamines and nitramines shall not exceed 0.3 ng/m3 in air and 4.0 ng/L in water [1].
The Norwegian Labour Inspection Authority (NLIA) have not established specific Occupational Exposure Limit Values (OELV) for NDMA. Equinor is a responsible operator for TCM and was included in the pre-work for a full- scale plant at Mongstad. In collaboration with key personnel from the pre-work, physicians, and occupational hygienist at TCM it was established that TCM as the only CO2-facility in Norway should adopt the health based calculated occupational cancer risk (4 x 10-5, for 40 years of exposure to 0.2 x 10-2 mg/m3) values from Netherlands of 200 ng/m3[5].
Among known CO2-capture related components, piperazine (amine), formaldehyde and NDMA are components of very high concern due to their inherent properties. In addition, piperazine, formaldehyde and NDMA are the components with the lowest OELVs to workers (Table 1). Formaldehyde is classified to be toxic, a skin sensitizer, mutagenic and a carcinogenic component. Piperazine is classified as skin corrosive, and may cause allergic skin reactions, asthmatic symptoms or breathing difficulties if inhaled, and is also suspected to damage fertility. NDMA is considered as acute toxic, both swallowed and inhaled, carcinogenic, and may damage specific organs [8]
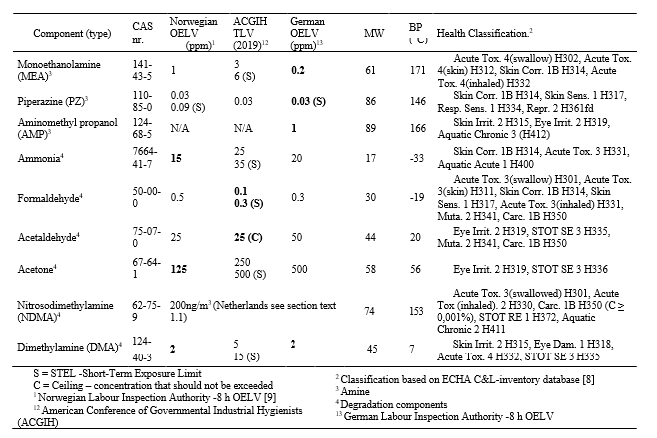
Table 1. Inherent properties of amines, ammonia, formaldehyde, acetaldehyde and acetone.
Determination of airborne nitrosamines has been prone to artefact formation (false positives) if solid sorbents are used, and in case of sample loss. The use of Thermosorb-N cartridges is a simple and credible method that has overcome this problem due to filters with an amine trap system. Linearity and controlled sampling tests have demonstrated that Thermosorb-N air samplers can be precise at low concentrations (25 ng) [2]. However, data on amine-concentration levels obtained at TCM are lower than the tests results described in the technical document [2]. Consequently, some of the initial Thermosorb-N filter analyses detected positive results at plant locations where it was not expected to be found nitrosamines. The credibility of these low quantity results was questioned.
Therefore, in collaboration with SINTEF, TCM introduced a midget impinger (25 ml) as an improved analysing method in 2016. In addition to nitrosamines, the impinger system is also able to detect and quantify amines in the ambient air. However, impinger sampling is considerably more challenging and time consuming to perform and require more training for preparation and sampling compared to use of filters.
TCM represents one of the largest test facilities for CO2 capture worldwide. To our knowledge, data concerning work environmental exposure in such facilities have not previously been reported over this extended time period and covering a large amount of amine technologies. During different test periods between 2012-2020, TCM have investigated background concentrations of different harmful substances and especially nitrosamines.
The primary aim of this paper was to provide an overview of work environmental exposure over time, and specifically sampling of nitrosamine concentrations, during different CO2 capture test periods at TCM. The secondary aim was to provide future CO2 capture plants with specific information about expected background concentrations around an amine plant.
2. Method, analysis, and strategy
Data were collected between 2012-2020, inside the TCM premises. Both personnel (n = 35) and static (n = 35) sampling was performed. During personnel sampling, workers were equipped with a sampling medium placed within a 30 cm radius, corresponding to the breathing zone. Static sampling was performed by stationing a sampling setup at strategic locations. Workplace measurements were performed using filters, impingers and direct reading instruments. To gain a greater insight into measurement methods that can be used in connection with amine plant Azzi et al. describes the various measurements methods in more detail [15]. The methods described in Azzi et al. are more related to the amine stack and amine emission but are also be relevant for the work environment.
Static filter samples were taken inside the amine plant or in close proximity (n = 24), in addition to indoor samples (n = 11). The indoor samplers were taken to verify if indoor environment could be influenced by emissions from amine stack. The indoor samples were placed in the office building, which is the most elevated sampling location inside the TCM area, approximately 200 m from the amine plant. In addition, samples were taken from the laboratory inside the building that represents a working area where personnel open and analyse the solvent and its relevant components. The laboratory was included along with the other indoor samples, because is connected to the same mechanical ventilation system. By dividing the results, it is possible to determine if the laboratory concentrations differ from the rest.
The first 7 samples of Thermosorb-N filters in 2012 were analysed by the Ramboll laboratory, whereas most filters and impinger samples from 2013 and onwards were sent to SINTEF for analysis. SINTEF has been involved in amine- based CO2 capture technology for several years and perform numerous other analyses for TCM as well as degradation tests for many of the tests vendors before testing at TCM.
In collaboration with the University of Oslo (UiO), TCM have conducted investigations into ambient air concentrations close to the plant since start-up in 2012. UiO have performed method development and sampling with direct reading, Proton Transfer Reaction Mass Spectrometer (PTR-MS).
Multiple technology developers have utilized TCM’s capture plant as a CO2 test facility over the years, and TCM is committed to uphold all confidential agreements with those vendors. Samples collected during proprietary test campaigns are therefore masked as general samples without dates, non-proprietary data will be presented without limitations.
2.1 Thermosorb-N Filters
The principle behind active sampling is the use of a pump connected to a sampling medium through a hose (Figure 1). The medium can be either a filter, cartridge, tubes or impingers. TCM have used a SKC Sidekick pump connected to a Thermosorb-N filters and operated at approximately 2 L/min. The flow is controlled before, under and at the end of the measurements with the help of a rotameter. The average concentration is given in ng/m3. The filter tubes were prepared with magnesium silicate and an amine-trapping agent [6].
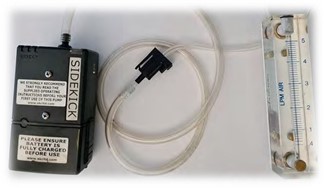
Figure 1. Sampling setup – from left sidekick pump connected to hose and filter. To right rotameter to measure flow (Photo: A. Reyes-Lingjerde).
According to SINTEF, to retrieve trapped Nitrosamines, the filters were eluted with MeOH/H2O (80/20). An internal standard consisting of isotope-label variants was added to ensure complete elution. The matrix was analysed with LC/MSMS, a liquid chromatography instrument coupled with a tandem mass spectrometer. The spectrometer is of type 6495 Triple Quadruple MS for quantification. The instrument limit of quantification (ILQ) is set to 0.05ng/mL for most nitrosamines, which is presented as <0.05 ng/cartridge in the obtained analysis results.
2.2 Impinger
With impinger it is possible to capture both amines and nitrosamines in the work atmosphere. The setup consists of three impingers in a series, where a pump draw gas through the three components. The impinger with sampling medium was stored in a compartment, filled with water and ice to maintain the temperature as close to 0°C as possible (Figure 2).

Figure 2. (a) Midget impinger setup used; (b) Picture of impinger setup (Illustration: A. Reyes-Lingjerde).
The principle behind impinger sampling is like filter sampling. The flow rate should ideally be 2.83 L/min according to Hinds, 1999 [7]. However, it was not possible to meet this flow rate with a SKC Sidekick. The maximum operational flow was 2.3 L/min. Capture medium for the amines was 0.1 M Sulphuric acid and 0.1 M Sulphamic acid for nitrosamines, respectively. As illustrated in Figure 3, the complexity of the sampling method, only allows static sampling.
2.3 Direct reading instruments
Measurement of background sampling of trace compounds for a longer period (1-2 weeks) was conducted by a Proton Transfer Reaction Time of Flight Mass Spectroscopy (PTR-TOF-MS). This is an instrument used for online monitoring of volatile organic compounds and can achieve a detection limit in the single pptV level. The sampling principle is described more detailed in Languille et al. (2020) [11].
2.4 Data processing and comparison
Our background data were compared with OELV’s from different sources (Table 1). Norwegian and German OELV’s as well as American TLV are presented in Table 1, where most conservative approach was selected as comparison level. For measurement data below the instrument quantification level (IQL) values has been substituted with IQL/√2 (2). The level of detection (LOD) and quantification (LOQ) of the filters was calculated as follows; LOD = (S.E mean)*α*β, where α=β and taken from a Student-t distribution, and LOQ = S.E mean *10 [10]. For statistical analysis of the data Microsoft Excel was used (Office 365). The data seem to be neither normal nor log- normal distributed. This is expected as the data were gathered over a longer period and during different campaigns with different amines. Data are therefore presented as both AM (Arithmetic Mean) and Median, together with
Maximum and Minimum values compared with OELV’s. Confidence interval is not presented due to unclear data distribution.
Our focus in this paper has been on background data from static samples inside TCM. Whereas some data from personnel sampling are also included, a more extensive presentation on this topic will be addressed in a future paper according to standard EN 689 [14].
3. Results
The presentation of the results is divided into three parts, 1) Testing of methods, 2) Background exposure at TCM- plant and 3) Personnel samples.
3.1 Testing methodes
The methodology testing includes results from blank filters, comparing old vs. new filters and exposure the Thermosorb-N filters to known NDMA concentrations.
3.1.1 Blank filters
In total 10 blank filters were analysed. In 50% of the filters NDMA was detected above the ILQ of 0.05 ng/cartridge, with an AM of 0.78 ng/cartridge (Table 2). This indicates possible artefacts at these low levels. The LOD and the LOQ of the method is estimated to be 1.0 and 2.9 ng/cartridge, respectively.
Table 2. Blank filter results. Results reported for filters with detected levels above IQL (n = 10).
Nr. | Nr. (%) | AM | SD | Min | Max | LOD | LOQ |
samples | <IQL | [ng/cartridge] | [ng/cartridge] | [ng/cartridge] | [ng/cartridge] | [ng/cartridge] | [ng/cartridge] |
10 | 5 (50%) | 0.78 | 0.96 | <0.05 | 2.33 | 1.02 | 2.90 |
3.1.2 Comparison of filters stored for a short and long time
A comparison was performed between filters stored for less than a month and filters older than 24 months. TCM personnel were wearing a parallel set of a new and old filter between 2-5 hours sampling, during normal workdays (Table 3). The work performed was representing a full shift day. Four samples were taken by 4 different operators. The results indicate an average difference of -19.5% and an average absolute average difference of 33%.
Filter set | 1 | 2 | 3 | 4 |
New (ng/m3) | 6.11 | 4.68 | 12.62 | 4.00 |
Old (ng/m3) | 8.30 | 3.37 | 11.76 | 1.26 |
%-difference | 26% | -28% | -7% | -69% |
% avg. difference | -19.5% | |||
% absolute avg. difference | 33% |
Table 3. Comparison of filters stored for a short (<2 years) and long time (>2 years)
3.1.3 Laboratory test with known concentrations
A test experiment was set up intended to study filters exposed to a known nitrosamine matrix. A standardised package of nitrosamines was retrieved from Sigma-Aldrich (EPA 8270). The package contains a 1mL ampule with a concentration of 2000µg/mL of each nitrosamine (including NDMA) diluted in methanol. The ampules were further diluted as following 345, 172.5, 69, 34.5, 17.3, 5.2 ng/mL.
For the experiment, the Thermosorb-N filters where first aligned on a test bench. A weighted funnel was attached to the filters inlet to function as an evaporation chamber for the nitrosamines. To the filter’s outlet, a pump was attached to pull ambient air through the filters. Aliquots of 1 µL from the dilutions were extracted by a micropipette and supplied to the Thermosorb-N filters via the weighing funnels coupled to the filter’s inlet (Figure 3).
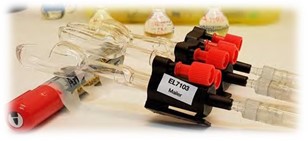
Figure 3. Setup for exposing Thermosorb-N filters for known concentrations of NDMA (Illustration: A. Reyes-Lingjerde).
The main objective with the experiment was to study exposed filters to a source known to contain NDMA. A total of 6 filters with 6 different concentrations was used in the experiment. The results are presented in Table 4 and shows deviations between the theoretical and analysed concentrations varying from -18% to 61%.
Theoretical [ng/10mL] | Analyzed [ng/cartridge] | Δ% |
345.0 | 447.7 | 29.8 |
172.5 | 219.0 | 26.9 |
69.0 | 110.7 | 60.5 |
34.5 | 29.6 | -14.3 |
17.3 | 18.3 | 5.6 |
5.2 | 4.8 | -17.8 |
Table 4. Laboratory experiment, exposing individually Thermosorb-N filters and midget impingers (Sulfamic acid) series for six theoretical concentrations of NDMA.
3.2 Background exposure at TCM-plant
The background results are divided into two parts, 1) active sampling with filters and impingers and 2) PTR-MS direct reading instrument.
3.2.1 Filter and impinger
Results included 35 background samples, divided into outdoor and indoor concentrations, a total of 24 samples (20 filter and 4 impinger) and 11 samples (5 filter and 6 impinger), respectively (Table 5). The sampling time for all samples was between 1 and 5 hours (avg. 3 hours). The indoor results included 8 samples from inside the laboratory and 3 samples from the remaining building.
The median outdoor background concentrations during the different test campaigns were 0.2 ng/m3 (AM 5.8 ng/m3, range <0.01 ng/m3 – 39 ng/m3). The average and maximum concentration represents 3% and 20% of the given OELV of 200 ng/m3 for NDMA, respectively. Of all the 24 background measurements 2 samples were approximately 20% of the given OELV. Both samples were taken in close proximity to the analysis house. The remaining 22 samples were <9% of the given OELV.
The indoor median concentration for the whole building was 3.1 ng/m3 (AM 2.4 ng/m3, range <0.01 – 7.4 ng/m3). When separating laboratory samples from other parts of the building, the median was 2.1 ng/m3 (AM 2.3 ng/m3, range <0.01 – 6.2 ng/m3). The average and maximum concentration for all indoor samples was 1% and 4%, and for laboratory samples 1% and 3% of the given OELV, respectively.

Table 5. Background concentration of NDMA around the TCM plant (number of samples = 35).
3.2.1 Direct reading sampling
From October 8th to 20th 2015 (non-proprietary MEA-campaign) direct reading measurements on air concentrations were carried out in close vicinity to the instrument house (online instruments measuring stack emissions with local instrument emission point) in the plant. NDMA was not detected, while MEA was found in very small quantities (AM 0.20 ppbV). The following degradation components were also detected at a very low concentration: Dimethylamine (DMA), Formaldehyde and Acetone (0.18 – 0.79 ppbV), and Acetaldehyde and Ammonia (2.42 – 14,12 ppbV). Such detection of degradation components is expected according to Morken et al [3]. The AM concentration of all the direct reading measurements was 0.4% or less than the given OELV’s (Table 6). Two task specific personnel samplings where performed during this period indicating presence of NDMA, 4.7 ng/m3 (0.002 ppb) and 11.4 ng/m3 (0.004 ppb).
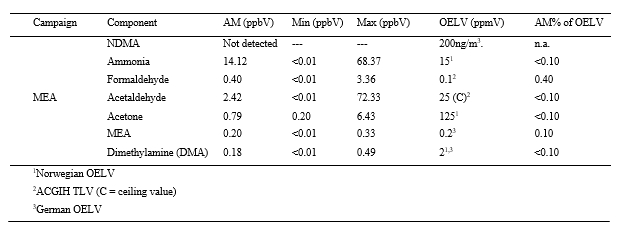
Table 6. Traced components during MEA-campaign, from 8th to 20th of October 2015 (continuous sampling with a PTR-TOF-MS instrument).
From January 13th to 17th 2020 (non-proprietary CESAR 1-campaign) direct reading measurements were carried out in the amine plant. NDMA was not detected, while Piperazine was found in very small quantities (AM 0.01 ppbV; range <0.01 – 0.04 ppbV) and AMP (AM 0.30 ppbV; range 0.03 – 1.28 ppbV) (Table 7). It was also possible to detect nitroso-piperazine (N-PZ) up to 6 pptV (28 ng/m3), but mostly below 4 pptV (19 ng/m3).

3.3 Personnel samples
Thirteen full shift samples were conducted with a sample time ranging from 4.5 to 6.5-hour. The median concentration was 3.4 ng/m3 (AM 3.8 ng/m3, range 0.8 – 10.7 ng/m3). The average and highest measured full shift exposure was 2% and 5% of the given OELV, respectively (Table 8). Task results are based on 22 samples, with 1 to 3-hour sampling time. The median concentration was 6.1 ng/m3 (AM 6.1 ng/m3, range <0.5 – 12.6 ng/m3). The average and highest measured full shift exposure was 3% and 6% of the given OELV, respectively.
Nr. samples | n (%) <IQL | AM [ng/m3] | Median [ng/m3] | Min [ng/m3] | Max [ng/m3] | AM% of OELV | |
Full shift | 13 | 0 (0.0%) | 3.8 | 3.4 | 0.8 | 10.7 | 2 |
Task | 22 | 1 (4.5%) | 6.1 | 6.1 | <0.5 | 12.6 | 3 |
Table 8. Personal Thermosorb-N filter samples of NDMA at TCM (number of samples = 35)
4. Discussion
4.1 Main findings and significance
Our main findings show that NDMA can be present when amine-based CO2 capture tests are performed at TCM, however median and average background levels were generally present at low concentrations. These results demonstrate that background levels from TCM are in compliance with today’s OELV of 200 ng/m3. In fact, most of the measurements were below or in the same magnitude as the level of quantification.
The intention with the personnel sampling results in this article was to give a general indication on expected concentrations of NDMA. As the results show, the personnel sampling mean concentrations for full shift and task operations were 2% and 3% of the OELV, respectively. These preliminary findings suggest that direct personnel exposure was also low.
Of concern, two background NDMA samples were around ~20% of the given OELV. These samples were both taken close to the analysis facility, which probably explain this finding, as the analysis house is a diffuse emission point.
The first sampling period that included direct reading of air concentrations detected DMA but not NDMA. DMA could potentially form NDMA, which might explain why this was detected in two of the personnel samplings. However, most probably the NDMA found was related to task-based work. These two personnel task-based samples were performed during circumstances where evaporation from the solution is expected. Under such circumstances personnel always wear PPE. Detection of formaldehyde was also considered a factor of concern. The background concentrations were low compared to the OELV, but when personnel perform any risk-based tasks which can lead to direct exposure to the solvent, either physical or by inhalation, appropriate PPE and personal alarm instruments must be used.
Some of the samples during the second test period also identified very low background concentrations. With the direct reading measurements, NDMA air concentrations was not detected, while N-PZ was. When filter sampling was performed, the analysis indicated that NDMA was also present. It is important to emphasize that the Thermosorb-N sampling was performed at the end of an extended test campaign, which can explain the presence of nitrosamines as the solvent degrades over time. The source of the detected nitrosamine background levels can be questioned. Piperazine is not a naturally occurring amine. Detection of N-PZ in proximity to the amine plant most likely indicate that the background levels originate from the amine plant.
It is important to underline that even if the background concentrations found around an amine plant are low, all types of physical contact with the solvent must be avoided due to its inherent hazardous properties to human health. Personnel must be specifically trained to handle leakages, modifications and other tasks that can lead to contact with the solvent. Furthermore, personnel protective equipment (PPE) must be easily available, as well as personal alarm instruments to ensure that personnel have the possibility to detect amine related source of exposure.
To our knowledge, this is the first study that has examined work environment and exposure-risks at an amine-based carbon capture plant of such a magnitude and over a longer time period. In our opinion, the reported findings are reassuring with respect to possible health risks and the work atmosphere in the facility.
4.2 Methodological considerations
When analysing filters after testing, false positive was detected in 50% of the blanks. Even though the concentration were low, this indicates that filters may generate the very same artefacts they are designed to remove. These artefact formations probably represent a limitation for outdoor environment sampling when trying to compare Thermosorb-N filter samples with the recommended exposure levels for the population.
Normally, any “background noise” identified blank filters is subtracted from the findings in exposed filters. However, since 50% of the exposed filters showed values <IQL and the blank filters were analyzed over different test periods, we chose not to subtract such values. If this method had been applied, our study would been reported even lower mean concentrations. The calculated LOQ value for the sampling system (combination of analysis and filter) in this study is based on few measurements and should therefore be subject for further study.
The laboratory experiment exposing filters with known concentrations of amines was a pilot test and a relatively easy to reproduce. The presented results show that Thermosorb-N filters are reliable and can be used in work environment assessments. However, the experiment also illustrates the uncertainties at these low concentrations levels and additional tests should conducted even more precisely e.g. in accordance with Xiao Chen et al [6].
Sampling with old Thermosorb-N filters (stored more than 24 months) compared to new filters indicates a possible loss with an average difference of -20% (-69% to 26%) in the quantity of nitrosamines trapped. This could mean that less nitrosamines are captured on average with filters that has been stored over a longer time. However, it is difficult to evaluate by an only 4 parallel filter comparison and at these very low concentrations. When possible, similar test will be performed in future studies.
An important discovery during the CESAR 1 campaign (2019-2020), the nitrosamine N-PZ was detected by the direct reading instrument. However, when sampling with Thermosorb-N filters during the same period SINTEF couldn’t manage to extract any N-PZ. This discovery shows that it is important to determine which components can be trapped by different sampling methods and at which concentrations.
To strengthen sampling methods and results in the future, TCM have initiated a study suggesting more tests comparing filter with impingers, filter with PTR-TOF-MS, and the use of different adsorbents in impingers. The purpose of comparing measurement methods is to demonstrate difference between the methods and be able to give an assessment of what is the “golden” standard method to use for sampling nitrosamines. In addition, TCM have plans to sample in near surroundings (200-1000m radius). Such data are of interest to understand the background levels in a wider perspective which is relevant for both the work and external environment.
4.3 Conclusions
Our findings demonstrate that the risk of exposure to NDMA in a facility such as TCM is very low when amine- based CO2 capture tests are performed. The required conditions TCM operates at and the design of the plant appears to maintain exposure background levels in the working atmosphere down to a satisfactory level, compared with todays recommended OELV for nitrosamines. Still, low concentrations detected inside the office building indicate that NDMA can be present. It is therefore important to study this further and determine if such findings are related to the location of the facility and/or ventilation system, and if the source is the absorber tower or ground concentrations.
Future research should focus on developing improved methods to identify low concentrations of potentially harmful substances in relation to amine-based CO2 capture plants
Acknowledgments
The authors gratefully acknowledge the staff of TCM DA, Gassnova, Equinor, Shell and Total for their contribution and work at the TCM DA facility. The authors also gratefully acknowledge Gassnova, Equinor, Shell, and Total as the owners of TCM DA for their financial support and contributions.
References
- Låg M, Lindeman B, Instanes C, Brunborg G, Scwarze P. (2011). Health effects of amines and derivatives associated with CO2 capture. Folkehelseinstituttet (Norwegian Institute of Public Health), April 2011, p.30.
- Thermosorb-N Air Sampling Cartridges, Ellutia Chromatography Solutions
- Morken A.K, Pedersen S, Romslo E.K, Wisthaler A, Vernestad K, Ullestad Ø, Flø N.E, Faramarzi L, Hamborg E.S. (2016). Degradation and Emission Results of Amine Plant Operations from MEA Testing at the CO2 Technology Centre Mongstad.
- Zhu L, Mikoviny T, Wisthaler A, Nielsen C (2015). TCM Ambient Air Measurement. University of Oslo (Unpublished)
- Committee of the Health Council of the Netherlands, December 1999. N-Nitrosodimethylamine (NDMA) Health based calculated occupational cancer risk values.
- Reunbehler D.P, Reisch J.W, Fine D.H. (1980). Nitrosamine Air Sampling Using a New Artifact-Resistant Solid Sorbent System.
- Hinds W. C. (1999). Aerosol Technology, Properties, Behaviour, and Measurement of Airborne Particles (second edition, pp. 226-227). John Wiley & Sons, Inc.
- European Chemical Agency. (2019.11.28). C&L Inventory. https://echa.europa.eu/information-on-chemicals/cl- inventory-database
- Norwegian Labour Inspection Authority. (2019.11.28). Regulations concerning action and limit values for physical and chemical agents in the working environment and classified biological agents 2020, S.I.No.FOR-2011- 12-06-1358, Norwegian Labour Inspection Authority. https://www.arbeidstilsynet.no/globalassets/regelverkspdfer/forskrift-om-tiltaks–og-grenseverdier
- Eurachem. 2014. Eurachem Guide: The Fitness for Purpose of Analytical Methods – a Laboratory Guide to Method Validation and Related Topics. 2nd ed., edited by B. Magnusson and U. Örnemark.
- Languille B, Drageset A, Mikoviny T, Zardin E, Benquet C, Ullestad Ø, Aronson M, Romslo E, Wisthaler A. (2020). Best practice for measurement of 2-amino-2-methyl-1-propanol, piperazine and their degradation products in amine plant emissions.
- American Conference of Governmental Industrial Hygienists (ACGIH) (2019). Threshold Limit Values and Biological Exposure Indices.
- Institut für Arbeitsschutz der Deutschen Gesetzlichen Unfallversicherung. (2019.11.28). GESTIS International Limit Values. https://limitvalue.ifa.dguv.de
- Comite Europeen de Normalisation (CEN) (2019). Workplace exposure – Measurement of exposure by inhalation to chemical agents – Strategy for testing compliance with occupational exposure limit values, EN 689.
- Azzi M, Day S, French D, Halliburton B, Jackson P, Lavrencic S, Riley K, Tibbett A (2010). CO2 Capture Mongstad – Project A – Establishing sampling and analytical procedures for potentially harmful components from post-combustion amine based CO2 capture.
Results of the fourth Technology Centre Mongstad campaign: LVC testing (2019)
Philip Loldrup Fosbøla,⁎, Randi Neerupa, Susana Almeidaa, Amirali Rezazadeha, Jozsef Gaspara, Anette Beate Nesse Knarvikb, Nina Enaasen Fløb
aCenter for Energy Resources Engineering (CERE), Department of Chemical Engineering, Technical University of Denmark (DTU), Søltofts Plads, Building 229, DK-2800 Kongens Lyngby, Denmark bTechnology Centre Mongstad (TCM DA), 5954 Mongstad, Norway
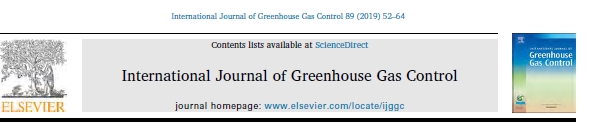
Received 3 October 2018; Received in revised form 24 June 2019; Accepted 27 June 2019
Available online 22 August 2019
1750-5836/ © 2019 Elsevier Ltd. All rights reserved.
Abstract
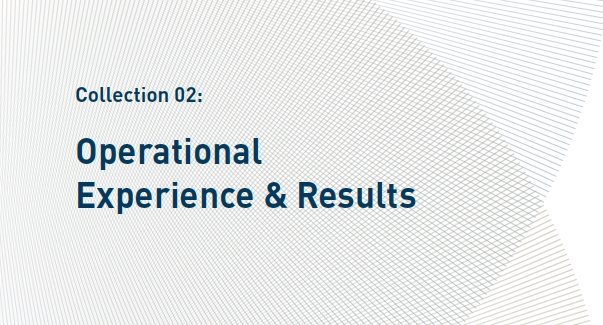
The lean vapor compressor (LVC) unit at Technology Centre Mongstad (TCM), Norway has been tested using 30 wt% monoethanol amine (MEA) and flue gas from the combined cycle gas turbine (CCGT) based combined heat and power (CHP) plant. The aim was to study the impact of LVC on the CO2 capture efficiency and energy profile of the TCM plant. 16 cases have been tested with and without LVC, and with various process parameters such as LVC pressure, solvent flow, inlet flue gas CO2 concentration, and stripper pressure. Absorber and stripper process conditions were recorded during these tests. The operation of the TCM amine plant was very steady. Standard deviation and reproducibility of the various process parameters were satisfactory.
Overall, the LVC results are as expected. A clear trend shows lower operating LVC pressure gives less specific reboiler energy consumption. A maximum thermal energy reduction of 25% was obtained when applying LVC at the expense of a typical LVC electrical energy consumption of 0.1 to 0.2 GJ electric/ton CO2. Additional results show that the specific reboiler duty (SRD) may have a characteristic non-linear dependence on solvent flow rate. Higher stripper pressure may decrease the specific reboiler duty and be beneficial to the thermal power used in the plant at the expense of increased LVC electrical power consumption.
Lower SRD was obtained when increasing the inlet flue gas CO2 concentrations both with and without LVC. For the LVC cases, no significant indication of additional energy requirement was observed when increasing the CO2 capture rate. The LVC power consumption in this study was to a large extend conservative due to a specific LVC design chosen. The presented results will help to enhance the accuracy of future CO2 capture engineering designs.
This article is behind a paywall. For futher information: https://www.sciencedirect.com/science/article/abs/pii/S1750583618307552?via%3Dihub
ION’s 6-month campaign at TCM with its low-aqueous capture solvent removing CO2 from natural gas-fired and residue fluid catalytic cracker flue gases (2018)
E.E.B. Meuleman, A.R. Awtry, T.R. Silverman, S. Heldal, G.A. Staab, R. Kupfer, C. Panaccione, R. Brown, J.S. Atcheson, A.E. Brown
ION Engineering, Boulder, CO, 80301 USA
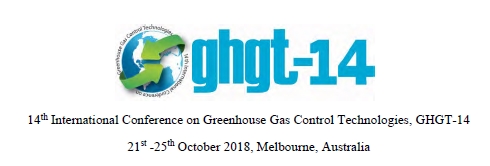
Abstract
ION Engineering’s (ION) advanced solvent is one of the leading second-generation solvent systems currently under development for post-combustion carbon dioxide (CO2) capture. This paper discusses the results obtained at CO2 Technology Centre Mongstad (TCM) in Mongstad, Norway between September 2016 and April 2017, where ION captured over 14,800 tonnes of CO2 throughout the 2,775-hour testing campaign. The testing was done on flue gases from a natural gas-fired combined cycle heat and power facility (CHP) and a residue fluid catalytic cracker (RFCC) from the adjacent Statoil refinery at a scale comparable to 12 MWe. The CO2 concentrations in both flue gas types could be varied using recycle from the stripper or dilution by air. In this work, CO2 concentration settings of between 3.6% and 15.0% were tested. In the TCM plant, which is not optimized for ION’s solvent system, ION achieved a specific reboiler duty (SRD) as low as 3.2 MJ/kg CO2 during the testing at TCM while demonstrating 90% capture efficiency with low emissions and low corrosion. Furthermore, testing showed capturing 98% of the CO2 with ION’s solvent results in only a 10% increase in energy consumption. The results from ION’s campaign at TCM were then used to validate the ION process model in ProTreat® to a high accuracy. Subsequent process design optimization shows ION’s solvent is capable of an SRD of less than 2.5 MJ/kg CO2 when incorporating ION’s key process operations. Throughout pilot testing, ION has confirmed its understanding of process improvements and analytics that will enable successful operation of its solvent system at significantly lower L/G circulation rates, packing heights, and regeneration energies than traditional baseline mono-ethanolamine (MEA). ION anticipates that the recently completed demonstration at TCM, along with future projects, will facilitate further advancements in the field of CO2 capture and deployment of ION’s technology.
1. Introduction
Many research organizations and companies are developing and investigating carbon capture technologies to reduce the quantity of CO2 emitted into the atmosphere from industrial emissions. The increased CO2 levels in the atmosphere are attributed mainly to emissions from large point sources including fossil fuel power generation and other industrial facilities. Solvent-based CO2 capture technologies that interface with flue gas are most common for post-combustion processes and represent the most promising technology for retrofitting existing power plants.
Throughout small-scale pilot testing with coal and natural gas-fired flue gas, bench-scale pilot and laboratory testing with ION’s proprietary solvent, ION has consistently demonstrated significant reductions in regeneration energy requirements in comparison to traditional aqueous mono-ethanolamine (MEA). This reduction is directly correlated to ION’s physiochemical solvent characteristics, which include higher carrying capacity, a lower specific heat capacity, and advanced process design.
ION is rapidly developing its technology by leveraging existing facilities with several global and local partners. In 2013, ION completed a proof-of-principle campaign at the University of North Dakota Energy & Environmental Research Center (EERC) at the 0.25 MWe scale, testing on both coal and natural gas-fired flue gas.1,2 In 2015, ION collaborated with Southern Company to perform parametric and steady-state operations at the National Carbon Capture Center’s Pilot Solvent Test Unit (NCCC, PSTU), a 0.5 MWe coal-fired post-combustion testing facility located in Wilsonville, Alabama, USA.3-6
Following the successful campaign at the NCCC, ION tested its solvent in the Amine Plant at CO2 Technology Centre Mongstad (TCM). This TCM facility provides an absorber-stripper configuration for amine-based technologies to test carbon capture from a slipstream of flue gas from either a natural gas-fired combined heat and power (CHP) plant or residue fluid catalytic cracker (RFCC). TCM is currently the largest facility for advanced testing of CO2 capture technologies in the world. Carbon capture technologies demonstrated at TCM can readily be scaled up to commercial industry levels.
1.1 CO2 Technology Centre Mongstad
Before ION’s test campaign at TCM, TCM executed two separate campaigns to baseline the Amine Plant utilizing a 30 wt-% MEA capture solvent on flue gas from the CHP plant. In 2014, the baseline campaign utilized 3.5% CO2 concentration in the flue gas, flowing at 47,000 Sm3/hr and targeted 90% capture efficiency. The resulting SRD from the optimization of run conditions was 4.1 MJ/kg CO2,7 which was independently validated by Electric Power Research Institute (EPRI).
In 2015, the baseline campaign was repeated to demonstrate improved performance due to the incorporation of antifoam into the 30 wt-% MEA solvent. The need for antifoam became apparent after reviewing the data from the previous baseline campaign, where the stripper temperatures and pressures were very erratic, indicating foaming. The flue gas was still 3.5% CO2 with a flow rate of 60,000 Sm3/hr and achieved a capture efficiency of 83.4%. Under these conditions, and with antifoam addition to the solvent, the SRD was 3.62 MJ/kg CO2, which is now considered as the baseline case moving forward.8,9
1.2 ION’s Test Campaign at TCM
The ION test campaign at TCM was divided into two consecutive campaigns. The first campaign involved testing on flue gas from the adjacent natural-gas fired CHP plant. The second campaign was testing with RFCC flue gas, which closely approximates the composition of coal-fired flue gas. Fig. 1 shows the primary constituents of each of the flue gases available at TCM.8
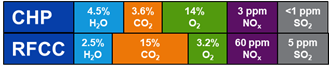
Fig. 1. Comparison of flue gas composition between CHP and RFCC sources.
The Amine Plant at TCM has the capability to recycle captured CO2 back into the flue gas to increase the CO2 concentration in CHP flue gas from 3.6 vol-% up to 14 vol-%. Similarly, the RFCC flue gas can be diluted with air to drop the CO2 concentration from 15% down to 4%.8 With this flexibility, the CO2 concentration of either flue gas can be adjusted to a value that closely approximates flue gas from a coal-fired power plant (ION typically uses 12.5 vol-% when simulating flue gas from a coal-fired power plant). The benefit of using CHP flue gas for amine-based carbon capture is that the NOx and SO2 concentrations are lower and do not contaminate the solvent. The RFCC flue gas more closely approximates coal-fired flue gas, not only in CO2 but also in O2, NOx, and SO2. The primary difference between RFCC flue gas at TCM and flue gas from coal plants is the lack of fly-ash and the presence of sulfuric acid mists or aerosols. Once TCM installed and commissioned a Brownian Demister later in ION’s campaign to address aerosol inflow, the RFCC gas at TCM was an excellent representation of coal-derived flue gas.
Beginning the testing campaign with CHP gas in October 2016, ION tested flue gas with a CO2 concentration of 4 vol-% and gradually worked up to 12.5 vol-%, using captured CO2 recycle, in preparation for testing with the RFCC flue gas by February 2017. ION classified the capture efficiency, specific reboiler duty, and optimal L/G as primary performance metrics and they were all studied during both the CHP and the RFCC campaigns. Also, secondary performance indicators of emissions, breakdown rates, and solvent make-up rates were studied during both campaigns. ION’s CHP campaign lasted from mid-October 2016 until mid-February 2017. The RFCC campaign immediately then began and concluded at the end of April 2017. The solvent was changed out at the start of the RFCC campaign to evaluate the above-mentioned secondary metrics based on the same starting conditions of the solvent.
1.3 Process Description
Fig. 2 shows the process flow diagram for the TCM Amine Plant.8 The flue gas has a specified capacity and minimum turndown of 67,200 Sm3/hr, and 25,000 Sm3/hr, respectively, for the portion of the testing using the CHP plant as the feed source for the flue gas. The ION testing on CHP flue gas testing utilized a gas flow rate of 50,000 Sm3/hr. The flue gas feed used for the RFCC campaign was supplied by the refinery and has a specific capacity and minimum turndown of 60,000 Sm3/hr and 20,000 Sm3/hr, respectively. After the installation of the BD filter, the maximum gas flow rate from the refinery was about 37,000 Sm3/hr, and ION typically used a flow of 35,000 Sm3/hr. The Direct Contact Coolers (DCC) for each flue gas source were used to cool the incoming flue gas down to the target of 20-25 °C and saturate the flue gas with water vapor. This is typical conditioning of the flue gas prior to introduction into the absorber column. The absorber is a rectangular polypropylene-lined concrete column with a cross- section of 3.55 m x 2.00 m and a height of 62 meters (m). The amine-flue gas contact area in the absorber consists of three beds of stainless-steel (SS) structured packing with a total height of 24 m across three beds, where the lower bed has a height of 12 m, and the middle and upper are both 6 m tall. ION ran experiments utilizing various amounts of packing height throughout the test campaign.9
Above the upper part of the absorber section, two water wash sections are installed with the purpose to remove any carryover solvent vapors prior to venting to the atmosphere. Both of the water washes consist of a 3 m section of SS structured packing and were also used to maintain the water balance in the system by adjusting the circulating water temperature of the upper and lower water-wash sections as the scrubbed flue gas exits the column.9 While the lower water-wash was always operated as a typical water wash system, the upper water wash had the flexibility to be operated as either a water wash section or as an acid wash for the tests presented in this paper. The option of adding acid to the upper wash section at TCM enables technology developers to neutralize any solvent vapors to keep emissions below the acceptable limits established by TCM. The consequence of utilizing the upper wash section as an acid wash, however, is that any amine emissions captured cannot be returned back to the system which directly affects the solvent make-up rates. It is therefore desirable to test the effectiveness and need for an acid wash during the campaign but to strive for a twofold water wash system during normal operation.
ION installed two Multi-component Liquid Analyzers (MLA), one on each of the rich and lean solvent streams (not shown in Fig. 2.) in order to monitor near real-time solvent composition. The data from the MLA was used to add makeup solvent and maintain a stable water balance. Additionally, the MLA provided CO2 loading information about the solvent and process changes could be evaluated in near real-time, thereby providing critical information on reaching steady-state operation.10 The rich solvent then passes through a liquid-liquid heat exchanger to the regeneration side of the process. This heat exchanger transfers heat from the hot, lean solvent into the cold CO2-rich solvent, often referred to as the lean-rich cross exchanger. TCM has two stripper/reboiler systems (CHP and RFCC) available to recover the captured CO2 and return CO2-lean solvent back to the absorber. The CHP stripper was designed to process the amount of CO2 that is generally captured from a flue gas containing 3.5-6% CO2.
The larger RFCC stripper/reboiler was used to recover the captured CO2 and return CO2-lean solvent back to the absorber when testing was performed on flue gas with CO2 content above 6 vol-% (CHP + recycled CO2, or RFCC with and without air dilution).
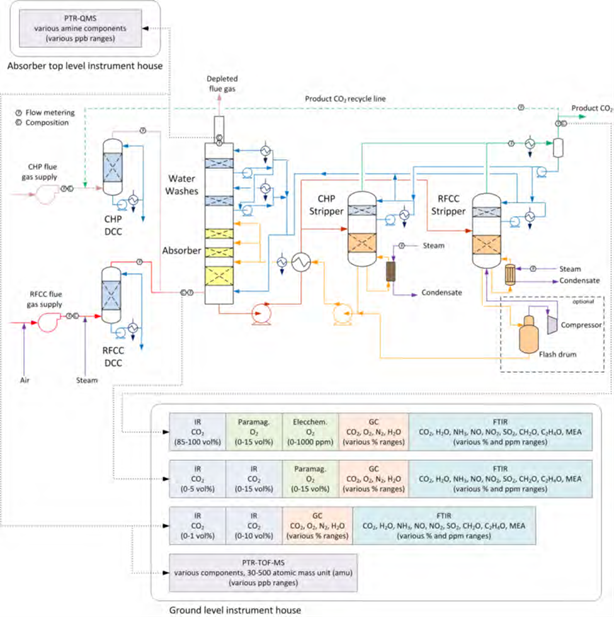
Fig. 2. The TCM amine plant with two flue gas sources, CHP and RFCC, and the corresponding two strippers. Flue gas analysers and flow meters are located at absorber inlet (I), outlet/depleted flue gas (II) and CO2 product (III). The dotted green line shows that CO2 can be recycled back to the absorber inlet for tests at elevated CO2 concentration in the flue gas flow. (Figure from Gjernes et al., Procedia GHGT-13, 2017).
Aside from the water washes on the absorber column, and the DCCs, there were two other processes that used cooling water. The overhead condenser, located on a common line that was shared by the CHP and RFCC strippers, was used to knock down the water content of the CO2 product gas. This was typically operated to cool the product gas to around 20 °C. Additionally, a trim cooler was present after the lean-rich cross exchanger which allowed for control of the solvent temperature entering the absorber.
2. Results and Discussion
2.1 CHP Campaign
ION has made definite conclusions from the data obtained from this campaign. Namely, ION’s solvent outperformed TCM’s MEA base cases7,9 which are summarized in Table 1, in a facility not optimized for ION’s solvent.
During a parametric study using CHP flue gas, the best-case achieved by ION at 3.5 vol-% CO2 was 3.37 MJ/kg CO2 with 50,000 Sm3/hr flue gas flow rate. This represents a reduction of approximately 10% in steam energy compared to the base MEA case at TCM (3.62 MJ/kg CO2),9 and was achieved without the need for additives to control foaming.
MEA (2014) | MEA (2015) | MEA + Antifoam (2015) | ION (2016) | |
CO2 Concentration, % | 3.6 | 3.6 | 3.6 | 3.5 |
Capture, % | 90.0 | 83.5 | 87.4 | 91.8 |
SRD, MJ/kg CO2 | 4.10 | 3.90 | 3.62 | 3.37 |
Table 1 – Comparison of ION CHP results at 3.5% CO2 to MEA base cases at TCM.
By adjusting the flow rate of already-captured CO2 from the stripper column and routing it to the inlet of the absorber, ION obtained testing conditions of four intermediate CO2 concentrations in the flue gas while working the CO2 concentration up to mimic what would be expected at a coal-fired power plant (11-15%). With 6.1% CO2 in a 50,000 Sm3/hr flue gas flow, the lowest SRD demonstrated was 3.24 MJ/kg CO2. Increasing the concentration up to 9.2% CO2 in the flue gas resulted in an SRD of 3.23 MJ/kg CO2. The final step up to 13.1% CO2 in the flue gas resulted in an SRD of 3.33 MJ/kg CO2. At the time of preparing this paper, there are no known published MEA baseline cases at elevated CO2 concentrations against which to compare these results. Also, these results do not represent the optimal run conditions for each CO2 concentration tested, as no optimization experiments were conducted.
Table 2 shows the key performance indicators (KPI) for a select group of tests that were executed during the CHP campaign. Each of the work packages listed in the table, apart from Aged-0, show the best-operating conditions at each of the CO2 concentrations utilized during the CHP campaign with respect to the SRD. Further optimization at each of the flue gas concentrations would likely have resulted in better performance. The test marked as Aged-0 was conducted using CHP gas but after the RFCC campaign had concluded; therefore, the experiment was performed with an aged solvent. This test was performed as a repeat of Base-0 but using the aged solvent (where Base-0 was taken on near virgin solvent). The results from Base-0 and Aged-0 can be compared to the MEA based case performed at TCM, where the SRD was determined to be 3.62 MJ/kg CO2 during the 2015 TCM baseline campaign. The water and lean CO2 content of the solvent were constant in the two experiments, meaning the active components were reduced in content by the number of breakdown products in the solvent. The results of this last test, compared to those of Base- 0, show the presence of the breakdown products in the solvent resulted in a 5% decrease in performance.
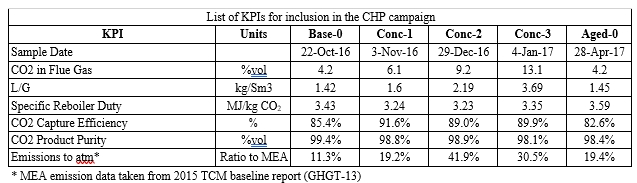
Table 2 – Table of operating conditions and resulting KPI of crucial tests performed during the CHP campaign. Base-0 test conditions are with pure ION solvent and should be compared with the Aged-0 test.
Emissions were relatively low during the CHP campaign when testing on flue gas with low CO2 concentrations (3.5-6.0 vol-%). However, when the CO2 concentration was increased towards 13 vol-%, the maximum absorber temperature increased; the higher temperature in the absorber resulted in greater evaporative solvent losses, which contributed to slightly higher emissions.
Table 3 compares the solvent and breakdown product emissions from ION’s CHP campaign with the 2015 TCM MEA campaign.8 The table demonstrates the emissions of one CO2 concentration of the inlet flue gas for MEA and compares it to four different CO2 concentrations of the inlet flue gas for ION’s campaign. The ION solvent results compare very favourably with the MEA base case’s total emissions (solvent and breakdown) of 20.8 ppm when utilized under similar and more aggressive operating conditions.

Table 3. CHP emission comparison to the TCM MEA campaign.
2.2 RFCC Campaign
The ION campaign using RFCC flue gas was performed while mixing air with the flue gas to achieve a stable CO2 concentration of 12.5 vol-%. As a result of air mixing the O2 concentration increased from 4.5 vol-% of the raw RFCC gas to 7.0 vol-%. The solvent used in the CHP campaign was removed, and the RFCC campaign proceeded with a pure solvent in the system. The solvent change-out allowed for distinguishing solvent breakdown products, solvent make-up rates, and emission effects between the two flue gas sources (see Fig. 1). ION’s RFCC campaign began on February 20, 2017, immediately following the successful demonstration of 90% capture of CO2 from CHP (+ recycle) flue gas at 13.1 vol-% CO2 concentration. Due to emission issues, in the absence of the BD filter, TCM had never operated with RFCC gas for prolonged periods of time before ION’s campaign, and as such at the time of this paper’s submission there is no baseline to compare ION’s results to on RFCC flue gas.
Table 4 shows the KPIs for select tests performed during the RFCC campaign. The Base-0 test was part of a U- curve series of tests and represented the minimum SRD. This condition was repeated March 4-6, 2017 (Base-1), and again March 14-16, 2017 (Base-2), to build up run times under these conditions and evaluate the reproducibility of the results. The three EPRI tests are the second series of tests that were conducted for several days under constant operating conditions. The EPRI tests were conducted when EPRI was on site to provide third-party verification of testing procedures, telemetry, and lab analysis.
The remaining tests included in Table 4 are “Low SRD”, which is the test that achieved the lowest SRD of all the tests conditions performed during the RFCC campaign. The operating conditions that were established in “Low SRD were repeated in the EPRI tests. Finally, test “Conc-1” was included in the list of main experiments as it was the non- optimized removal for flue gas with 14.5 vol-% CO2 concentration.

Table 4 – Table of operating conditions and resulting KPI of key tests performed during the RFCC campaign.
All of the testing during ION’s RFCC campaign was carried out with 18 m of packing in the absorber column. The consequence of using 18 m instead of 24 m of packing is that the residence time of the solvent in the absorber is lower, leading to higher lean flow rates for similar capture efficiencies. With the utilization of more packing, the flow rate would have been reduced to achieve the same residence time, and the energy lost to heating solvent in the stripper would be reduced per tCO2 captured. However, a benefit of minimizing packing height is a reduction in capital expenditures.
ION completed an extensive set of parametric tests during the RFCC campaign. The results of these tests have demonstrated the optimum L/G for obtaining low SRDs. The best SRD achieved was 3.25 MJ/kg CO2, which was achieved at the highest tested operating pressure in the stripper. Operating at this higher pressure required more steam to the stripper sump, where the stripper sump temperature also increased. Reducing the pressure of the stripper led to higher water vapor losses and, as expected, an increase in SRD.
Typically, during the RFCC campaign where the CO2 concentration was 12.5 vol-%, the maximum absorber temperature increased up to 78 °C, which is the maximum temperature recorded during the entire ION test campaign. This higher temperature in the absorber resulted in greater vapor-liquid equilibrium (VLE) losses, which contributed to higher emissions passing through the water washes and leaving the absorber stack. Consequently, the acid wash was utilized briefly in the RFCC campaign to assist in reducing emissions until operational controls could be determined that assisted in maintaining low emissions.
The RFCC campaign started up on Feb 21, 2017, and ran through April 28, 2017, where the Amine Plant was available for testing to ION for 1,346 hours of 1,427 hours. ION was successfully testing for 1,222 hours; there were stoppages of 7 hours due to emissions, and planned stoppages for 115 hours for process changes. These durations led to an on-stream factor of 99.3% when taking into account only issues related to the use of ION’s proprietary solvent.
2.3 U-curves/SRD
Optimization experiments were conducted in both the CHP and RFCC campaigns to determine the run conditions at which the best energetics could be achieved for each flue gas. Fig. 3 shows the results of two of these optimization curves where the CHP flue gas at 4.0 vol-% CO2 and RFCC flue gas at 12.5 vol-% CO2. The CHP data was acquired using the smaller CHP stripper. The final difference between the two sets is that the RFCC testing was performed at 35,000 Sm3/hr gas flow rate, which is lower than the 50,000 Sm3/hr flow rate used for CHP testing. The slower flow rate leads to more residence time in the absorber and improves the capture of CO2 by the solvent.
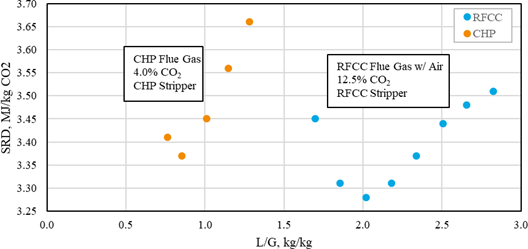
Fig. 3. – U-curves generated for CHP flue gas and RFCC flue gas.
ION conducted a test to evaluate various capture efficiencies with fixed L/G, while only changing the steam flow to the reboiler heat exchanger (HEX). This test included operating conditions where the CO2 capture efficiency was increased up to 98% in order to evaluate the cost of high capture rates. In Fig. 4 below, each point is increased stripper sump temperature (while holding all other parameters nearly constant) and the results of SRD and capture efficiency are plotted connecting the increasing sump temperatures. The capture efficiency increases by increasing the carrying capacity of the solvent (further leaning the solvent at the higher temperature). Simultaneously, the variation of SRD for each sump temperature suggests that there is an optimum capture efficiency at a particular L/G that reduces the steam flow rate to the system; the optimum capture rate is around 85% in this example. The higher SRD at the lower temperatures (left side of the graph below) is due to the energy losses associated with the penalty of re-heating the solvent at the fixed solvent flow rate. Just like the traditional U-curve plots, this data demonstrates the optimal capture efficiency (and required SST) for a particular L/G. Although not every data point is the result of an optimized setting the graph indicates that for ION’s solvent when the capture efficiency is increased from 90% to 98%, there is only about 10% increase in SRD.

Fig. 4. – Plot of SRD as a function of capture efficiency while increasing steam flow to the reboiler (increasing the SST) and holding L/G constant (i.e., a hockey stick plot).
2.4 Solvent Composition
The evaluation of the heat stable salts (HSS) formation rates in the solvent can provide information on the dominant degradation pathways for both the CHP and RFCC campaigns. The concentrations are plotted against the total CO2 captured by the solvent in each of the campaigns. Fig. 5 shows the results of the solvent analysis on four individual HSS throughout both campaigns: Oxidation Products 1, 2, 3, and nitrate. The data were evaluated with the expectation that the CHP campaign would show more oxidative degradation than the RFCC campaign due to the higher O2 concentration in the CHP flue gas.
Starting with Oxidation Product 1 in Fig. 5, the formation rate as a function of tonnes of CO2 captured is very similar for both the CHP and RFCC flue gas sources, where the accumulation of Oxidation Product 1 is slightly higher with the RFCC flue gas. Oxidation Product 2 show a significantly higher accumulation rate (relative to the amount of CO2 captured) during the CHP campaign where the oxygen content in the flue gas is two to three times higher than that of the RFCC flue gas. Oxidation product 2 is an oxidative decomposition product of the solvent and can thermally decompose to Oxidation Product 3 and CO2. Therefore, it makes sense that the accumulation of oxidation product 3 increases at a faster rate in the CHP campaign where there is more Oxidation Product 2. Finally, the nitrate comparison is shown in Fig. 5. The NOx concentration in the CHP flue gas is significantly lower (<5ppm)8 than what is present in the RFCC flue gas (60ppm)8 and the two charts show the effect of the higher concentration. A percentage of NOx is captured by the solvent, and the end products are nitrate HSS; thus, as was expected, the nitrate HSS values are elevated in the RFCC results.
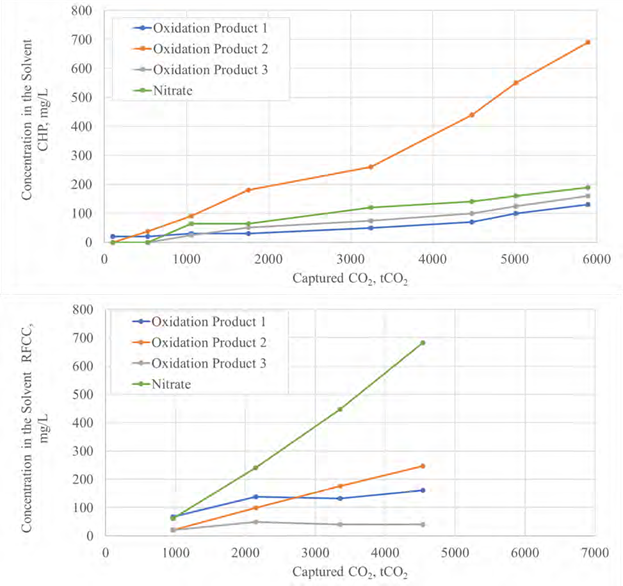
Fig. 5. HSS formation for the CHP (top) and RFCC (bottom) campaigns as a function of total CO2 captured.
2.5 Corrosion Coupon Analysis
TCM installed several corrosion coupons into the system to evaluate the ION solvent’s impact on typical industrial materials. The coupons were installed at two locations: one in the rich stream, just after the LRXC on the stripper side (hot rich solvent) and the second one was in the lean stream, just prior to the LRXC (hot lean solvent). Table 5 shows the results from this corrosion study.
The corrosion coupons were installed prior to the start of testing and left in place throughout the entire ION test campaign (including down times and periods where TCM was upgrading the system). They were removed after the campaign and evaluated to determine weight loss of the materials. As can be seen in Table 5, the carbon steels tested, S235 carbon steel (similar to C1010 carbon steel) and A106 Gr B (pipe grade carbon steel) had no remaining coupons at the conclusion of the testing in either installed location. By way of comparison, ION also utilized a carbon steel coupon in the NCCC test campaign of a very similar variety to S235 (C1010). and has included those results for comparison in Table 5.
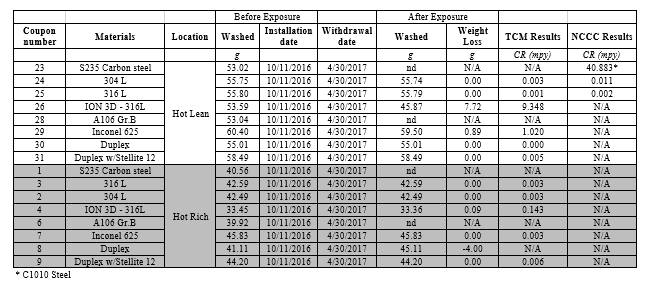
Two other samples were evaluated at TCM that can directly be compared to the results obtained during the NCCC test campaign. The 304L and 316L samples in the hot lean solvent showed similar low corrosion rates similar to what was seen at NCCC. The other alloys tested with coupons include Inconel 625, and two Duplex coupons. The Inconel alloy had a corrosion rate (CR) of 1.0 mils/yr in the hot lean solvent and an insignificantly small CR in the hot rich solvent. The Duplex coupon, which is the material used in constructing the Amine Plant, also showed little to no corrosion.
In addition to these standard materials, ION provided four unique coupons (labelled as ION 3D – 316L in Table 5) which were 3D printed by Lawrence Livermore National Laboratory (LLNL) using 316L stainless steel material. Fig. 6 shows the images of the 3D printed coupons provided by LLNL, where a single print job was used to create the coupons, that were cut into slices according to the dimensions required for insertion into coupon holder at TCM. Only two coupons were used in the campaign, and both coupons had a portion of the surface printed as a textured lattice seen in Fig. 6. ION is investigating 3D printed materials for possible use in future development work.
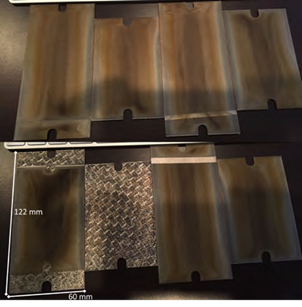
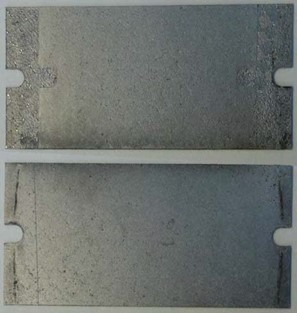
Fig. 7. – 3D printed coupon made of 316L stainless steel. This coupon was installed in the hot lean solvent line. These photos show the front and back of the coupon after exposure to the solvent throughout the ION test campaign.
As can be seen in Fig. 7, the 3D printed coupon installed on the hot lean solvent flow showed appreciable corrosion, with a CR of 9.4 mils/yr. The stock 316L coupon showed no corrosion under the same conditions (see results in Table 5). This supports the concern that the more porous 3D printed material is subject to advanced corrosion rates when exposed to hot lean solvent. Fig. 7 shows the hot-lean coupon after the ION test campaign, where the texture at the ends of the coupon has evidently been reduced. The porosity of the coupon can also be more easily seen in this figure. The data for the coupon in the hot rich solvent indicates that this location in the process is not as corrosive as the hot lean location. There is still a measurable loss of material (CR = 0.1 mils/yr), but it is two orders of magnitude smaller than the hot lean location. Fig. 8 shows the images of the coupon installed in the hot rich solvent and, unlike the hot lean location, the coupon appears very near the original condition. Additional exposure of these coupons at other locations in the Amine Plant will aid in determining if this material is suitable for use in an amine-based carbon capture plant.
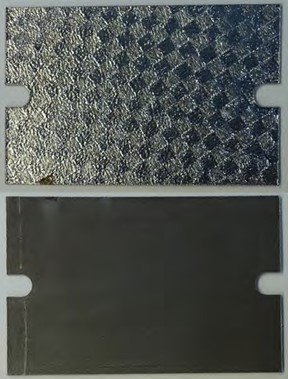
Fig. 8. – 3D printed coupon made of 316L stainless steel. This coupon was installed in the hot rich solvent line. These photos show the front and back of the coupon after exposure to the solvent throughout the ION test campaign.
2.6 Process Model Validation
One of the key benefits of testing at TCM is to obtain the telemetry and key performance indicators from steady state operations can be used to validate ION’s process model. The validation of this process model is more important in advancing the case for a commercial system based on ION’s advanced solvent than the demonstrated test results on TCM’s 12 MWe pilot plant.
The empirical results from testing on an existing plant, where only minor modifications were implemented when incorporating ION’s advanced solvent, will not yield the energy savings that have been shown in the ION optimized design process model. The primary obstacle in achieving the low SRDs is that there is not enough capability in the stripper to prevent excess energy (via steam) from leaving the stripper to the condenser. For ION’s high carrying capacity solvent, a cold-rich bypass (CRB) strategy is needed to keep the energy in the system.11 Additionally, TCM does not currently have the capability for solvent cooling in the absorber via an inter-stage cooling system. This cooling increases the uptake of the CO2 in the absorber, and further increases the carrying capacity of the solvent.
ION has built a model of the TCM process in ProTreat® and modeled the capture processes using the same parameters that were tested in the field.12 The following section demonstrates how the test results at TCM were compared against the results from the process model, in order to verify the accuracy of the model and build confidence that a custom-built plant would achieve the designed performance of below 2.4 MJ/kg CO2.
During the TCM campaign, ION tested over 150 operating configurations with 76 of those configurations being on RFCC flue gas. The scatter plots in Fig. 8 show the diversity of operating conditions that ION covered in the RFCC test campaign. ION selected 51 random operating conditions to simulate in ProTreat® to generate model results for comparison. In Fig. 9 are highlighted markers (orange) indicating the operating conditions of the 11 experiments that were used to generate a parity plot shown in Fig. 10. These 11 experiments were selected to cover a wide range of testing conditions and Fig. 10 shows the resulting parity plot, where the results of the model are compared to the empirical data. The ProTreat® process model successfully predicts the key parameters such as densities, capture rate, SRD, working capacity, and stripper sump temperature. From these results, the data has demonstrated how well the actual and modeled results converge over this wide range of operating conditions. This allows ION to incorporate its custom process operations and confidently design commercial plants that provide significant cost-savings that are required for commercial deployment.
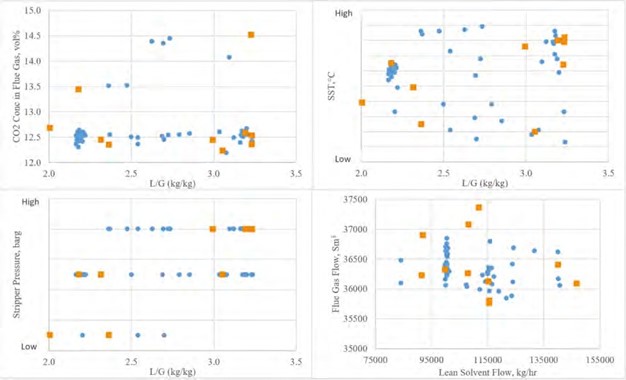
Fig. 9. – Scatter plots showing the range of variables tested on RFCC flue gas. The orange markers represent the 11 experiments that are used to generate the parity plot.
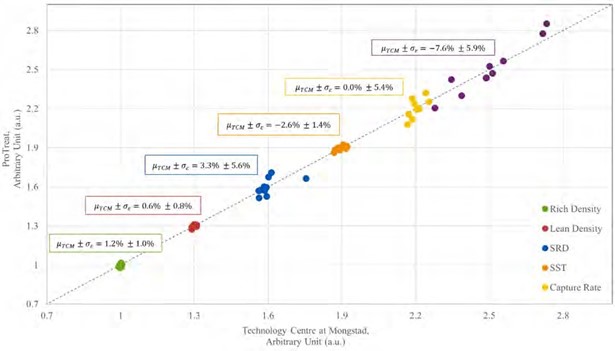
3. Conclusions
3.1 ION’s Campaign Conclusions
ION is very encouraged by the results of both the CHP and RFCC campaigns executed at TCM. The following are the main findings from the more than 2,750 hours of operation, where 150 test settings led to capturing well over 14,000 tCO2.
Specific Reboiler Duty:
The CHP campaign concluded with optimization testing in April 2017 with aged ION solvent and found that under optimal operating conditions the best achieved specific reboiler duty (SRD) was 3.37 MJ/kg CO2 for scrubbing
4.0 vol-% CO2 flue gas. This represents a reduction of 15% in steam energy compared to the base case of MEA without anti-foam at TCM (3.9 MJ/kgCO2) and approximately 10% when compared to the base case of MEA with anti-foam (3.62 MJ/kgCO2). ION’s results were achieved without the need for additives to control foaming.
The RFCC campaign produced a low SRD of 3.25 MJ/kg CO2 when scrubbing 12.5 vol-% CO2 flue gas after optimization of operating parameters. At the time of this reporting, TCM has yet to publish MEA baseline testing on RFCC flue gas that might be used for comparison.
Process Model Validation:
ION has concluded from the results at TCM that its module in the ProTreat® process model accurately predicts the performance of its solvent over a wide operating window. A close investigation of the rich and lean loadings indicates a slight underprediction of the working capacity, and these findings have led ION to conclude that its commercial- scale plant designs provided conservative estimates of actual plant performance; the current ProTreat® model resulted in process designs with an energy consumption of 2.4 MJ/kgCO2.
Material compatibility:
The corrosion coupon analysis showed that carbon steel coupons installed in the process (both rich and lean locations) were not recovered, which indicates high corrosion rate of these materials. The 304L and 316L stainless steel, as well as the Duplex and Inconel specialty metals all had acceptable corrosion rates (<0.01 mils/yr). The only degradation occurring was noticeable on the Inconel coupon in the hot lean solvent (~1 mils/yr).
MLA Performance:
ION implemented an online liquid monitoring system for real-time analysis of solvent, water, and CO2. Overall, the MLA performed excellently with precise detection of near-real-time trends, where changes with increments of
0.5 wt-% could be observed. With these promising results in the initial pilot release, ION believes the MLA to be a useful and vital tool for both monitoring liquid compositions as well as providing a mechanism to automate and optimize the control of CO2 capture processes.
3.2 Concluding Statement
ION has conducted a thoughtful, comprehensive, and successful campaign in close collaboration with TCM. CO2 was successfully removed and captured for extended periods of time from CHP as well as RFCC gas. Throughout pilot testing, ION has confirmed its understanding of process improvements and analytics that will enable successful operation at significantly lower L/G circulation rates, packing heights and regeneration energies than MEA. ION’s process design tool has been validated to a high accuracy that allows ION to incorporate its custom process operations. ION anticipates that the recently completed demonstration at TCM, along with future projects, will directly impact the state-of-the-art of CO2 solvent technologies and facilitate advancement of CO2 capture towards commercialization and widespread implementation of ION technology.
Acknowledgments
This material is based upon work supported by the U.S. Department of Energy National Energy Technology Laboratory (DOE-NETL) under cooperative award number DE-FE0013303. ION would also like to wholeheartedly thank the teams at TCM and their stakeholders for their hospitality and support throughout ION’s campaign. LLNL is kindly acknowledged for providing 3D-printed coupons for corrosion testing.
References
- Brown A, Brown N, Heller G, Staab G, Silverman T, Kupfer R, Brown R. Evaluating the Impact of ION’s CO2 Capture Technology on a Sub-Critical Pulverized Coal Power Plant, EUEC Conference Proceedings, NM, USA; 2014
- Brown N, Heller G, Staab G, Silverman T, Kupfer R, Brown R, Brown A. ION Advanced Solvent System for CO2 Capture, DOE-NETL CO2 Capture Technology Project Review Meeting, Conference Proceedings, PA, USA; 2014.
- Brown N, Heller G, Staab G, Silverman T, Kupfer R, Brown R, Brown A. Novel advanced solvent-based carbon capture pilot demonstration at the National Carbon Capture Center, Energy Procedia 2017; 114:1075-1086.
- Meuleman E, Brown N, Panaccione C, Staab G, Silverman T, Heller G, Brown A. Novel Advanced Solvent-based CO2 Capture Pilot Plant demonstration; ION at NCCC, The 41st International Technical Conference on Clean Coal & Fuel Systems, Clearwater FL; 2016.
- Meuleman E, Brown N, Panaccione C, Staab G, Silverman T, Heller G, Brown A. Novel Advanced Solvent-based CO2 Capture Pilot Demonstration – Fast-tracking the development & scale-up, ECI CO2 Summit II: Technologies & Opportunities, Santa Ana Pueblo, NM; 2016.
- Meuleman E, Silverman T, Staab G, Heller G, Brown N, Brown R, Kupfer R, Atcheson J, Brown A. ION Advanced Solvent CO2 Capture Pilot Project, DOE-NETL CO2 Capture Technology Project Review Meeting, Conference Proceedings, PA, USA; 2016.
- Hamborg ES, et al. Results from MEA testing at the CO2 Technology Centre Mongstad. Part II: Verification of baseline results. GHGT-12, Energy Procedia 2014; 63:5994-6011.
- Morken AK, Pedersen S, et al. Degradation and Emission Results of Amine Plant Operations from MEA Testing at the CO2 Technology Centre Mongstad, GHGT-13, Energy Procedia 2017; 114:1245-1262.
- Gjernes E, et al. Results from 30 wt% MEA performance testing at the CO2 Technology Centre Mongstad. GHGT-14, Energy Procedia 2017; 114:1146-1157.
- Panaccione C, Staab G, Awtry A, Kupfer R, Silverman T, Brown R, Atcheson J, Meuleman E, Brown A. Multi-component liquid analyser during steady-state and dynamic CO2 capture operations: Near real-time feedback in industrialized environment, GHGT-14 Proceedings, Melbourne, Australia; 2018
- Cousins A, et al. Model verification and evaluation of the rich-split process modification at an Australian-based post-combustion CO2 capture pilot plant, Greenhouse Gas Sci Technol. 2012; 2:329-345.
- Brown N, Staab G, Silverman T, Heller G, Kupfer R, Panaccione C, Brown A. ProTreat® simulation accurately represents experimental results for post-combustion carbon dioxide capture with novel mixed amine solvent in real process environment, Energy Procedia 2017; 114:1380- 1387.
CO2 capture from RFCC flue gas with 30 wt% MEA at Technology Centre Mongstad, process optimization and performance comparison (2018)
Muhammad Ismail Shaha*, Gerard Lombardob, Berit Foståsc, Christophe Benquetd, Anne Kolstad Morkena, Thomas de Cazenovea
aTechnology Centre Mongstad, 5954 Mongstad, Norway bGassnova SF, Dokkvegen 10, 3920 Porsgrunn, Norway cEquinor ASA, PO Box 8500, 4035 Stavanger, Norway dTotal E&P Norge, Finnestadveien 44, Dusavik, 4029 Stavanger, Norway
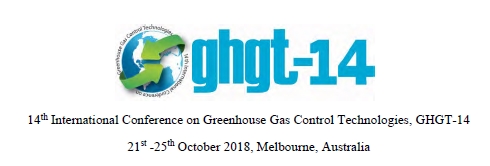
Abstract
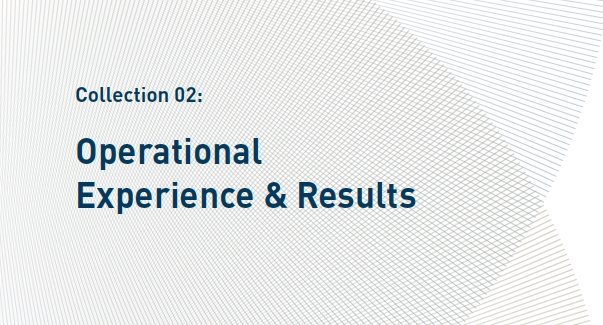
Aerosol based amine emission from post combustion carbon capture process is very challenging in terms of accurate online measurement, compliance to emission permit and operating cost due to high solvent makeup. At Technology Centre Mongstad (TCM), an advanced process configuration is developed and tested to control and reduce amine emissions in parallel to accurately measure MEA emissions by online FTIR. The advanced configuration consists of a Brownian diffusion filter upstream the absorber, RFCC water wash, special design and operation of online sampling system and a fractional cold rich amine bypass to the stripper. With the flue gas from the Residue fluidized catalytic cracker (RFCC), promising results are achieved by applying the advanced process configuration. MEA emissions are reduced to about 2 ppm and specific reboiler duty of 3.5 GJ/ton CO2 is demonstrated with a capture rate of about 90%.
1. Introduction
The Technology Centre Mongstad (TCM) is the world’s leading facility for verifying and improving CO2 capture technologies. TCM is located at Mongstad, one of Norway´s most complex industrial facilities. TCM has been operating since autumn 2012, providing an arena for qualification of CO2 capture technologies on an industrial scale. In autumn 2017, Gassnova (on behalf of the Norwegian state), Equinor (formerly Statoil), Shell and Total entered into a new ownership agreement securing operations at TCM until 2020. The owners of TCM started their most recent monoethanolamine (MEA) test campaign in June 2017 where a large number of public, industrial, research and academic stakeholders were involved [1]. The campaign included demonstration of a model-based control system, dynamic operation of the amine plant, investigating amine aerosol emissions and specific tests targeted at reducing the specific cost of CO2 capture. Through the testing, both flue gas sources currently available at TCM were used. These sources are the combined cycle gas turbine (CCGT) based heat and power plant (CHP) and the residue fluidized catalytic cracker (RFCC). They provide flue gases with a wide range of properties and CO2 content from 3.6 to 14 vol%. TCM is located next to the Equinor refinery in Mongstad. The Mongstad refinery is the source of both flue gases supplied to TCM.
Until 2017, TCM had not been able to operate the amine plant with RFCC flue gas due to very high amine emissions (> 20 ppmv) caused by sulfuric acid aerosol and dust particles present in the flue gas [2]. By installation of a Brownian diffusion (BD) filter upstream the absorber, more than 95% of the aerosol were removed and together with optimization of plant process parameters and configuration, the amine emissions were reduced to levels well below TCM’s emission permit (< 6 ppmv for amines.) this allowed for long term testing with RFCC flue gas in the amine plant.
TCM participated in the Climit Demo project AeroSolve (616125) that was led by SINTEF with NTNU, Uniper, Engie, TNO and the Road project as partners. The project aimed to close knowledge gaps related to aerosol emissions from CO2 capture plants whereas a part of the project TCM conducted a 3 months test campaign treating the RFCC flue gas with MEA under “work package 4” of the project (Testing at industrial demo scale). Based on the learnings gained through this campaign, TCM optimized and modified process configurations and online emission sampling system followed by further testing with the RFCC flue gas and MEA under MEA-4 campaign during Q2- 2018. The conventional amine process configuration was modified to an advanced amine process configuration which is able to efficiently capture CO2 from flue gases containing aerosol, and the sampling system was modified to accurately and reliably measure amine aerosol. Description of the sampling system, optimal TCM amine plant process configuration to minimize aerosol emissions and specific reboiler duty as main results from testing, is presented in the current paper.
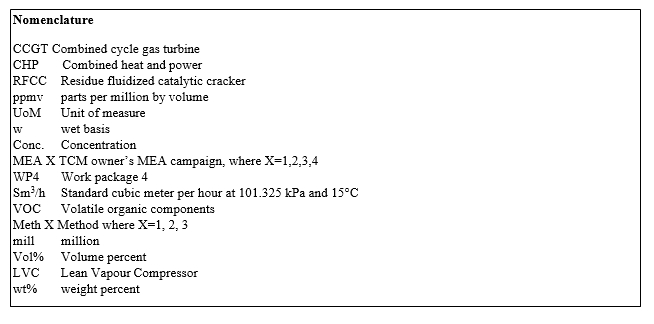
2. TCM’s experience with Aerosol based emissions and its control
TCM is regulated under emission permit from the Norwegian environmental authority (Miljødirektoratet). The emission permit regulates amine plant’s emissions to air of ammonia (NH3), Amines (primary, secondary and tertiary) and aldehydes. Table 1 given below shows the allowable emission limits applicable to the amine plant.
Emission component | Emission source | Emission limits | |
Daily average concentration limit | Yearly limit(kg/year) | ||
Ammonia (NH3) | Amine plant | 100 ppmv | 6,000 |
Total Amines | Amine plant | 6 ppmv* | 2,800 |
Total Aldehydes | Amine plant | 1 g/s |
Table 1. TCM Amine plant applicable emission permit.*
Maximum hourly averaged emission 15 ppmv.
Under normal operation conditions the amine plant capturing CO2 with 30 wt% MEA from CCGT flue gas has amine emissions to air below 1 ppmv and ammonia emissions about 10-20 ppmv [3] . TCM tested capturing CO2 with 30 wt% MEA for the first time, from the RFCC flue gas in spring 2013. It was soon found that emissions were very high and shortly further testing with RFCC and MEA were abandoned to avoid violation of the emission permit and to find ways to mitigate high amine emission to air.
To understand and control high amine emissions further tests with CCGT flue gas with recycled CO2 and controlled addition of RFCC flue gas supported by several manual isokinetic sampling of the depleted flue gas were conducted in autumn 2015 [11]. After through testing, control and repeatability of high amine emission tests, it was concluded that high amine emission is caused by sulfuric acid aerosol in the RFCC flue gas together with process conditions which causes high amine emission in the form of aerosol. From tests in autumn 2015, the need for RFCC flue gas aerosol removal, upgrade of the absorber water wash system and online flue gas sampling systems was deemed necessary to be able to run with RFCC flue gas and 30 wt% MEA in compliance to the applicable emission permit.
During late 2016 a high efficiency Brownian diffusion (BD) filter with flue gas capacity of 35,000 Sm3/h was installed downstream the Direct Contact Cooler (DCC) and upstream the absorber, followed by upgrade of the water wash systems to increase its cooling capacity to 12 MW (thermal), where 6 MW (thermal) on the lower water wash and 6 MW on the upper water wash system. The later upgrade allows keeping the plant in water balance and allows for flexible operation in terms of lean amine temperature, and selection of the ratio of cooling needed in the water washes.
During period summer-autumn 2017, the amine plant with the new installations was tested with 30 wt% MEA under the AeroSolve project. TCM amine plant’s ability to run with RFCC flue gas, 30 wt% MEA and compliance with the emission permit was demonstrated thoroughly and continuously supported by manual isokinetic sampling. During this period it was observed that the online flue gas analysis system was suffering stability issues due to accumulation of aerosol and degradation of amines. The online flue gas sampling system was upgraded and modified by TCM, to overcome aerosol accumulation and degradation of amines in the sampling line.
The upgraded online flue gas sampling system with advanced process configuration to reduce specific reboiler duty (SRD) was thoroughly and successfully tested during spring 2018 with 30 wt% MEA and RFCC flue gas.
2.1 TCM’s Amine plant
The amine plant is a generic and highly flexible CO2 capture plant designed and constructed by Aker Solutions and Kværner. The amine plant can either capture CO2 from CCGT flue gas or RFCC flue gas with a design CO2 production capacity of 80 tonnes/day and 200 tonnes/day respectively [4]. Figure 1 given below shows a simplified process flow diagram with online meters and instrumentation.
Flue gas from the blower is conditioned and saturated with water to the required temperature (normally 20-50°C) in the DCC. The CHP DCC system cools the flue gas from about 195°C down to the required temperature while the RFCC DCC saturates the flue gas from 20°C up to 50°C by injecting live steam into the DCC as the RFCC flue gas leaving the upstream (refinery side) flue gas desulfurization unit (FGD) is at around 20°C. Conditioned and water saturated RFCC flue gas enters the high efficiency BD filter where most part of aerosol and catalyst particles from the flue gas are removed. Filtered RFCC flue gas enters the rectangular absorber, where flue gas flows counter currently to lean amine solvent. The lean amine solvent can be fed either at 12m, 18m or 24m to the absorber structured packed bed. In the conventional configuration CO2 depleted flue gas enters the lower water wash followed by upper water wash to reduce VOC, NH3 and some amine emission to the air and condition the flue gas to the required humidity and thus keeps the plant in good water balance.
Rich amine from the absorber is pumped through the rich/lean cross plate heat exchanger to the top of either RFCC or CHP stripper depending on the flue gas source and CO2 amount to be produced. The RFCC stripper is a structured packed bed column equipped with water wash and shell and tube type natural thermosiphon reboiler which utilizes low pressure steam to regenerate rich solvent, CHP stripper is described elsewhere [4]. Stripped CO2 is cooled to about 20°C in the overhead condenser utilizing sea water. Condensate from cooled CO2 product is separated in the reflux drum and pumped back into the stripper top, while CO2 product is vented to the ambient via CO2 stack. The RFCC stripper is also equipped with a Lean vapor compressor (LVC) system, which can be lined-up with the RFCC stripper if required. In the LVC system, hot lean amine which is at bobble point is throttled to a lower pressure and fed to the flash drum generating steam. In the flash drum steam and lean amine solvent are separated. Steam from the flash drum is compressed to stripper bottom pressure in a compressor by the expense of electrical energy. The superheated steam from compressor is fed to the stripper which provides extra energy to regenerate rich amine and reduces consumption of low pressure steam. Lean amine solvent from the flash drum is pumped back to the absorber through rich/lean cross plate heat exchanger followed by lean amine cooler. The lean amine is cooled to the required feed temperature in the lean amine cooler.
The amine plant is heavily instrumented with dedicated online analyzers and flow meters. Details of the online analyzer and meters are given in Figure 1.
2.2 RFCC flue gas composition and its challenges for CO2 capture amine based process
RFCC flue gas contains high concentration of CO2, with about 14.7 vol% of CO2 (wet basis), 3.2 vol% of O2, 77 vol% N2 and saturated with water. This makes the RFCC flue gas equivalent to flue gas from coal power plant. Further details of the RFCC flue gas are given in Table 2 below. The concentration of trace elements in the RFCC flue gas fluctuates during normal operation.
RFCC flue gas composition: | Inlet BD Filter | Inlet of Absorber | |
N2 | mol% | 77.0 | 77.0 |
Ar | mol% | 0.9 | 0.9 |
O2 | mol% | 3.2 | 3.2 |
CO2 | mol% | 14.7 | 14.7 |
H2O | mol% | 4.2 | 4.2 |
SO2 | ppmv | 5 | 5 |
NOx | ppmv | 100 | 100 |
NO2 | ppmv | 2.5 | 2.5 |
NH3 | ppmv | 0.2 | 0.2 |
CO | ppmv | 10 | 10 |
Total Particulates | mg/Sm3 | 15-40 | <0.5 |
H2SO4 Aerosol | mg/Sm3 | 10-25 | <0.5 |
Salts | mg/Sm3 | 5-15 | <0.5 |
Non-water soluble (SiO2,CaCO3,metals) | mg/Sm3 | 0-2 | <0.1 |
Particle number concentration | aerosol/cm3 | 21* million | 300,000 to 500,000** |
Table 2. Typical RFCC flue gas composition upstream and downstream the BD filter.
*Aerosol conc. upstream the BD filter may vary from 15 million to 25 million. ** conc. downstream the BD filter varies between 300,000-800, 000 aerosol/cm3.
RFCC flue gas contains catalyst fines in the range of a micron to submicron sizes which are different in composition and nature to fly ash contained in coal power plant flue gas. If coal power plant flue gas is filtered for example with a bag house filter to reduce mercury, it will result in very clean flue gas comparable to RFCC flue gas downstream the BD filter. H2SO4 aerosol shown on mass basis in table 2 is equivalent to about 21 million aerosol/cm3 most of them are of submicron size.
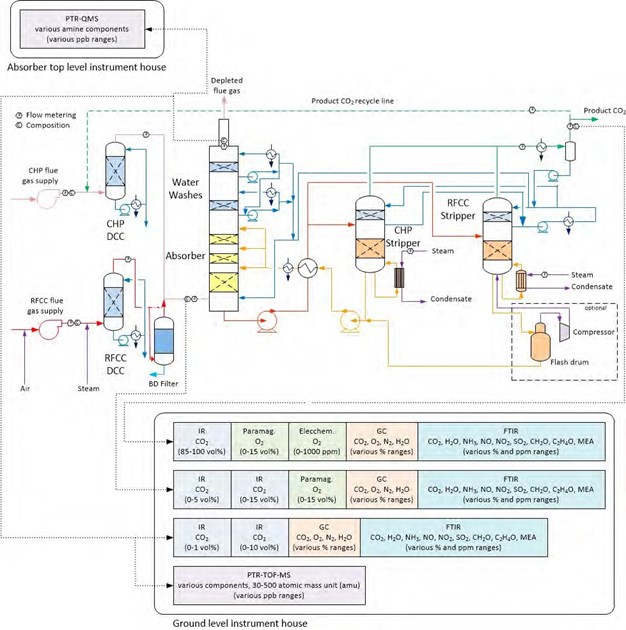
Figure 1. TCM Amine plant with two flue gas sources, CHP and RFCC with corresponding strippers, flue gas analyzers and meters.
BD filter reduces aerosol in the RFCC flue gas from around 21 million aerosol/cm3 to around 500,000 aerosol/cm3. Further details on performance of BD filter can be found elsewhere [2]. A bypass over the BD filter allows higher aerosol concentrations to the absorber in order to study its effects on emissions. The sensibility of advance amines may be compared to MEA at various aerosol concentrations and operational parameters.
Submicron aerosol larger than 0.1 µm grow in the absorber in the presence of supersaturated water vapor due to exothermic reaction of CO2 and MEA. The submicron aerosol absorb MEA from the flue gas in the region close to the lean amine inlet and absorber bulge zone, MEA has the highest partial pressure in this region of the absorber. Submicron aerosol from the absorption section will follow the depleted flue gas and will not be removed efficiently by conventional mesh pads or water wash packing bed(s). MEA emission in the form of aerosol can be reduced by reducing the number of aerosol nuclei in the feed flue gas to the absorber and by avoiding/reducing supersaturation in the absorber. At TCM the former is achieved by filtering the flue gas via the BD filter. The latter is achieved by operating the amine plant in such a way to minimize supersaturation in the absorber and water wash sections which allows for maximum MEA removal from the gas phase before the depleted flue gas enters the upper water wash.
Depleted RFCC flue gas containing MEA aerosol poses a great challenge to the online emission monitoring (FTIR, PTR-QMS, PTR-TOF-MS) system installed at TCM as MEA aerosol accumulate in the sampling system (filters, pumps, lines etc.) which makes online analysis erratic.
The existing sampling system for online emission monitoring in the TCM amine plant, which has been verified for gas phase emissions [5], is not suitable when aerosol are present in the sample flue gas. The problem was particularly experienced at higher MEA emissions (> 4-6 ppmv). With emissions around 2 ppmv MEA, the weight of the aerosol is in the range 30-50 mg/Sm3, while at 6 ppmv MEA, the weight of the aerosol may be up to 100 mg/Sm3 due to the increased diameter. The aerosol, which mainly consist of water, accumulate in the sampling system despite that sampling line has filters and is heat traced. The sampling system was designed for homogenous gas phase emissions and it has been proven to function very well when there are no aerosol present. In previous campaigns with CHP flue gas there has been good agreement between online measurements and manual isokinetic sampling and laboratory analysis [5].
In contrast aerosol carrying amines in the depleted RFCC flue gas accumulated in the sample line and associated filters, pump, and fittings resulting in erratic analysis and unreliable behavior. Upon occurrence of such problems, the sampling system was flushed several times but helped only for a short time. To ensure reliable measurements, proper design of online sampling system is required to avoid condensation, degradation and accumulation of aerosol and flue gas components. TCM’s online flue gas sampling was therefore modified to be able to efficiently evaporate aerosol, avoid accumulation, degradation and reliably and to accurately measure emissions.
2.3 Modified online flue gas sampling system
During tests with RFCC flue gas and 30 wt% MEA regular manual isokinetic sampling were collected and analyzed to make sure that the online emission monitoring system is working properly. The data was also used to properly design a robust online emission monitoring system. Several modifications to the online emission monitoring system were made during the period (2017-2018). This resulted in a robust and reliable emission monitoring system capable of accurately analyzing flue gas even in the presence of aerosol.
The modified online flue gas sampling system as shown in Figure 2, consists of an electric heat traced sampling probe equipped with 6 mm nozzle pointing at 90° to the horizontal plane and placed at 250 mm from the absorber stack’s inner wall. The sampling probe is flushed with cold instrument air if needed. The temperature of the heat tracing elements of the probe can be controlled from 40 to 200°C. Flue gas sample via the probe leads to evaporator, the evaporator is a 316ss double pipe type of electric heater, where the flue gas sample travels in the annulus. The flue gas sample in the annulus of the evaporator is heated by 622 W heating elements installed on the outside of shell and the heating elements inside the inner rod located in the center of the evaporator. The rod runs along the length of the evaporator. The annulus of the evaporator is 12.5 mm wide and 670 mm long. A suction pump sucks 1 m3/h of flue gas sample through the probe resulting in a flue gas sample velocity similar to the velocity in stack, which makes it isokinetic. The flue gas has a residence time of ~4 seconds in the evaporator. Flue gas sample from the pump is filtered with several filters ranging in sizes from 0.1 µm to 10 µm located in the filter house.
The filtered flue gas sample delivers a feed of 0.4 m3/h to the online FTIR over a flowmeter while rest of the sample is routed back to the absorber. The FTIR analyzer is located in the analysis house close to the bottom of the absorber. A sampling line of 110 m length in sulfonated and polished stainless steel which is heat traced and insulated carries the flue gas sample to the FTIR analyzer. This arrangement avoids accumulation of aerosol and condensable components on the surfaces. To avoid chemical degradation of the sample the flue gas sample is not overheated and kept close to 80°C.
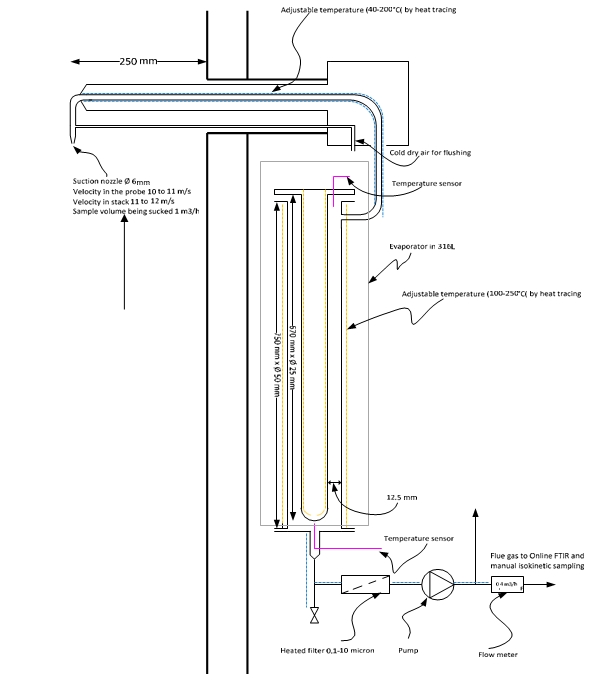
Figure 2. Sketch of TCM modified online flue gas sampling system able to accurately analyze flue gas containing aerosol.
2.4 Isokinetic sampling sketch and description
To verify online sampling system, manual isokinetic sampling of the absorber depleted flue gas for quantification of the concentration of emitted chemical components, were planned to be taken several times on weekly basis and more frequent in demanding periods during testing with RFCC flue gas.
In 2016, TCM further developed the existing method for isokinetic sampling to enable capturing very fine liquid droplets and aerosol. Up to then, the amine plant had mainly been used for capturing CO2 from the CCGT flue gas with very low to almost negligible concentration of SO2 and no aerosol. The development resulted in a modified manual sampling method for amine emission in presence of aerosol. Figure 3 illustrates a sketch of the modified manual isokinetic sampling method. The sampling train consists of a cold probe, a condenser, a dry impinger with jet inlet design, distribution manifold and 0.05 M H2SO4 impinger train. The method has been further optimized since 2016, and the mist trap now consists of only one bottle with jet inlet and no glass wool. The jet-formed inlet of the bottle accelerates the gas containing particles/aerosol/droplets and over a fixed distance lets the particles impinge against a flat glass surface at higher velocity. During this operation droplets gets broken and agglomerated to bigger droplets which are less prone to further re-entrainment.
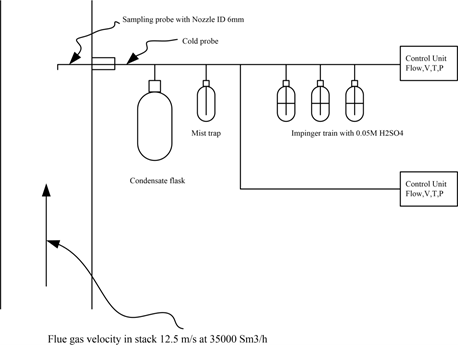
Figure 3. Modified manual sampling train configurations at TCM for collection of mist and flue gas sample. This method has been further optimized and the mist trap now consists of only one bottle with jet inlet and no glass wool.
2.5 Comparison of manual isokinetic and online emission results
While running with RFCC flue gas the TCM online emission monitoring system was suffering from severe aerosol accumulation resulting in erratic emission numbers. Erratic functioning of the online emission monitoring system was monitored by comparing water concentration in the depleted flue gas reported by FTIR to calculated water concentration from steam table based on the actual temperature and pressure of the depleted flue gas.
Fluctuations or discrepancies between the measured water concentration and calculated concentration reveal problems with online emissions monitoring system. Figure 4a shows such an example.
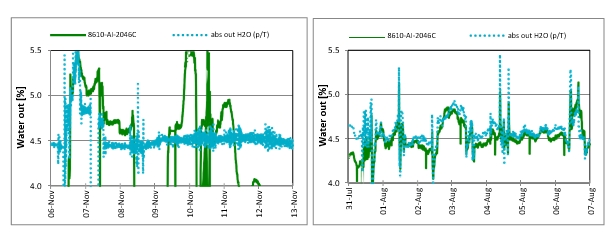
Figure 4a (left) Water measured by online FTIR (Green solid line) showing fluctuations and discrepancy problems with the sampling system. water concentration from FTIR does not match with calculated water concentration (dotted line in light blue) in the depleted flue gas. All process parameters were kept unchanged during this period. Figure 4b (right), shows good agreement between water concentration both from the FTIR and calculated.
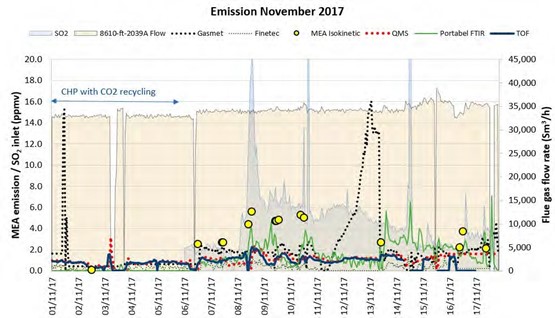
Figure 5 Comparison of isokinetic sampling results to the non-modified online sampling system.
Figure 5 shows comparison of FTIR (Gasmet) and isokinetic results from November 2017, before modification of the sampling system. FTIR mentioned in this paper is FTIR (Gasmet) and will be denoted by FTIR for reference. In Figure 5, on left side, FTIR results compared to manual isokinetic show good agreement during this period the plant was running with CHP flue gas with CO2 recycle having similar CO2 conc. as RFCC flue gas but free of aerosol and has less SO2. From 6th of November the flue gas source is switched to RFCC. During the first couple of days differences in results from FTIR and Isokinetic is not very pronounced. From the 8th of November the difference in results from isokinetic and FTIR begins to increase this can also be noticed from Figure 4a showing mismatch between the water conc. measured by FTIR and calculated. This instance reveals accumulation of aerosol in the sampling system and perhaps enhanced by non-representative sample due to the fact that the probe for FTIR was installed at location S6 as shown in Figure 11. S6 is located in the concrete absorber wall where the probe may not have received a representative sample due to its non-optimal design. This was verified by manual sampling at S6 which does not match manual isokinetic results at S14 (shown in Figure 11). From 11th of November the deviation in results from FTIR to isokinetic gets very large, the behavior renders the online system inadequate for flue gas containing aerosol. Therefore, it was deemed necessary to modify the existing online sampling system to be able to analyze accurately and reliably in the presence of aerosol in the flue gas.
The objective of the TCM modified online sampling system is to be able to measure total amine emission in the depleted flue gas both in the form of aerosol and gas phase, and to increase the online systems availability and reliability with challenging flue gases.
Figure 6 shows comparison of results from the modified online sampling system with FTIR installed at S14 and manual isokinetic samples. All process parameter (i.e.) flue gas flow rate, CO2 concentration in the inlet flue gas, lean amine temperature, water wash(s) process parameters, CO2 capture rate, and lean amine flow rate were kept unchanged while performing manual isokinetic sampling and collecting data from the online FTIR.
It is obvious from Figure 6 that isokinetic and online FTIR results from the modified sampling system are in good agreement and is not suffering from aerosol accumulation and degradation. The modified system is tested thoroughly for more than two months with RFCC without any problems of aerosol accumulation.
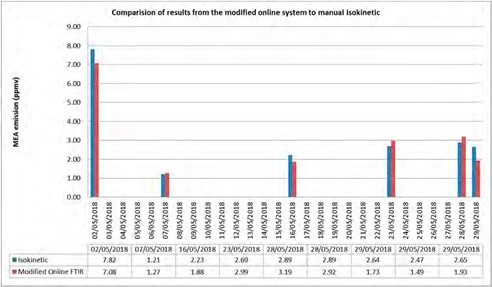
Figure 6. Comparison of results from the modified online sampling system with FTIR and isokinetic.
3. Process optimization for energy consumption and low emission
During the AeroSolve CLIMIT project (August-November 2017), testing with RFCC flue gas and 30 wt% MEA was conducted to find optimal process conditions resulting in low emissions and optimum SRD. Some of the tests conducted during AeroSolve project were revised and further optimized with the modified online sampling system in operation during spring 2018 under TCM owner’s MEA-4 test program. During all these tests caustic soda solution was injected in the RFCC DCC to reduce SO2 in the flue gas entering the absorber.
Some of the process parameters and plant configuration which were optimized in the AeroSolve project are:
- Lean amine temperature
- Lean amine loading for minimum Specific reboiler duty (SRD)
- Process plant configuration to result in minimum emissions
As a result, an advanced process plant configuration together with the mentioned modified online sampling system was developed which results in lower SRD and low emissions. Details of the optimized process parameters are given below.
3.1 Lean amine temperature optimization
CO2 absorption in chemical solvents like MEA, MDEA or MEA+AMP etc. is an exothermic process resulting in temperature increase of the absorbing solvent and flue gas in mutual contact. The temperature increase is largest in the absorber bulge zone as shown by the temperature profile of the TCM amine absorber in Figure 7. Due to heat generation and temperature increase in the absorber bulge zone water is evaporated from the bulk of the solvent to the gas phase and thus saturates the flue gas at a given temperature, pressure and composition. The saturation of gas phase with water can be further increased to supersaturation, S as given by equation (1), by creation of aerosol (including both homogenous and heterogeneous aerosol) due to rapid quenching with cold lean amine and in presence of large amount of submicron foreign nuclei. Aerosol formation and its growth in gas-liquid contactors such as absorbers and scrubbers has been extensively studied for quenching of acid gases [6], [7], [8].

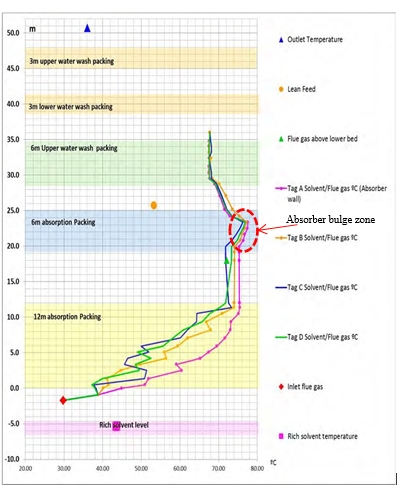
Figure 7. Absorber temperature profile, running with RFCC flue gas. CO2 capture of 85%.
For homogenous supersaturation a higher degree of saturation is required S>2 [9], depending on temperature and composition. For heterogeneous aerosol formation, the degree of supersaturation required could be as low as close to S~1 due to presence of large number of nuclei available in the gas phase. The aerosol formed in the absorber bulge zone will follow the flue gas stream to the downstream water wash system(s). The aerosol may grow further due to condensation, coalescence and process parameters which favor rapid quenching.
Lean amine entering the absorber is typically around 35-40°C where the highest bulge temperature in the absorber is around 50-55°C for CCGT type of flue gas at 85% CO2 capture [5], while for RFCC or coal flue gas having around 14% CO2 the bulge temperature is around 75-78°C for 85% CO2 capture with 30 wt% MEA. The environment for creation and growth of aerosol due to supersaturation will be favorable if the temperature difference between the lean amine and absorber bulge (ΔTbl) is large.

Therefore, keeping small difference between the lean amine temperature and bulge temperature will help reducing aerosol formation and hence reduce amine aerosol emissions. On the other hand running CO2 capture plants with high lean amine temperature to reduce the ΔTbl may lead to increased SRD due to the fact that less energy from hot lean amine is recovered in the rich lean cross heat exchanger. As a result more energy is lost to cooling water in the water wash system. To reduce the energy loss in a conventional amine plant configuration, ΔTbl needs to be kept largest possible to allow for optimal SRD and acceptable amine emission in compliance to the applicable emission permit.
Several tests were conducted during the testing at TCM within the AeroSolve project to optimize the lean amine temperature in terms of reducing emissions. Figure 8 shows MEA emission as function of ΔTbl.
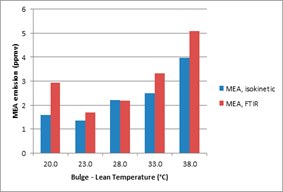
Figure 8 shows reduction in MEA emissions by reducing ΔTbl.
From Figure 8 it is obvious that MEA emissions are reduced by reducing ΔTbl. This supports the theory of reducing supersaturation in the gas phase reduces MEA emissions. During tests with RFCC flue gas TCM targeted to run the plant with less than 1-2 ppm of MEA emissions. Based on the results it was decided to keep ΔTbl below 25°C for tests with RFCC flue gas at 87% CO2 capture rate which allows keeping MEA emissions below 2 ppm.
3.2 Lean amine loading for minimum Specific reboiler duty (SRD)
The plant performance was optimized for 18 m absorber packed height, with about 14% CO2 by varying lean solvent flow rate and manipulating steam flow rate to stripper reboiler to find process conditions resulting in 87% CO2 capture with lowest SRD. As the online sampling system during the AeroSolve project was not able to accurately and reliably measure MEA emissions resulting from tests with RFCC flue gas, it was decided to run SRD optimization tests with CHP and CO2 recycle flue gas to avoid any breach of emission permit. CHP flue gas with CO2 recycle flowrate from the stripper overhead was adjusted, to achieve CO2 concentration in the flue gas at absorber inlet similar to RFCC flue gas CO2 concentration.
Table 3 given below summarizes range of process parameters tested during SRD optimization tests. At each solvent flow rate, the steam pressure was manipulated and hence the steam flow rate to achieve 87% CO2 capture. At stable conditions, lean and rich solvent samples were collected for analysis of MEA and CO2 concentration. After every 24 hours, the solvent flow rate was changed to the next set point and the procedure was repeated at each solvent flow rate.
Parameter | UoM | Range |
Number of test cases | 10 | |
Absorber Packing height | m | 18 |
Flue gas flow into absorber | Sm3/h (w) | 35,000 |
Flue gas composition: | ||
CO2 | mole% | 13.1-13.5 |
H2O | mole% | 4.0 – 4.2 |
O2 | mole% | 12.2 – 13.5 |
Flue gas inlet temperature | °C | 29 – 30 |
Conc. of MEA in lean solvent (CO2 loaded) | wt% | 28-30.2 |
Lean solvent flow rate | kg/h | 100,000 – 165,000 |
Lean solvent temperature | ºC | 50 to 55 |
Liquid to Gas ratio | kg/Sm3 | 2.8-4.6 |
Stripper bottom temperature | °C | 119.5 – 122.6 |
CO2 capture rate | % | 86-89 |
Stripper pressure | barg | 0.95-0.96 |
Table 3. List of process parameters during SRD optimization tests.
Figure 9 shows results for the SRD optimization tests. Capture rate during these tests was within 86-88% as denoted by red david (*) stars in the figure. For the targeted 86-89% CO2 capture, a minimum SRD of 3.67 GJ/ton CO2 was achieved. For optimal SRD, a lean solvent circulation rate of 120,000 kg/h with 30 wt% MEA is required while utilizing 18 m packing height of the absorber bed. Table 4 summarizes some more details for tests reported in Figure 9. More details about SRD(Meth 1) and SRD( Meth 3) as shown in figure 9. can be found elsewhere [10].
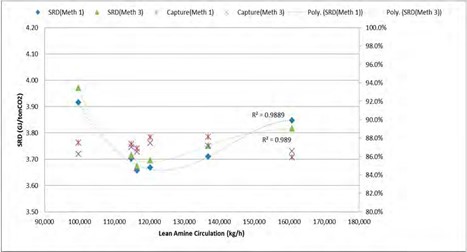
Figure 9. U-curve for SRD optimization, CHP flue gas with CO2 recycle and 30 wt% MEA.
Case ID | Flue gas flow | Lean amine flow | Lean amine loading(mol | CO2 Capture | SRD (GJ/ton |
rate (Sm3/h) | rate (kg/h) | CO2/mol MEA) | rate (%)* | CO2)* | |
2C-CHP- 6C Recy | 33,908 | 99,670 | 0.160 | 88.3% | 3.92 |
2C-CHP- 6A Recy | 33,900 | 114,873 | 0.19 | 87.3% | 3.70 |
2C-CHP- 5C Recy | 33,934 | 116,455 | 0.204 | 87.3% | 3.67 |
2C-CHP- 8A Recy | 33,918 | 120,360 | 0.199 | 87.4% | 3.67 |
2C-CHP-3 Recy | 33,699 | 136,867 | 0.251 | 88.1% | 3.71 |
2C-CHP-4 Recy | 33,874 | 160,821 | 0.273 | 85.9% | 3.85 |
*Tabulated Capture rate and SRD is based on Meth 1.
Table 4. List of process parameters during SRD optimization tests.
4. Advanced process configuration for reduction and control of amine aerosol emission
TCM developed and tested an advanced novel concept to reduce and control amine aerosol emission and improve the energy efficiency of the overall CO2 capture process. The advanced process configuration was tested for an extended period during spring 2018 under TCM owner’s MEA-4 campaign. The advanced process configuration’s performance was independently verified by a third party, Electric Power Research Institute (EPRI) in May 2018. The independent verified advanced process configuration’s performance with RFCC flue gas will serve as baseline for bench marking other amine based technologies. The independent verified RFCC baseline will be published later. Following modifications were made to the amine plant prior to running tests with RFCC flue gas under the MEA-4 campaign, in order to allow for accurate and reliable online emission monitoring, amine aerosol emission reduction, and improve the energy efficiency of the overall process.
- Modification of online emission monitoring system
- Modification of the 3rd absorption bed to “RFCC water wash”
- Installation of cold rich by pass line to the stripper
- Installation of Brownian diffusion (BD) filter
Brownian diffusion filter was installed in December 2016 and thoroughly tested with RFCC flue gas during 2017 and 2018. Details about performance of TCM BD filter can be found elsewhere [2]. Modification of online emissions monitoring system with FTIR is described in section 2.3 while rests of the modifications are described below.
4.1 Modification of the 3rd absorption bed to RFCC water wash
The RFCC flue gas downstream the BD filter contains around 500,000-800,000 aerosol/cm3, most part of the aerosol are submicron (0.1-0.5 µm) [11]. In absorber the submicron aerosol grow by condensation of water and coalescence followed by absorption of MEA present in vapor phase in the bulge zone. Majority of aerosol carrying amine from the absorber bulge zone will follow the supersaturated depleted flue gas to downstream sections of the absorber (i.e) water wash(s) and demisters.
A conventionally designed amine plant treating flue gas which contains aerosol and particulates cannot remove submicron aerosol. This is due to the fact that in a conventional absorber system, the depleted flue gas from absorption section is quenched abruptly to keep the plant in water balance and recover some amines and ammonia. Abrupt quenching in the presence of nuclei generates and grows more aerosol due to heterogeneous supersaturation which results in increased emissions. Therefore, abrupt quenching of the depleted flue gas needs to be avoided when amine are present in the gas phase. At TCM a three stage water wash system is tested in order to mitigate the aerosol emissions. The system is tested with up to 2000,000 aerosol/cm3 in the flue gas at the absorber inlet.
Abrupt quenching of the depleted flue gas containing aerosol at TCM is avoided by a special designed water wash which is termed “RFCC water wash” utilizing the pre-existing 6 m deep upper absorption bed. As suggested by its name the RFCC water wash is operated when capturing CO2 from RFCC flue gas. The purpose of the RFCC water wash is to remove as much as possible of the amines in gas phase with hot and relatively clean water from the upper water wash [12]. Simultaneously, large aerosol above 5 µm generated above the bulge area are captured in the RFCC water wash. In the future, a demister shall be installed upstream of the RFCC water wash in order to capture larger aerosol and increase the RFCC water wash efficiency.
The lower water wash is operated at the highest possible temperature in order to capture the remaining amines in gas phase and to avoid water condensation on aerosol.
- The upper water wash cools down the flue gas for the plant water balance.
- The RFCC water wash consists of 6 m Flexipac 2X (SS) structured packing with equivalent diameter similar to the absorber equivalent diameter and a special distributor.
The special distributor has a capacity corresponding to the total clean water condensed in the upper water wash. This is about 6-8 m3/h of water during normal conditions. Hot water at around (60-70°C) either from the upper or lower water wash, preferably from the upper water wash together with inherent leakage of about 1 m3/h of water from the lower water wash collector tray is fed to the RFCC water wash. Water fed to the RFCC water wash distributor irrigates the packing and aerosol in the depleted flue gas counter currently contacts hot water. Aerosol in the depleted flue gas grow to a larger size which makes it possible to be removed from the flue gas in the RFCC water wash. Major part of aerosol containing amine is recovered here. Water from the RFCC water wash containing removed aerosol flow down to the absorber packing and eventually to absorber sump. Figure 10. shows details of the RFCC water wash configuration.
The amine captured in each water wash is estimated based on the laboratory analysis of the water wash circulation water and the flow meters of each water wash drain. The tests confirm that more than 90% of the amines are captured in the RFCC water wash. 5% to 8% are captured in the lower water wash. Less than 2% are captured in the upper water wash. The total amines captured in the three water washes correspond to a concentration up to 2,000 ppmv of MEA in the flue gas upstream the water washes. As the theoretical MEA concentration in the gas phase is lower than 400 ppmv, it is deducted that most of the amines captured in the RFCC water wash are caused by MEA condensed on aerosol.
A different water wash configuration is tested elsewhere [12] with a limited water flow to the lower water wash further operation parameters are not available in the public domain.
At TCM depleted flue gas from RFCC water wash continues to lower water wash where the flue gas is cooled by removing about 1 MW of heat. From the lower water wash the depleted flue gas leads to upper water wash and cools down to a temperature just above the flue gas inlet temperature in order to keep the plant in water balance.
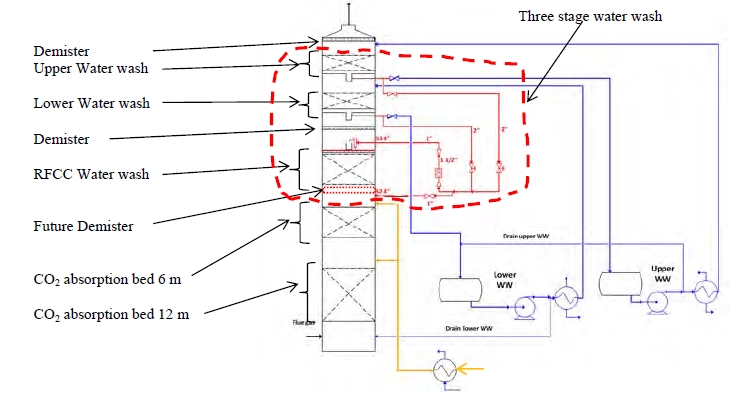
Figure 10. Water wash configuration for the TCM amine plant absorber.
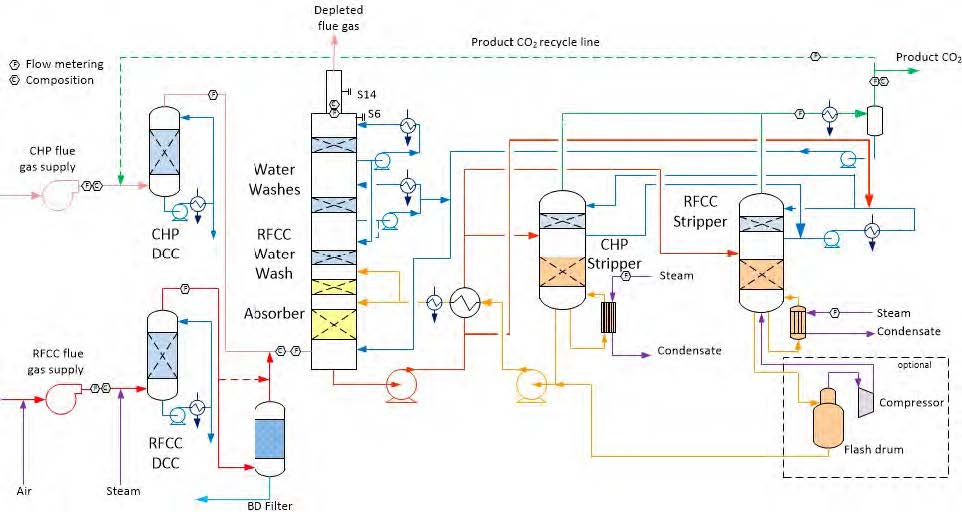
Figure 11. TCM Advanced process configuration for emissions control and optimal SRD. RFCC WW and rich amine bypass over cross heat exchanger is shown in the figure.
4.2 Installation of cold rich by pass line
As discussed in section 3.1, lean amine inlet temperature to absorber needs to be kept around 55°C while capturing CO2 from RFCC flue gas, this gives a ΔTbl~ 23°C. Lean amine temperature of 50°C or above can be achieved by two ways:
- Bypassing a fraction of hot lean amine over rich-lean cross heat exchanger
- Bypassing a fraction of cold rich amine over rich-lean cross heat exchanger
By applying the first approach a fraction of hot lean amine bypasses over the rich-lean cross exchanger, the bypass hot lean is mixed with cold lean amine exiting the cross heat exchanger and fed to the absorber without further cooling in the downstream trim cooler. Bypassing a fraction of hot lean amine increases SRD because the available recoverable heat in the cross heat exchanger reduces and the extra heat in the bypass stream is transferred to flue gas and thus lost in the cooling water.
By applying the second approach a fraction of cold rich solvent downstream the rich pump bypasses the cross rich-lean heat exchanger and fed to the stripper overhead system. Via the stripper overhead system, the rich bypass stream enters the stripper water wash section and functions as extra reflux by condensing water from the gas phase in the stripper top section accompanied by further cooling in the stripper top section. The energy from condensation of water in the stripper top section is recovered in the cold rich stream running down the stripping section thus reduces the energy lost in the overhead condenser. Around 2/3 of water in the stripper top section is condensed by the cold rich amine stream. While 1/3 of the water in the hot stripper gas stream is condensed in the overhead sea water cooled condenser. This reduces SRD from 3.67 to 3.5 GJ/ton CO2 at similar conditions. The second approach as described above was implemented to the TCM amine plant as illustrated in Figure 11 and tested thoroughly. The advanced configuration consisting of BD filter, three stage water wash system, cold rich bypass to stripper and modified online emission monitoring system was tested successfully over a long period and enabled TCM to run amine plant with RFCC in compliance with the applicable emission permit in an efficient manner. Table 5 summarizes results achieved with the advanced configuration and RFCC flue gas.
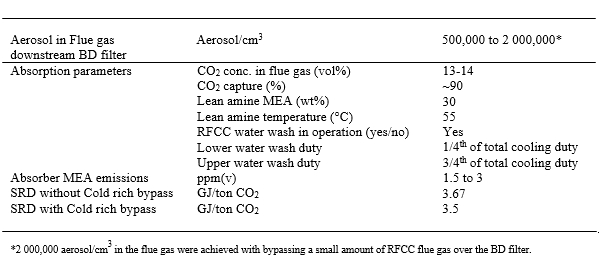
Table 5. Performance of advanced process configuration of amine plant.
Conclusion
TCM has developed and tested an advanced amine plant process configuration for RFCC flue gas with 30 wt% MEA. The advanced configuration in addition to conventional configuration consists of a Brownian diffusion filter, three stage water wash system, online sampling system tolerating aerosol, fractional bypass of cold rich amine stream and operational parameters which enables to reduce aerosol based amine emissions to around 2 ppm and SRD of 3.5 GJ/ton CO2. To avoid MEA emissions above 2 ppmv the flue gas entering the absorber should have no more than 1000,000 aerosol/cm3, the ΔTbl needs to be kept within 25°C and any abrupt quenching of aerosol containing depleted flue gas needs to be avoided. The latter is achieved by operating the RFCC water wash with the special procedure described in this paper. To reduce SRD a fraction of rich stream should be bypassed over the lean rich cross heat exchanger and fed to the stripper, this helps to reduce steam demand and thus lowers SRD. The sampling line for the online analysis and monitoring should be designed to avoid accumulation and degradation of chemical species and should be able to evaporate all chemical species and keep it in gaseous form.
Acknowledgements
The authors gratefully acknowledge the staff of TCM DA, Gassnova, Equinor, Shell and Total for their contribution and work at the TCM DA facility. The authors also gratefully acknowledge TCM owners and the Climit Demo project AeroSolve (616125) for their financial support and contributions.
References
- The Open-source Centre at TCM, https://catchingourfuture.com/
- Lombardo G, Shah MI, Fostås B, Hvidsten OA, Faramarzi L, Cazenove TD, Lepaumier H, Rogiers P. Results from aerosol measurement in amine plant treating gas turbine and residue fluidized catalytic cracker flue gases at the CO2 Technology Centre Mongstad (GHGT-14, 2018)
- Morken A.K, Pedersen S, Kleppe ER, Wisthaler A, Vernstad K, Ullestad Ø, Flø NE, Faramarzi L, Hamborg ES. Emission results of amine plant operations from MEA testing at the CO2 Technology Centre Mongstad, Energy Procedia 63(2014), 6023-6038
- Gjernes E,Pedersen S,Cents T, Watson G, Fotås BF, Shah MI, Lombardo G, Desvignes C, Flø NE, Morken AK, Cazenove TD, Faramarzi L,Hamborg ES. Results from 30 wt% MEA performance testing at the CO2 Technology Centre Mongstad, Energy Procedia 114(2017)1146-1157
- Faramarzi L,Timsen D,Hume S,Maxon A,Watson G,Gjernes E,Fostås BF,Lomarado G,Cents T,Morken AK,Shah MI,Cazenove TD,Hamborg ES. Results from MEA testing at the CO2 Technology Centre Mongstad: Verification of baseline results in 2015. Energy Procedia 114(2017)1128-1145
- Gretscher, H., Schaber, K., Aerosol formation by heterogeneous nucleation in wet scrubbing processes, Chem. Eng. Process. Process Intensif., 38, 541–548, 1999.
- Wix, A., Schaber, K., Ofenloch, O., Ehrig, R., Deuflhard, P. Simulation of Aerosol Formation in Gas-Liquid Contact Devices, Chem. Eng. Commun., 194, 565–577, 2007.
- Brachert, L., Kochenburger, T., Schaber, K., Facing the Sulfuric Acid Aerosol Problem in Flue Gas Cleaning: Pilot Plant Experiments and Simulation, Aerosol Sci. Technol.,47, 1083–1091, 2013.
- Purvil Khakharia. Aerosol-based Emission, Solvent Degradation, and Corrosion in Post Combustion CO2 capture (PhD thesis 2015)
- Hamborg ES, Smith V, Cents T, Brigman N, Pedersen OF, Cazenove TD, Chhaganlal M,Feste JK, Ullestad ØmUlvatn H,Gorset O,Askestad Inga,Gram LK, Fostås BF, Shah MI, Maxon A, Thimsen D. Results from MEA testing at the CO2 Technology Centre Mongstad. Part II: Verification of baseline results, Energy Procedia 630(2014) 5994-6011
- Lombardo G, Fostås BF, Shah MI, Morken AK, Hvidsten OA, Mertens J, Hamborg ES. Results from aerosol measurement in amine plant treating gas turbine and Residuel Fluidized Catalytic Cracker flue gases at the CO2 Technology Centre Mongstad. Energy Procedia 114(2017) 1210-1230
- Moser P, Schmidt S, Stahl K, Vorberg G,Lozano GA, Stoffregen T, Røsler F. Demonstrating Emission Reduction-Results from the Post combustion Capture Pilot Plant at Niederaussem. Energy Procedia 63(2014) 902-910.
CO2 product quality: assessment of the range and level of impurities in the CO2 product stream from MEA testing at the Technology Centre Mongstad (TCM) (2018)
Kim Johnsena,b, * , Eirik Romslo Kleppea, Leila Faramarzia,b, Christophe Benqueta,d, Erik Gjernesc, Gelein de Koeijerb, Thomas de Cazenovea, Anne Kolstad Morkena,b, Nina Enaasen Fløa, Muhammad Ismail Shaha,c, Magnus Aronssona, Øyvind Ullestada
aTechnology Centre Mongstad, 5954 Mongstad, Norway bEquinor ASA, PO Box 8500, 4035 Stavanger, Norway cGassnova SF, Dokkveien 10, 3920 Porsgrunn, Norway dTotal E&P Norge, Finnestadveien 44, Dusavik, 4029 Stavanger, Norway
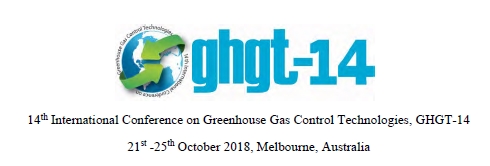
Abstract
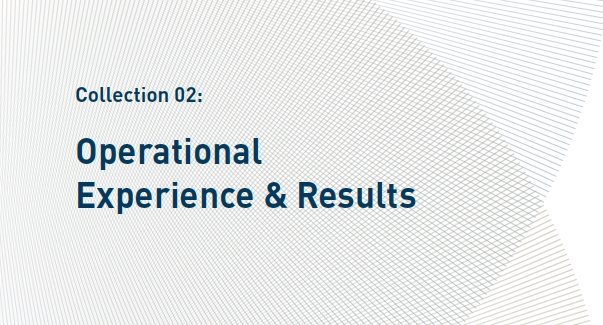
During the recent MEA campaign at the Technology Centre Mongstad (TCM), a broad range of operational conditions have been explored for the post-combustion amine-based CO2 capture demonstration plant. This paper presents CO2 product composition data from online gas analyzers, originating from CO2 capture of two different flue gas sources available at TCM. Detailed composition data obtained by manual sampling and laboratory analysis, both internally at TCM and by Airborne Labs International Inc. is presented. Among the impurities identified and analyzed for, ammonia, formaldehyde and acetaldehyde are the compounds not commonly reported in the literature. The solvent quality, in terms of metal content and amount of degradation products, seemed to be the most influential parameter affecting the concentration of acetaldehyde and ammonia in the CO2 product gas. In addition, ammonia slip was found to be correlated with operating temperature of the overhead stripper system.
1. Introduction
1.1 MEA campaign at TCM
The Technology Centre Mongstad (TCM) is the world’s leading facility for verifying and improving CO2 capture technologies. TCM is located at Mongstad, one of Norway´s most complex industrial facilities. TCM has been operating since autumn 2012, providing an arena for qualification of CO2 capture technologies on an industrial scale. In autumn 2017, Gassnova (on behalf of the Norwegian state), Equinor (formerly Statoil), Shell and Total entered into a new ownership agreement securing operations at TCM until 2020. The owners of TCM started their most recent monoethanolamine (MEA) test campaign in June 2017 where a large number of public, industrial, research and academic stakeholders were involved [1]. The campaign included demonstration of a model-based control system, dynamic operation of the amine plant, investigating amine aerosol emissions and specific tests targeted at reducing the cost of CO2 avoided. Through the testing, both flue gas sources currently available at TCM were used. These sources are the combined cycle gas turbine (CCGT) based heat and power plant (CHP) and the residual fluid catalytic cracker (RFCC). They provide flue gases with a wide range of properties and a CO2 content from 3.6 to 14%. TCM is located next to the Equinor refinery in Mongstad. The Mongstad refinery is the source of both flue gases supplied to TCM. One of the objectives of the campaign has been to characterize the CO2 product gas, which is presented in this paper.
1.2 Knowledge gaps
The compounds that make up the CO2 product stream from a CO2 capture plant can generally be grouped by their impact on the integrity of downstream transport- and storage systems, health and safety issues or cost impact on overall carbon capture and storage (CCS) value chain. There are several literature references [2,3,4,5,6] discussing the concentration range of compounds expected from the main capture technologies used with fossil-fueled power plants or other industrial sources. The most commonly reported impurities for post-combustion capture technologies, along with their impact on CCS value chain, are listed in Table 1.
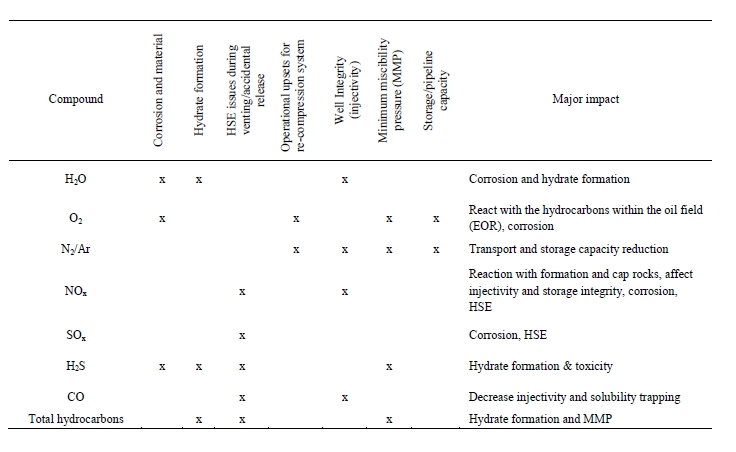
Table 1: Reported impact of CO2 product composition on compression system, transport and storage (incl. EOR) [2-6].
References with actual product CO2 composition data from large scale pilots or demonstration plants operated with amines are rather sparse. In particular, the concentrations of impurities such as amines, ammonia and aldehydes are not easily accessible in the open source literature, although some operational data have previously been reported by TCM during the 2015 MEA baseline tests [7]. Aldehydes, as a possible human carcinogenic by-product of MEA degradation, may represent a HSE risk for CCS facilities if present in high concentrations. Occupational exposure limits are presented by Gentry et al. [8] for both formaldehyde and acetaldehyde. For example, the Health and Safety Executive in the UK has put a long-term exposure limit of 2 and 20 ppm for formaldehyde and acetaldehyde respectively.
The CO2 product gas composition is likely to vary, depending on plant design, operational parameters and solvent properties. During the recent MEA campaign at TCM, a broad range of operational conditions have been explored for the amine plant. This paper presents CO2 product composition data from the online gas analyzers installed at TCM, originating from CO2 capture of both flue gas sources available. Moreover, detailed composition data obtained by manual sampling and laboratory analysis, both internally at TCM and by external labs (Airborne Labs International, Inc.) is presented. The assessment of the CO2 product composition in this work covers the following operational aspects and sensitivities:
- Composition data from both flue gas sources at TCM;
- Solvent quality;
- Stripper overhead system operation;
- Transient operation.
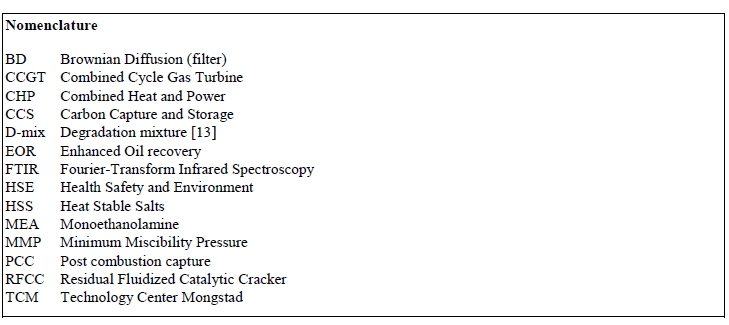
2. Instrumentation and sampling
2.1 TCM amine plant instrumentation
The major constituents of the CO2 product stream are measured by different online analyzers (FTIR/GC/IR) downstream the stripper overhead receiver, as shown in Figure 1. In addition, a manual sampling point is located adjacent to the analyzer off-take, enabling sampling and identifications of additional trace compounds. In the 2015 MEA campaign [7] the manual sampling was performed closer to the CO2 vent stack, and located further downstream of the new sample point, with a larger risk of condensation and non-representative sampling.
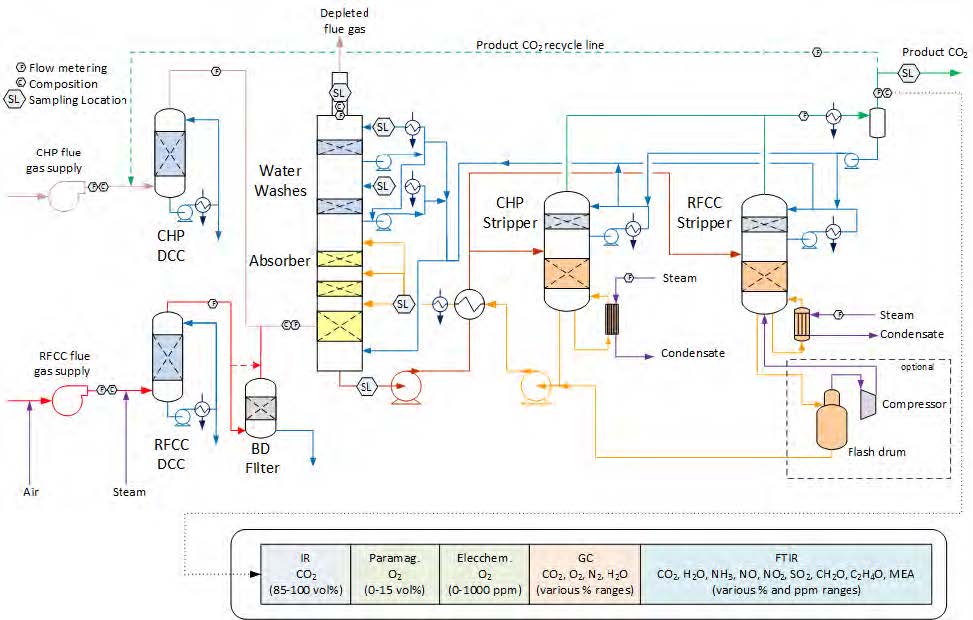
Figure 1: Schematic drawing of TCM amine plant and CO2 product analysis location.
At TCM there are two dedicated strippers for operation with each of the flue gas sources containing different CO2 concentration levels. Both strippers are equipped with a water wash circulation system in addition to the reflux, as shown in the schematic above. The purpose is to “polish” the gas, reducing traces of soluble impurities in the CO2 rich gas leaving the stripper. When the stripper water wash system is not in operation, only the reflux from the overhead condenser drum is returned to the stripper.
2.2 Airborne Labs analysis
CO2 product gas analysis was done by Airborne Labs International, which is an accredited ISO/IEC 17025 laboratory and provider of analytical chemistry testing involving high purity gases and other types of gaseous samples. Sampling was performed during two periods of MEA campaign in 2017 for both flue gas sources. The sampling was done by TCM lab personnel as instructed by the sample kits provided by Airborne Labs. The complete list of compounds analyzed for by Airborne Labs, including analysis method and uncertainty of analytic readings, is found in Appendix A.
3. Detailed composition data
3.1 Composition data from CHP and RFCC flue gas testing
The CO2 product gas sampling was conducted at two different time slots during the MEA campaign, operated with CHP and RFCC flue gas respectively. Table 2 shows typical flue gas conditions upstream the absorber at TCM.
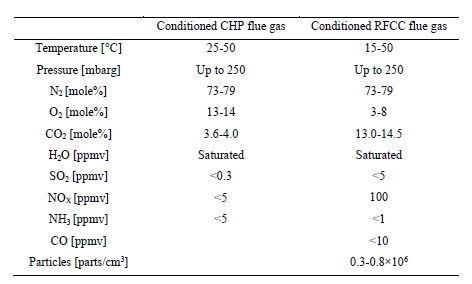
Table 2: Typical CHP and RFCC flue gas conditions upstream absorber.
The results from the detailed analysis from Airborne Labs are presented in Table 3. Compounds analyzed for, but not detected are not included the table (the complete list of compounds analyzed for is found in Appendix A). However, some selected impurities of particular interest for CCS, are still reported as not detected (Nd) in the table for the records. The concentrations are reported on an as-is wet basis, except for CO2 which is on a dry basis.
Three kits for each flue gas source were used during sampling. However, the gas cylinders for two of the sample kits used during the CHP campaign were reported to contain high levels of oxygen and nitrogen, indicating that air contamination may have occurred during the sampling process. Hence, these results are considered to be non- representative and concentrations of CO2 and non-condensables are not reported for these samples. It should be noted that in the period between the CHP and RFCC campaigns the sample probe was somewhat modified to reduce the risk of condensation in the sample probe.
Table 3 also lists some key operational process parameters during the sampling periods. Solvent quality in terms of metal content and degradation products during the campaign is reported elsewhere [9]. The first product gas sampling during the CHP flue gas campaign in June was performed only one week after the start-up of the amine plant, whereas the two last CHP samples were taken four weeks after the start-up. Sampling with the RFCC flue gas was done over a period of two weeks, four and five weeks after a thermal reclaiming campaign respectively. The impact of solvent quality on the product gas quality is also discussed later in this paper.
A Brownian diffusion (BD) filter is installed downstream the RFCC direct contact cooler (DCC), to control the particle concentration in the RFCC flue gas entering the absorber. A by-pass line is also provided to allow for testing at varying particle concentrations, and sampling was performed both for closed and partly open by-pass line during the RFCC testing. Lombardo et al. [10] provide details on the nature of the aerosols particles and removal efficiency of the Brownian diffusion filter.
The stripper overhead system was operated without the dedicated stripper water wash in operation, i.e. only reflux water returned to the upper stripper packing wash section, throughout all sampling periods.
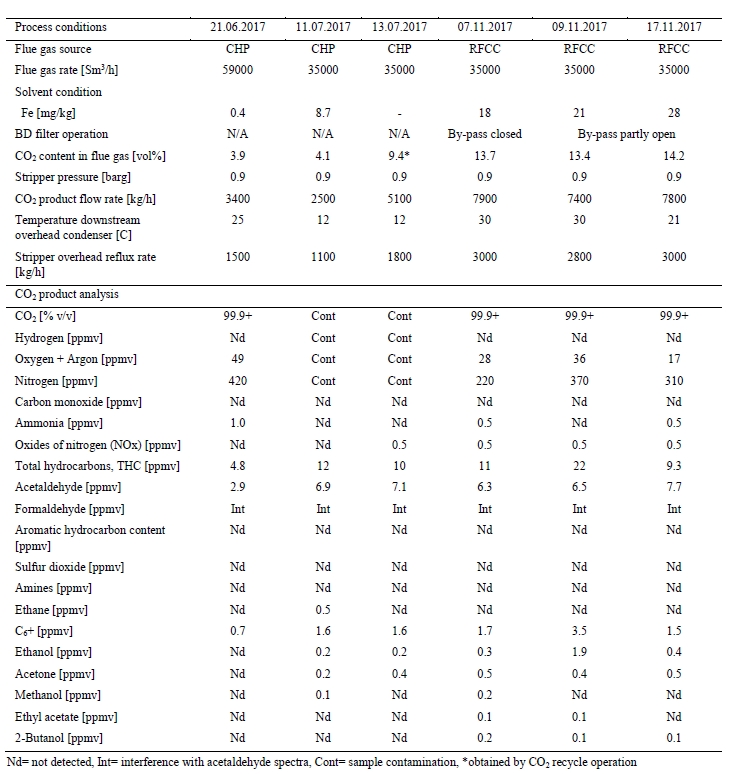
Table 3: Results from detailed CO2 product composition analysis by Airborne Labs.
3.2 Comparison with online instrumentation
A comparison of the Airborne analysis results with TCM online instrumentation is provided in Table 4 for two selected periods, running with CHP and RFCC flue gas, respectively. For some of the compounds there were additional manual samples and analysis performed by the TCM lab, as noted in the table.
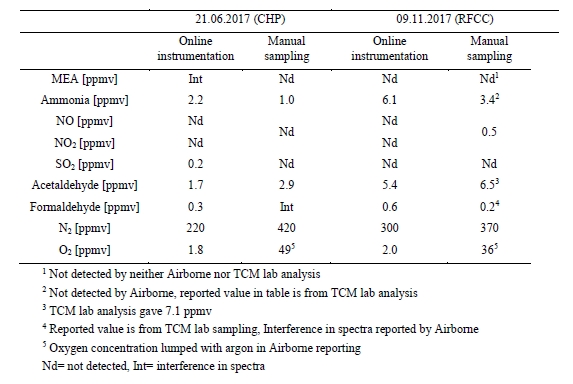
Table 3: Results from detailed CO2 product composition analysis by Airborne Labs.
Neither the online instrumentation nor the analysis from manual sampling could quantify any amines from the CO2 product gas in the selected periods of comparison. There is fairly good agreement for NOx and SO2 between the online FTIR and analysis by Airborne Labs. Moreover, nitrogen concentrations are also comparable, whereas the online electrochemical measurement for oxygen is significantly lower than reported by Airborne Labs. However, these oxygen results are not directly comparable, as Argon is lumped into the reported oxygen concentration from Airborne. For ammonia, the online FTIR is showing higher values than both analysis performed by Airborne Labs or by the TCM lab. Based on a comparison of a series of ammonia analysis done by the TCM lab throughout the MEA-3 campaign at different point in time, these manual samples are rather consistently and systematically showing approximately 50% of the concentrations found by the FTIR.
For aldehydes the concentrations measured by the FTIR are comparable with manual sampling. Figure 2 shows FTIR measurement of formaldehyde and acetaldehydes in the period of 7th to 9th of November. The results from manual sampling and analysis by Airborne and TCM lab, respectively, are included in the figure.
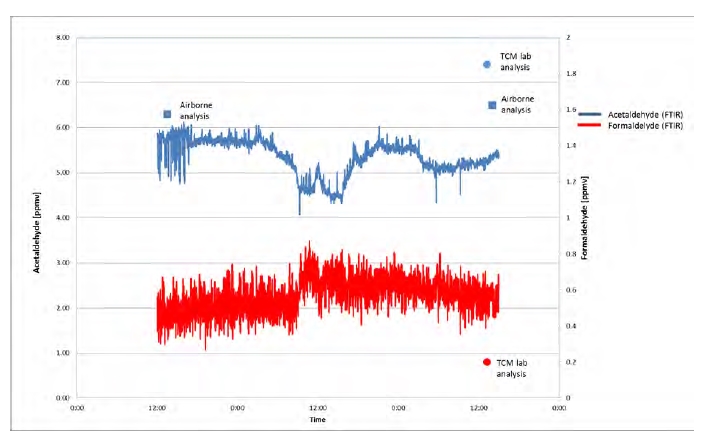
Figure 2: Online FTIR measurement of aldehydes, compared to results from manual sampling and analysis by Airborne TCM/SINTEF for 7th and 9th of November.
4. CO2 product composition sensitivities
4.1 Stripper overhead condensing temperature
The CO2 product is cooled down in the overhead condenser. The condensed vapor is collected in a reflux receiver drum and returned to the stripper as cold reflux over the upper water wash packing section, as shown in Figure 1. At TCM the CO2 stripper is also equipped with a stripper water wash circulation system in addition to the reflux. The operational mode of the overhead system will influence the CO2 quality. In particular, the effect of the condensing temperature and total reflux rate, is of interest with respect to traces and impurities in the CO2 product stream.
A test with CHP flue gas was performed, where the cooling duty of the condenser was reduced in steps, and consequently increasing the CO2 product temperature downstream the condenser from 18 to 25 and 35°C in a step- wise manner. The reflux rate was kept stable during the ramps, without operation of the dedicated stripper water wash system. With increased temperature, the water content in the CO2 product is increased, as an obvious consequence. More interestingly, it was observed that ammonia emissions increased from a steady value of 3 ppmv to almost 6 ppmv, for a condenser outlet temperature of 18 and 35°C, respectively. Reducing the temperature back to 18°C, restored the approximate same concentration of ammonia as prior to the temperature ramp-up, as seen in Figure 3.
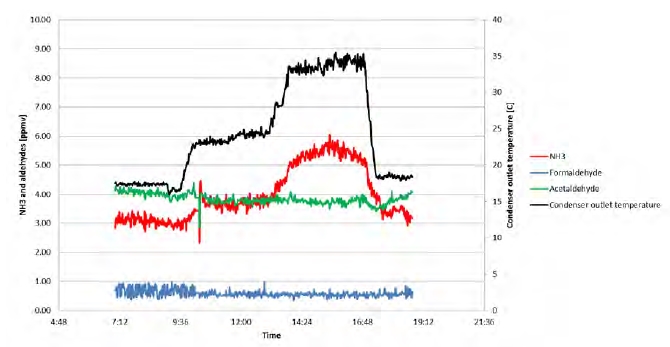
Figure 3: Ammonia and aldehydes concentrations during temperature change of CO2 product gas.
Increasing the CO2 product temperature will increase the vapor pressure of dissolved ammonium causing higher ammonia slip to downstream re-compression systems and transport system. Also shown in Figure 3 are the formaldehyde and acetaldehyde concentrations, which were not significantly influenced by the temperature changes.
The online FTIR did not detect any amines in the CO2 product gas for the temperature interval explored during this ramp test.
4.2 Solvent quality
During the MEA campaign both solvent reclaiming and partial or complete inventory replacement have been done to maintain good solvent condition. For certain periods of the campaign the solvent metal content has been higher than usual, as described by Morken et al. [9]. Two selected periods with aged and fresh solvent, denoted F and G respectively, have been assessed for any observable changes in the CO2 product composition. In period F, the solvent contained relatively high concentrations of metals and degradation products, whereas period G represents a period after a complete solvent inventory replacement and plant wash. More details on the solvent condition in these periods are described elsewhere [9]. For both periods the capture plant was operated with the CHP flue gas. Some key operating conditions for a selected 12-hours window within both periods are listed in Table 5 along with average values for generation of iron, heat stable salts and D-mix.
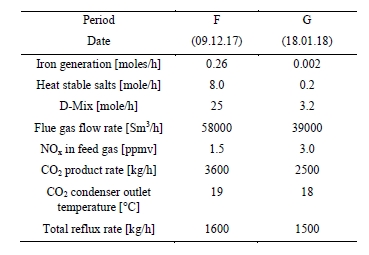
Table 5: Key operational parameters for comparing CO2 product impurities for two periods.
Figure 4 shows how ammonia and acetaldehyde in the CO2 product gas compare for a selected time interval of 12 hours in the two periods. Data points every minute are shown. First, it is evident that the ammonia concentration is significantly higher for period F than G, with concentrations in the region of 50-60 ppmv. This relates to the difference in metal concentration in the solvent for the two periods, as iron has an increased catalytic effect on oxidative degradation of the solvent, resulting in higher ammonia emissions. Also, it is seen that the concentration of acetaldehyde is significantly higher for period F with average of 16 ppmv, compared to approximately 2 ppm for period G. The concentration of formaldehyde, not shown in the figure, does not seem to be correlated to solvent conditions in the same way as acetaldehyde, as both periods show values in the same range of concentrations. Unfortunately, reliable readings of amines from the online FTIR was not available for both the periods under consideration.
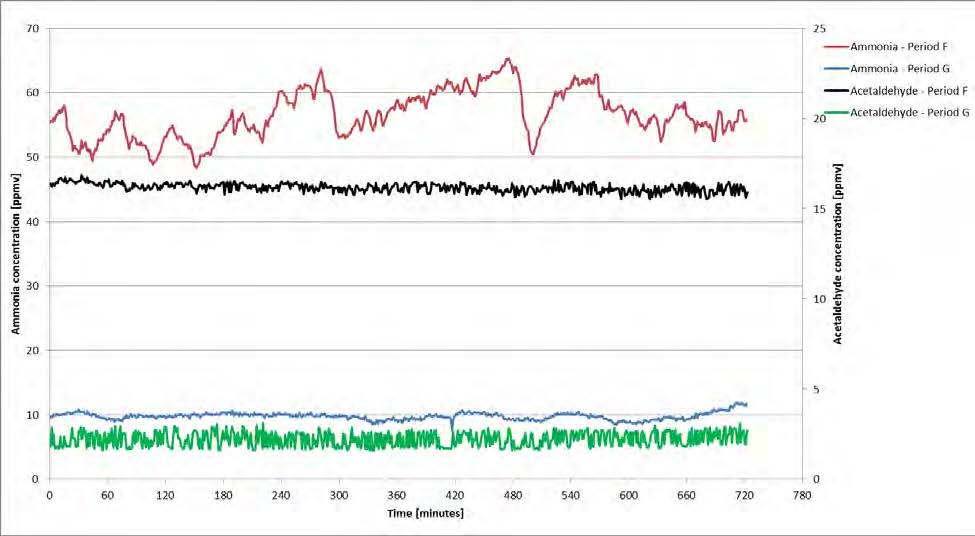
Figure 4: Ammonia and acetaldehyde concentrations (FTIR) in CO2 product over a 12-hours period for periods F and G. Data points averaged every minute.
4.3 Transient operation
A so-called rapid load change test was done by ramping the CHP flue gas rate between 55000 Sm3/h to 35000 Sm3/h within 5 minutes, while adjusting solvent circulation rate and reboiler duty to maintain a constant capture rate of approximately 85%. Figure 5 shows the corresponding solvent circulation and CO2 product flow rates for this test. This test intended to mimic a rapid load change/turn down of the power plant, to study if there were any observable changes in the CO2 product composition.
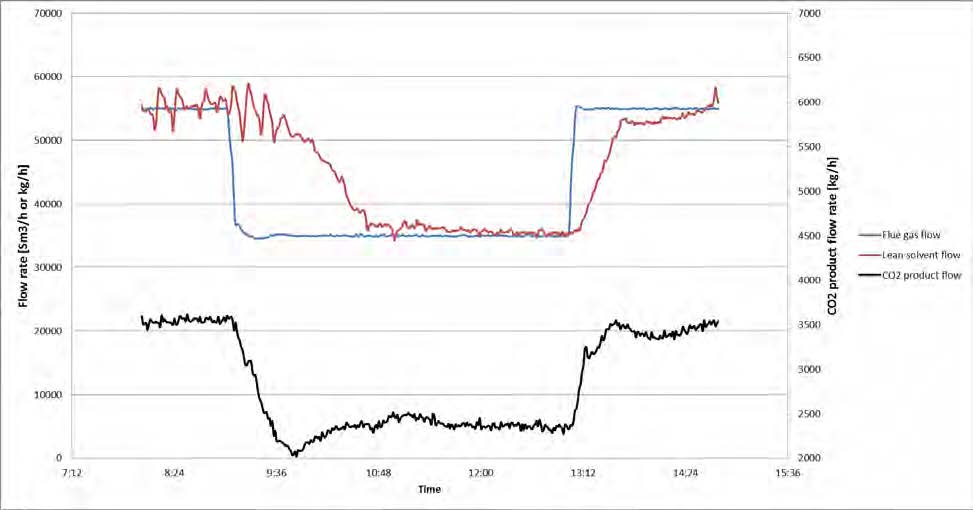
Figure 5: Flow rates of flue gas (CHP), solvent and product gas for transient rapid load change test.
For the ramp-down, the stripper outlet temperature is slightly increased during the transient as the total product flow rate decreases, reducing the required cooling duty of the overhead condenser. As the condenser temperature controller was not properly tuned for such a transient, this resulted in a slight increase in CO2 product temperature and hence ammonia slip, as a seen in Figure 6. The aldehydes concentrations are rather stable during the transients, except for a small peak in acetaldehyde concentration observed during the ramp-up. There was not detected any MEA, NOX or SO2 by the online FTIR during this test.
For changes in flue gas and solvent circulation rate, it could be foreseen that contact time for different gas/liquid (G/L) ratios could influence that amount of dissolved trace compounds in the rich amine leaving the absorber sump. In addition, if significant foaming occurs in absorber, the amount of non-condensable that are carried-under as gas bubbles could increase with increased solvent circulation. However, from the online instrumentation no significant changes are seen for the for the O2 and N2 concentrations, which remained at approximately 3 ppmv and 100 ppmv, respectively.
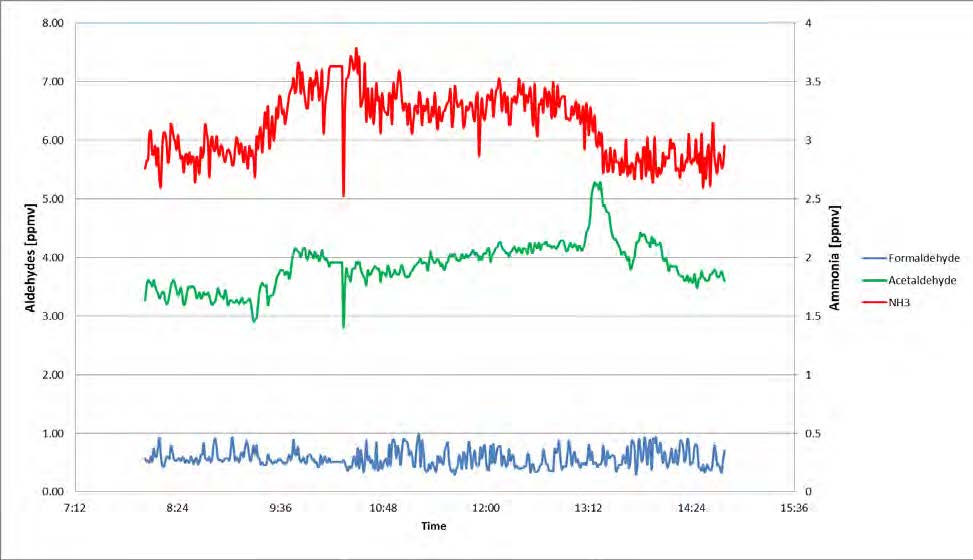
Figure 6: Ammonia and aldehydes concentrations in product gas during rapid load change test.
5. Discussions
The reported dry basis purity of CO2 of 99.9% is very high and in accordance with other references reporting purity of 99.6-99.8% from post combustion capture by chemical absorption processes [3]. The CO2 product gas leaving the stripper overhead system will always be water saturated at the pressure and temperature in overhead reflux condenser and receiver. For transportation purpose, a drying unit will almost always be required downstream the capture unit. The final saturation degree, dictating the design of the drying system, will be set by compressor and intercoolers configuration. The amount of water to be handled by downstream systems is not an inherent feature of post combustion, but rather a choice of operational settings, and is therefore not reported explicitly as an impurity in this work.
Nitrogen is found to be the impurity with highest level in the product gas, regardless of flue gas source, operational condition or solvent condition with concentrations ranging from 200 to 400 ppmv. Nitrogen can arise from entrainment of gas bubbles in the rich solvent flow from the absorber or possibly from NOX conversion. Other non-condensables reported from the Airborne analysis were O2 and Ar, where the sum was ranging from 10-50 ppmv. Presence of non- condensables at higher concentrations could have an adverse effect on operation of rotating equipment in the downstream compression and liquefaction part of the value chain, as they will influence the phase envelope characteristics. In particular, the presence of gas bubbles in liquid CO2 could cause increased vibration on CO2 injection pumps.
Ammonia concentration in the CO2 product gas has during the MEA campaign at TCM varied with the solvent quality. In general, the ammonia levels throughout the campaign has been low (< 10 ppmv). However, in periods where the solvent contained relatively high amounts of degradations products, e.g. prior to reclaiming operation, the ammonia emissions occasionally exceeded 60 ppmv. At these elevated concentrations there is a risk of solids formation downstream the stripper, such as ammonium carbamate, carbonate and bicarbonate as CO2 reacts with NH3. This was experienced at TCM, observed by increased pressure drop over the pressure control valve at the outlet of the condenser receiver vessel. Restricted flow and lack of operability of the pressure control valve caused plant shut down. Upon opening the control valve, salt precipitation was evident in the valve trim, restricting the flow and causing the high pressure drop. Such precipitation could also be a safety concern, if salts block impulse and feed lines to pressure safety valves that protect the stripper and overhead system. This is in particular valid for uninsulated and non-heat traced piping. Moreover, ammonia is reported [11, 12] to have an adverse effect on molecular sieve dehydration systems if deployed downstream, as it weakens the binding structure of sieves. No recommended threshold value was found reported in the literature.
Similar to ammonia, acetaldehyde concentration seems to correlate with the solvent quality. Formaldehyde seems to be less sensitive to the solvent condition with reported concentrations smaller than 1 ppmv. In general, the acetaldehyde concentration has been smaller than 10 ppmv throughout the campaign, whereas elevated concentration up to 15-20 ppmv was experienced in periods with increased degradation products and metal concentration in the solvent.
Amines were not detected from the samples analyzed by Airborne Labs, consistent with results from TCM lab analysis and FTIR online instrumentation. Based on analysis of MEA in liquid phase in reflux receiver drum and vapor pressure considerations, the expected MEA vapor phase concentration should be virtually zero. The design of the overhead condenser receiver at TCM is equipped with a wire mesh pad. The overhead receiver drum is common for both stripper configurations, which means that the load and consequently the separation efficiency is excepted to vary and some entrainment cannot be ruled out, although not found by the sampling probes in this study. In general, separation drums will not be 100% efficient and some liquid carry-over is to be expected, and design considerations of downstream systems should be made to include traces of amines. Consequently, trace levels over time will damage and reduce the lifetime of a molecular sieve used for drying, if constant carry-over is experienced.
6. Conclusions
After evaluating several months of operational data from the recent MEA campaign, it is evident that the CO2 product gas is rather unaffected by flue gas source and process conditions dictating the capture rate. CO2 concentrations of 99.9 v/v% on dry basis was obtained with nitrogen being the major impurity.
Among the impurities identified and analyzed for, ammonia, formaldehyde and acetaldehyde stand out as compounds not commonly reported in the literature. The solvent quality, in terms of metal content and amount of degradation products, seems to be the most influential parameter on the concentrations of acetaldehyde and ammonia the CO2 product gas. In addition, the ammonia slip was found to be correlated with temperature of the overhead stripper system.
High ammonia emissions were experienced in periods where plant was operated with a highly degraded solvent. For ammonia concentrations exceeding 60 ppmv, precipitation of salts as ammonia combines with CO2, caused operational upsets in the stripper overhead system due blocking and extensive pressure drop. Hence, special considerations for solvent quality management should be given with respect to ammonia emissions from CO2 stripper. It should be noted that the presented results are only typical and valid for MEA and the process parameters at TCM.
The variation of the measurements suggests that the limitation of the trace compounds in the CO2 product is challenging and sensitive to many parameters. This is also likely to be valid for other amines.
Acknowledgements
The authors gratefully acknowledge the staff at TCM DA, Gassnova, Equinor, Shell and Total for their contribution and work at the TCM DA facility. The authors also gratefully acknowledge Gassnova, Equinor, Shell and Total as the owners of TCM DA for their financial support and contribution.
Appendix A. Airborne Lab International analysis details
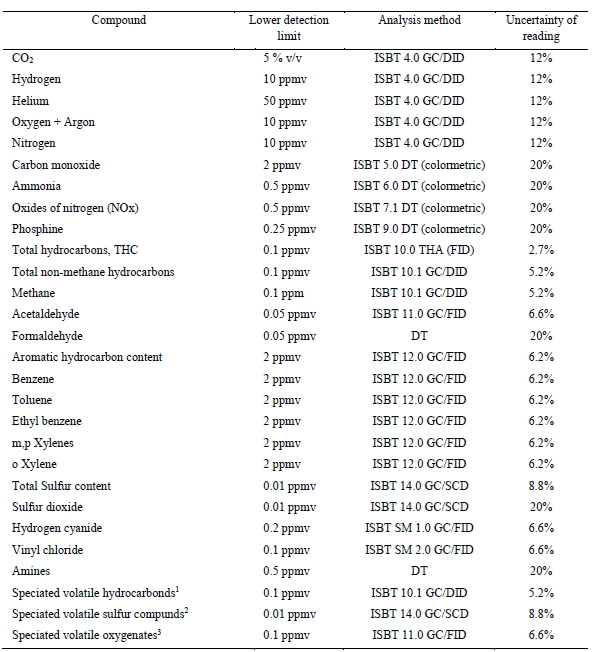
Table 6: CO2 product analysis provided by Airborne labs.
1Ethane, Ethylene, Propane, Propylene, Isobutane, n-Butane, Butene, Isopentane, n-pentane, Hexanes+
2Hydrogen sulfide, Carbonyl sulfide, Methyl mercaptan, Ethyl mercaptan, Dimethyl sulfide, Carbon disulfide, t-Butyl mercaptan, Isopropyl
mercaptan, n-Propyl mercaptan, Methyl propyl sulfide, 2-Butyl mercaptan, i-Butyl mercaptan, Diethyl sulfide, n-Butyl mercaptan, Dimethyl disulphide
3Dimetyl ether, Ethylene oxide, Diethyl ether, Propionaldehyde, Aceton, Methanol, t-Butanol, Ethanol, Isopropanol, Ethyl acetate, Methyl ethyl ketone, 2-Butanol, n-Propanol, Isobutanol, n-Butanol, Isoamyl alcohol, Isoamyl acetate
References
- The open-source centre at TCM, https://catchingourfuture.com/
- de Visser E, Hendriks C, Barrio M, Mølnvik MJ, de Koeijer G, Liljemark S, Le Gallo Y. Dynamis CO2 quality recommendations. Int. Journal of Greenhouse Gas Control, Vol. 2, Issue 4, 2008, p. 478-484
- Porter RTJ, Fairweather M, Pourkashananian M, Woolley RM. The range and level of impurities in CO2 streams from different carbon capture sources. Int. Journal of Greenhouse Gas Control, Vol. 36, 2015, p. 161-174
- Abbas Z, Mezher T, Abu-Zahra MRM. Evaluation of CO2 Purification Requirements and the Selection of Processes for Impurities Deep Removal from the CO2 Product Stream. Energy Procedia, Volume 37, 2013, p. 2389-2396,
- DNVGL-RP-F104. Design and operation of carbon dioxide pipelines, 2017
- IEA GHG. Impact of CO2 impurity on CO2 compression, liquefaction and transportation. Report 2016/01, April 2016
- Faramarzi L, Thimsen D, Hume S, Maxon A, Watson G, Pedersen S, Gjernes E, Fostås B, Lombardo G, Cents T, Morken AK, Shah MI, de Cazenove T, Hamborg ES. Results from MEA testing at the CO2 Technology Centre Mongstad: Verification of baseline results in 2015. Energy Procedia, Volume 114, 2015, p.1128-1145
- Gentry PR, House-Knight T, Harris A, Greene T, Campleman S. Potential occupational risk of amines in carbon capture for power generation. Int Arch Occup Environ Health (2014) 87:591–606
- Morken AK, Pedersen S, Nesse SO, Flø NE, Johnsen K, Feste JK, de Cazenove T, Faramarzi L, Vernstad K. CO2 capture with monoethanolamine: solvent management and environmental impact (GHGT-14, 2018)
- Lombado G, Shah MI, Fostås B, Hvidsten OA, Faramarzi L, Cazenove TD, Lepaumier H, Rogiers P. Results from aerosols measurement in amine plant treating gas turbine and residual fluidized catalytic cracker flue gases at the CO2 Technology Centre Mongstad (GHGT-14 ,2018)
- Kempra J, Sutherland L, Watt J, Santos S. Evaluation and analysis of the performance of dehydration units for CO2 capture, Energy Procedia 63 (2014) p. 7568 – 7584
- Purcell T. Effects of Contaminants on Molecular Sieves, Hydrocarbon Engineering, 1997
- Morken AK, Pedersen S, Kleppe ER, Wisthaler A, Vernstad K, Ullestad Ø, Flø NE, Faramarzi L, Hamborg ES. Degradation and Emission Results of Amine Plant Operations from MEA Testing at the CO2 Technology Centre Mongstad, Energy Procedia 114, 1245-1262
Results from 30 wt% MEA performance testing at the CO2 Technology Centre Mongstad (2016)
Erik Gjernesa,*, Steinar Pedersenb, Toine Centsc, Guillaume Watsond, Berit F. Foståsb, Muhammad Ismail Shaha, Gerard Lombardoa,e, Coralie Desvignese, Nina Enaasen Fløe, Anne Kolstad Morkenb,e, Thomas de Cazenovee, Leila Faramarzib,e, Espen Steinseth Hamborgb,e
aGassnova SF, Dokkvegen 10, 3920 Porsgrunn, Norway bStatoil ASA, PO Box 8500, 4035 Stavanger, Norwa cSasol Technology, PO Box 5486, Johannesburg 2000, South Afric dShell Global Solutions International B.V., PO Box 663, 2501CR The Hague, The Netherlands eCO2 Technology Centre Mongstad (TCM DA), 5954 Mongstad, Norway *Corresponding author
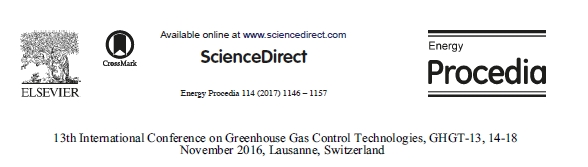
(http://creativecommons.org/licenses/by-nc-nd/4.0/).
Peer-review under responsibility of the organizing committee of GHGT-13.
doi: 10.1016/j.egypro.2017.03.1276
Abstract
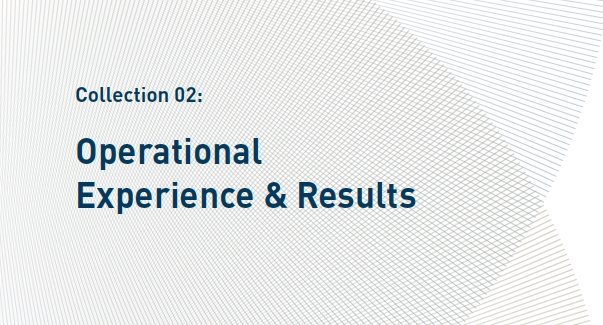
In 2015, the CO2 Technology Center Mongstad (TCM DA), operated a test campaign using aqueous monoethanolamine (MEA) solvent at 30 wt%. The main objective was to demonstrate and document the performance of the TCM DA Amine Plant located in Mongstad, Norway. The main elements were: verifying mass balances over the capture plant, revise the performance baseline from 2014, challenge the plant capacity, investigate mist/aerosol induced emission to the air and parameter variation in order to further stretch the plant performance. The current paper presents an overview of the campaign and reports on mass balance and plant performance.
1. Introduction
The CO2 Technology Centre Mongstad (TCM DA) is located next to the Statoil refinery in Mongstad, Norway. TCM DA is a joint venture set up by Gassnova representing the Norwegian state, Statoil, Shell, and Sasol. The facility run by TCM DA entered the operational phase in August 2012 and it is one of the largest post-combustion CO2 capture test centres in the world. A unique aspect of the facility is that either a flue gas slipstream from a natural gas turbine based combined heat and power (CHP) plant or an equivalent volumetric flow from a residual fluidized catalytic cracker (RFCC) unit can be used for CO2 capture. The CHP flue gas contains about 3.5% CO2 and the RFCC flue gas contains about 13-14% CO2. One of the main test plants at TCM DA is a highly flexible and well-instrumented amine plant. The amine plant was designed and constructed by Aker Solutions and Kværner to accommodate a variety of technologies, with capabilities of treating flue gas streams of up to 60,000 standard cubic meters per hour. The plant is being offered to vendors of solvent based CO2 capture technologies to, among others, test; (1) the performance of their solvent technology, and (2) technologies aimed to reduce the atmospheric emissions and environmental impact of amines and amine based degradation products from such solvent based CO2 capture processes. The objective of TCM DA is to test, verify, and demonstrate CO2 capture technologies suitable for deployment at full-scale. Up to now the vendors Aker Solutions, Alstom, Cansolv Technologies Inc. and Carbon Clean Solutions Ltd. have successfully used the TCM DA facilities to verify their CO2 capture technologies.
2. The 2015 MEA campaign
From July to October 2015 a test campaign capturing CO2 from flue gas from the CHP plant at Mongstad refinery was executed at TCM. The flue gas has typically 3.5% CO2 while the solvent comprised 30% aqueous monoethanolamine (MEA). The campaign was a joint project between TCM DA and its owners Gassnova, Statoil, Shell, and Sasol.
The campaign was split in five test series:
- Verify mass balances
- Revise the performance baseline
- Challenge the plant capacity
- Mist investigation
- Stretch targets
Series 1: The verification of the mass balances is described in section 4. The flow and composition measurements and methods for calculating total and CO2 mass balances are explained in detail and performance results are given. This test series (Series 1) was carried out at a flue gas flow rate of about 47,000 Sm3/h. Data collection was done under stable operating conditions and when the capture rate was 85%.
Series 2: The plant performance for operating conditions very similar to those reported from TCM in 2014 [1] was investigated with the new gas phase composition measurements that provided improved control of the mass balances. This test series (Series 2) used the stripper bottom temperature as the controlling variable and the solvent circulation rate was used to adjust capture rate as close as possible to 85% before experimental data was collected. The optimum performances for operation without and with the use of anti-foam were identified by the obtained u-curves, showing relation between the specific reboiler duty and the stripper bottom temperature or the lean loading. Results are given in section 5.
Series 3: The use of anti-foam improved significantly the plant performance. It also became clear that using anti- foam would allow stable plant operation at the full design flue gas flow plant capacity. Therefore a test series (Series
3) was run with 59,000 Sm3/h flue gas flow rate. The plant performance was documented according to the independent verification protocol (IVP) [2]. This new baseline is reported in [3] and will replace the TCM baseline published in 2014 [1]. Results from reducing absorber packing is, however, presented in section 6.
Series 4: A two week period of the campaign was used to investigate effect of mist/aerosol particles in the incoming flue gas on emissions to atmosphere (Series 4). This is reported in [4].
Series 5: The test series 5 (stretched targets) was planned to include tests with the use of lean vapor compressor (LVC, see bottom right corner of Figure 1), increased amine concentration (40%) and CO2 capture from flue gases at elevated CO2 concentrations. Due to time constraints, only the latter part of test series 5 was implemented. All tests were with the use of anti-foam and section 6 presents results from tests made from 3.6 to and 9 % CO2 in the flue gas flow into the absorber.
The total campaign included close to 2,000 hours of plant operation and results are reported in several papers that cover emissions and degradation [5], reclaiming [6] and corrosion [7].
Table 1 below presents an overview of the test series and main parameter ranges used during the 2015 MEA campaign at TCM.
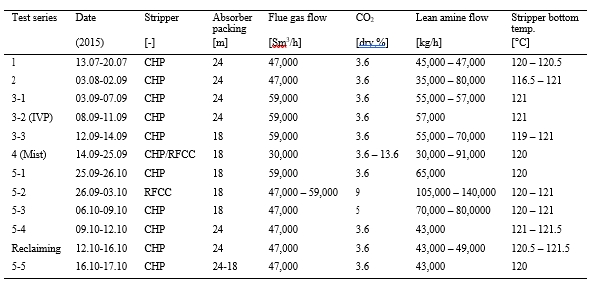
Table 1. Overall test activities with reference to tests series: 1 Verify mass balances, 2 Revise the performance baseline, 3 Challenge the plant capacity, 4 Mist investigation and 5 Stretch targets. Plant performance documented according to the independent verification protocol [2] is labeled 3-2 (IVP). The test series 5 covered variation in packing height and CO2 in flue gas into the absorber. At the end of the campaign, reclaiming was performed followed by two days of CO2 capture. The test series includes two weeks plant stop between test series 1 and 2 and a two days stop between test series 5-2- and 5-3. Stripper bottom pressure was typically maintained at around 0.95 barg.
3. The amine plant
The amine plant was designed and constructed by Aker Solutions and Kværner. It is a generic and highly flexible plant allowing testing at different configurations and with a wide range of flue gas compositions and flow rates. The process flow diagram is shown in Figure 1. The plant capacity is about 80 and 274 tonnes of CO2 per day for the CHP and RFCC flue gas operations respectively. The flue gas blower output capacity is up to about 270 mbar and 70,000 Sm3/h. The flue gas is cooled by a direct contact cooler with wash water. Water saturated flue gas flows upwards the rectangular cross-section absorber tower where it comes into contact with falling lean solvent solution. The absorber has three beds of structured packing and column packing heights can be 24, 18 or 12 m. Liquid distributors, liquid collector trays and mist eliminators are installed at various locations in the tower. The flue gas depleted in CO2 passes through two recirculating water wash stages before being emitted to the atmosphere. The process is operated with water balance. The water washes are used to control the depleted flue gas temperature and water content.
The CO2 rich solvent solution is pre-heated by exchange with hot lean solution and pumped to the upper part of a stripper tower. The rich solution falls down the stripper packing section and comes into contact with rising steam and released CO2. The lean solution is collected at the stripper bottom section and is circulated through a steam-heated thermosiphon reboiler system which provides the heat necessary to release the CO2. The lean solution is pumped back to the top of the absorber packing.
The amine plant has two independent stripper columns with overhead condenser systems. Both columns have a total height of 30 m. The structured packing internals are of 8 m height. One stripper is designed for the CHP flue gas and measures 1.3 m in diameter while the other stripper is 2.2 m in diameter. The second stripper is suited for higher flow capacities and is utilized when testing flue gases of higher CO2 content.
The CO2 product stream leaves the stripper and is cooled with recovery of condensate that is returned to the stripper as a reflux. The cooled CO2 stream is vented. When CHP flue gas is used it is possible to recycle a portion of the CO2 to the CHP flue gas upstream of the direct contact cooler. This allows for testing a range of CO2 concentrations in the inlet flue gas stream. More details on the plant design and equipment can be found in [1,2].
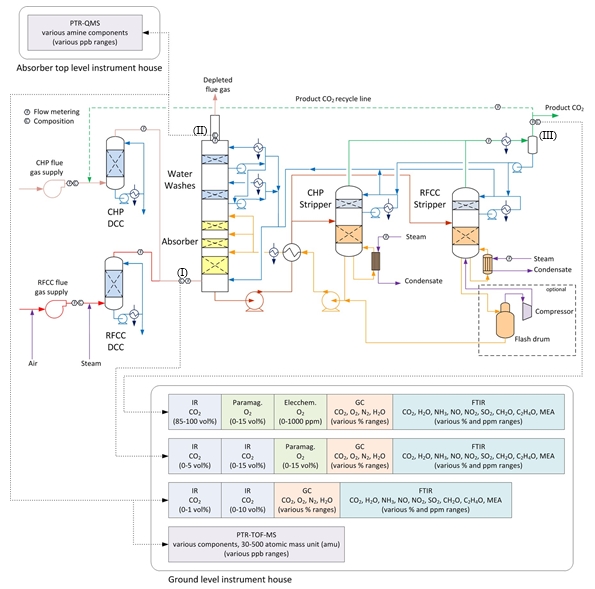
Figure 1. The TCM amine plant with two flue gas sources, CHP and RFCC, and the corresponding two strippers. Flue gas analyzers and flow meters are located at absorber inlet (I), outlet/depleted flue gas (II) and CO2 product (III), see also section 4, Table 2 and Table 3. The sets of IR meters for absorber in and out, IR CO2 (0 – 5 vol%)/IR CO2 (0 – 15 vol%) and IR CO2 (0 – 1 vol%)/IR CO2 (0 – 10 vol%) are referred to as IR-low and IR-high in Table 3. The dotted green line shows that CO2 can be recycled back to the absorber inlet for tests at elevated CO2 concentration in the flue gas flow.
4. Mass balance closure (Series 1)
The amine plant is planned and equipped for conducting research and development activities and in 2015 TCM completed implementation of a major upgrade of the gas phase composition measurement equipment. The original set up was with one common FTIR analyzer that in 90 minute cycle shifted between measuring each of the tree gas streams [1]. Figure 1 shows the new gas composition measurement setup that includes multiple gas composition analyzers at each gas stream providing continuous measurements. The CO2 measurements are based on fourier transform infrared spectroscopy (FTIR), infrared gas analysis (IR) and gas chromatography (GC). Absorber in and out have IR meters that cover both % and ppm range [3].
During the first part of the MEA 2015 test campaign the total- and CO2-mass balance of the amine plant was checked carefully. There are two meters for the inlet flue gas flow rate, one meter for the flue gas flow out of absorber and two meters for the CO2 product flow, see Table 2. The absorber out flue gas flow meter FT-2431 does not provide reliable measurements [1], thus flow out of absorber (V& ) is also calculated from flow into the absorber assuming all components except water (CH2O) and CO2 (CCO2) are conserved:
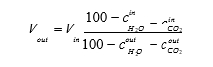
The mass balance is calculated as sum of absorber out and product flow divided by absorber in flow. This balance is based on 15 minutes averages of the measured gas flows in and out of the plant. No shift in time is applied, i.e. in order to take into account the residence time from gas phase absorber to gas phase stripper. Thus, stable operation is assumed. In Table 2 mass balance for four combinations of flow instruments, method A to D, are shown. Method A to C provide mass balances close to 100%. Method D which uses the absorber out pitot-based meter FT-2431 provides a mass balance around 95%, which suggests that this meter reports too low flow. For reference the CO2 concentration (dry) into the absorber is shown. Around July 14 the CHP changed firing mode which resulted in a decrease in the CO2 content in the flue gas and was stable for the rest of the week.
As shown in Figure 1 above there are four CO2 analysers at the absorber inlet and at the outlet and three analysers at the product stream. Based on method A to C in Table 2 the CO2 mass balance has been calculated using a combination of the CO2 analyzers. Table 3 shows the cases investigated. For A1, A2, B1 and C1 the gas composition out of stripper is assumed to be only CO2 and water were the latter is calculated from pressure and temperature assuming saturated conditions (f(T,p)). For A3 and A4 CO2 concentration is based on GC and FTIR measurements. All three methods give wet CO2 > 97 vol%.
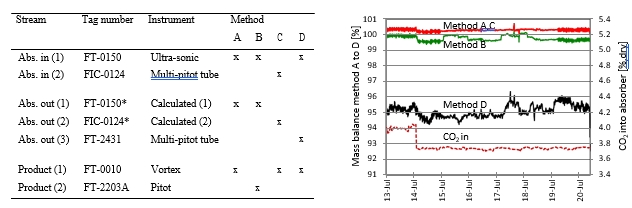
Table 2. To the left instrumentation for absorber in (Abs. in) and out (Abs. out) and product flow. The absorber out flow (1) and (2) are marked with asterisks since these flows are calculated from absorber in flows by use of equation 1. Mass balance based on four combinations of instruments, methods A to D, are presented for one week of operation in the figure to the right. CO2 concentration (dry) into the absorber is also shown.
The CO2 mass balance calculated as:
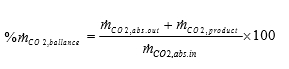
Figure 2 shows that method A1 to A4 and C1 results in CO2 mass balance within 100 +/- 5%. Method B1 which is based on the gas flow rates of method B has a larger spread and is underestimating the CO2 product flow resulting in an average CO2 mass balance around 90%. In conclusion all composition meters results in an acceptable CO2 mass balance, but flow should be based on method A or C.
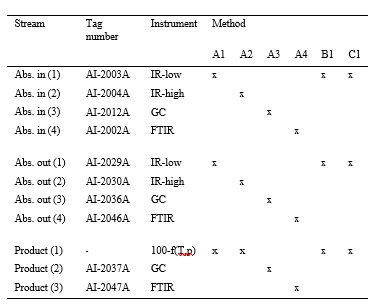
Table 3. Instruments for CO2 measurement at absorber in (Abs. in) and out (Abs. out) and product flow. With reference to Table 2 the measurements were combined with flow meters according to method A for four sets of instruments while method B and C were presented using the IR-low and CO2 product concentration by difference from calculated moisture (f(T,p)).
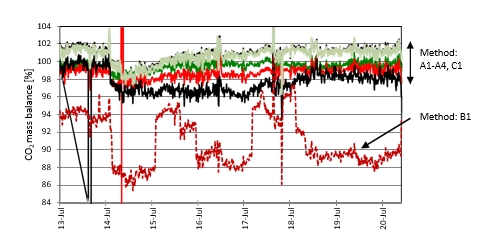
Figure 2. CO2 mass balance based on method A1 to A4, B1 and C1 in Table 3.
5. Performance (Series 2)
One of the objectives was to investigate the plant performance under the improved control of heat and mass balances as explained above. A key question from the 2014 baseline testing [1] was whether the CHP stripper was operated under optimal conditions. Indicators of poor stripper performance are; fluctuating temperature sensors, a radial temperature gradient, and a reduced temperature gradient over the packing section. This results in higher temperatures above the stripper packing, 100 to 102°C, as well as higher pressure drop over the stripper packing section. Reasons for this behaviour could be moderate foaming or maldistribution over the packing section of the upcoming steam and/or the down coming liquid solvent. TCM had some earlier experience that adding anti-foam to the solvent flow could improve the situation.
In industrial amine units, anti-foam chemicals are often injected when operators suspect foaming to occur in the columns, which can lead to large solvent carry-over to the downstream overhead units. This could result in production turn down or worse, unplanned shutdown. The increase or rapid fluctuation of pressure drop over the amine column, and the unexpected level change in the amine unit (with rapid change of the control valve) are general indicators for foaming. Note that such foaming event in the TCM facility was likely not experienced during the campaign, and that the columns were operating within their design hydraulic operating window (i.e. no flooding).
This part of the test campaign repeated conditions from the 2014 tests at TCM [1] and included operation with and without the use of anti-foam. The main parameters used for creating u-curves and determining the optimum steam reboiler duty (SRD) under series 2 are given in Table 1 above. The tests were run at stable conditions with CO2 inlet concentration about 3.6 vol %, dry. The stripper bottom pressure was held constant at 0.95 barg. The stripper bottom temperature was used as the controlling variable. For each selected temperature one point on the u-curve was created. The solvent flow rate was used to tune in the capture rate as close as possible to 85% at each test temperature before data collection.
The data for u-curves were prepared as shown in Figure 3 below. At a set stripper bottom temperature the lean solvent flow was tuned in order to achieve 85% capture rate. Rich and lean solvent was sampled during stable operation. Rich and lean loading data were obtained. The rich loading were always close to the equilibrium value of 0.50 mole CO2/mole amine while the lean loading responded closely to the set stripper bottom temperature. The solvent flow rate was reduced in corresponding steps with the lean loading.
The test series started without the use of anti-foam. The main performance parameters are shown in Table 4 below. The SRD value is calculated based on the difference in steam enthalpy (ΔH) over the reboiler, the steam mass flow (ṁsteam) and mass flow of CO2 out of the product line (ṁCO2):
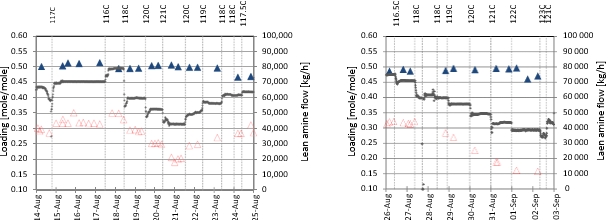
Figure 3. To the left tests without anti-foam and to the right tests with the use of anti-foam. Lean and rich loading are shown as filled blue and open red triangles, respectively. Lean amine flow (black points) is adjusted to get approximatively 85% CO2 capture and then kept constant at each level of stripper bottom temperature. The latter is indicated as vertical dotted lines.
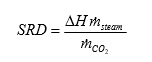
The CO2 capture rate is calculated based on a simplified expression using CO2 concentration in and out of the absorber:
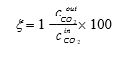
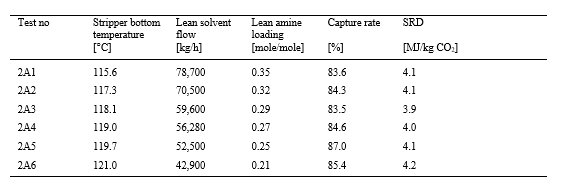
Table 4. Results for test cases without the use of anti-foam. The use of “A” and “B” (Test no) in Table 4 and Table 5 identifies tests without and with anti-foam, respectively. Loading is reported as mole CO2/mole amine.
The stripper performance was observed by following the temperature profiles over the stripper packing section, the pressure drop over the packing and the temperature sensor placed above the stripper packing. All the indicators showed that the stripper was not performing optimal and therefore the anti-foam injection was decided. At August 26 four litre of anti-foam was added. After anti-foam had been injected all the indicators showed good stripper performance. The test series were continued in order to create a u-curve and determine optimum SRD value also for operation with the use of anti-foam. The strategy was to inject one litre of anti-foam if the indicators again showed signs of undesired behaviour to secure optimal performance for all the points on the u-curve. Figure 4 below illustrates how this operation was managed for the whole test series.
The most important performance parameters for the test cases with the use of anti-foam are shown in Table 5 below.
Data from Table 4 and Table 5 were used to create the u-curves shown in Figure 5 below.
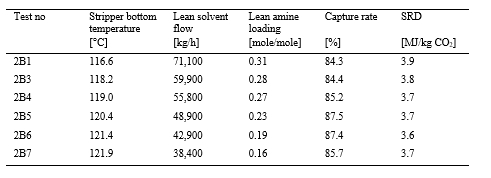
Table 5. Results for test cases with the use of anti-foam. The use of “A” and “B” (Test no) in Table 4 and Table 5 identifies tests without and with anti-foam, respectively. Loading is reported as mole CO2/mole amine.
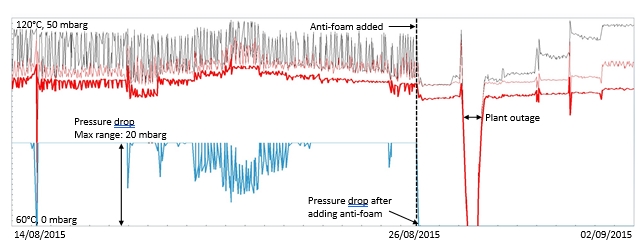
Figure 4. Stripper performance and result of using anti-foam is shown for the whole test series 2, see Table 1.The dashed vertical line shows the first use of anti-foam August 26 2015. The upper black and red thin lines show temperature sensors inside the stripper packing. The bold red and blue lines are temperature above the stripper packing and pressure drop over the stripper packing, respectively. Note that before adding anti-foam the pressure drop exceeded max range of 20 mbarg for the meter. Anti-foam resulted in immediate stabilising of temperatures and reduced the pressure drop over stripper. The further drop in temperature to the right of this is due to a short plant outage.
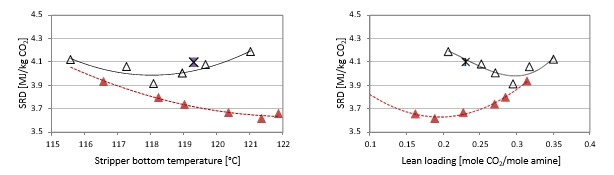
Figure 5. U-curves from series 2 and operation with anti-foam are shown as red filled triangles while results without the use of anti-foam are shown as open triangles. To the left SRD is given as function of stripper bottom temperature. To the right SRD is given as function of lean loading. The asterisk represents the 2014 baseline [1] made without the use of anti-foam.
The significant effect of anti-foam is clearly seen from the graphs. The stripper behaviour becomes much more optimal and the heat is no longer lost through the stripper overhead but used in efficient release of the CO2 from the solvent amine. This leads to significantly lower specific reboiler duty and the optimum operation is shifted towards much leaner amine and less solvent circulation.
During test series 3 the independent verification protocol (IVP) and the 3rd party measurements were documented. Since the use of anti-foam allowed stable plant operation also at the full flue gas design capacity this operating condition was chosen for the verification testing, see series 3-1 (IVP) in Table 1. This test series established at 59,000 Sm3/h flue gas flow will replace the baseline published in 2014 [1] and is reported in [3]. In Table 6 the main characteristics for the 2014 baseline are compared with test results from series 2. These tests were conducted at about the same flue gas flow of 47,000 Sm3/h, CO2 below 4 vol.% and with 24 meters of absorber packing. For comparison the table includes test “2A5” that have similar parameters as the 2014 baseline. The cases “2A3” and “2B6” represent optimum energy performance for operation without and with the use of anti-foam, see also Figure 5 above. The use of anti-foam gave about 20% reduction in lean amine flow rate and 12% reduction in SRD compared to the 2014 baseline.
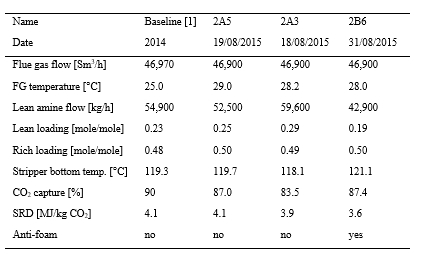
Table 6. Comparison of the 2014 baseline and results from optimal performance testing. All tests are with 24 m absorber packing and around 3.6% dry CO2 in flue gas from the CHP. Data sets “2A5” and “2A3” are without the use of anti-foam and are taken from Table 4, while “2B6” is with anti-foam and data are taken from Table 5. Loading is reported as mole CO2/mole amine.
6. Parameter variations (Series 3 and 5)
The test series 3 and 5 included tests made with 18 m absorber packing height and also tests at elevated CO2 concentration in the flue gas flow into the absorber. These parameter variations will be discussed below.
With a new baseline established for full flue gas flow capacity (59,000 Sm3/h) and use of 24 m absorber packing height [3] it was suggested to challenge the plant capacity even further with a test series at 18 m packing height. The flue gas flow rate was fixed at 59,000 Sm3/h and anti-foam was injected prior to the tests if needed. These results are presented in Table 7. In case “3A3” the absorber packing height was reduced from 24 to 18 m. The SRD value increased and rich loading decreased from 0.48 to 0.46, indicating that 18 m is not sufficient to give equilibrium. In case “3A4” the stripper bottom temperature was decreased from 121 to 119°C, resulting in a corresponding increase in lean loading from 0.20 to 0.26 and the capture rate decreased from 83 to 68%. In case “3A7” the stripper bottom temperature was increased to 120°C giving a lean loading of 0.23 and capture rate 76%. In case “3A8” the target was to achieve 85% capture rate at 120°C by changing the lean solvent flow rate. An increase in flow rate from 59,000 to 67,700 kg/h was required. For all these parameter variations the SRD was 3.6 to 3.9 MJ/kg CO2.
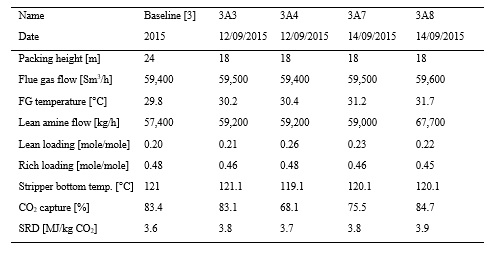
Table 7. Parameter testing with 18m packing height compared to the new baseline (all with anti-foam). Loading is give as mole CO2/mole amine.
Test series 5 also included tests at elevated CO2 concentrations. The test series 5-2 and 5-3 started at stable conditions with 18 m packing height, flue gas flow 46,200 Sm3/h and stripper bottom temperature 120.5°C. The objective was to investigate performance with increased CO2 flue gas inlet concentration. At TCM the CO2 inlet concentration can be varied by recycling CO2 from the CO2 product vent and back into the incoming flue gas. The CO2 concentration was varied in controlled steps between nine and three percent (wet). The capture rate was kept close to 85% by adjusting the parameters stripper bottom temperature and lean solvent flow rate. The observed effects on SRD and solvent loading are shown in Figure 6 below.
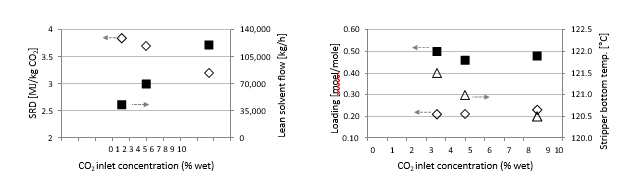
Figure 6. To the left SRD (diamonds) and lean solvent flow rate (squares) observed as function of inlet CO2 concentration. To the right lean (diamonds) and rich (squares) solvent loading and stripper bottom temperature (triangles) observed as function of inlet CO2 concentration.
The testing started with CO2 concentration about 9 % wet and lean solvent flow 120,000 kg/h. The amount of captured CO2 was 7,500 kg/h. When the CO2 concentration was reduced to about 5% wet the lean solvent circulation was correspondingly reduced to 70,000 kg/h to reach 85% capture rate and the resulting amount of CO2 captured was 3,900 kg/h. The baseline conditions were then tested with 3.6 % wet CO2 inlet concentration. The CO2 captured was 2,700 kg/h.
The capture rate was within the range 85 to 88% for all the three selected test cases. From the right panel in Figure 6 it is seen that the stripper bottom temperature was only slightly adjusted between 120.5 and 121.5°C giving some minor changes in rich and lean loading.
As expected, the SRD increased with decreasing CO2 inlet concentrations. It is interesting to further investigate the trade-off between CAPEX and OPEX parameters for operating conditions relevant for various gas power turbines and exhaust gas recycling systems in order to assess how total capture cost can be minimized.
7. Conclusion
The MEA 2015 campaign at TCM has provided a verification of mass balance over the plant and shown that the CO2 mass balance based on gas phase can be maintained at a level better than +/- 5%. The plant performance presented in 2014 [1] has been revisited under operation with and without the use of anti-foam. Use of anti-foam enabled stable operation at lower lean solvent loading which resulted in lower lean amine flow rate and reduced SRD. Absorber packing height has been challenged and the results points towards operation at lower packing heights, but current tests also indicated that equilibrium was not achieved at reduced packing height. Tests at elevated CO2 concentration showed as expected reduced SRD with increasing CO2 concentration. The campaign has also resulted in reports on: new baseline [3], mist/aerosol induced emission to the air [4], emissions and degradation [5], reclaiming [6] and corrosion [7].
Acknowledgements
The authors gratefully acknowledge the staff of TCM DA, Gassnova, Statoil, Shell and Sasol for their contribution and work at the TCM DA facility. The authors also gratefully acknowledge Gassnova, Statoil, Shell, and Sasol as the owners of TCM DA for their financial support and contributions.
References
- Hamborg ES, Smith V, Cents T, Brigman N, Falk-Pedersen O, de Cazenove T, Chhaganl M, Feste JK, Ullestad Ø, Ulvatn H, Gorset O, Askestad I, Gram LK, Fostås BF, Shah MI, Maxson A, Thimsen D. Results from MEA testing at the CO2 Technology Centre Mongstad. Part II: Verification of baseline results. Energy Procedia. Volume 63; 2014. p. 5994-6011.
- Thimsen D, Maxson A, Smith V, Cents T, Falk-Pedersen O, Gorset O, Hamborg ES. Results from MEA testing at the CO2 Technology Centre Mongstad. Part I: Post-Combustion CO2 capture testing methodology. Energy Procedia, Volume 63; 2014. p. 5938-5958.
- Faramarzi L, Thimsen D, Hume S, Maxson A, Watson G, Pedersen S, Gjernes E, Fostås BF, Lombardo G, Cents T, Morken AK, Shah MI, de Cazenove T, Hamborg ES. Results from MEA testing at the CO2 Technology Centre Mongstad: Verification of baseline results in 2015. Energy Procedia (GHGT-13), Forthcoming 2017.
- Lombardo G, Fostås BF, Shah MI, Morken AK, Hvidsten OA, Mertens J, Hamborg ES. Results from aerosol measurement in amine plant treating gas turbine and residual fluidized catalytic cracker flue gases at the CO2 Technology Centre Mongstad. Energy Procedia (GHGT- 13), Forthcoming 2017.
- Morken AK, Pedersen S, Kleppe ER, Wisthaler A, Vernstad K, Ullestad Ø, Flø NE, Faramarzi L, Hamborg ES. Degradation and Emission Results of Amine Plant Operations from MEA Testing at the CO2 Technology Centre Mongstad. Energy Procedia (GHGT-13), Forthcoming 2017.
- Flø NE, Faramarzi L, de Cazenove T, Hvidsten OA, Morken AK, Hamborg ES, Vernstad K, Watson G, Pedersen S, Cents T, Fostås BF, Shah MI, Lombardo G, Gjernes E. Results from MEA degradation and reclaiming processes at the CO2 Technology Centre Mongstad. Energy Procedia (GHGT-13), Forthcoming 2017.
- Hjelmaas S, Storheim E, Flø NE, Thorjussen ES, Morken AK, Faramarzi L, de Cazenove T, Hamborg ES. Results from MEA amine plant corrosion processes at the CO2 Technology Centre Mongstad. Energy Procedia (GHGT-13), Forthcoming 2017.
Field Demonstration of Advanced CDRMax Solvent at the USDOE’s National Carbon Capture Centre and the CO2 Technology Centre Mongstad DA, Norway (2016)
Prateek Bumba*, Dr Avinash Patkar. P.E, a, Richard Mathera, Ramesh Kumara, Dr. James Halla Frank Mortonb, and Justin Anthonyb
a Carbon Clean Solutions Limited, 47, Castle Street, Reading, Berkshire, RG1 7SR, United Kingdom b Southern Company, National Carbon Capture Center (NCCC), Wilsonville, AL, USA
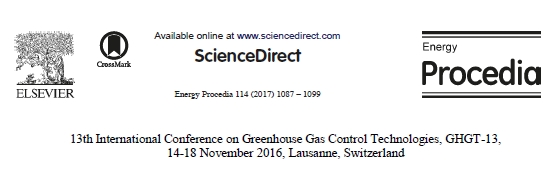
(http://creativecommons.org/licenses/by-nc-nd/4.0/).
Peer-review under responsibility of the organizing committee of GHGT-13.
doi: 10.1016/j.egypro.2017.03.1261
Abstract
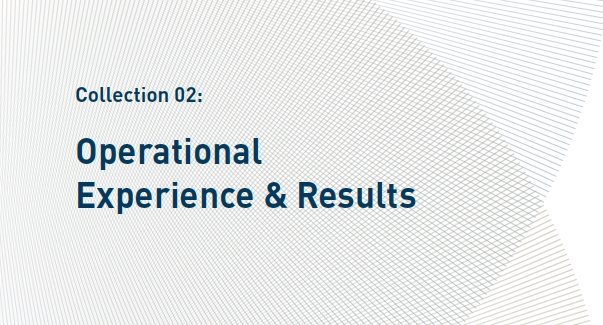
Carbon capture solvents should have a low Specific Reboiler Duty, resistance to oxidative degradation, should not be corrosive and should have low emissions to atmosphere. Carbon Clean Solutions Ltd have developed the CDRMax solvent for use on power plant flue gases. The solvent has been tested at both the National Carbon Capture Centre, USA and the Technology Centre Mongstad, Norway. At both centers the SRD, emissions to atmosphere and concentrations of metals in the solvent were measured. The results show that CDRMax was less corrosive and had a lower SRD than 30wt% MEA, had low emissions and was resistant to oxidative degradation.
1. Introduction
Carbon Clean Solutions Ltd is a company based in Reading, United Kingdom. The company offers its range of innovative solvents for gas treatment. This paper describes testing of the CDRMax solvent on a flue gas containing ~ 4 mole% CO2. This is the concentration of CO2 which occurs in flue gas from a gas-fired power plant. The solvent was tested during two campaigns. The first campaign was on the Pilot Scale Test Unit at the National Carbon Capture Centre, Alabama, USA from March 2014 to April 2014. The second test campaign was on the amine plant at the Technology Centre Mongstad, Norway from November 2015 until January 2016. During both campaigns the Specific Reboiler Duty (SRD) emissions to atmosphere and corrosion were measured.
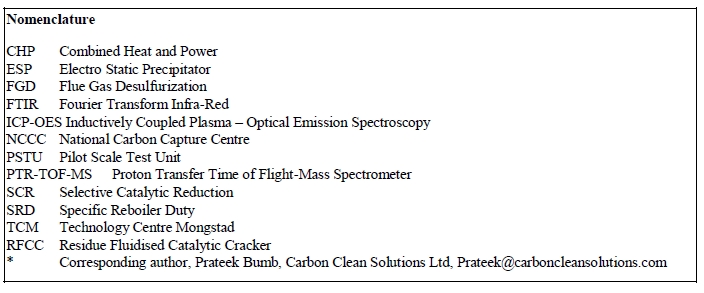
2. NCCC Campaign
2.1 Overview of the NCCC facility
The Pilot Scale Test Unit (PSTU) at the NCCC facility is a post combustion capture test facility. It can operate on coal flue gas or a simulated natural gas flue gas. The flue gas is taken as a slipstream from an 800 MW coal fired boiler. Before entering the test unit, the flue gas is treated by SCR, ESP and FGD to reduce the concentration of NOx, fly ash and SOx. If required, the flue gas is diluted with air to achieve gas fired flue gas conditions. A final polishing NaOH wash reduces the concentration of SOx still further and saturates the flue gas.
The flue gas and lean solvent flow rates can be adjusted so that the liquid to gas ratio can be varied. The absorber can be configured so that it can be operated with 12m or 18m height of packing. The dimensions of the equipment at the PSTU are shown in Table 1 below.
Column | Height, m | Outer diameter m | Number of Beds | Bed height m | Packing type |
Pre-Scrubber | 14 | 0.76 | 1 | 6.1 | Mellapakplus M202Y |
Cooler/Condenser | 9.1 | 0.61 | 1 | 3.05 | Mellapakplus M252Y |
Absorber | 32.9 | 0.66 | 3 | 6.1 | Mellapakplus M252Y |
Wash Tower | 9.1 | 0.61 | 1 | 3.05 | Mellapakplus M252Y |
Regenerator | 23 | 0.61 | 2 | 6.1 | Mellapakplus M252Y |
Table 1. The dimensions of equipment in the PSTU.
2.2 Overview of the NCCC test campaign
A series of parametric trials were conducted on the PSTU plant with the CDRMax solvent. These allowed the SRD to be measured under a range of conditions. The solvent was tested on both a coal flue gas and a simulated natural gas flue gas. However, only the simulated natural gas flue gas results are provided here. The ranges of the test conditions are provided in Table 2 below. During each test phase only one parameter was changed at a time to ensure that the impact of each change could be isolated. Laboratory analysis was carried out on solvent samples to determine water content, lean and rich loading as well as the concentration of metals.
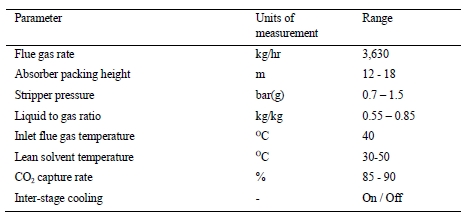
Table 2. Operating conditions for the NCCC campaign.
Table 3 below shows the composition of the flue gas used in the trials at the NCCC.
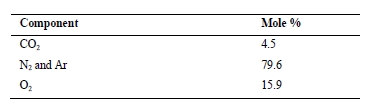
Table 3. Flue gas composition for the NCCC campaign on a dry basis.
2.4 Optimization of SRD by varying the liquid to gas ratio
A series of tests were carried out to determine the liquid to gas ratio that would provide the lowest SRD. For these tests a constant flue gas rate of 3,630 kg/hr was maintained, the flue gas temperature was 40 OC and the stripper pressure was 0.7 bar(g). The solvent flow was set to 2,000 kg/hr for the first test then increased to 2,722 kg/hr for the second test before finally being increased to 3,085 kg/hr for the third test. This gave liquid to gas ratios of 0.65, 0.75 and 0.85 kg of solvent per kg of flue gas respectively. For each test condition the steam to the reboiler was adjusted until the CO2 capture rate was 90%. As can be seen in Figure 1 below the optimal L/G was found to be close to 0.75 kg/kg.
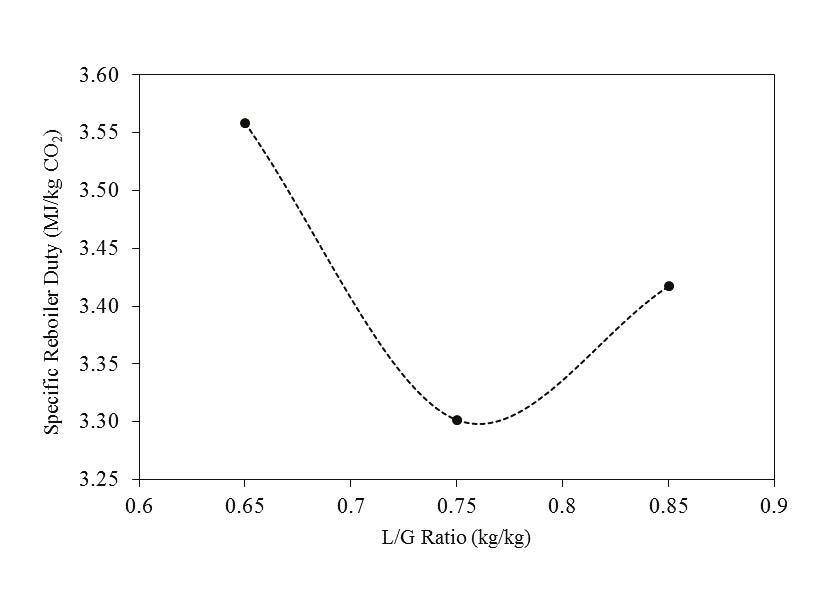
Figure 1. Optimisation of SRD for CDRMax at NCCC by varying the liquid to gas ratio while maintaining a constant stripper pressure of 0.7 bar(g).
2.5 Optimization of SRD by varying the stripper pressure
To determine the optimal stripper pressure, a series of energy measurements were made while the liquid to gas ratio was held at the optimum of 0.75 kg/kg. The stripper pressure was varied from 0.8 to 1.54 bar(g) and at each condition the steam flow to the reboiler was adjusted until the CO2 capture rate was 90%. As shown in Figure 2 below there is an optimal stripper pressure close to 1.0 bar(g) where the SRD was 3.1 MJ/kg CO2 . For the 1.0 bar(g) condition the actual CO2 capture rate was above 90%, therefore, the SRD would be lower for a capture rate of 90%. In addition, it was noted that the cross-over lean rich heat exchanger was not optimal for the CDRMax solvent. CCS Ltd simulated the SRD for the same operating conditions but with an optimized cross-over heat exchanger and an advanced stripper configuration. The SRD was projected to be reduced to 2.8 MJ/kg CO2.
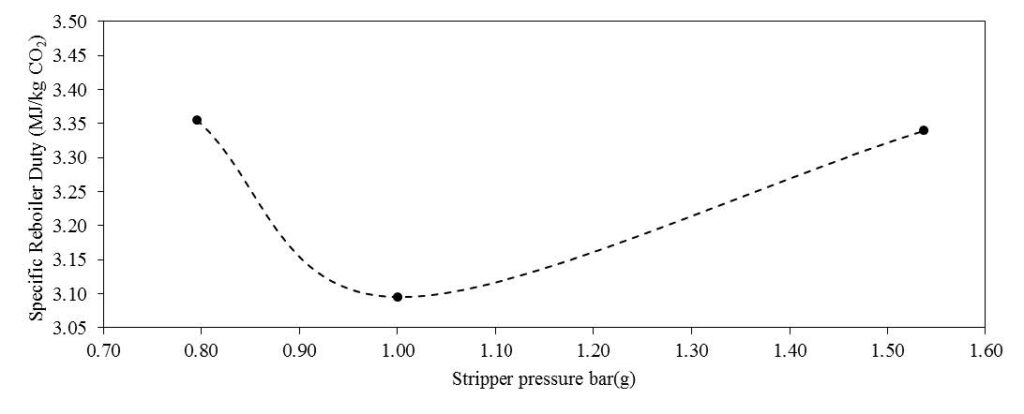
Figure 2. Optimisation of SRD for CDRMax at NCCC by varying the stripper pressure at a constant liquid to gas ratio of 0.75 kg/kg.
The NCCC have reported an optimal SRD for 30 wt% MEA of 3.5 MJ/kg CO2 at a CO2 capture rate of 86% [1]. Therefore the optimal CDRMax value of 3.1 MJ/kg CO2 at a capture rate of 90% provides an 11% reduction in the SRD. With design modifications, CCS Ltd estimate that the energy savings could be 20%.
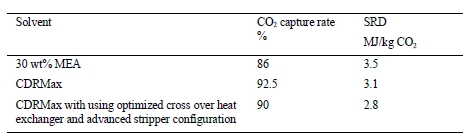
Table 4. Comparison between 30 wt% MEA, CDRMax and projected CDRMax values if optimal cross over heat exchanger and stripper design is implemented.
2.5 Effect of absorber height
To determine the effect of the absorber packing height on SRD for 90% CO2 capture efficiency, two tests were carried out with a packing height of 18m and 12m. The flue gas rate, L/G and the flue gas temperature and stripper pressure were maintained constant for both conditions while the steam flow to the reboiler was adjusted to achieve a target CO2 capture rate of 90%. There was a reduction in the SRD of 5.4% when the packing height was increased from 12m to 18m.
2.6 Emissions of ammonia
Ammonia emissions are an indicator of solvent stability against the oxidative degradation. The oxygen content in the flue gas was 15.9 mole% on dry basis. During the NCCC campaign three tests of ammonia emissions through the flue gas outlet from the water wash were made and average concentration was found to be 3.2 ppmv.
2.7 Corrosion
During a campaign using 30 wt% MEA, the NCCC had reported chromium concentrations in the solvent [2]. After 300 hours of operation the chromium concentration was 45,090 µg/L. For the CDRMax solvent, after 500 hours of operation the chromium concentration was 2,120 µg/L. Even though the CDRMax campaign was longer, the concentration of chromium was 20 times lower than for the MEA campaign.
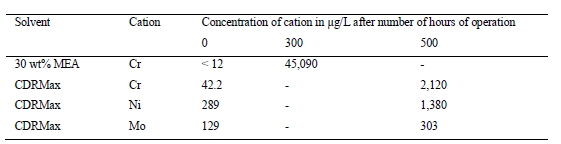
Table 5. Concentration of cations in 30wt% MEA and CDRMax reported in µg/L.
3. TCM campaign
3.1 Overview of the TCM test facility
The Technology Centre Mongstad is one of the largest post combustion capture test facilities in the world. It is highly instrumented to give a detailed understanding of the process conditions which occur within each section of the plant. The facility can operate with flue gas rates of 60,000 Sm3/hr and with flue gases from different sources. Figure 3 below shows the Process Flow Diagram for the plant. Flue gas from a Combined Heat and Power plant can be operated on its own. The flue gas is derived from natural gas combustion so is equivalent for CCGT flue gas.
Product CO2 from the stripper can be recycled into the CHP flue gas to increase the CO2 content of the inlet flue gas to 13 mole%, this provides a synthesised coal or cracker flue gas but without aerosols. Controlled amounts of cracker gas (RFCC) can be added so the effect of aerosols on emissions can be observed. During the test campaign on CDRMax all three modes of operation were used. However, only the results obtained on CHP flue gas are reported here.
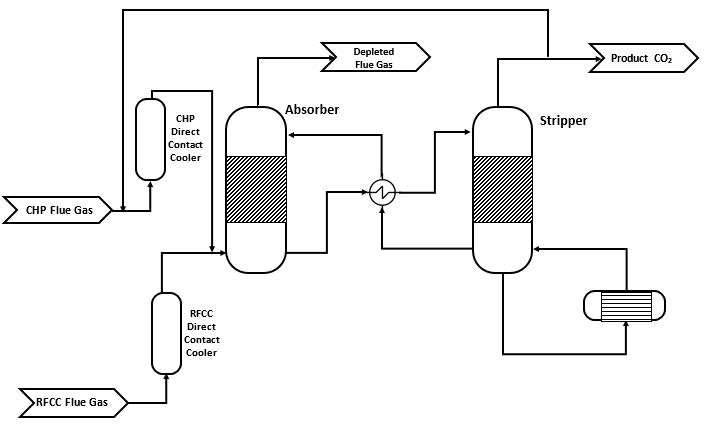
Figure 3. TCM Process Flow Diagram.
The incoming flue gas is cooled to a desired temperature and saturated in a direct contact cooler. In this vessel the gases are contacted with a recirculating stream of brackish water. The absorber can be operated with up-to 24 m height of packing. Above the absorber is a two stage water wash. Make-up water is added to the higher bed which then cascades into the lower bed before being purged into the absorber. The stripper has 8 m of packing and is heated by a plate reboiler. The details of the equipment are provided in Table 6 below.
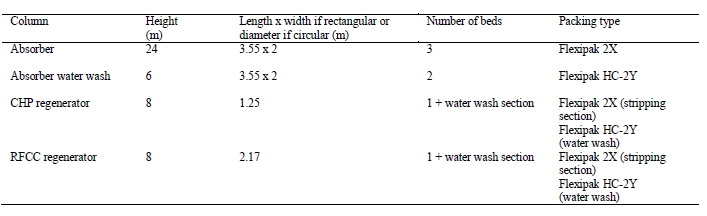
Table 6. Dimensions of equipment at the TCM.
3.2 Overview of the TCM campaign
The objective of the test campaign was to demonstrate the CDRMax solvent to determine the SRD, emissions to atmosphere, solvent degradation and corrosion of the plant. The test campaign started on the 17th November 2015 and concluded on the 6th January 2016. The CDRMax solvent was operated on a flue gas containing 3.7 mole% CO2 (dry basis). The SRD was measured at different process conditions which are shown in Table 7 below. The composition of the CHP flue gas on a dry basis is provided in Table 8 below.
Throughout the campaign, the emissions of solvent and ammonia were measured in the depleted flue gas using a Proton Transfer Time of Flight Mass Spectrometer (PTR-TOF-MS) and periodically by iso-kinetic sampling.
Further details of the emissions monitoring equipment can be found in [3].

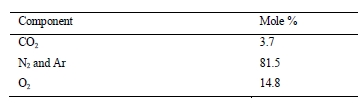
3.3 Energy required for the regeneration of solvent
3.3.1 Comparison between 30wt% MEA and CDRMax
The TCM have previously reported test results for 30 wt% MEA [4]. The paper describes that streaming was observed in the stripper column. This was corrected by the addition of anti-foam. It was found that after the addition of anti-foam the SRD was reduced. During this test, the flue gas rate was 47,000 Sm3/hr, the flue gas temperature was 25 OC, lean solvent temperature was 25 OC, the CO2 capture rate was 85 %, stripper pressure 0.9 bar(g) and 24 m of absorber packing were used. The liquid to gas ratio was optimized to provide the lowest SRD value. CCS Ltd replicated this test with the CDRMax solvent to provide a comparison.
Figure 4 below shows results of the testing. As can be seen, the 30 wt% MEA with no anti-foam the SRD was 4.0 MJ/kg CO2. Following the addition of anti-foam, for 30 wt% MEA the SRD was reduced to 3.7 MJ/kg CO2. For CDRMax, the SRD was 3.3 MJ/kg CO2. The CDRMax solvent showed a 16.7 % energy reduction compared to 30 wt% MEA without anti-foam and a 10% reduction from 30 wt% with anti-foam. If the CCS Ltd patented stripper configuration were incorporated into the design then the SRD would be reduced further still.
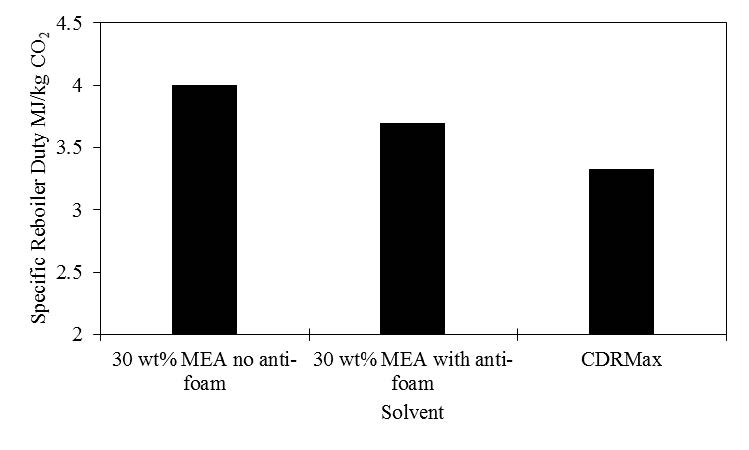
Figure 4. Comparison of SRD between 30 wt% MEA (with and without anti-foam) and CDRMax solvents.
3.3.2 Optimization of SRD
Parametric tests were carried out to optimize the specific reboiler duty for the CDRMax solvent. The inlet flue gas and lean solvent temperatures were held constant at 35 OC. The flue gas rate was 56,000 Sm3/hr and the CO2 capture rate was 90 %. The CDRMax solvent was operated at three different stripper pressures of 0.8, 1.0 and 1.2 bar(g). At each pressure the liquid to gas ratio was varied and the steam rate to the reboiler adjusted until the target CO2 capture rate was achieved. The lowest SRD found for each stripper pressure is plotted in Figure 5 below. As can be seen the lowest recorded SRD of 3.25 MJ/kg CO2 was found at 1.0 bar(g). The temperature of gas inlet the absorber and lean solvent temperature are varied to find the best fit of operating conditions for the CDRMax keeping the stripper pressure at 1 bar(g) the corresponding liquid to gas ratio.
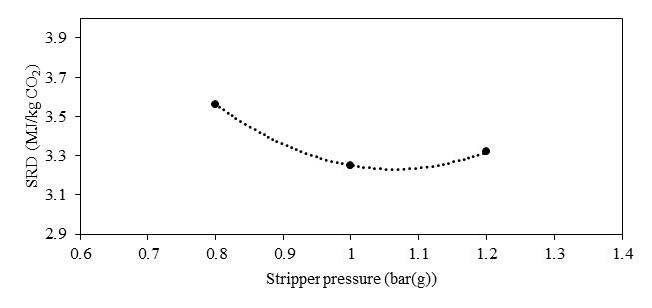
Figure 5. Optimisation of stripper pressure for CDRMax solvent.
3.4 Emissions
3.4.1 Emissions of solvent in the depleted flue gas
The emissions of solvent were monitored in the depleted flue gas throughout the campaign using a PTR-TOF-MS instrument. The results are shown in Figure 6 below and are reported on a 24 hour average basis. The permitted level of emissions was 6 ppmv which is shown by the dashed line. As can be seen, the emissions remained below 1 ppmv for the duration of the campaign.
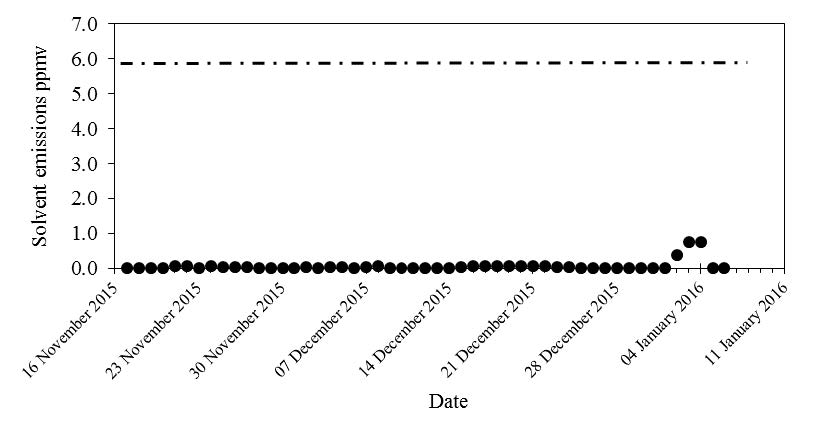
Figure 6. Emissions of solvent in the depleted flue gas during the CDRMax campaign. Values are 24 hour average and measured by PTR-TOF-MS. The dashed line is the emissions permit limit of 6 ppmv.
To verify the PTR-TOF-MS instrument values, periodic iso-kinetic samples of emissions were also taken. The condensate from the samples were analysed by LC-MS. The concentrations in the condensate were then used to calculate the concentration of the solvent in the gas phase. The results of the iso-kinetic sampling are shown in Table 9 below. As can be seen, the values are all below 1 ppmv which gives good agreement with the PTR-TOF-MS measurements.
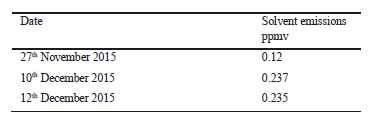
Table 9. Emissions of solvent during the TCM campaign. Values determined by iso-kinetic sampling. Condensate analysed by LC-MS.
3.4.2 Emissions of ammonia in the depleted flue gas
The emissions of ammonia in the depleted flue gas were measured by the PTR-TOF-MS throughout the campaign. The results are shown in Figure 7 below. The emissions limit for ammonia was 33 ppmv and this is shown on the figure by a dashed line. As can be seen, the emissions achieved during the campaign were generally less than 2 ppmv. Emissions of ammonia are indicative of oxidative degradation of the solvent. The ammonia emissions are stable and low, this indicates that the CDRMax solvent is resistant to oxidative degradation.
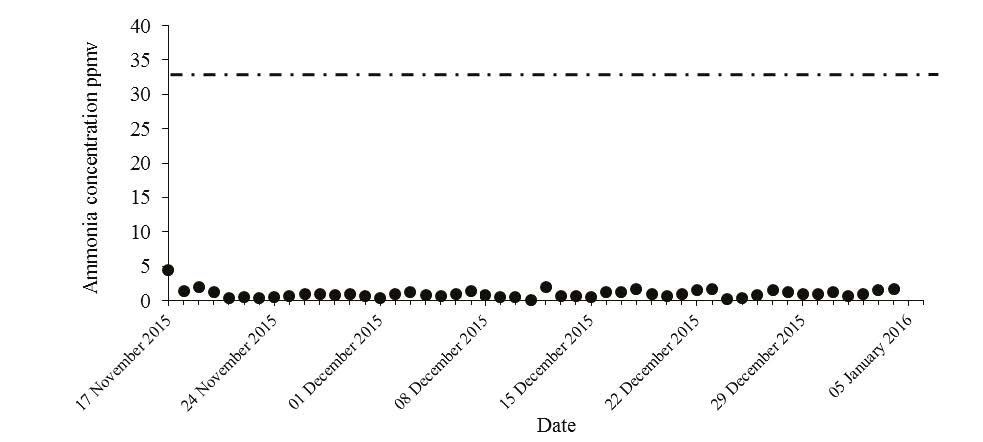
Figure 7. Emissions of ammonia in the depleted flue gas during the CDRMax campaign. Values measured by PTR-TOF-MS and reported on a 24 hour average basis. The dashed line represents the emissions permit limit of 33 ppmv on a 24 hour average basis.
3.5 Operating hours
The cumulative operating hours achieved during the campaign are shown in Figure 8 below. As can be seen there were very few interruptions in the progress of the campaign. The interruptions that did occur were minor plant issues and none were associated with the solvent operation. The solvent on-stream factor over the campaign was 100% while the overall on-stream factor was 97%.
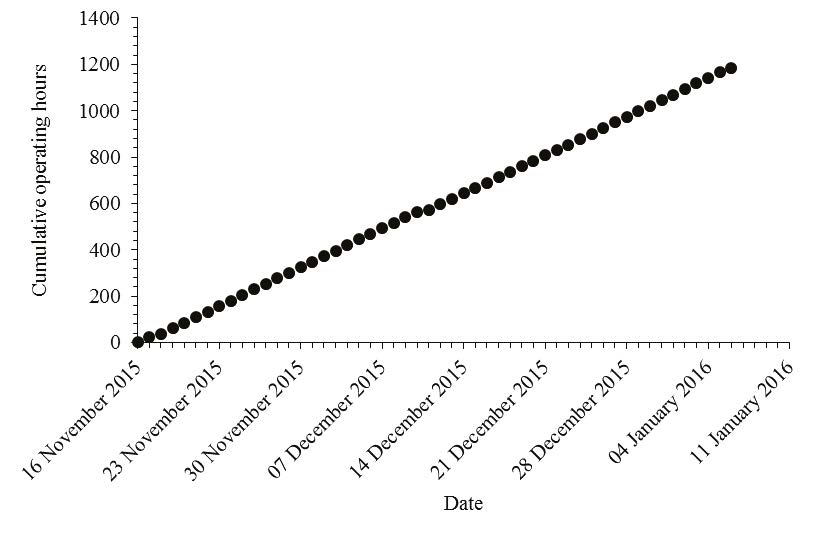
Figure 8. Cumulative operating hours during the campaign. The solvent operation on-stream factor was 100%.
3.6 Corrosion
The TCM stripper and process pipework is constructed from stainless steel and 22 % chromium Duplex steel. Figure 9 below shows the concentration of molybdenum, chromium and nickel in the CDRMax solvent during the campaign. All of these elements are constituents of stainless steel so their change in concentration is related to corrosion. The concentration of molybdenum, nickel and chromium all remained below 0.5 mg/L throughout the campaign. The chromium concentration remained at or below 0.1 mg/L at the end of the 1,200 hour campaign which was the limit of quantification. The result from the NCCC campaign was that the concentration of chromium was
2.1 mg/L after 500 hours of operation. The higher value observed at the NCCC over a shorter campaign might be explained by the fact that the absorber at the NCCC is fabricated from stainless steel while at the TCM the absorber is a polypropylene lined concrete structure. Therefore, the surface area of stainless steel is relatively smaller at the TCM.
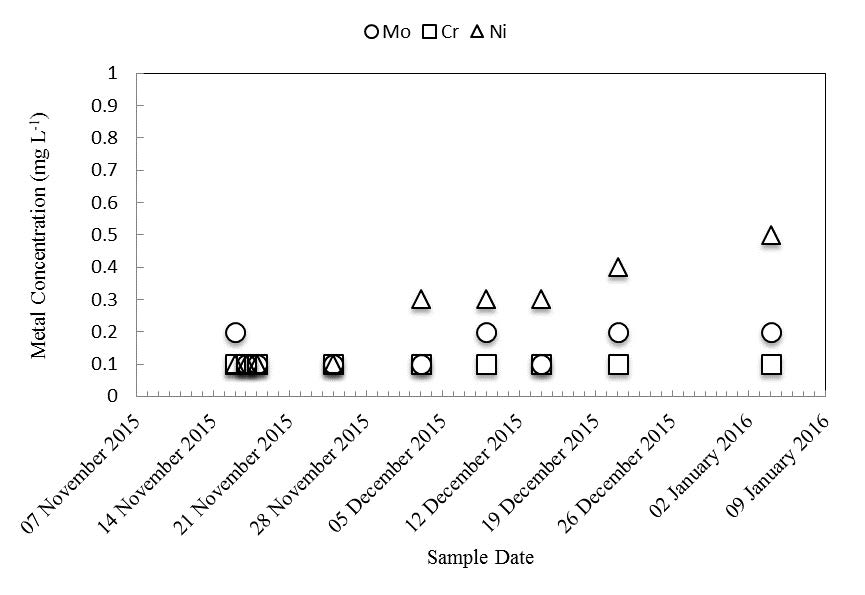
Figure 9 Concentration of molybdenum, chromium and nickel in the CDRMax solvent during the TCM campaign.
3.7 Health, Safety and Environment
Before the campaign could be authorized it was necessary to be confident that the plant could operate within its environmental permit using the CDRMax solvent. CCS Ltd estimated what the emissions from the plant would be while operating on the CDRMax solvent. The effect of atmospheric conditions on solvent emissions was considered to estimate the degradation products which might form in the atmosphere. The dispersion and hence ground level concentrations of emissions and products of degradation were then estimated using simulation software which considered local climatic conditions. The analysis concluded that it would be possible to operate the CDRMax solvent and achieve the environmental emissions permit. Throughout the campaign there were no exceedances of the environmental permit so this conclusion was valid. A REACH format Safety Data Sheet for the CDRMax solvent was provided to inform the site of precautions to be taken when handling the solvent. There were no accidents or near misses during the test campaign.
4. Conclusions
- At the NCCC and operating on flue gas containing 4.5 mole% CO2, the lowest recorded SRD for CDRMax was 3.10 MJ/kg CO2. For 30wt% MEA the equivalent value was 3.5 MJ/kg CO2. This is an 11% reduction in the SRD. During the CDRMax trial the CO2 capture rate was 92.5% while for 30 wt% MEA it was 86%. From simulation work, CCS Ltd projects that the SRD could be reduced to 2.8 MJ/kgCO2 for the CDRMax solvent if the process designed for CDRMax solvent.
- At the TCM and operating on a CHP flue gas containing 3.7 mole% CO2 test facility the CDRMax solvent was operated on equivalent conditions to 30wt% MEA. For 30wt% MEA the lowest SRD was 3.7 MJ/kg CO2, for CDRMax the SRD was 3.3 MJ/kg CO2. This is a 10% reduction in the SRD. An SRD of 3.1 MJ/kg CO2 was achieved for CDRMax at different operating conditions. The SRD can be further reduced by optimizing the cross-over exchanger and using the CDRMax solvent designed process configuration.
- For the TCM campaign, ammonia emissions in the depleted flue gas remained significantly below the emission limit for the duration of the 1,200 hours of operation. Testing during the NCCC campaign showed ammonia emissions of 3.2 ppmv. This indicates very low levels of oxidative degradation.
- For the TCM campaign, solvent emissions in the depleted flue gas remained below 1 ppmv which is significantly below the emission limit.
- The concentration of chromium in the CDRMax solvent at the NCCC was 2.1 mg/L after 500 hours of operation. The NCCC had measured a chromium concentration of 45 mg/L for 30wt% MEA after 300 hours of operation. This is 20 times higher than observed for CDRMax. At the TCM the concentration of chromium in the CDRMax solvent after 1,200 hours of operation was 0.1 mg/L.
- During the TCM campaign, the CDRMax solvent was operated for 1,200 hours and a solvent on-stream factor of 100% was achieved.
- No breaches of the environmental permit occurred at the TCM test facility during testing of the CDRMax solvent.
- No accidents or lost time incidents occurred at either test facility during testing of the CDRMax solvent.
5. Acknowledgements
Carbon Clean Solutions Ltd wishes to acknowledge the contribution of the following organizations to the test work in this paper. These are: the US Department of Energy and the National Carbon Capture Centre, the CO2 Technology Centre Mongstad, Norway and the United Kingdom’s Department of Industry, Energy and Industrial Strategy.
6. References
- Morton, F. The National Carbon Capture Center: Cost-effective test bed for carbon capture R&D, GHGT 11, Energy Procedia, 2013
- Wheeldon, J. 2013, NCCC Post Combustion CO2 Capture Program, Presentation made at NETL CO2 Capture Technology Meeting, July 8-11, 2013.
- Morken, A.K, Emission results of amine plant operations for MEA testing at the CO2 Technology Centre Mongstad, GHGT 12, Energy Procedia, 2014.
- Brigman N, Results of amine plant operations from 30wt% and 40wt% aqueous MEA testing at the CO2 Technology Centre Mongstad, GHGT 12, Energy Procedia, 2014.
Results from testing of Aker Solutions advanced amine solvents at CO2 Technology Centre Mongstad (2014)
Oddvar Gorset*, Jacob Nygaard Knudsen, Otto Morten Bade, Inga Askestad
Aker Solutions, PO Box 222, NO-1326 Lysaker, Norway *Corresponding author
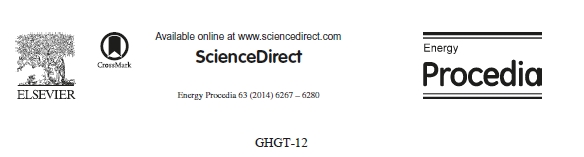
(http://creativecommons.org/licenses/by-nc-nd/3.0/).
Peer-review under responsibility of the Organizing Committee of GHGT-12
doi: 10.1016/j.egypro.2014.11.658
Abstract
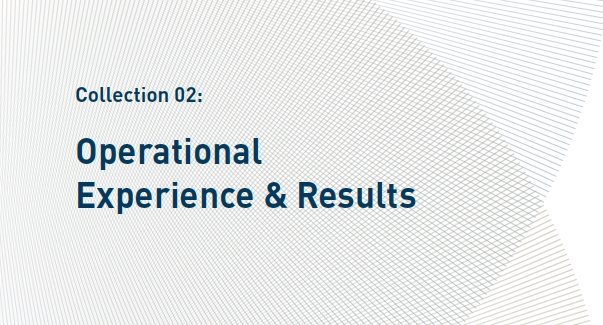
The overall objective of the test program at CO2 Technology Centre Mongstad (TCM DA) is to verify Aker Solutions’ Advanced Carbon CaptureTM process including two proprietary advanced amine solvents, ACCTM-solvents S21 and S26. Also a short benchmark campaign is conducted with 30% MEA solvent in order to establish a reference. Key performance results are presented for MEA, S21 and S26.
Close to 10 000 hours of operation of the TCM DA amine plant was obtained in the three campaigns, with high availability, showing that there are no operational issues related to the S21 and S26 solvents.
Optimum SRD for 30 wt% MEA was found to be 3.8 MJ/kg CO2 when capturing CO2 from CHP gas with CO2 concentration 3.4-4.0% and CO2 capture rate of 87%. SRD was found to be approximately 10% lower for ACCTM advanced solvents S21 and S26. SRD values down to 3.4 MJ/kg CO2 was obtained for CHP flue gas with CO2 concentrations below 4 vol% and 87% capture without heat integration or use of ACCTM Energy Saver.
Emissions to atmosphere using ACCTM emission control system were shown to be very low for solvent amines and alkyl amines, with measured levels below 0.1 mg/Nm3 in total. Emission of nitrosamines and nitramines were all below analytical detection limits typically around 0.1 μg/Nm3.
Solvent amine losses have been quantified to approximately 2.6 kg amine/ton CO2 captured for MEA, 0.5-0.6 kg amine/ton CO2 captured for ACCTM advanced solvent S21, and 0.2-0.3 kg amine/ton CO2 captured for ACCTM advanced solvent S26.
Successful reclaiming of ACCTM advanced solvents S21 and S26 was performed towards the end of the campaigns. Reclaiming was performed for validation purposes and not due to any indications of critical loss of solvent performance, high emissions, high viscosity or other operational problems that could be an indication of excessive degradation. No operational problems such as precipitation or fouling were encountered during reclaiming. HSS and most impurities and degradation products were removed from the solvent by more than 80%.
The test campaigns at CO2 Technology Centre Mongstad have shown that ACCTM advanced solvents S21 and S26 show good energy performance and are superior to 30 wt% MEA with respect to solvent degradation, ammonia emission and nitrosamine formation.
Based on the successful execution and evaluation of the campaigns, it can be concluded that Aker Solutions’ Advanced Carbon CaptureTM technology is proven and ready for full scale implementation.
1. Introduction
CO2 Technology Centre Mongstad (TCM DA) is one of the world’s largest test facilities for CO2 post combustion capture technology. Aker Clean Carbon, now part of Aker Solutions, has in a joint venture with Kvaerner constructed the amine plant at TCM DA.
A simplified process flow diagram is given in Figure 1, indicating the standard process for the CHP flue gas amine plant used in the campaigns, consisting of flue gas blower, direct contact cooler (DCC), absorber with 3 packing sections and 2 water wash sections and vent stack, rich and lean solvent circulation pumps, lean-rich heat exchanger, desorber with 1 packing section and 1 water wash section, steam reboiler, CO2 overhead condenser, and reclaimer. Further descriptions of the TCM DA amine plant are given elsewhere [1].
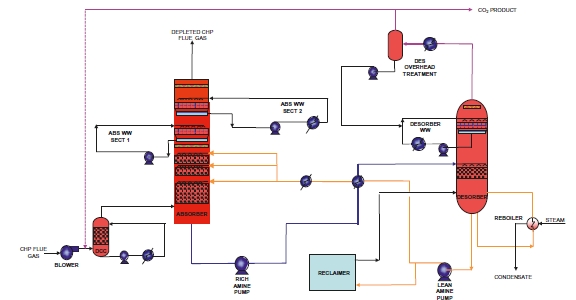
Figure 1. Process flow diagram of the amine plant at CO2 Technology Centre Mongstad for treatment of CHP flue gas.
Following start-up of the amine plant in 2012 and for the first 15 months of operation, Aker Solutions has been responsible for the test program. The overall objective of the test program at TCM DA is to verify Aker Solutions’ Advanced Carbon CaptureTM process including two proprietary solvents S21 and S26. Also a benchmark campaign is conducted with 30% MEA solvent in order to establish a reference.
Aker Solutions’ ACCTM-solvents S21 and S26 are solvents developed in Aker Solution’s solvent research program SOLVit. From a list of possible solvents, S21 and S26 were chosen due to their excellent characteristics with respect to environmental issues. They show very low levels of produced nitrosamines and have very low emissions to atmosphere. They were also chosen due to low degradation rates, where S26 were the one of the two tested solvents with lowest degradation potential.
Key performance results are presented for MEA, S21 and S26 solvents.
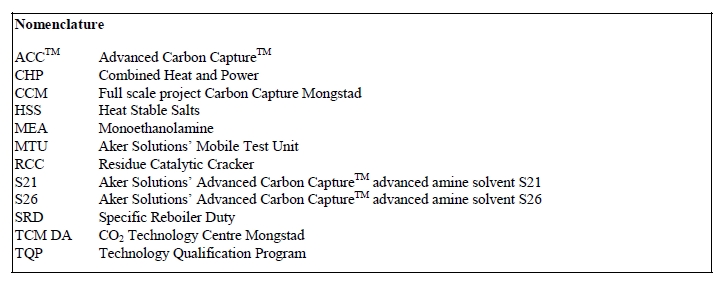
2. Overview of test campaigns
Aker Solutions has performed 3 test campaigns at TCM DA, with 3 different solvents. In order to generate reference data, reference solvent 30 wt% MEA has been used. Aker Solutions’ ACCTM advanced amine solvents S21 and S26 were tested in separate campaigns.
All of the test campaigns are executed using a slip stream of flue gas from the combined heat and power (CHP) plant at Mongstad, which has relatively low (~3.5-4.0 vol%) CO2 content. Results from experimental runs with recirculation of CO2 to increase inlet flue gas CO2 concentration are not covered in this paper. Neither are results related to operation on cracker gas from the refinery (RCC).
Key operating data such as campaign time period, total number of operating hours, CO2 captured, treated gas volume and availability for the campaigns are listed in Table 1.
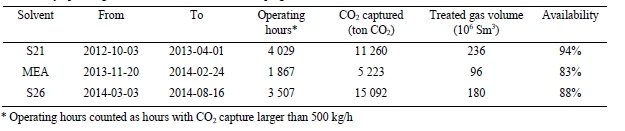
Table 1 Key operating data for S21, MEA and S26 campaigns.
Aker Solutions’ ACCTM advanced amine S21 campaign was part of the Technology Qualification Program (TQP) for the full scale project Carbon Capture Mongstad (CCM). Figure 2 shows accumulated operation hours and CO2 capture for the campaign.
Accumulated operation hours and CO2 capture for the MEA reference campaign are shown in Figure 3.
Experiments with 40wt% MEA, conducted at the end of the MEA campaign, is not covered in this paper.
Figure 4 shows accumulated operation hours and CO2 capture for Aker Solutions’ ACCTM advanced amine S26 campaign. Please note the increased CO2 capture accumulation rate, due to increased flue gas inlet CO2 concentration by CO2 recirculation in the TCM DA amine plant. Experiments with increased CO2 concentrations are
not covered in this paper.
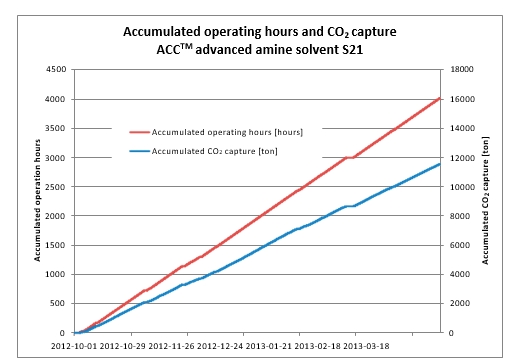
Figure 2. Accumulated operating hours and CO2 capture for the ACCTM advanced amine solvent S21 campaign.
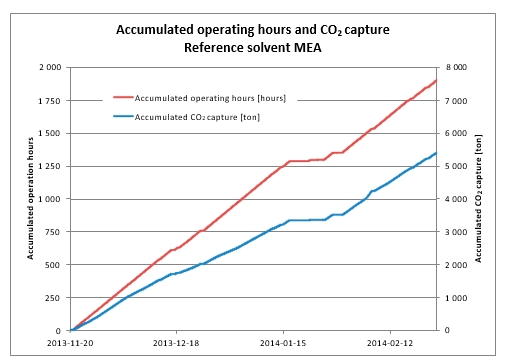
Figure 3. Accumulated operating hours and CO2 capture for the reference MEA campaign.
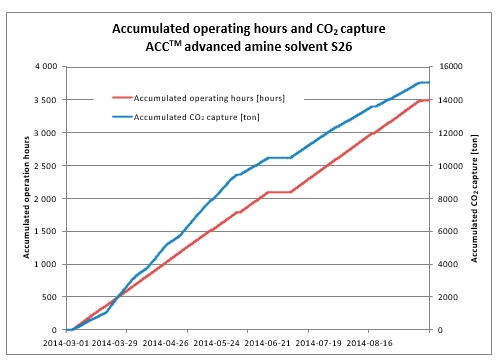
Figure 4. Accumulated operating hours and CO2 capture for the ACCTM advanced amine solvent S26 campaign.
Operation of the plant has been executed without serious problems such as severe problems with equipment, precipitation of solvent, significant corrosion, extremely fast degradation, emissions of large and long lasting emissions, reported operator accidents, large solvent leakages, etc. Relatively small increases in metal ion concentrations were measured in the campaigns, indicating no significant corrosion. For solvent S26 the iron content was never larger than 2 wtppm, while the level reached 17 wtppm after the 30 wt% MEA campaign. Indications of foaming in the desorber were observed in some cases, in particular during operation with 30% MEA. However the foaming never affected the overall operability of the plant and could easily be eliminated with small doses of antifoam. Altogether this is reflected in the high operating availability, ref. Table 1.
It can hence be concluded that Aker Solutions’ ACCTM advanced amine solvents S21 and S26 is well suited for operation in an amine based CO2 capture plant.
3. Mass balances
Total mass balance recovery over the plant boundary typically shows an excellent match, as shown in Figure 5, leftmost figure, where total mass recovery is within +/- 0.5%. The example is given for results from the ACCTM advanced amine solvent S26 campaign. For the same set of results total CO2 mass balance recovery is shown in Figure 5, rightmost figure, indicating typical magnitude of precision of +/- 5% within distinct time periods, but these time periods seem to be periodically biased up to +/- 10%.
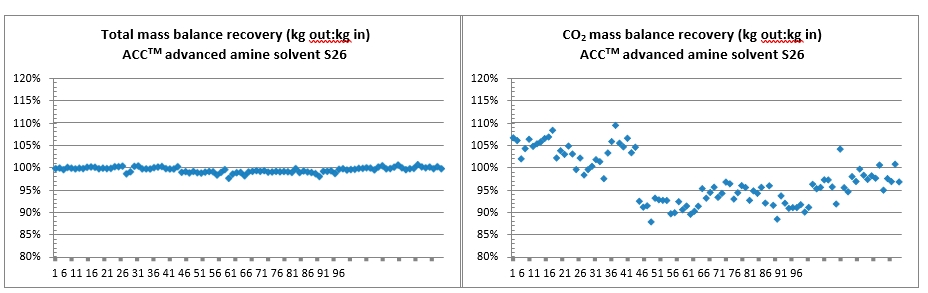
Figure 5. Mass balances for ACCTM advanced amine solvent S26 campaign. Each marker represents one run, i.e. a (normally) two hours stable operation period. Leftmost figure: Total mass balance recovery (kg out:kg in). Rightmost figure: Total CO2 mass balance recovery (kg out:kg in).
Plant CO2 capture has been derived by three methods:
- abs: Difference in CO2 mass flow in flue gas in to and out of absorber, calculated by total gas flow and gas CO2 concentrations in and out of absorber measured by FTIR, and H2O concentrations in and out of absorber estimated from steam tables.
- str: CO2 content in CO2 product stream from stripper overhead, calculated from gas flow measured by vortex flow meter and H2O content estimated by steam tables and measured saturated gas temperature.
- solv: Difference in CO2 transfer in rich and lean solvent flows, calculated by rich and lean flows measured by
Coriolis flow meters and CO2 concentration lab analysis.
Average used for calculating other parameters, for instance SRD, is based on the average of abs and str only. A comparison of the CO2 capture derived by the three methods is shown for the MEA campaign in Figure 6. CO2 mass balances obtained from the absorber and stripper side typically deviates by +/- 5%, however with distinct periods in which the quality of the mass balances varies. The solvent side, solv, deviates more from the two other methods, with a typical magnitude of precision of +/- 5% within distinct time periods, but a bias/accuracy varying +/- 10% compared to the average between abs and str. Similar results are seen for all solvent campaigns.
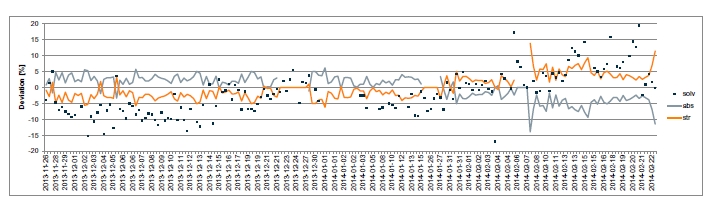
Figure 6. Deviation (%) between the three methods used for calculation of CO2 capture. The methods are compared to the average of absorber
(abs) and stripper (str) side. Results shown for the MEA reference campaign.
4. Energy performance
Effects on SRD from variation of main operating conditions were assessed, and it was confirmed that too high CO2 capture degree (>90%) (equivalent to too low outlet flue gas CO2 concentration), as well as high inlet flue gas temperature (47oC), gave penalties in SRD number. Absorber packing height was shown to have impact on SRD, the higher packing height the better SRD. Flue gas flow rate (Sm3/h) was shown to be without significant effect on SRD.
Optimum SRD for 30 wt% MEA was found to be 3.8 MJ/kg CO2 when capturing CO2 from CHP gas with CO2 concentration 3.4-4.0%, inlet temperature 25oC, approximately 87% CO2 capture, 24 m absorber packing, stripper pressure 1.9 bara, as shown in Figure 7. The figure also shows the insignificant effect of varying inlet flue gas flow.
Please note the difference in reported minimum SRD values for 30 wt% MEA from the TCM DA amine plant reference solvent campaign [1]. The difference in reported values is due to the way CO2 capture is calculated; while the authors of this paper use the average for CO2 mass balances obtained from stripper side (str) and absorber side (abs) (ref. Mass and energy balances section above), [1] makes use of the stripper side (str) only.
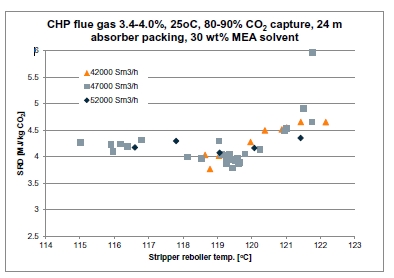
Figure 7. SRD versus stripper reboiler temperature for runs with 30 wt% MEA, CHP flue gas with CO2 concentration 3.4-4.0%, inlet temperature 25oC, 87% CO2 capture, 24 m absorber packing, 1.9 bara stripper pressure.
SRD was found to be lower for ACCTM advanced solvents S21 and S26. SRD values down to 3.4 MJ/kg CO2 was obtained for CHP flue gas with CO2 concentrations below 4 vol% without heat integration or use of Energy Saver.
Figure 8 shows a stripper reboiler U curve for operation on CHP flue gas with 4.0% CO2, 50 000 Sm3/h, 30oC inlet temperature, 87% CO2 capture, 18 m absorber packing and 1.9 bara stripper pressure using ACCTM advanced solvent S26.
Figure 9 shows SRD during 2½ weeks of stable operation on CHP flue gas with 3.4% CO2, 58 000 Sm3/h, 30oC inlet temperature, 87% CO2 capture, 18 m absorber packing and 1.9 bara stripper pressure using ACCTM advanced solvent S21.
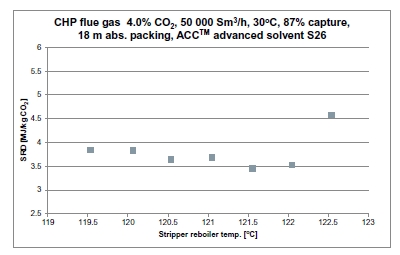
Figure 8. SRD versus stripper reboiler temperature for runs with ACCTM advanced amine solvent S26, CHP flue gas with CO2 concentration 4.0%, flow 50 000 Sm3/h, inlet temperature 30oC, 87% CO2 capture, 18 m absorber packing, 1.9 bara stripper pressure.
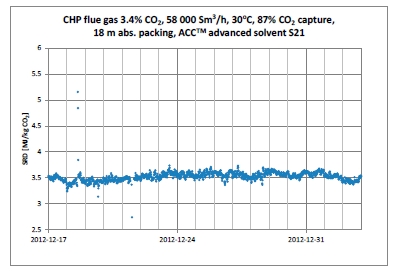
Figure 9. SRD versus stripper reboiler temperature for stable test period with ACCTM advanced amine solvent S21, CHP flue gas with CO2 concentration 3.4%, flow 58 000 Sm3/h, inlet temperature 30oC, 87% CO2 capture, 18 m absorber packing, 1.9 bara stripper pressure.
Even though ACCTM advanced solvents S21 and S26 were not primarily chosen due to their energy performance characteristics, they anyhow show a significant reduction in SRD compared to standard MEA solvent. Compared to the 30 wt% MEA reference case at TCM DA, SRD levels are 10% lower for the ACCTM advanced solvents S21 and S26.
Please note that this is for CHP gas with low CO2 concentration (down to 3.4 vol%) without use of heat integration or Energy Saver. SRD levels for S21 and S26 are shown to be significantly lower when operating on flue gas from higher CO2 concentration sources, as for instance coal fired boilers. Experiments performed at TCM DA amine plant with ACCTM advanced solvent S26 for flue gas with increased CO2 concentration (9 vol%) using the Energy Saver (but still without heat integration) showed SRD values down to 2.8 MJ/kg CO2.
5. Emissions
Extensive emission measurements have been performed during all test campaigns at TCM DA. The TCM DA amine plant includes two circulating water washes at top of the absorber before discharge of CO2 depleted flue gas to atmosphere. The TCM DA amine plant is not equipped with the ACCTM emission control system.
The emission of ammonia was significant during the MEA campaign, indicating relatively high degradation rate even from the start of the campaign. A comparison of the NH3 emission levels as measured by FTIR for the three solvents using standard TCM DA amine plant emission control design is shown in Figure 10. While NH3 emissions during the MEA campaign reached 20-40 volppm already after 1 300-1 400 hours of operation, emission levels reached 10 volppm after 3 000-3 500 hours for solvent S21. NH3 emission level was as low as 2 volppm even after 3 500 hours for the S26 campaign. The very low levels of NH3 emission seen during the S26 campaign compares well with the low degradation rate and low levels of metals in solution. It may be noted that the test programs were not conducted with emphasis on operation that could reduce the stress on the solvents.
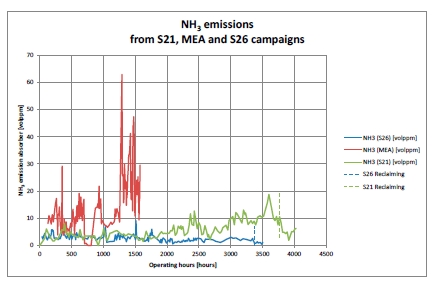
Figure 10. Ammonia emission levels from absorber as measured by FTIR using the TCM DA amine plant emission control.
Solvent amine emissions were low during all campaigns. The FTIR reading of amine emission is not reliable for emissions below approx. 1 ppm. Instead, manual sampling campaigns were conducted. The results from the MEA campaign is presented in [4]. The summary of emission measurements performed on the S21 and S26 campaign is presented in Table 2. The emission measurements are performed under stable operation of the plant.
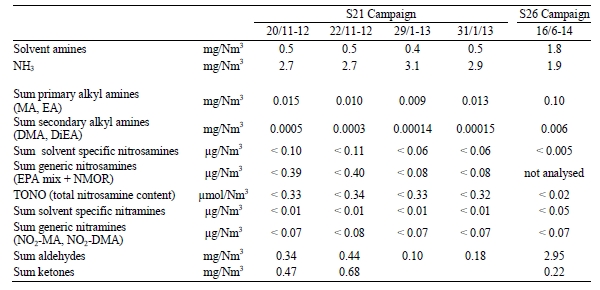
Table 2 Emission results from the TCM DA amine plant during the S21 and S26 campaigns.
In order to verify the performance of Aker Solutions’ ACCTM emission control design, which includes the Aker Solutions’ anti mist system and acid wash polishing step, emission measurements were done making use of Aker Solutions’ Mobile Test Unit (MTU) in the S21 campaign. The MTU is equipped with the ACCTM emission control system. A more detailed description of the MTU can be found in [2]. The MTU was located at TCM DA, and operating on the same flue gas source as the TCM DA amine plant. Degraded solvent from the TCM DA amine plant was transferred to the MTU, and four emission sampling campaigns with altogether nine emission measurements were performed. The results showed excellent emission performance with very low amine emissions levels, and all nitrosamine and nitramine emissions were below detection limits. Table 3 presents emission results using Aker Solutions’ ACCTM emission control design during the ACCTM advanced solvent S21 campaign.
Similar excellent results were obtained for S26 solvent in the MTU at TCM DA.
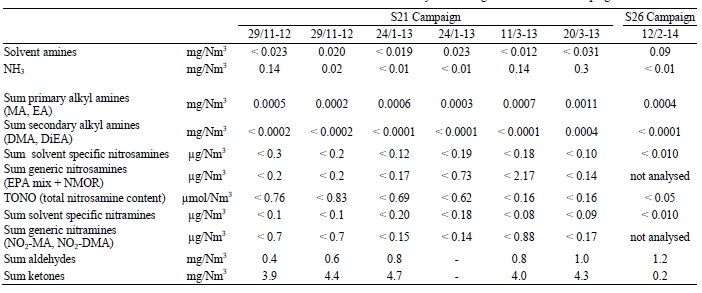
Table 3 Emission results from the MTU with ACCTM Emission Control System during the S21 and S26 campaigns.
The ACCTM advanced solvent S21 campaign was part of the full scale Carbon Capture Mongstad (CCM) technology qualification program (TQP), where Aker Solutions was one of four technology suppliers. Emission levels for the various technology suppliers were presented as ranges, and Aker Solutions’ values make out the lower limits of these ranges for all emission component groups, ref. Figure 11.
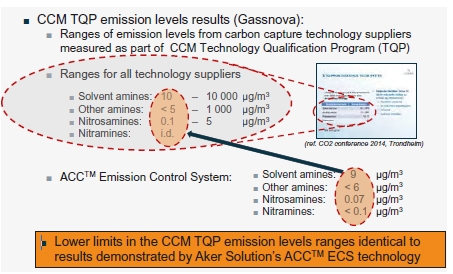
Figure 11. Emission levels from the CCM Technology Qualification Program using ACCTM advanced solvent S21 sampled and analysed by third parties KEMA (Netherlands) and Rambøll (Finland), showing the relative performance of ACCTM Emission Control System compared to other technology suppliers. Gassnova slide excerpt from [3].
A long term test to verify ACCTM emission control system’s acid wash technology demonstrated that acid wash technology works well with high capture efficiency for alkaline components. The emission of alkyl amines and ammonia was very low. No nitrosamines/nitramines are formed in the acid wash.
Possible emission of unknown compounds was qualitatively investigated through LC-MS and GC-MS scans from emission samples collected from the verification plants. In addition, the flue gas from the TCM DA amine plant was quantitatively screened for unknown compounds by use of PTR-TOF-MS technique. In general, the results indicate that no major emissions of compounds not currently included in Aker Solution’s analytical program were observed. The detected compounds were all amine-like components. No nitrosamines or nitramines were detected with the used analysis methods.
6. Solvent stability, degradation
For the ACCTM advanced solvent S21 campaign, the concentrations of solvent amines and degradation products in the solvent loop were followed throughout the campaign, and the concentrations of solvent amines were seen to remain stable over relatively long time periods indicating reasonable low degradation rates of the solvent amines. The main degradation products of S21 were found to be amides, amino acids and other amines of low volatility. Also minor amounts of more volatile degradation products were observed such as ammonia, simple alkyl amines, aldehydes and ketones, however their concentrations in the solvent remained relatively low due to continuously venting of these compounds. The concentration of degradation products of low volatility in the S21 solvent was 1.8 wt%.
No generic nitrosamines were found in the S21 solvent or absorber wash water. Three solvent specific nitrosamines were detected in the solvent as degradation progressed, however the total concentration of nitrosamines remained at low level (<22 wtppm). Only one solvent specific nitrosamine was detected in tiny amounts (0.02 wtppm) in the absorber wash water, indicating that the volatility of the solvent specific nitrosamines is low and emissions to be insignificant. This is consistent with the reported emission activities above.
Only very low concentrations (<0.3 wtppm) of solvent specific nitramines were observed in the S21 solvent, and no generic nitramines.
The amount of heat stable salts (HSS) in S21 increased to 0.10 mol/kg after 3 600 hours of operation, before reclaiming.
For the 30 wt% MEA campaign, HSS increased more rapidly and linearily with time to a level of 0.12 mol/kg (0.7 wt% as MEA) already after 1 600 hours of operation. The sum of degradation products (HEI, HEF, OZD, HEPO, HeGly, BHEOX, HEA and NDELA) and organic and inorganic acids were found to be 2.9 wt% at the end of the 30 wt% MEA campaign.
The concentration of HSS in ACCTM advanced solvent S26 stays very low (below or slightly above the detection limit at 0.01 mol/kg), even after 3 300 hours of operation, indicating very low degradation rate.
Figure 12 shows the HSS buildup for the 3 different campaigns. The effect of the solvent reclaiming towards the end of campaigns S21 and S26 is obvious. More detailed results from the reclaiming is described in section 7.
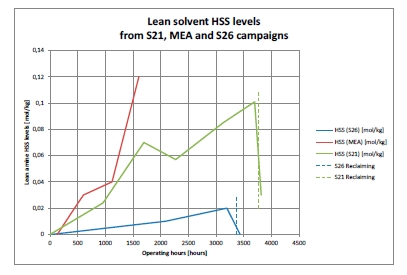
Figure 12. Lean solvent HSS levels from S21, MEA and S26 campaign.
Figure 13 shows total nitrosamine buildup in the solvent for the respective campaigns. It can be seen that S21 and S26 solvents are less prone to form nitrosamines compared to MEA. None of the solvent amines are forming nitrosamines directly. However, degradation components may do, and in the MEA campaign it was shown that nitroso-HeGly was the dominating nitrosamine, resulting from nitrosation of MEA degradation product HeGly.
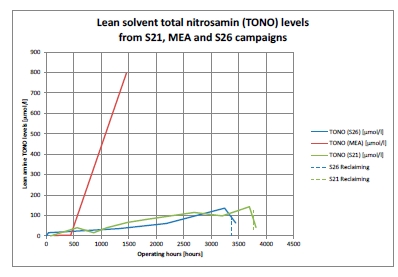
Figure 13. Total nitrosamines level buildup in lean solvent during the S21, MEA and S26 campaigns.
Amine inventory calculations at the TCM DA amine plant indicate an ACCTM advanced solvent S21 amine loss corresponding to 0.5-0.6 kg amine/ton CO2 captured. The calculations include the effect of reclaiming performed at the end of the test campaign. The total loss of MEA in the campaign corresponds to 2.6 kg MEA/ton CO2 (note that this includes 290 hours of operation with 40 wt% MEA but excludes possible loss due to reclaiming if executed), and for ACCTM advanced amine S26 approximately 0.2-0.3 kg amine/ton CO2 (including reclaiming). Comparison of total solvent amine loss for the three solvents are summarised in Table 4. It appears that the consumption of MEA is almost 5 and 10 times higher than that of S21 and S26, respectively, demonstrating the superior degradation resistance of Aker Solutions’ ACCTM advanced solvents.
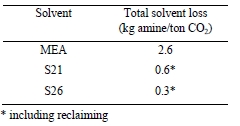
7. Reclaiming
Reclaiming was performed in the ACCTM advanced amine S21 and S26 campaigns.
Please note that reclaiming was not initiated by any indications of critical loss of solvent performance, high emissions, high viscosity or other operational problems that could be an indication of excessive degradation, but rather performed to verify reclaimability of the solvent.
S21 solvent reclamation was performed in the TCM DA amine plant after 24 weeks of operation, equivalent to more than 3 500 hours of operation with CO2 capture.
No problems with precipitation or fouling were encountered. The total steam demand of the capture plant (stripper reboiler plus reclaimer heater duties) was found to be the same during reclaiming as during normal operation as the vapours from reclaiming are transferred to the desorber.
No significant increase in emissions was observed during the reclaiming campaign, indicating that degradation rate was not increased even though parts of the solvent were experiencing higher temperatures in the reclaimer. No increased amine emissions were detected either.
As a result of reclaiming, the colour of the solvent changed drastically (ref. Figure 14) and the amine concentration increased with 2-3 wt%. The amine concentration increases as amine bound in heat stable salts (HSS) and other degradation products are released. This shows that the reclaiming of amine is in the same order of magnitude as the amount of amine lost in reclaimer waste, or even a bit larger. About 80% of most impurities and degradation products were removed, as expected from the total solvent volume fed to the reclaimer during the reclaiming campaign. HSS content decreased from 0.10 mol/kg to 0.03 mol/kg. Similar reduction can be seen of nitrosamines and nitramines in the solvent, since most of the solvent specific nitrosamines and nitramines have low volatility. Accordingly, there will not be any significant build-up of nitramines and nitrosamines in S21 when reclaiming is performed on a regular basis. The viscosity of the solvent was decreased.
Ammonia emissions were decreased after reclaiming, indicating reduced oxidative degradation.
The resulting amount of reclaimer waste generated is equivalent to 0.26 kg reclaimer waste/ton CO2 captured. The reclaimer waste consisted mostly of various non-volatile degradation products (15%), metals (2.5%) and remaining solvent amine (6 wt%), with nitrosamines only in the order of a few wtppm. Maximum viscosity of XQGLOXWHG ZDVWH LV 114 F3 DW 70Û&. The waste proved to be possible to manage and it was possible to remove it from the ACCTM reclaimer system.
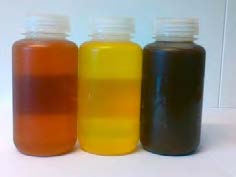
Figure 14. Aker Solutions’ ACCTM advanced amine S21 solvent samples before and after reclaiming at TCM DA amine plant, and reclaimer waste.
S26 solvent reclamation in the TCM DA amine plant was performed after 22 weeks of operation, equivalent to 3300 hours of operation with CO2 capture.
Again, no operational problems such as precipitation or fouling were encountered during reclaiming.
HSS, impurities and degradation products were removed from the solvent by about 90 % during reclaiming, as expected from the total solvent volume fed to the reclaimer during the reclaiming campaign. The HSS level before reclaiming was rather low, approximately 0.02 mol/kg, and decreased to below detection limit (<0.01 mol/kg) after reclaiming.
The colour of the solvent changed during reclaiming as showed in Figure 15.
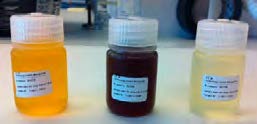
Figure 15. Aker Solutions’ ACCTM advanced amine S26 solvent samples before and after reclaiming at TCM DA amine plant, and reclaimer waste (in the middle).
The successful operation of the TCM DA reclaimer serves to prove the feasibility of Aker Solutions’ ACCTM reclaimer design and operation procedure.
8. Conclusion
Aker Solutions has performed 3 test campaigns at TCM DA, with 3 different solvents. In order to generate reference data, reference solvent 30 wt% MEA has been used. Aker Solutions’ ACCTM advanced amine solvents S21 and S26 were tested in separate campaigns. S21 and S26 were shown to have excellent characteristics with respect to environmental issues; very low levels of produced nitrosamines, very low emissions to atmosphere and very low degradation rates.
Close to 10 000 hours of operation of the TCM DA amine plant was obtained in the three campaigns, with high availability. This indicates the robustness of the ACCTM process and ACCTM advances amine solvents S21 and S26.
Optimum SRD for 30 wt% MEA was found to be 3.8 MJ/kg CO2 when capturing CO2 from CHP gas with CO2 concentration 3.4-4.0%. SRD was found to be approximately 10% lower for ACCTM advanced solvents S21 and S26. SRD values down to 3.4 MJ/kg CO2 was obtained for CHP flue gas with CO2 concentrations below 4 vol% without heat integration or use of Energy Saver.
Emissions to atmosphere using ACCTM emission control system were shown to be in the lower range for amine components. Emission level of solvent amines was in the range 10-90 μg/Nm3, and emission levels of individual nitrosamines and nitramines were below detection limits typically around 0.1 μg/Nm3.
Total solvent amine losses was quantified to approximately 2.6 kg amine/ton CO2 captured for MEA, 0.5-0.6 kg amine/ton CO2 captured for ACCTM advanced solvent S21, and 0.2-0.3 kg amine/ton CO2 captured for ACCTM advanced solvent S26.
Reclaiming of ACCTM advanced solvents S21 and S26 was performed towards the end of the campaigns, even though there were no indications of critical loss of solvent performance, high emissions, high viscosity or other operational problems that could be an indication of excessive degradation. No operational problems such as precipitation or fouling were encountered. HSS and most impurities and degradation products were removed from the solvent by more than 80%.
The test campaigns at CO2 Technology Centre Mongstad (TCM DA) have shown that ACCTM advanced solvents S21 and S26 show good energy performance and are superior to 30 wt% MEA with respect to solvent degradation, ammonia emission and nitrosamine formation.
Based on the successful execution and evaluation of the campaigns, it can be concluded that Aker Solutions’ Advanced Carbon CaptureTM technology is proven and ready for full scale implementation.
Acknowledgements
MEA and S21 campaigns have been performed as part of the SOLVit project. The SOLVit project is sponsored through the strategic Norwegian research program CLIMIT. The authors would like to express their gratitude to the partners and sponsors of the program, Gassnova, SINTEF and EnBW. Also the authors acknowledge the staff at TCM DA, Norway, for their cooperation and support with the test campaigns.
References
- Brigman N, Shah M I, Falk-Pedersen O, Cents T, Smith V, De Cazenove T, Morken A K, Hvidsten O A, Chhaganlal M, Feste J K, Lombardo G, Bade O M, Knudsen J, Subramoney S C, Fostås B F, De Koeijer G, Hamborg E S. Results of amine plant operations from 30 wt% and 40 wt% aqueous MEA testing at the CO2 Technology Centre Mongstad. Energy Procedia; 2014.
- Bade O M, knudsen, J N, Gorset O, Askestad I. Controlling amine mist formation in CO2 capture from Residual Catalytic Cracker (RCC) flue gas. Energy Procedia; 2014.
- Kaasa, S. Fullskala CO2-fangst på Mongstad – Kansellert, men ikke forgjeves. CO2-konferansen 2014, Kursdagene Tekna, Trondheim, 2014
- Morken A K, Nenseter B, Pedersen S, Chhaganlal M, Feste J K, Tyborgnes R B, Ullestad Ø, Ulvatn H, Zhu L, Mikoviny T, Wisthaler A, Cents T, Bade O M, Knudsen J, De Koeijer G, Falk-Pedersen O, Hamborg E S. Emission results of amine plant operations from MEA testing at the CO2 Technology Centre Mongstad. Energy Procedia; 2014.
Results of amine plant operations from 30 wt% and 40 wt% aqueous MEA testing at the CO2 Technology Centre Mongstad (2014)
Natasha Brigmana,b, Muhammad I. Shahc, Olav Falk-Pedersena,c, Toine Centsa,b, Vian Smitha,b, Thomas De Cazenovea, Anne K. Morkena,d, Odd A. Hvidstena,d, Milan Chhaganlala,d, Jane K. Festea,d, Gerard Lombardoa,c, Otto M. Badee, Jacob Knudsene, Shalendra C. Subramoneyb, Berit F. Foståsd, Gelein de Koeijerd, Espen S. Hamborga,d,*
aCO2 Technology Centre Mongstad (TCM DA), 5954 Mongstad, Norway bSasol Technology, P.O. Box 5486, Johannesburg 2000, South Africa cGassnova SF, Dokkvegen 10, 3920 Porsgrunn, Norway dStatoil ASA, P.O. Box 8500, 4035 Stavanger, Norway eAker Solutions, P. O. Box 222, 1326 Lysaker, Norway
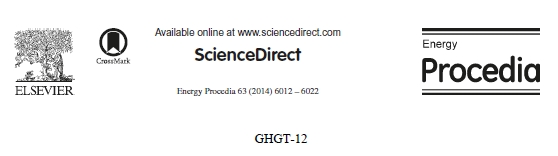
(http://creativecommons.org/licenses/by-nc-nd/3.0/).
Peer-review under responsibility of the Organizing Committee of GHGT-12
doi: 10.1016/j.egypro.2014.11.635
Abstract
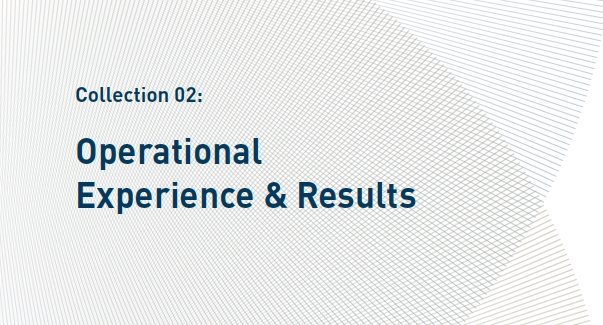
An amine plant campaign has been performed at the CO2 Technology Centre Mongstad applying the aqueous 30 wt% and 40 wt% monoethanolamine (MEA) solvent systems for treatment of flue gas from a combined heat and power (CHP) plant. CHP flue gas flow rates were ranging from about 40.000 Sm3/h to 60.000 Sm3/h and the CO2 content was about 3.5 vol%.
Minimum specific reboiler duties (SRD) of respectively 4.0 MJ/kg CO2 and 3.7 MJ/kg CO2 were obtained for the aqueous 30 wt% MEA solvent system without and with the addition of anti-foam solution. A minimum SRD of 3.4 MJ/kg CO2 was obtained for the aqueous 40 wt% MEA solvent system. Lower SRD and absorber liquid to gas (L/G) ratios were obtained with higher concentration MEA solvents.
Increased absorber packing heights resulted in lower SRD. Variation in flue gas supply flow rates and corresponding variations in solvent flow rates, i.e. constant L/G ratios, did not yield any significant variations in SRD. Decreased flue gas supply temperatures resulted in lower SRD.
For any future large scale post-combustion capture (PCC) amine plant, engineering aspects such as the flue gas supply temperature and instrumentation monitoring CO2 content in the flue gas must be evaluated to avoid the chemical equilibrium pinch behavior. Engineering and environmental aspects related to the use of anti-foam solutions for future large scale PCC amine plants must also be considered.
1. Introduction
The CO2 Technology Centre Mongstad (TCM DA) is the one of the world’s largest and most advanced facilities for testing and improving CO2 capture technology. The facility enables vendors of suitable amine formulations and other post-combustion capture processes to test their process, collecting performance data to support full-scale design. The vendors can then anticipate the associated performance and operating costs of their amine formulations and capture processes. As a result, one of the main objectives of TCM DA is to investigate and demonstrate the flexibility of post-combustion amine based solvent systems with respect to load changes, variations in flue gas composition, variations in amine plant operations and solvent system compositions in order to achieve optimal and environmentally safe operating conditions. The flue gas utility system allows for flue gas supplies with varying temperatures, flow rates, and CO2 content and also different types of flue gases with various trace components from either a combined heat and power (CHP) plant or a refinery catalytic cracker. In the CHP plant, the natural gas is combusted in a gas turbine and the flue gas content and characteristics are similar to those of a combined cycle gas turbine (CCGT) power plant. The amine plant at TCM DA is a highly flexible and well instrumented generic amine plant, designed and constructed by Aker Solutions, aimed to accommodate a variety of technologies with capabilities of treating flue gas streams of up to 60.000 Sm3 per hour. The flexibility of the amine plant allows for handling of a wide range of flue gas flow rates, temperatures, and CO2 content in the flue gas, and also a wide range of various operational parameters, i.e. solvent flow rates, absorber packing heights, stripper pressures, reboiler heat duties, lean amine and cross heat exchanger duties, absorber water wash temperatures and flow rates with or without acid injections, anti-foam solution injections, etc. [1, 2]
The campaign described in the current paper was conducted at TCM DA in the period December 2013 to
February 2014 as a part of Aker Solutions’ test period. In general, during the campaign the aqueous 30 wt% monoethanolamine (MEA) solvent system was applied treating the flue gas from the CHP plant. The primary purposes and goals of the campaign were:
- Generate results from CHP plant operations with CO2 capture
- Generate an independently verified TCM DA amine plant base case while treating CHP plant flue gas with the aqueous 30 wt% MEA solvent system [3, 4]
- Investigate the performance potential of higher MEA concentration solvents
- Verify design capacities and flexibilities of the TCM DA amine plant and specific functionalities
- Gain better understanding of scale-up, performance, and emission aspects and transient operations of the TCM DA amine plant
- Verify and improve process simulation models
- Test and improve various online analyser for emission monitoring [5]
- Scientific dissemination of some results
These purposes and goals are aimed for gaining experience and knowledge for future large scale carbon capture and storage (CCS) projects.
This work is part of a continuous effort of gaining better understanding of the performance potential of the non- proprietary aqueous MEA solvent system, conducted by TCM DA and its affiliates and owners, in order to test, verify, and demonstrate CO2 capture technologies. [3, 4, 5] The purpose of the current work is to provide results of various operational conditions of the TCM DA amine plant, and hence demonstrating some capacities, flexibilities, and performances of the plant while treating CHP flue gases.
2. Testing Philosophy
An overview of the TCM DA amine plant has been given elsewhere. [3, 4, 5]
The test philosophy during the current campaign was to adjust one operational parameter at a time, e.g. the solvent flow rate, the gas flow rate, etc., whilst subsequently allowing the amine plant to reach steady-state operations and simultaneously manually controlling the CO2 capture rate to a specific value. The CO2 capture rate was controlled to about 85% for most of the campaign by manually adjusting the reboiler steam flow rate. The response time of the amine plant was up to about 3 hours, depending on the varied operational parameter. The plant was operated for at least an additional 3 hours of steady-state operations after an operational parameter change before the plant was considered to provide representative process values. Any solvent sampling for laboratory analysis was conducted once representative process values were obtained. Certain transient operations were conducted during the campaign, and the aforementioned test philosophy was adapted in order to accommodate such operations. During Base-Case testing, as described elsewhere [3, 4], the amine plant was operated at steady-state operations for about 1 week.
Table 1 provides the main operational parameters and ranges adjusted during the campaign. Approximately 150 different operating conditions were conducted during the campaign, and the results of some of these are presented in the current work.
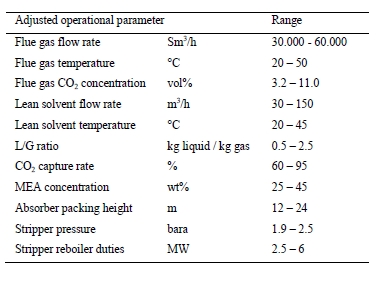
Table 1: MEA campaign overview.
The calculations procedures for the various performance indices presented in the current work are as described by Thimsen et al. [3] and Hamborg et al. [4].
3. Chemicals
MEA [CAS: 141-43-5] was supplied by AkzoNobel, and was diluted to a desired solvent concentration by addition of demineralized water. Anti-foam solution was supplied from KCC Basildon.
4. Results and Discussion
4.1 Mass recovery and MEA solvent concentrations
The total mass and CO2 mass recovery also referred to as the total mass and CO2 mass balances, for the complete campaign, were determined as described by Thimsen et al. [3] and displayed in Figure 1. The total mass recovery is, as expected, close to 100% during the complete campaign. The CO2 mass recovery is however scattered, and this may be attributed to inadequate instrumentation for monitoring of the CO2 gas phase concentrations in the flue gas supply and depleted flue gas. The gas phase concentrations of CO2 in the flue gas streams were monitored by the installed Fourier transform infrared spectroscopy (FTIR) analyzer, and accuracy and precision challenges with respect to this FTIR analyzer setup has been described by elsewhere. [4] The scattering of the CO2 mass recovery displayed in Figure 1 leads to uncertainties in the CO2 capture rates, whereas the specific thermal use, as derived in the current work, is independent of the FTIR analyzer system. [4]
The MEA solvent concentrations, based on sampling and laboratory analysis of the lean amine, are displayed in Figure 2. The MEA solvent concentration was maintained at about 30 wt% during most of the campaign, and was increased to above 40 wt% towards the end. The MEA solvent water balance was maintained by adjusting the depleted flue gas temperature to the flue gas supply temperature, and, if necessary, addition of demineralized water to the MEA solvent. Due to the rapid change of operational parameters and conditions and additional time consuming sampling and laboratory analysis, the MEA solvent concentration could not be maintained at constant values throughout the campaign.
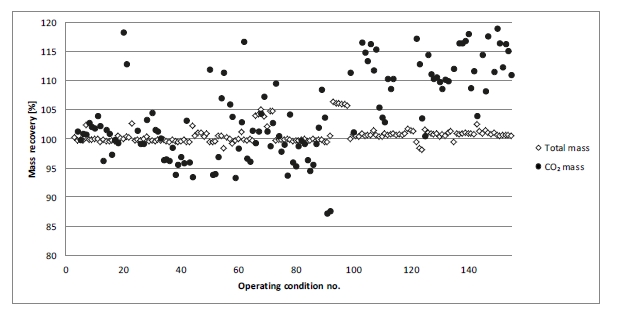
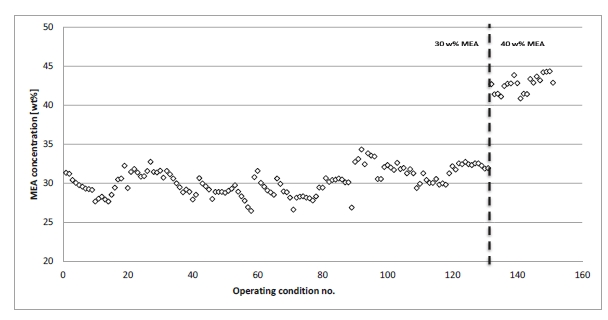
4.2 Overall energy performances
Figure 3 displays the specific reboiler duties (SRD) for the aqueous 30 wt% MEA solvent system with and without the use of anti-foam solutions. The plant was operated with 24 meters of absorber packing heights, 1.9 bara stripper pressure, and a flue gas flow rate of about 47.000 Sm3/h at 25 °C. The CO2 capture rate was kept at about 85%. The results in Figure 3 show a clear minimum in the SRD of about 4.0 MJ/kg CO2 at a lean amine loading of about 0.25 for operations without anti-foam solutions added. Results refer to Base-Case testing as presented elsewhere [4] provided a SRD of 4.1 MJ/kg CO2 and is displayed in Figure 3. For operations with addition of anti- foam solutions, the minimum SRD is shifted towards lower lean CO2 loadings, and the cause for this behavior is described later. The minimum SRD for these operations with anti-foam addition may have not been achieved. The lean amine CO2 loading can be assumed closely proportional to the MEA solvent circulation rate, assuming steady- state plant operations, and in these specific cases solvent circulation rates approached the minimum achievable due to solvent pump limitations. Lower solvent flow rates could have been achieved with the use of the solvent filtration system however this was not tested during operations with addition of anti-foam solutions. The minimum SRD obtained for operations with anti-foam solutions added was approximately 3.7 MJ/kg CO2.
Figure 4 displays the SRD for the aqueous 40 wt% MEA solvent system. The plant was operated with 24 meters of absorber packing heights, 1.9 bara stripper pressure, and a flue gas flow rate of about 59.000 Sm3/h at 25 °C. The CO2 capture rate was kept at about 85 %. The results in Figure 4 show a minimum in the SRD of about 3.4 MJ/kg CO2 at lean amine loadings ranging between 0.2 and 0.25. A batch of anti-foam solutions were added several days prior to these tests, and the effect of the anti-foam solution was likely present during these operating conditions.
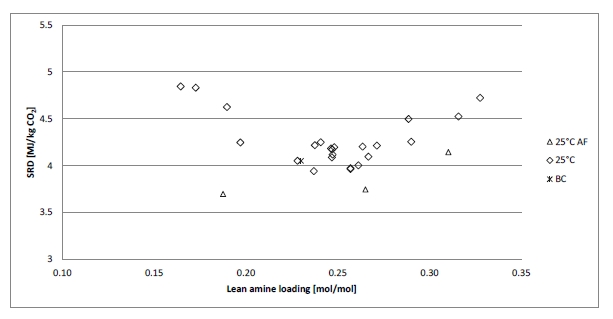
Figure 3: SRD for the 30 wt% aqueous MEA solvent system as a function of the lean amine CO2 loading. AF indicates operations with anti-foam solutions injected into the aqueous MEA solvent system. BC indicates the Base-Case operation as in described by Hamborg et al. [4].
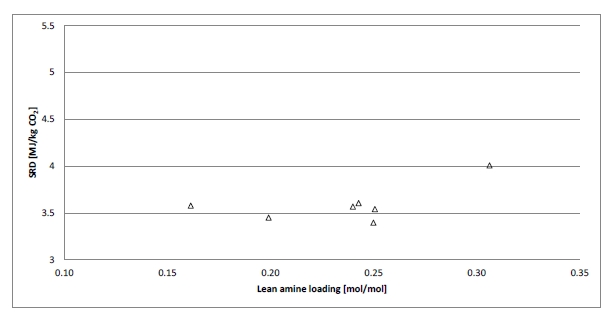
Figure 4: SRD for the 40 wt% aqueous MEA solvent system as a function of the lean amine CO2 loading.
Figure 5 displays a comparison of the results presented in Figure 3 and Figure 4 as a function of the ratio of solvent flow rate to the flue gas supply rate on mass basis (L/G ratio). Operations with the 40 wt% aqueous MEA solvent system clearly provide lower values of the SRD and L/G ratios. The use of 40 wt% or higher MEA concentrations must however be considered with respect to higher solvent degradation rates, as described by Morken et al. [5], and possible material corrosion rates. The latter is however irrelevant for the TCM DA amine plant as it is constructed primarily of high grade stainless steel and polypropylene plastic material for absorber lining. The metal ion concentrations were monitored during the MEA campaign, and no significant increase in ion concentration was observed for 40 wt% operations.

4.3 Effects of absorber packing heights
Figure 6 displays the effects of absorber packing heights. The SRD obtained with 24 meters of absorber packing heights of about 4.0 MJ/kg CO2 are lower than those of 18 meters of about 4.5 MJ/kg CO2. The plant was operated at 1.9 bara stripper pressure and a flue gas flow rate of about 47.000 Sm3/h at 25 °C. The CO2 capture rate was kept at about 85 %.
It is well known that MEA is considered an amine with a relatively high kinetic reaction rate towards CO2, and equilibrium conditions could be expected in the absorber bottom section. Solvent sampling and laboratory analysis resulted in rich solvent CO2 loadings of about 0.44 and 0.48 for respective 18 meters and 24 meters of absorber packing heights, whereas the expected CO2 equilibrium loading for the aqueous MEA system was approximately 0.50. Preliminary simulation work has indicated that it is most likely the kinetic rate which limits the approach to equilibrium in the test runs.
Similar trends, as displayed in Figure 6, were observed with the 40 wt% aqueous MEA solvent system at different absorber packing heights.
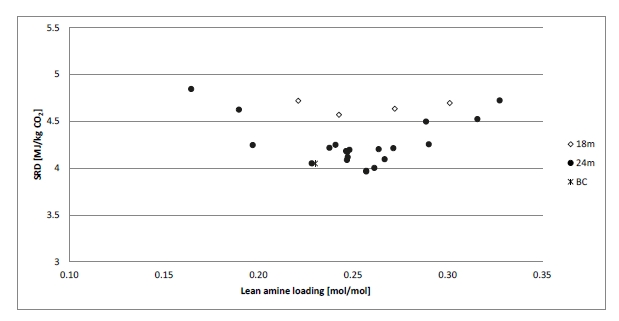
Figure 6: SRD for the 30 wt% aqueous MEA solvent system as a function of the lean amine CO2 loading and absorber packing heights.
4.4 Effect of flue gas supply flow rates
Figure 7 displays the effects of flue gas supply flow rates. The flue gas supply rate shows no significant effect on the SRD at specific lean amine loadings. The plant was operated with 24 meters of absorber packing heights, 1.9 bara stripper pressure, and a flue gas supply temperature of 25 °C. The CO2 capture rate was kept at about 85 %. At specific lean amine loadings it can be assumed that the amine plant was operated at close to identical conditions for the various flue gas supply flow rates, except the correlated adjustment of the solvent flow rate. This would ideally create a constant L/G ratio for the various flue gas supply flow rates at a certain lean amine loading. The minor differences in the SRD between the various flue gas supply flow rates at a certain lean amine loading must therefore be attributed to normal operational variations of the various amine plant unit operations.
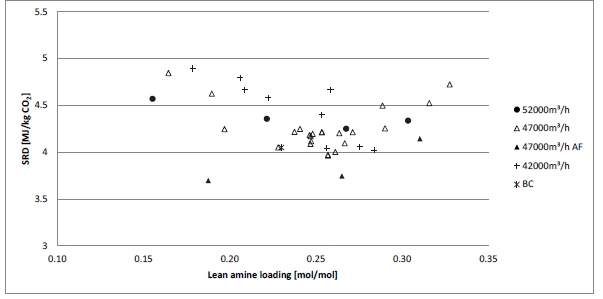
4.5 Effect of flue gas supply temperatures
Increased SRD were observed when increasing the flue gas supply temperatures from 25 °C to about 50 °C. The SRD was determined to be about 4 MJ/kg CO2 for the 30 wt% aqueous MEA solvent system at 25 °C flue gas supply temperatures, whereas the SRD was determined to be about 5.0 MJ/kg CO2 for 50 °C flue gas supply temperatures. Some increase is expected due to the temperature dependent CO2 vapor liquid equilibria behavior in the absorber bottom, leading to a lower rich amine loading at increased absorber bottom temperature, and the fact that the partial pressure of CO2 is slightly lower in the flue gas supply stream of 50 °C than 20 °C leading to decreased mass transfer driving forces. However, the more important aspect encountered during these test conditions at elevated flue gas supply temperatures was chemical equilibrium pinching of the upper section of the absorber. This was encountered when the lean amine loading was not sufficiently low, i.e. the CO2 equilibrium pressure in the lean amine solvent entering the absorber is close to or identical to the actual CO2 partial pressure in the gas phase of the upper section of the absorber. At such conditions little mass transfer will occur in the upper section of the absorber, as mass transfer driving forces are low. In order to avoid such chemical equilibrium pinching, the lean amine loading would need to be lowered by e.g. increasing the stripper bottom temperature. Aspects around this are described further below.
The chemical equilibrium pinch behavior, as aforementioned, was encountered primarily as a result of the very
low targeted depleted flue gas CO2 partial pressure, as is a consequence of CO2 capture from low partial CO2 pressure CHP flue gases. Assuming flue gas supply CO2 content of about 3.5 vol% and a corresponding partial pressure of about 35 mbara by assumption of ideal gas law behavior, the depleted flue gas CO2 partial pressure would be about 5 mbara at 85 % CO2 capture rate. In order to avoid and control such chemical equilibrium pinching behavior for any future large scale PCC amine plants in the upper section of the absorber, engineering considerations such as e.g. flue gas supply temperatures and sufficient instrumentation for monitoring of the CO2 content in the depleted flue gas should be taken into account.
4.6 Effect of stripper behavior
Figure 8 and Figure 9 displays the effect of addition of anti-foam solution to the solvent. The effect of anti-foam solution addition on the SRD is more pronounced at lower lean amine loadings. The plant was operated at 1.9 bara stripper pressure and a flue gas flow rate of about 47.000 Sm3/h at 25 °C. The CO2 capture rate was kept at approximately 85 %.
Addition of anti-foam solutions showed no impact on the absorber temperature profile as displayed by Figure 8, but showed a considerable impact on the stripper temperature profile as displayed by Figure 9. The temperature values displayed in the Figure 8 and Figure 9 are the average value of four temperature sensors in the radial plane at each axial column position. For operations without anti-foam solutions, the stripper temperature profile shows relatively high temperatures in the upper section of the stripper of about 115 °C. It is well known that such will lead to excessive amounts of water vapor leaving the stripper and being further directed to the overhead condenser, which will lead to an unnecessarily high SRD. Upon analysis of the stripper temperature profiles in the radial plane and axial direction, it was concluded that transient channeling in the stripper bed occurred during operations without addition of anti-foam solution. This resulted in poor gas liquid distribution and contact, and condensation of the stripping gas and water vapor occurred in the overhead condenser rather than inside the stripper bed. Addition of anti-foam solution reduced the channeling behavior in the stripper, and well defined as expected stripper temperature profiles were obtained in the axial direction, as displayed by Figure 9, and minor temperature differences were observed in the radial plane. At these stripper operating conditions, only moderate amounts of water vapor, as defined by chemical phase equilibria, will leave the stripper and be further directed to the overhead condenser. This is defined as optimal stripper behavior. The exact cause of the observed transient steam channeling is not yet clearly understood, however it may be caused by the solvent foaming. Engineering aspects related to this and the use of anti-foam solutions for future large scale PCC amine plants must be considered.
Environmental aspects of the use of anti-foam in such amine plants where the depleted flue gas may be emitted to air must also be considered.
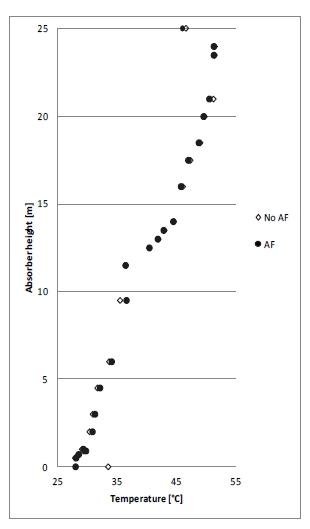
Figure 8: Absorber temperature profile with and without antifoam.
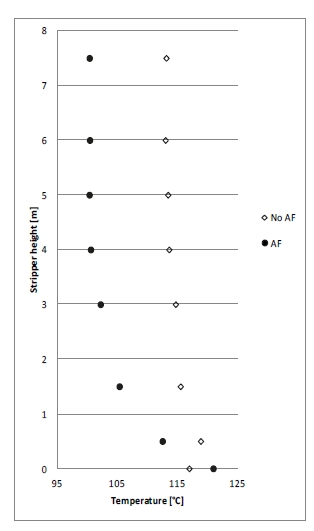
Figure 9: Stripper temperature profile with and without antifoam.
5. Conclusion
A campaign has been performed in the amine plant at the CO2 Technology Centre Mongstad applying the aqueous 30 wt% and 40 wt% MEA solvent systems for treatment of flue gas from a combined heat and power (CHP) plant. CHP flue gas flow rates were ranging from about 40.000 Sm3/h to 60.000 Sm3/h and the CO2 content was about 3.5 vol%.
Minimum steam reboiler duties (SRD) of respectively 4.0 MJ/kg CO2 and 3.7 MJ/kg CO2 were obtained for the aqueous 30 wt% MEA solvent system without and with addition of anti-foam solution. Minimum SRD of 3.4 MJ/kg CO2 was obtained for the aqueous 40 wt% MEA solvent system. Lower SRD and absorber liquid to gas (L/G) ratios could be obtained with the higher concentration MEA solvents.
Increased absorber packing heights resulted in lower SRD. Variation in flue gas supply flow rates and corresponding variations in solvent flow rates did not yield any significant variations in SRD. Decreased flue gas supply temperatures resulted in lower SRD, as rich amine loadings increased and chemical equilibrium pinch behavior in the upper section of the absorber was limited.
Engineering aspects such as flue gas supply temperatures and instrumentation for gas phase monitoring of the CO2 flue gas contents must be considered for any future large scale PCC amine plant in order to avoid chemical equilibrium pinch behavior during treatment of CHP flue gases. Engineering and environmental aspects related to the use of anti-foam solutions for future large scale PCC amine plants must also be considered.
Acknowledgements
The authors gratefully acknowledge the staff of TCM DA, Gassnova, Statoil, Shell, Sasol, and Aker Solutions for their contribution and work at the TCM DA facility.
The authors also gratefully acknowledge Gassnova, Statoil, Shell, and Sasol as the owners of TCM DA and Aker Solutions for their financial support and contributions.
References
- Andersson V, Wittmeyer K. Operational Experience and Initial Results from the First Test Period at CO2 Technology Centre Mongstad. Energy Procedia; 2013; 37:6348-6356
- de Koeijer G, Enge Y. CO2 Technology Centre Mongstad – Design, functionality and emissions of the amine plant. Energy Procedia; 2011; 4:1207-1213
- Thimsen D, Maxson A, Smith V, Cents T, Falk-Pedersen O, Gorset O, Hamborg E S. Results from MEA testing at the CO2 Technology Centre Mongstad. Part I: Post-Combustion CO2 capture testing methodology. Energy Procedia; 2014
- Hamborg E S, Smith V, Cents T, Brigman N, Falk-Pedersen O, De Cazenove T, Chhaganlal M, Feste J K, Ullestad Ø, Ulvatn H, Gorset O, Askestad I, Gram L K, Fostås B F, Shah M I, Maxson A, Thimsen D. Results from MEA testing at the CO2 Technology Centre Mongstad. Part II: Verification of baseline results. Energy Procedia; 2014
- Morken A K, Nenseter B, Pedersen S, Chhaganlal M, Feste J K, Tyborgnes R B, Ullestad Ø, Ulvatn H, Zhu L, Mikoviny T, Wisthaler A, Cents T, Bade O M, Knudsen J, De Koeijer G, Falk-Pedersen O, Hamborg E S. Emission results of amine plant operations from MEA testing at the CO2 Technology Centre Mongstad. Energy Procedia; 2014.
Chilled Ammonia Process at Technology Center Mongstad – First Results (2013)
Gerard Lombardoa, Ritesh Agarwalb, Jalal Askanderb,*
aTCMDA Mongstad Norway bALSTOM Power Inc. Knoxville TN USA *Corresponding author
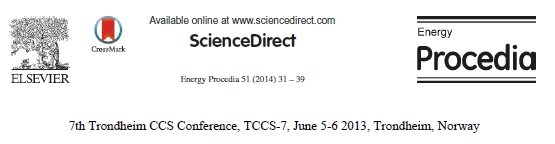
(http://creativecommons.org/licenses/by-nc-nd/3.0/).
Selection and peer-review under responsibility of SINTEF Energi AS
doi: 10.1016/j.egypro.2014.07.004
Abstract
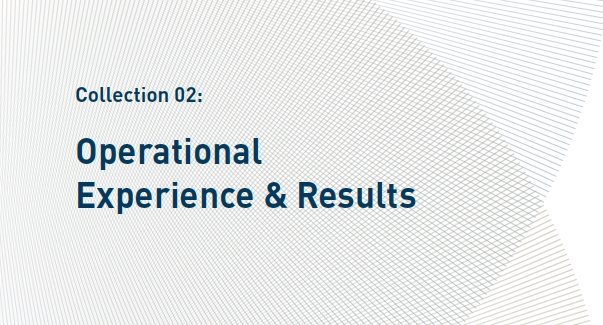
According to the latest IEA report, Carbon Capture and Storage (CCS) from fossil fuel fired power plants is a key option to mitigate CO2 emissions in the 450 scenario. In addition it is the only technology capable of large CO2 emission reduction from industrial applications and in combination with biomass firing the only currently available technology for reducing CO2 concentration in the atmosphere by means of negative emission performance. Alstom develops CCS technologies for post- combustion and oxy-combustion, and have shown that these technologies can compete with renewable power generation on the basis of Levelized Cost of Electricity (LCoE). It is now essential that governments give the same priority to CCS as to renewables in order for large demonstration plants to be built, a necessary step in the development of the technology.
The Norwegian Government, through its special purpose company Gassnova, is at the forefront of making this happen by construction of the world’s largest test site for Carbon Capture. The Technology Center Mongstad (TCM) is owned by Gassnova, Statoil, Shell and Sasol. The unique location of TCM, next to the Mongstad refinery, provides interesting opportunities in terms of gases to be treated. The plant at TCM is designed to treat both refinery off-gas from a cracker operation as well as the exhaust from a gas turbine based combined heat and power plant. In addition, the captured CO2 can be recycled to achieve any CO2 concentration between 4 and 13% by volume. The Alstom Chilled Ammonia Process (CAP) is post-combustion technology that captures CO2 emitted from power plants or industrial sources. Deployment of this technology requires operating data and validated simulation tool for design that can evaluate various CAP configurations to achieve the lowest possible capital cost, energy demand and operating cost. A special focus will be directed to the CAP Installation at TCM, which was commissioned in 2012. The plant is designed to treat both refinery off-gas from a cracker operation as well as the exhaust from a gas turbine based combined heat and power plant.
This paper will report on the first results of Chilled Ammonia Process (CAP) as part of Alstom’s development program of commercial solution for carbon capture, at Technology Center Mongstad in 2012.
© ALSTOM 2013. All rights reserved. Information contained in this document is indicative only. No representation or warranty is given or should be relied on that it is complete or correct or will apply to any particular project. This will depend on the technical and commercial circumstances. It is provided without liability and is subject to change without notice. Reproduction, use or disclosure to third parties, without express written authority, is strictly prohibited.
1. Introduction
Power generation is one of the biggest sources of man-made carbon dioxide (CO2) emissions, the main anthropogenic greenhouse gas. Innovative carbon neutral technologies will be required to enable the power sector to meet the global demand for electricity, while controlling CO2 emissions and thus reducing the impact on global warming. To achieve meaningful reductions, it will be necessary to develop technologies that can be applied to both Greenfield projects and to the existing fleet through cost effective retrofits.
Alstom is currently developing two main technologies for carbon capture; post combustion capture and oxy combustion. Among these technologies, post-combustion carbon capture and storage (CCS) using the Chilled Ammonia Process (CAP) is one of the more promising solutions.
The Chilled Ammonia Process uses an ammoniated aqueous carbonate solution to absorb CO2 from the flue gases at ambient pressure and low temperature. Unlike other technologies, the ammonium solution stability is not affected by oxygen or acidic trace components present in the incoming flue gas. The CAP process consumes a comparatively low parasitic load, which offers savings in OPEX over the life of the plant. Operation at low process temperatures allows the use of waste energy that is not available to other post-combustion CO2 capture technologies. Since gaseous emission and liquid waste streams are non-toxic, no additional treatment facilities are required.
From the standpoint of plant operations, the Chilled Ammonia Process has demonstrated stable operation at turndown conditions. The CAP process offers the flexibility and ability to follow daily and weekly changes in plant load requirements in the typical range of 25-100% without impact on the process.
As ammonia is a common and widely used chemical, the ammonia reagent in the CAP plant also lends itself to established permitting requirements, including any waste disposal issues that may arise. The by-product from the CAP facility is a liquid ammonium sulfate stream with commercial value as a fertilizer. Optionally the ammonia is recovered in a dedicated Ammonia Recovery Unit, and in this case the final by-product is gypsum, which is a well- known by-product for Power Plant Operators.
The power consumption for CO2 compression represents a substantial part of the total power consumption for the different CO2 technologies. The CAP concept involves the production of higher pressure CO2, resulting in significantly lower power consumption of CO2 compression equipment.
This paper will give an introduction to the CAP plant at TCM as well as a summary of the data collected from the operations in 2012 in comparison with simulation results. The unique location of TCM, next to the Mongstad refinery, gives interesting opportunities in terms of gases to be treated. The plant at TCM is designed to treat both refinery off-gas from a cracker operation as well as the exhaust from a gas turbine based combined heat and power plant.
2. Description of the chilled ammonia process
The Chilled Ammonia Process (Figure 1) is based on the chemistry of the NH3-CO2-H2O system and the ability of the ammoniated solution to absorb CO2 at low temperature and to release the CO2 at moderately elevated temperature.
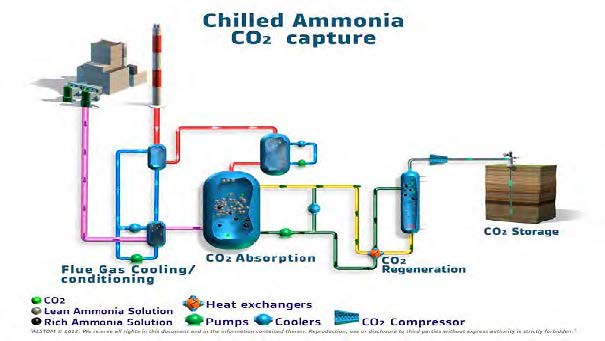
Figure 1 Chilled Ammonia CO2 Capture and storage (Alstom).
The primary CAP chemical reactions for CO2 capture are presented in Equations 1–4. During absorption, CO2, ammonia, and water combine to form ammonium carbonate, ammonium bicarbonate and ammonium carbamate mainly in ionic forms.
CO2 (g) ļ CO2 (aq) (1)
2NH3 (aq) + H2O (l) + CO2 (aq) ļ (NH4)2CO3 (aq) (2)
(NH4)2CO3 (aq) + CO2 (aq) + H2O (l) ļ 2(NH4) HCO3 (aq) (3)
(NH4)2CO3 (aq) ļ NH2CO2 NH4 (aq) + H2O (l) (4)
The reactions in the process are all reversible and their direction depends on pressure, temperature and concentration in the system. Equations 1-4 are exothermic reactions in the left to right direction requiring removal of heat from the process in order to maintain the desired CO2 absorption temperature. Equations 1-4 are endothermic reactions in the right to left direction that require energy to produce the desired products.
A distinguishing feature of the Chilled Ammonia Process, relative to a host of amine-based technologies is solvent stability. Ammonia does not undergo the types of oxidative and thermal degradation reactions that are encountered with amines. The latter characteristic allows for higher temperature regeneration to produce a higher pressure CO2 product. The Chilled Ammonia Process (CAP) consists of the following unit operations:
- Flue gas conditioning
- CO2 Absorption
- Water wash for NH3 capture
- Regeneration for CO2 release
- Stripper for ammonia recovery and wash water conditioning
- CO2 dehydration and compression
- Refrigeration system
A flow diagram of the process is shown in Figure 2.
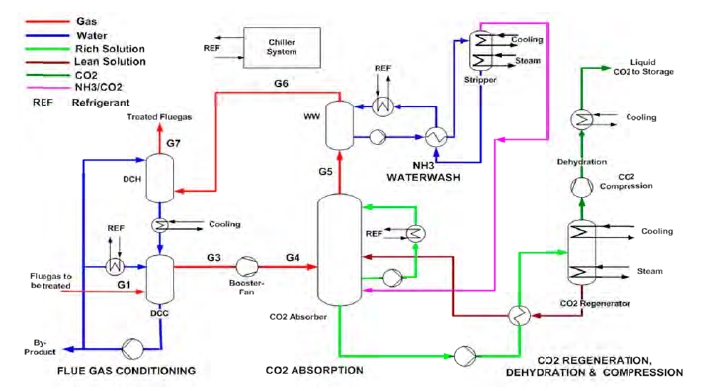
Figure 2 Chilled Ammonia Process flow diagram (Alstom).
3.Field pilots and validation facilities
3.1 CAP Field Pilot Facilities
Alstom has over 18000 hours of operating experience with CAP, through partnerships with SRI international (Menlo Park, CA) the electric Power Research Institute (EPRI –Palo Alto CA), WE energies (Pleasant Prairie, WI) E.ON (Karlshamm, Sweden) and Electric Power (AEP- Columbus OH).For description of early field pilots, please see article “CCS with the Alstom Chilled Ammonia Process Development Program -Field Pilot Results” from GHGT-10[1, 2].
3.2 Mountaineer Product Validation Facility
The Product Validation Facility is extensively described in [1]; however a short description is repeated here for better understanding of the final achievements listed below.
The CCS plant treated a slipstream of power plant flue gas using Chilled Ammonia Process (Figure 3). The flue gas was taken from a location downstream of an existing Wet Flue Gas Desulphurization system. The unit was designed to capture and store approximately 100,000 metric tons of CO2 annually and treat approximately 80,000 Nm3/hr of flue gas, or 1.5% of the total plant flue gas flow.
All the achievements were confirmed during steady-state operation of the CCS validation plant. The formal testing program for the validation project was successfully completed end of May 2011 after a 21 month period. Analysis of the operating results has been used to validate the predictions of Alstom’s process simulation models.
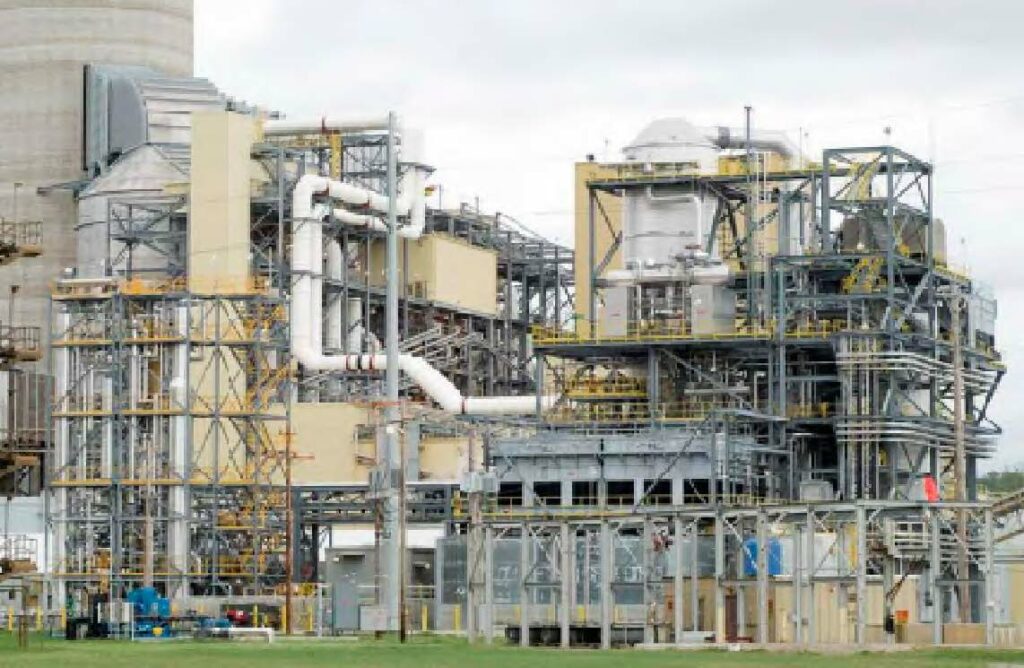
Figure 3 : Mountaineer Product Validation Facility (AEP – Alstom).
4. TCM Installation
4.1 Technology Centre Mongstad (TCM)
TCM, which is owned by Gassnova, Statoil, Shell and Sasol, is the world’s largest facility for testing of Carbon Capture technologies. The centre is located next to the Mongstad Refinery on the west coast of Norway. The CAP installation at TCM is a natural step to follow after the successful application of CAP at American Electric Power’s Mountaineer Plant, where Alstom successfully showed the robustness and competitiveness of the CAP Technology applied to coal power plant flue gas. Figure 4 shows the CAP installation at Mongstad.
The unique location of TCM, next to the refinery, provides interesting opportunities in terms of gases to be treated. The plant at TCM is designed to treat both refinery off-gas from an oil residue cracker unit as well as the exhaust from a gas turbine based combined heat and power plant.
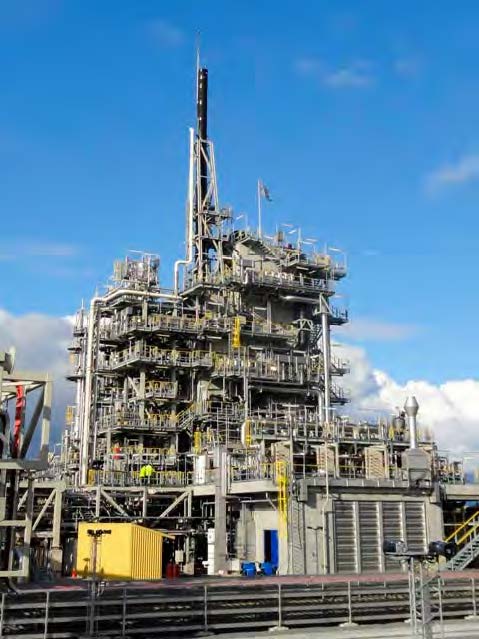
Figure 4 : CAP Installation at Mongstad (TCM DA).
4.2 CAP design at Mongstad
The design conditions for the Mongstad plant is shown in Table 1.

† The capture efficiency is the targeted efficiency for each stream. Higher capture efficiency can also be achieved.
The plant, which initially was designed in 2008, is of a very compact design. The footprint is only 1300 m2, and the height of the absorber tower is limited to 29 meters. Figure 5 shows a cut-out of the absorber tower, which in addition to 3 separate absorption sections (ABS 1, ABS 2 & ABS 3) also houses the Direct Contact Cooler (DCC), the Water Wash (WW) and the Direct Contact Heater (DCH), all of which also are of a packed bed design. All-in- all the 29 meter high structure houses almost 50 meter of packed bed height, 24 meter of sump hold-up and 15 meter of gas space!

Figure 5 : TCM Concrete Structure showing the 6 packed beds (TCM DA) The flow path of the flue gas in the tower is: DCC –>ABS 1–>ABS 2 –>ABS 3 –>WW –>DCH , and the function of the beds are in consecutive order: cooling, CO2 absorption (ABS1 & ABS 2), NH3 recovery, NH3 polishing and re-hating.
Also the regeneration section of the CAP plant is of a compact design, since the elevated pressure (approx. 20- bar) allows for a relatively small vessel. In addition to the regenerator, which is used to release the CO2 from the ammoniated solvent, the plant is also equipped with an ammonia stripper to recover NH3 and CO2 from the water wash liquid, and an appendix stripper to control the water balance and impurity build up. Figure 6 shows the regenerator to the left and the ammonia stripper to the right.
4.3 Operation Modes
As described above, the Mongstad installation is able to run either on Refinery Off-gas from the Residue Fluid Catalytic Cracker (RFCC), or on flue gas from the gas turbine powered Combined Heat and Power (CHP) plant.
The two gases differ not only in CO2 concentration as described in Table 1, but there are also differences in terms of SOx, NOx and particulate loadings. In order to provide flexibility in terms of testing, the RFCC gas supply system has been equipped with a dilution system that allows in bleed of air to lower the incoming gas CO2 concentration.
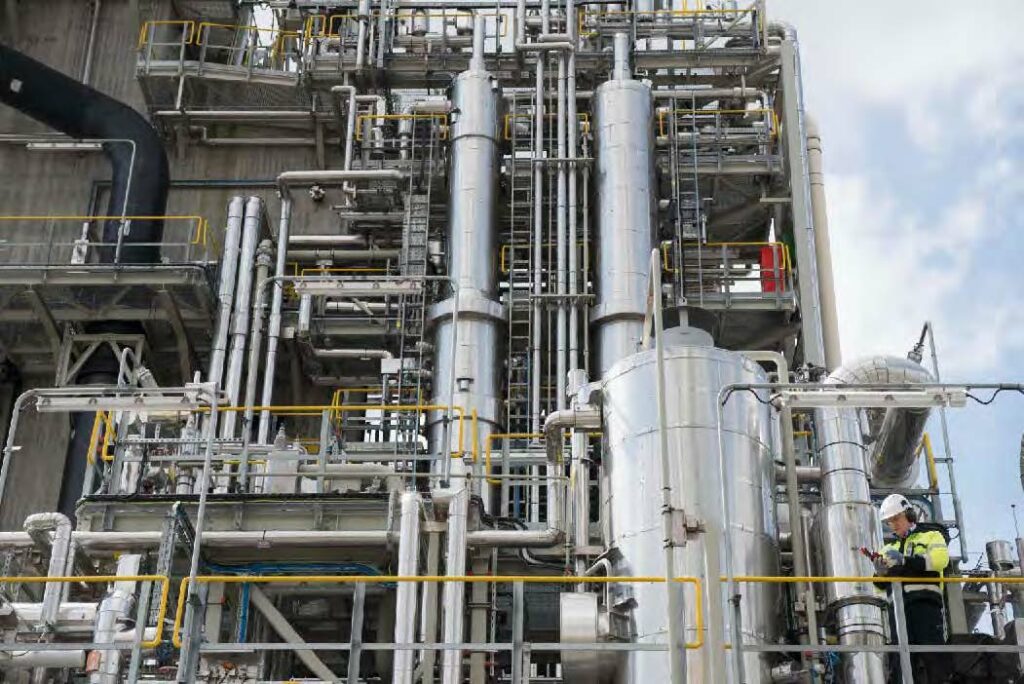
Figure 6 : CAP Regenerator and Ammonia Stripper (TCM DA).
Initial operation at TCM had been focused on achieving steady state operation as outlined in the Technology Qualification Program (TQP) for the CO2 Capture Mongstad (CCM) full scale capture project. The modifications of the plant which has been completed in April 2013 are based on development of the CAP technology since the initial design of the TCM Mongstad installation in 2008. Among other things, an additional heat exchanger will be installed to improve the heat integration concept and solvent lines will be added to increase flexibility in terms of lean solution feed to the absorption beds.
4.4 Validation Objectives
In parallel to the qualification for CCM, the TCM installation is serving as a validation facility for several improvements which have been engineered following the Mountaineer PVF experience as well as testing in the in- house pilot located in Alstom’s research facility in Växjö. These validation objectives include, but are not limited to:
- Absorption performance
- Improved two stage water wash design
- Advanced control system
- Concrete design of flue gas contactors
- Low pressure stripper design
- Trace component balance and impact
- Predictive capability of modelling software
- Energy consumption with optimized heat integration
- No degradation of solvent
5. TCM operation tuning first results
During start-up and tuning operation, there were at least 18 stable periods that were considered for data analysis. Data analysed for the full range of operations during start-up, including refinery cat-cracker gas diluted with air. Observations during this provided confidence that the unit will meet performance targets when all units are operating at design conditions as the followings:
- Start-up focused on achieving the target solvent molarity and performance of each unit operation.
- NH3 Emissions (from DCH and CO2 product) – The CAP process demonstrated l NH3 emission in both the flue gas outlet through the DCH, and the CO2 product at the CO2 wash outlet. Solvent degradation is not an issue for ammonia; however, the control of ammonia emission was acceptable even before any major tuning
- CO2 Capture – rates varied between 75 and 85%, as expected while building solvent molarity and tuning the operations.
- The CAP Performance at TCM was very much in line with what we have experienced at the AEP Mountaineer plant like quick start up, low ammonia emissions and satisfactory of individual unite operation performance.
Summary and conclusion
Alstom CCS development road map involves commercialization of CAP by 2020 and includes Bench scale research and testing, pilot plant, validation facilities, large scale demonstration plant. A delayed large scale demonstration plant has extended the CAP Commercialization date.
TCM is the largest CO2 capture test facility in the world .The Mongstad installation is the stepping stone towards a fully validated product offering which is needed to combat climate change. Alstom is fortunate to be part of the unique facility for testing CCS installations at TCM Mongstad and intends to make best use of the involvement by showing that CAP is a viable option not only for coal plants but also for gas and industrial applications
The Alstom CAP technology offers major advantages like Low cost, commodity chemical solvent, No thermal or chemical degradation, No harmful emissions or liquid waste streams, Saleable Ammonium Sulphate as by-product, and High purity and high pressure CO2 product.
CAP operation at TCM tuning first results is: CO2 capture rates from 80% to as high as 87%, CO2 purity of greater than 99.9%, Low NH3 emissions
The Process improvements that have been derived from operating experience and tests conducted at the TCM facility offered an opportunity to design and construct large CAP facility in Norway
References
- V. Telikapalli F. Kozak et al (2011) “CCS with the Alstom Chilled Ammonia Process Development Program – Field Pilot Results”, Energy Procedia, Volume 4, 2011, Pages 273–281.
- S. Jönsson, V. Telikapalli (2013)” Chilled Ammonia Process installed at the Technology Centre Mongstad” GHGT-11 (11th International Conference on Greenhouse Gas Control Technologies), Kyoto, 18-22 November 2012,
Operational Experience and Initial Results from the First Test Period at CO2 Technology Centre Mongstad (2013)
Vibeke Anderssona*, Kristina Wittmeyerb, Oddvar Gorseta, Yolandi Mareeb, Knut Sandena
aAker Clean Carbon, N-1360, Oslo, Norway bTCMDA, N-5954, Norway *Corresponding author
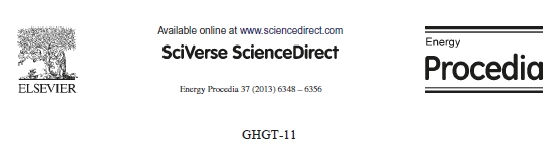
Selection and/or peer-review under responsibility of GHGT
doi: 10.1016/j.egypro.2013.06.564
Abstract
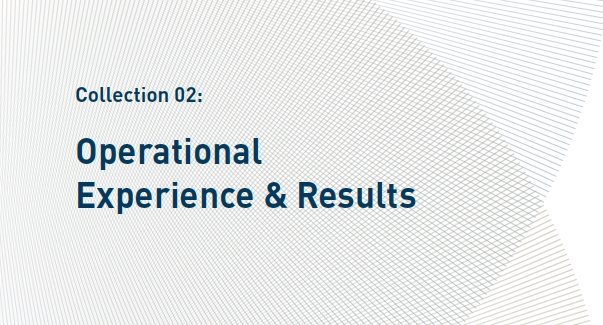
The CO2 Technology Centre Mongstad (TCM) is currently regarded as the largest CO2 capture technology test center for testing and improving CO2 capture. The aim of the TCM facility is to provide a platform for improving CO2 capture processes by establishing the means for technology providers to further develop and verify their technologies on a larger scale, thereby promoting the application of CO2 capture processes at full scale, worldwide.
The amine plant at TCM came on-line during the second quarter of 2012. This paper outlines the main functionalities of the amine plant and presents some operational experiences and initial results from the first operation period with MEA. Further testing in the plant over the next 15 months is dedicated to qualification programs aimed towards full third-party facilitated qualifications for large scale plants with ACC technology.
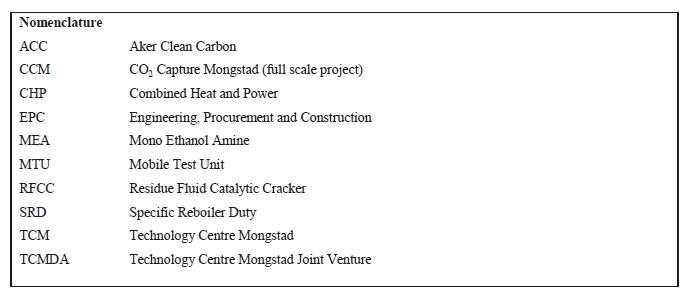
1. Technology Centre Mongstad
The CO2 Technology Centre Mongstad (TCM) is currently regarded as the largest CO2 capture technology test center for testing and improving CO2 capture processes. The facility is owned by TCMDA – a joint venture between Gassnova (the Norwegian state) (75%), Statoil (20%), Shell (2.4%) and Sasol (2.4%) [1]. The is 100 000 tons of CO2 captured per year, and the test results will be valid for direct scale-up to full scale CO2 capture plants. The design and functionality is described in detail elsewhere [2].
The aim of the TCM facility is to provide a platform for improving CO2 capture processes by establishing the means for technology providers to further develop and verify their technologies on a larger scale, thereby influencing the applicability of CO2 capture processes worldwide.
There are two capture plants installed at TCM, one utilizing amine technology, designed and delivered by Aker Clean Carbon (ACC), and the second utilizing a chilled ammonia technology, designed and delivered by Alstom.
The two technologies will both be tested on two different flue gas sources. One of the sources is off- gas from the Residue Fluid Catalytic Cracker (RFCC) at the Mongstad Refinery. In addition to being a typical refinery emission gas this source exhibits similar characteristics and properties as flue gas from coal fired plants. The other source is exhaust gas originating from the Combined Heat and Power plant (CHP) at Mongstad.
As part of the EPC contract awarded by TCMDA to ACC, ACC was allocated the right – upon delivery of the plant to TCMDA – to lease the facility for the first period of operation. In essence, ACC being the user of the facility will specify the test program for the first 15 months of operation. TCM DA has the responsibility of operations of the facility including the obtaining of emission permit [3], as well as provision of operational support. Detailed results from testing with ACC proprietary solvents are owned by ACC.
2. Amine Plant
2.1 Absorber and Regeneration units
The purpose of the absorber tower and the associated water wash sections is to absorb a minimum of 85 % of the CO2 in the flue gas, to maintain the water balance in the plant and to minimize amine and amine degradation products in the treated flue gas before exiting the tower.
The absorber tower in the amine plant is more flexible than commercial CCS plants, with three absorption sections – each with a separate lean amine inlet and a total of 60 temperature sensors, thus enabling thorough investigation of solvent reaction rates and distribution. Results to date have shown clear temperature profiles in the areas of reactions when feeding at all of the three inlets, both horizontally as well as vertically over the packing. This, in turn, provides a comprehensive understanding of the packing height requirements while confirming proper liquid distribution throughout the column.
In the sides of the rectangular-shaped absorber tower, four columns are installed through which gamma radiation sources are fitted (on an ad-hoc basis) to provide a scan of the column internals [4]. This scan has been performed twice; the first serving as a base- line scan and the second was performed shortly after full load of the plant was achieved (flue gas and solvent load). The scans showed no abnormalities, and good liquid distribution profile through the tower. A third scan is planned after a few months of operation to assess if any blockages or mal-distribution have occurred.
The two water wash systems each consist of a three meter packing section, a holding tank, a pump and a cooler. The top washing section may be utilized as an acid wash section. Two demisters are installed – one above the last absorption section and one above the upper water wash packing section. Both water wash systems have been operated at full load (50 t/h and 60 t/h respectively) without acid addition. Very low levels of amines have been detected from the absorber flue gas (below 1ppm) which verifies that the current water wash system was appropriately designed for the MEA specific runs.
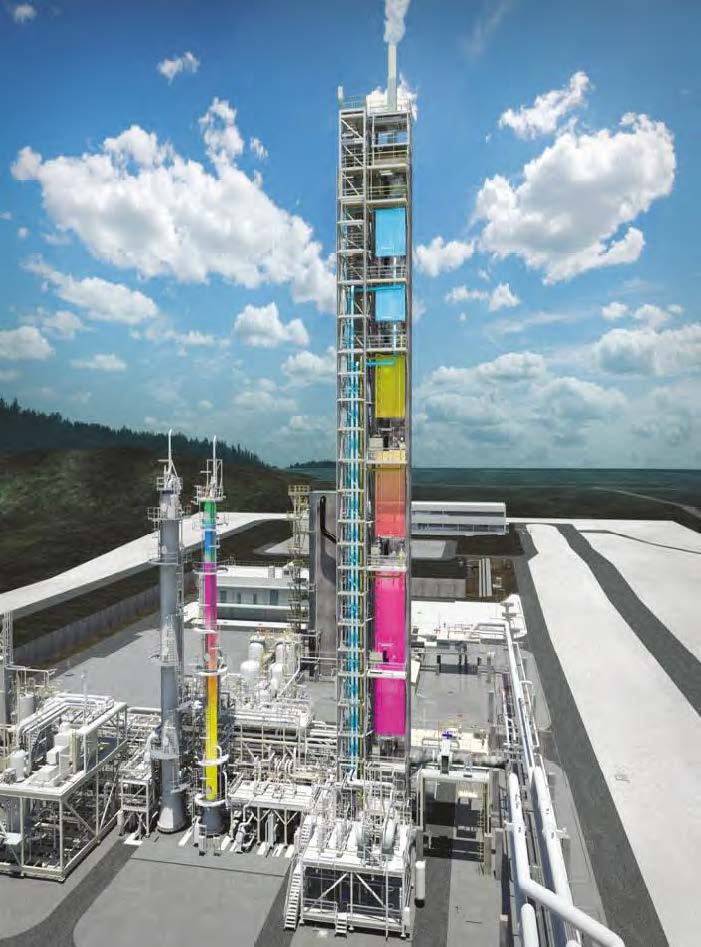
Figure 1 : Absorber and regeneration units in the amine plant.
To accommodate for the difference in CO2 concentration in the two flue gas sources, two strippers (desorbers) are installed. The strippers are installed with different types of reboilers, one is a plate and frame reboiler and the other is a shell and tube reboiler. This enables validation of reboiler suitability in various operating scenarios. The welded plate and frame reboiler has proven to be sensitive towards steam/water hammer, subsequently leading to micro-cracking of the internals. While this was being attended to, the RFCC reboiler was put in operation with no further difficulties experienced. The CHP reboiler is expected to be back in service for testing with the ACC propriety solvent soon.
Figure 1 shows a picture from the 3D model of the amine plant, illustrating the absorption and desorption sections.
2.2 Data collection and laboratory
To be able to ensure good technology qualification, a vast amount of data is collected from more than 1000 online instruments in the amine plant and more than 1100 in the utility plant. In addition, there are multiple sampling points for liquid sampling throughout the amine plant. A laboratory has been established as part of the TCMDA infrastructure to analyze the liquid samples using state-of-the-art technologies. As the analytical procedures for many of the measurements required for particularly emissions related activities are in the development phase, extensive amount of time has been spent in establishing methods within the TCM laboratory. This process is on-going as improvements to existing methods are made by outside research organisations. In conjunction to analyses, methods for physical sampling also had to be established. This relates in particular to the isokinetic sampling at the absorber tower exhaust.
Properties such as conductivity, pH and density are measured online in the amine streams and these data can also be verified by lab analyses. Also, emissions monitoring is mainly done online and is regularly verified by isokinetic sampling and lab analyses.
To establish the mass balances and to monitor emissions to air, an FTIR analyzer is installed, measuring various components in the inlet flue gas stream, the treated flue gas stream out of the absorber and the CO2 product stream out of the regenerator. The FTIR analyzer is the main piece of equipment used for emissions reporting to the authorities, especially for amine, ammonia and aldehyde components [2]. All data is logged and stored in an IP21 data management system.
3. Utilities
The TCM plant provides its own utilities and also receives some utilities from the adjacent Mongstad refinery and the CHP plant. Utilities such as cooling water (seawater), demineralised water, plant and instrument air and nitrogen are provided from the TCM facility directly. The imported utilities include process (raw) water, fire water, potable water and high-pressure steam, which is provided at 30 Barg and
335 C. Both the technology plants have their own steam let-down systems to medium- and low pressure steam. The plants also have their own steam condensate receiving system from where the condensate is returned directly to the Mongstad refinery.
The two flue gas sources are first run through a separate blower to obtain enough transport pressure to reach the TCM plant. The RFCC flue gas is also run through a sea water cyclone for particle removal. The flue gas from the CHP has a CO2 concentration of ca. 3.5 mole%. There is a possibility to recycle CO2 when the CHP flue gas source is in use, to boost the CO2 content up to 9 mole%. It is a relatively clean flue gas with small amounts of NOx, SOx and ammonia, see Table 1.
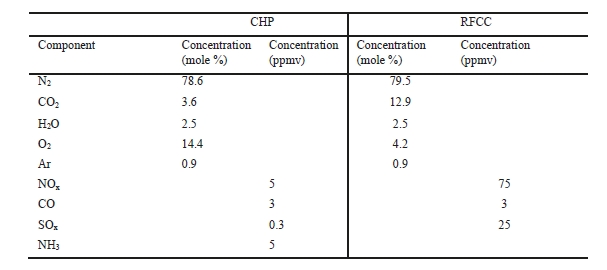
Table 1: Typical flue gas compositions.
The online FTIR is set to measure the quality of the flue gas entering the system, but difficulties were experienced in the calibration of the instrument at low levels of NOx. The estimated detection limit of NO (as NOx) is 5ppm at this stage as interferences with water peaks were observed. The result was that the instrument read 0ppm for levels below 5ppm during most of the MEA specific run.
4. General operational experience at TCM
Hot commissioning of the plant was carried out with MEA and flue gas from the CHP. A successful stability test conducted as part of commissioning marked the hand-over of the plant from Aker Clean Carbon to TCMDA and at the same time marked the start-up of the ACC test period at TCM. The initial tests in this test period was also carried out with MEA and flue gas from CHP.
By the end of August 2012, the plant had been in operation capturing CO2 for approx. 500 hours. Figure 2 below shows the time trend of the flue gas flow into the Absorber. The trend illustrates the operational period with CO2 capture, during this time frame. It is worth noting that significant time during this period was dedicated to different commissioning-related activities, and several periods of down-time were necessary due to these activities, as evident from the figure. Figure 3 below shows both the accumulated operating hours of the amine plant and the accumulated CO2 capture for this period.
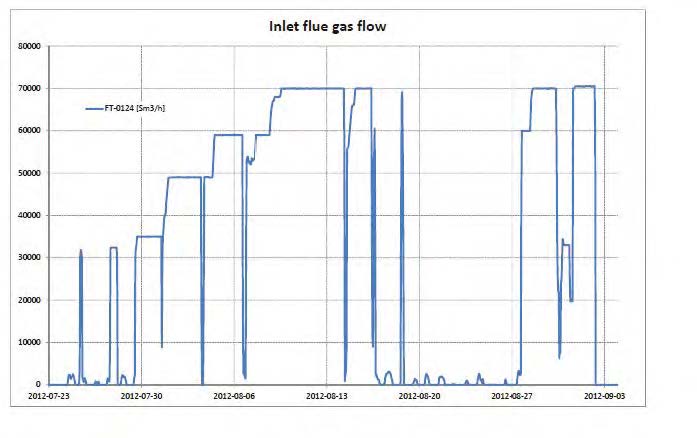
Figure 2: Inlet flue gas flow indicating operational periods, i.e.periods with CO2 capture.
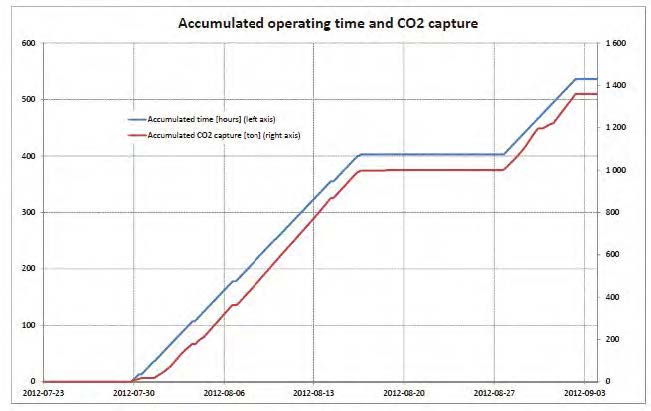
It was expected that a plant of such complexity in terms of amount of instrumentation would require substantial effort before normal operation was established. This has proven to be the case. The main operational focus this far has therefore been related to tuning of the plant, especially tuning of flow instruments and gas analyzers.
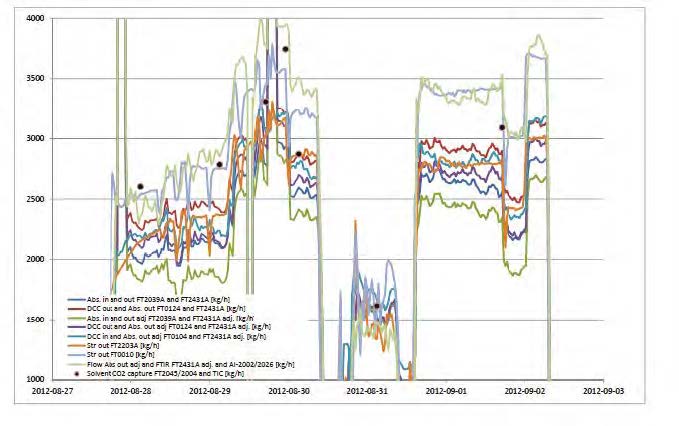
Figure 4 illustrates the challenge of mass balance closure, through different measured readings of the captured CO2. A total of 8 online measurements as well as solvent analysis are available for calculating the CO2 capture, and as seen, the readings had a discrepancy of ~40%. Through thorough investigations and testing of the flow meters set-up, we have now decreased the discrepancy and are able to close the balances to acceptable levels. Establishing and verification of the mass and heat balances, both in-house and by independent third party is still on-going at TCM.
5. Initial Results
5.1 CO2 capture degree
During the initial start-up period, it was not our focus to maintain a constant CO2 capture degree, or to maximize this. As seen from Figure 5, the capture degree has varied between 68% and close to 100% during operation. However, operational experience has now shown that the capture degree can be set at the required level and maintaining the capture at required 85-90% is achievable.
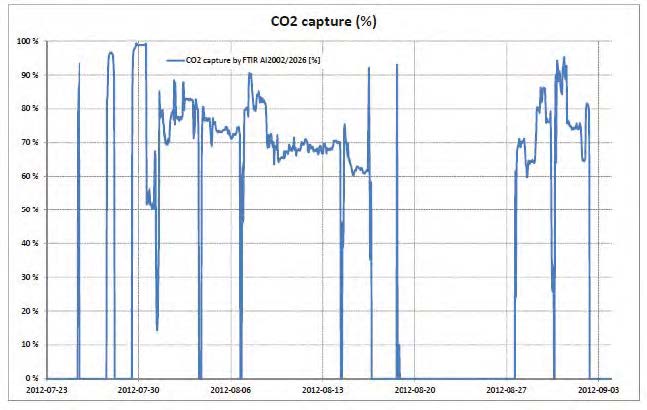
Figure 5: CO2 capture degree throughout the period.
5.2 Energy Consumption
The calculated Specific Reboiler Duty (SRD) in terms of MJ thermal/kg CO2 captured is shown in Figure 6. Also in the figure, the measured steam consumption and the CO2 capture is shown. The initially achieved SRD lies between 4.1 and 5 MJ/kg CO2 and is within what we expected for MEA for these operational conditions, based on earlier experiences.
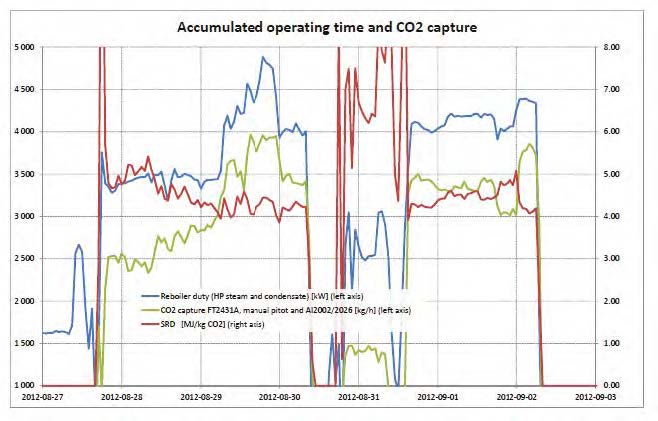
Figure 6: Measured energy consumption.
5.3 Emissions
The surveillance and minimization of emission from the TCM plant was and remains top priority [2,3]. The emission from the amine plant is closely monitored through online measurements, isokinetic sampling and lab analysis. In Figure 7, the emission of MEA throughout the period as measured by the online FTIR instrument is shown. It is seen that during this first operational period, low levels of MEA emissions were detected with the online measurements, well within the expectation level and emission permit [2]. Superimposed on the graph are points representing the results from isokinetic sampling and laboratory analysis of MEA. As seen from the figure, these manual measurements have confirmed the readings from the online instrumentation.
6. Future Testing
ACC is responsible for developing a test program at TCM during the Test Period and will utilize the plant for their proprietary solvent development and technology qualification.
Recently, the MEA has been replaced with one of ACC`s proprietary amines and for the next months, operation of the plant will be dedicated to a qualification program for the full-scale Mongstad project (CCM) using one of ACC`s amine developed to minimize environmental impact and steam consumption. The amine plant at TCM, ACC`s Mobile Test Unit (MTU), testing at supplier and laboratory testing are all inputs to this program.
Following completion of the ongoing qualification program, a reference run with MEA (Baseline Reference Case) will be conducted, providing more details and confidence to the data presented as the first initial results. Subsequent to the reference case, ACC will continue to utilize the TCM plant for further testing of their proprietary solvent using both the CHP and RFCC flue gas source.
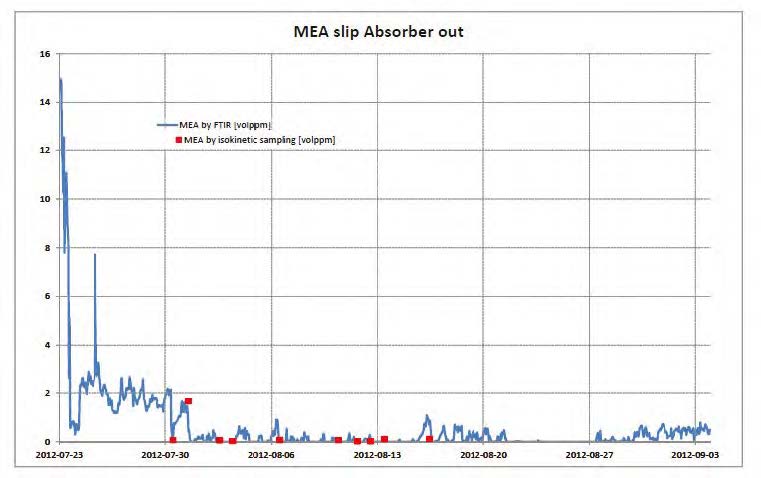
Figure 7: Emission profile as measured by online instrumentation as well as isokinetic sampling.
7. References
- www.tcmda.com
- De Koeijer G, Enge, Y., Sanden, K., Graff, O.Fr., Falk-Pedersen-, O., Amundsen, T. and Overå, S.; CO2 Technology Mongstad Design, Functionality and Emissions of the Amine Plant, GHGT10
- Maree Y, Nepstad S, De Koeijer G, Establishment of knowledge base for Emission Regulation for the CO2 Technology Centre Mongstad. 2012
- Gallon A, TRACERCO DiagnosticsTM Tower Scan of the Flue Gas Absorber, TCM unit, Mongstad August 2012 [Restricted report]